Le processus de moulage des pièces en fonte de roulette
Grâce à la recherche sur le processus de coulée et le matériau de la plaque de laminage du lit de refroidissement des plaques moyennes et lourdes, une nouvelle méthode de fabrication de pièces moulées en fonte de roulette avec plusieurs piles de noyaux de sable en résine métallique est étudiée. La méthode a un processus simple, une productivité élevée, des performances globales de coulée élevées et une bonne qualité de surface.
Statut actuel du processus de moulage de pièces en fonte de roulette
Les pièces en fonte de roulette font référence à un type de pièces moulées dont le diamètre est beaucoup plus grand que la hauteur. Généralement, les exigences de traitement du trou d'arbre intermédiaire sont relativement élevées, le moyeu et la jante sont plus épais et la paroi au niveau du rayon est mince, ce qui provoque facilement une température inégale et une grande différence de température. Le moyeu et la jante sont deux points chauds. Si le processus de moulage est déraisonnable, le moulage est sujet à une cavité de retrait, une porosité de retrait et des défauts de fissure. À l'heure actuelle, la plupart des fabricants nationaux produisent des pièces moulées pour roulettes en utilisant des méthodes de moulage au sable d'argile ordinaire, de moulage en une seule pièce, d'injection de porte tangentielle et d'alimentation de colonne montante ou de coulée utilisées conjointement avec de la fonte réfrigérée au moyeu. Cette méthode occupe un grand espace, le rendement du processus, le rendement et l'efficacité de la production sont faibles et la qualité de surface de la coulée est médiocre.
Après que nous ayons reçu la tâche de production de rouleaux de lit de refroidissement de fonte de type roulette (plus de 5700 pièces), le premier problème à résoudre est la recherche du processus de coulée. Le processus doit être simple, afin que les travailleurs qui ne sont pas familiers avec le moulage puissent opérer. Il est nécessaire de réduire la zone de moulage et de coulée et de répondre aux besoins de production dans les conditions de production existantes. Lors de l'étude du processus de coulée, nous avons à nouveau rencontré des problèmes de matériaux. La plaque de rouleau fabriquée était très fragile et ne pouvait pas du tout être utilisée dans la production. Grâce à la recherche sur le processus de coulée et le matériau de la coulée, un nouveau type de processus de coulée pour les pièces en fonte de roulette a été recherché et des rouleaux qualifiés ont été produits.
Principaux contenus de recherche et technologies clés
1.Recherche de matériaux
La plaque à rouleaux est l'un des composants clés de l'équipement du lit de refroidissement. Il nécessite une bonne qualité de surface et une résistance élevée à la chaleur. La résistance à la chaleur de la fonte dépend principalement de sa résistance à l'oxydation à haute température (c'est-à-dire si le film d'oxyde formé à la surface de la fonte a un effet protecteur) et de la croissance de la fonte (c'est-à-dire l'expansion irréversible de la taille de pièces en fonte qui travaillent à haute température). Ces deux propriétés sont étroitement liées à la composition chimique de la fonte. La solidité et la résistance aux chocs des pièces moulées en fonte dépendent principalement du nombre d'éléments d'alliage, de sorte que l'étude du matériau des pièces moulées devient un problème très important. Pour cette raison, nous avons mené des recherches sur le matériau et fait un choix raisonnable de composition chimique, qui non seulement améliore la résistance à la chaleur de la coulée, mais garantit également les propriétés mécaniques de la coulée. Le matériau de conception d'origine du rouleau est le RQTSi5 et sa composition chimique (%) est : wC = 2.30 % ~ 2.89 %, wSi = 4 % ~ 5 %, wMn = 5.5 % ~ 0.50 %, wP = 0.77 % ~ 0.06 %, wS=0.09 %~0.062 %, wCr=0.089 %~0.38 %. Ses propriétés mécaniques sont les suivantes : résistance à la traction 0.49-140MPa, dureté 220-160 HBW. La température de fonctionnement maximale est de 270~750℃. En raison de la teneur élevée en silicium de ce matériau, la température de transition fragile de la fonte est augmentée. Par conséquent, le moulage est très fragile et ne convient pas à la production de pièces sensibles à la fragilité avec une épaisseur de paroi inégale. La plaque à rouleaux appartient à la coulée de cette structure. En conséquence, la production vient de démarrer. À cette époque, de nombreux déchets étaient causés par des problèmes matériels. De plus, comme le matériau du RQTSi900 est cassant et que le rendement est faible, la plupart des fabricants nationaux n'utilisent plus ce matériau pour fabriquer des rouleaux. Compte tenu de la situation ci-dessus, afin d'éviter la mise au rebut par lots des tôles de rouleau et d'assurer le démarrage en douceur du projet de tôles moyennes et fortes, la production d'essai d'un matériau émergent pour la production de tôles de rouleau est devenue une priorité absolue. A travers de nombreuses expérimentations et démonstrations, nous avons décidé d'utiliser le nouveau matériel que nous avons développé. Sa composition chimique est : wC=5%~3.05%, wSi=3.51%~2.9%, wMn=3.5%~0.24%, wP=0.56%~ 0.05%, wS=0.09%~0.010%, wMo=0.030%~ 0.29%. Ses propriétés mécaniques sont les suivantes : résistance à la traction 0.6~580MPa, allongement 695%~8%, dureté 18~210 HBW. La température de fonctionnement maximale est de 280~750℃. En raison des bonnes propriétés des matériaux développés et du taux de rendement élevé, il a été reconnu par les utilisateurs.
Une fois le matériau déterminé, les ingrédients du matériau, le processus de sphéroïdisation, le processus d'inoculant et d'inoculation, le contrôle qualité devant le four, etc. ont été abordés et réussis. Les propriétés mécaniques du rouleau atteignent les meilleures de l'histoire de l'atelier de fonte. Niveau.
2.S'attaquer aux problèmes clés du processus de fusion
Pour obtenir du fer fondu de haute qualité une fois la composition chimique déterminée, un processus de fusion raisonnable est nécessaire. Pour les pièces moulées en fonte ductile résistantes à la chaleur, le traitement de sphéroïdisation est particulièrement important (c'est-à-dire le choix de l'inoculant et du procédé de sphéroïdisation). Les propriétés mécaniques des pièces moulées sont également bonnes lorsque la sphéroïdisation est traitée. Nous avons sélectionné un inoculant approprié grâce à la recherche et développé un processus de sphéroïdisation raisonnable, de sorte que le fer fondu puisse être bien sphéroïdisé, ce qui améliore non seulement la résistance de la coulée, mais augmente également son allongement et l'effet est très bon.
- Sélection de l'agent de sphéroïdisation La qualité de l'agent de sphéroïdisation affecte directement l'effet de sphéroïdisation et affecte la qualité de la fonte en fusion et des pièces moulées. Grâce à de nombreuses expériences et démonstrations, nous avons finalement déterminé que l'agent de sphéroïdisation adopte la terre rare légère ReMg5-8, l'inoculant adopte 75SiFe et l'inoculant unique à longue durée d'action qui peut améliorer considérablement la résistance et l'allongement de la fonte.
- Sphéroïdisation Pour obtenir des moulages de haute qualité, le choix des inoculants et des procédés de sphéroïdisation est également très important. En s'attaquant à des problèmes clés, nous avons sélectionné un inoculant approprié et formulé un processus de sphéroïdisation raisonnable, qui a non seulement augmenté la résistance de la coulée, mais également augmenté son allongement, et l'effet était très bon.
Le processus de sphéroïdisation utilise un sac de barrage, qui doit être soigneusement séché. Divers alliages doivent être préchauffés. Les alliages ajoutés au sac de barrage de bas en haut sont : alliage léger de terres rares 1.8% → inoculant 0.8% → plaque de fer de couverture ou poudre de fer (selon la température du fer fondu) → surface alcaline 0.5%. Les 2/3 du fer sont prélevés et, une fois la réaction terminée, le fer est à nouveau prélevé jusqu'à la quantité requise et 0.6% de ferromolybdène, 0.6% d'inoculant sont ajoutés avec le flux et le laitier est éliminé.
3.S'attaquer aux problèmes clés du processus de coulée
Afin de créer un projet de haute qualité, notre société a mis en avant des exigences supérieures à la norme nationale pour la qualité de surface, les tolérances dimensionnelles et le volume de traitement des rouleaux. Cependant, les rouleaux ont des lots importants et des calendriers serrés. Afin de saisir l'horaire, l'atelier a dû utiliser certaines techniques de moulage. Les travailleurs temporaires non familiers produisent des disques à rouleaux, ce qui pose des exigences extrêmement élevées sur le processus de disques à rouleaux. Nous avons fait des recherches sur le processus de moulage.
- Recherche de processus de modélisation On constate à partir de la structure de la pièce que le moyeu est plus épais et les rayons sont plus fins. À l'heure actuelle, la plupart des fabricants nationaux produisent des pièces moulées avec cette structure en utilisant une pièce moulée ordinaire de type sable, avec des colonnes montantes au moyeu et des portes tangentielles. Avec ce processus, le taux de rendement du processus, le taux de produits finis sont faibles et l'efficacité de la production est également faible. Si le moule en sable ordinaire est utilisé pour la coulée en une seule pièce, la production de 5,700 144 rouleaux doit être achevée dans les délais requis, 288 rouleaux doivent être produits chaque jour, 16 bacs à sable, 8 moules métalliques et une zone de moulage et de coulée suffisante sont requis, et le complexe artisanal, incapable de fonctionner pour les travailleurs qui ne sont pas familiarisés avec le moulage et ne peuvent pas répondre aux exigences de production. À cette fin, nous avons choisi le processus d'empilement de noyau de sable de résine métallique par comparaison, c'est-à-dire que le sable de résine de boîte à noyau métallique est utilisé pour fabriquer le noyau, puis le noyau de sable est déposé ensemble et placé sur l'anneau de la boîte pour le versement. Seuls 3 ensembles de boîtes à noyaux métalliques sont nécessaires pour répondre aux besoins de production en adoptant ce processus. Chaque grappe est coulée avec 8 piles, chaque pile est coulée avec 48 pièces et une plaque inférieure est coulée avec XNUMX pièces en même temps. En raison de l'utilisation du système de déclenchement commun, le taux de moulage est élevé et la qualité de surface des moulages en sable de résine est bonne.
- Conception et production d'outillage Une fois le processus déterminé, nous avons conçu et réalisé l'outillage requis
- Le dosage, le mélange et la production de sable de noyau. Le processus de préparation du sable de noyau est la clé du processus d'empilement de noyaux d'assemblage de sable de résine. Au début de la production, en raison du rapport inadéquat de résine et d'agent de durcissement, le noyau de sable était difficile à retirer du moule métallique et la qualité de surface du noyau de sable était très mauvaise. La production d'essai du rapport a finalement déterminé le rapport entre la résine, l'agent de durcissement et le sable brut, et a produit des noyaux de sable qualifiés. Proportion : 0.45~0.224 mm (40/70 mesh) sable à récurer 100 %, la résine est de 1.8 % à 2 % de le poids du sable brut et l'agent de durcissement représentent 30 % à 50 % de la résine.Mélange : le mélangeur de sable S2512C est utilisé pour le mélange de sable de résine. Ajoutez le sable brut pesé au mélangeur de sable, puis ajoutez l'agent de durcissement, commencez à mélanger pendant 8 à 10 minutes, puis ajoutez la résine, mélangez et broyez pendant 8 à 10 minutes, puis sortez le sable. Production de noyau de sable : essuyez nettoyer la surface intérieure de la boîte à noyaux avant la production, appliquer un agent de démoulage, piler le sable uniformément lors de la fabrication du noyau et s'assurer que la taille est précise lors de la réparation du noyau. Les noyaux préparés sont numérotés dans l'ordre et du graphite à base d'alcool est utilisé. Brossez la peinture deux fois. Une fois la peinture enflammée, utilisez un chiffon sec pour polir la surface du noyau de sable en douceur.
- Le choix du système de coulée La taille du système de coulée affecte directement la qualité des pièces moulées. Si la zone du système de coulée est trop petite, des défauts tels qu'un coulage insuffisant et des barrières froides se forment facilement. S'il est trop grand, il est difficile de le nettoyer des pièces moulées. La fonte est en fonte ductile. Lorsque nous avons commencé la production, nous avons installé 4 roues internes en tête de puits. En conséquence, le disque du rouleau était souvent mis au rebut en raison du nettoyage de la porte. Plus tard, nous avons sélectionné un système de blocage raisonnable grâce à des expériences basées sur la forme et le poids des pièces moulées, et avons produit des pièces moulées qualifiées. Nous tirons pleinement parti de son expansion de graphitisation et de ses caractéristiques d'auto-alimentation et adoptons une méthode de coulée d'alimentation sans colonne montante. Seules deux portes plates de 80 mm × 40 mm sont ouvertes en tête de chaque rouleau. Ce système de coulée permet non seulement d'économiser du fer en fusion, mais réduit également les heures de travail pour nettoyer la colonne montante de coulée, et la qualité de surface de la coulée est également bonne.
- Détermination du nombre de rouleaux d'empilage Grâce à la technologie de coulée par empilement, le nombre de pièces coulées à chaque fois affecte directement la qualité des pièces moulées. Trop de pièces moulées sont sujettes à des trous de retrait en raison d'une mauvaise alimentation. Trop peu de pièces moulées, la productivité du travail et le rendement du processus sont trop faibles. Afin d'assurer la qualité lorsque l'équipe de recherche a commencé la production d'essai, seulement 6 pièces par pile ont été coulées. Avec l'accumulation continue d'expérience de production, selon notre calcul minutieux, nous coulons maintenant 8 pièces par pile et une carotte par 3 piles. En conséquence, il garantit non seulement la qualité des pièces moulées, mais améliore également la productivité du travail.
- Sélection de la température de coulée. Les pièces moulées avec une température de coulée élevée sont sujettes à des défauts tels que la porosité et le retrait, tandis que la température de coulée est trop basse pour provoquer des défauts tels qu'un coulage insuffisant et des grains de fer à la surface. Nous avons fixé une température de coulée raisonnable de 1280~1300 par le biais d'expériences. , produire des moulages qualifiés.
- Contrôle du temps de boxe. Les moulages sont faciles à déformer si la boxe est trop précoce, et cela affectera le versement ultérieur. Selon la taille et la quantité des moulages, nous avons stipulé que le temps de grève est de 6h.
Contrôle de la qualité
Afin de garantir la qualité des rouleaux produits, nous avons mis en place un système d'inspection strict : chaque rouleau doit être attaché à un bloc de test pour les tests de coulée, et les propriétés mécaniques, la structure métallographique et la composition chimique du bloc de test sont testées à 100 %. . Les non qualifiés ne quitteront pas l'usine.
Effet de production
- Le disque à rouleaux développé par le processus d'empilement multi-groupes de l'assemblage de noyau de sable en résine métallique a une résistance élevée et une bonne qualité de surface. Ses diverses propriétés dépassent de loin le matériau de conception d'origine et répondent aux besoins des utilisateurs.
- Après avoir adopté ce processus, le rapport sable/fer n'est que de 1.5:1, ce qui est bien inférieur au niveau de technologie de pointe domestique (3~4.5:1), ce qui permet d'économiser beaucoup de sable de résine.
- Le processus est simple à utiliser et la qualité est garantie. L'atelier de fonte a également produit des rouleaux de haute qualité en utilisant un grand nombre d'opérateurs non qualifiés.
- La productivité est augmentée de plus de deux fois, ce qui permet non seulement d'économiser des heures de travail, mais également d'économiser beaucoup de coûts de bac à sable.
- Étant donné que plusieurs jeux de rouleaux multiples utilisent un système de coulée commun et qu'aucune colonne montante n'est requise, le taux de rendement de coulée peut atteindre 95 %, ce qui est bien supérieur au taux de rendement de traitement de 70 % des méthodes de traitement ordinaires. En raison de la petite section transversale du système de porte, il ne peut être nettoyé qu'en martelant légèrement, ce qui réduit considérablement les heures de travail pour couper les pièces moulées et verser les colonnes montantes.
Depuis que la plaque de rouleau produite par notre société a été mise en production dans l'usine de plaques moyennes et lourdes, elle fonctionne bien, fonctionne correctement et normalement, et il n'y a eu aucune rayure du lit froid, aucune bosse sur la plaque d'acier ou déviation de la plaque d'acier en raison de la qualité de la plaque de rouleau. L'efficacité garantit le fonctionnement normal de la production de notre usine et crée de bons avantages économiques.
Conclusion
Grâce à la recherche sur le matériau et le processus de coulée de la plaque à rouleaux, nous avons terminé la tâche de coulée de la plaque à rouleaux à temps, en qualité et en quantité, posant ainsi les bases du démarrage en douceur du projet de plaques moyennes et fortes de notre société. En raison de la grande efficacité de ce processus et de la bonne qualité de surface des pièces moulées, sur la base de l'achèvement de nos rouleaux de refroidissement, nous avons entrepris plus de 20,000 XNUMX tâches de production de rouleaux de Lingang, Xianggang et d'autres fabricants. Les perspectives de promotion et d'application sont larges et économiques. Les bénéfices sont très importants.
Veuillez conserver la source et l'adresse de cet article pour réimpression:Le processus de moulage des pièces en fonte de roulette
Minghe Casting Company se consacre à la fabrication et à la fourniture de pièces de moulage de qualité et de haute performance (la gamme de pièces de moulage sous pression en métal comprend principalement Moulage sous pression à paroi mince,Chambre chaude coulée sous pression,Chambre froide coulée sous pression), Service rond (Service de moulage sous pression,Usinage CNC,Fabrication de moules,Traitement de surface). Tout moulage sous pression en aluminium personnalisé, moulage sous pression en magnésium ou en zamak/zinc et autres exigences en matière de moulages sont invités à nous contacter.
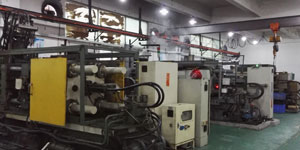
Sous le contrôle des normes ISO9001 et TS 16949, tous les processus sont effectués via des centaines de machines de moulage sous pression avancées, de machines à 5 axes et d'autres installations, allant des blasters aux machines à laver Ultra Sonic.Minghe dispose non seulement d'équipements de pointe, mais également de professionnels équipe d'ingénieurs, d'opérateurs et d'inspecteurs expérimentés pour réaliser la conception du client.
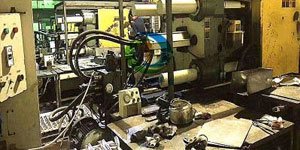
Fabricant sous contrat de moulages sous pression. Les capacités incluent des pièces de moulage sous pression en aluminium à chambre froide à partir de 0.15 lb. jusqu'à 6 lb, configuration à changement rapide et usinage. Les services à valeur ajoutée comprennent le polissage, la vibration, l'ébavurage, le grenaillage, la peinture, le placage, le revêtement, l'assemblage et l'outillage. Les matériaux travaillés comprennent des alliages tels que 360, 380, 383 et 413.
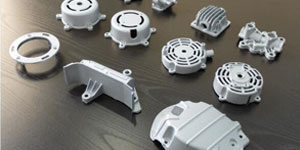
Assistance à la conception de moulage sous pression de zinc/services d'ingénierie simultanés. Fabricant sur mesure de pièces moulées en zinc de précision. Des moulages miniatures, des moulages sous pression à haute pression, des moulages en moules à glissières multiples, des moulages en moules conventionnels, des moulages sous pression unitaires et indépendants et des moulages à cavité scellée peuvent être fabriqués. Les pièces moulées peuvent être fabriquées dans des longueurs et des largeurs allant jusqu'à 24 po avec une tolérance de +/- 0.0005 po.
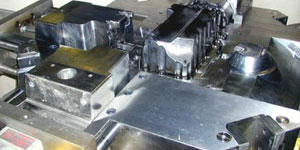
Fabricant certifié ISO 9001 : 2015 de magnésium moulé sous pression, les capacités incluent le moulage sous pression de magnésium sous pression jusqu'à une chambre chaude de 200 tonnes et une chambre froide de 3000 tonnes, la conception d'outillage, le polissage, le moulage, l'usinage, la peinture en poudre et liquide, une assurance qualité complète avec des capacités CMM , assemblage, emballage et livraison.
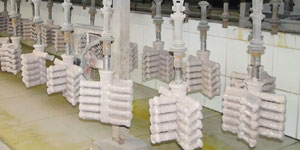
Certifié ITAF16949. Service de casting supplémentaire inclus coulée d'investissement,moulage en sable,Coulée par gravité, Coulée de mousse perdue,Coulée centrifuge,Coulée sous vide,Moulage de moule permanentLes capacités comprennent l'EDI, l'assistance technique, la modélisation solide et le traitement secondaire.
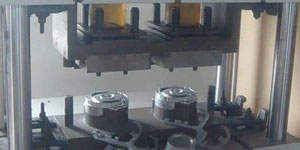
Industries de moulage Études de cas de pièces pour : voitures, vélos, avions, instruments de musique, motomarines, appareils optiques, capteurs, modèles, appareils électroniques, boîtiers, horloges, machines, moteurs, meubles, bijoux, gabarits, télécommunications, éclairage, appareils médicaux, appareils photographiques, Robots, Sculptures, Équipement de sonorisation, Équipement de sport, Outillage, Jouets et plus encore.
Que pouvons-nous vous aider à faire ensuite ?
∇ Aller à la page d'accueil pour Moulage sous pression Chine
→Pièces de fonderie-Découvrez ce que nous avons fait.
→Conseils à propos de Services de moulage sous pression
By Fabricant de moulage sous pression Minghe |Catégories : Articles utiles |Matières Mots clés: Moulage d'aluminium, Moulage de zinc, Coulée de magnésium, Moulage de titane, Fonderie en acier inoxydable, Coulée de laiton,Coulée de bronze,Vidéo de casting,Historique de l'entreprise,Moulage sous pression en aluminium |Commentaires fermés