Processus de traitement de la fonte nodulaire et questions nécessitant une attention particulière
Le traitement d'alliage de la fonte remonte aux années 1930 et 1940. Le traitement d'alliage a fait un saut qualitatif dans les propriétés de la fonte. Dans le même temps, certaines fontes spéciales telles que la résistance à l'usure, la résistance à la corrosion et la résistance à la chaleur sont nées. L'utilisation de l'inoculation pour produire de la fonte a également été produite au cours de cette période. À la fin des années 1940, la fonte à graphite sphérique après inoculation a remplacé la fonte à graphite lamellaire habituelle. Nous appelons ce type de fonte la fonte nodulaire.
La classification des éléments de sphéroïdisation et de desphéroïdisation
Les éléments de sphéroïdisation sont généralement divisés en trois groupes en fonction de leur effet de sphéroïdisation.
- Premier groupe : Mg, Y, Ce, La, Pr, Sm, Dy, Ho, Er.
- Le deuxième groupe : Ba, Li, Cs, Rb, Sr, Th, K, Na.
- Le troisième groupe : Al, Zn, Cd, Sn.
- Le premier groupe a la capacité de sphéroïdisation la plus forte, le deuxième groupe est le deuxième et le troisième groupe est le plus faible.
- Lorsque le magnésium est utilisé comme élément de sphéroïdisation, le troisième groupe d'éléments a tendance à produire un effet de désphéroïdisation.
Éléments de désphéroïdisation : Le soufre et l'oxygène sont des éléments de désphéroïdisation courants dans la fonte. De plus, Ti, Al, B, As, Pb, Sn, Sb, Bi, Te, Se, etc. sont des éléments de desphéroïdisation courants dans le fer en fusion. Le tableau ci-joint est classé selon son mécanisme d'action.
Comment choisir l'agent de sphéroïdisation
Les noduliseurs et les inoculants sont les matériaux les plus importants dans le processus de sphéroïdisation. En plus d'une qualité stable, les facteurs suivants doivent être pris en compte lors du choix d'un noduliseur approprié.
- Température de sphéroïdisation : Si la température de sphéroïdisation est supérieure à 1480℃, la réaction de sphéroïdisation sera plus intense, entraînant un taux d'absorption de magnésium inférieur. Afin de rendre la réaction de sphéroïdisation stable, un agent de sphéroïdisation avec une teneur en calcium relativement élevée peut être sélectionné. Si la température de sphéroïdisation est inférieure à 1480°C, un agent de sphéroïdisation avec une teneur en calcium relativement faible peut être utilisé.
- Taille du sac de traitement : Si le rapport hauteur/diamètre du sac de traitement est de 1:1, la perte de vapeur de magnésium réduira le taux d'absorption du magnésium. Il est recommandé d'utiliser un agent de sphéroïdisation avec une teneur en calcium plus élevée. Si le rapport hauteur/diamètre de l'ensemble de traitement est de 2:1, la réaction de sphéroïdisation sera relativement stable, la vapeur de magnésium se diffusera dans le fer en fusion et le taux d'absorption du magnésium sera amélioré.
- Processus de sphéroïdisation : Si la méthode de couverture n'est pas utilisée, la fumée générée par la réaction de sphéroïdisation entrera dans l'atmosphère et produira une lumière blanche éblouissante. Afin de rendre la réaction de sphéroïdisation stable, un agent de sphéroïdisation à faible teneur en magnésium et à haute teneur en calcium peut être utilisé. Si vous utilisez le procédé cap-and-wrap, le fer en fusion n'éclaboussera pas et produira moins de fumée. Vous pouvez utiliser un agent de sphéroïdisation à haute teneur en magnésium et à faible teneur en calcium pour réduire la quantité et le coût de la sphéroïdisation.
- Poids de traitement : si le poids de la fonte en fusion à traiter est inférieur à 500 kg, un agent de sphéroïdisation avec une taille de particule plus petite peut être utilisé, et un agent de sphéroïdisation avec une taille de particule de 12 mm ou moins est recommandé. Si le poids du fer fondu est de 500 à 1000 3 kg, un agent de sphéroïdisation avec une plus grande taille de particule peut être utilisé, tel qu'un agent de sphéroïdisation avec une taille de particule de 25 à 1000 mm. Si le poids du fer fondu est supérieur à 4 kg, l'agent de sphéroïdisation de 32 ~ XNUMX mm peut être utilisé.
- Teneur en silicium : si le produit de coulée a un faible rendement de traitement ou un taux de rebut élevé, il est souhaitable d'ajouter plus de matériau de four et de ferraille pour la fusion, et la coulée finale a des exigences strictes sur la teneur en silicium de la fonte en fusion. En partant du principe que le volume d'inoculation ne peut pas être réduit davantage, un agent de sphéroïdisation à faible teneur en silicium peut être utilisé pour le traitement, de sorte que 8 à 15 % du matériau de réchauffage peuvent être ajoutés, ce qui peut réduire le coût de production de la fonderie.
Teneur en soufre du fer brut liquide : si la teneur en soufre du fer brut liquide est élevée, si le traitement de désulfuration n'est pas effectué, un noduliseur à haute teneur en magnésium et en terres rares est requis et la quantité ajoutée sera plus élevée. L'agent de sphéroïdisation à faible teneur en magnésium et terres rares peut être utilisé, et la quantité ajoutée sera plus faible, et le coût de l'agent de sphéroïdisation à faible teneur en magnésium et terres rares sera moins cher.
Différentes méthodes de sphéroïdisation
À l'heure actuelle, les méthodes de sphéroïdisation couramment utilisées sont les suivantes : méthode de traitement en emballage (y compris méthode de poinçonnage direct, méthode sandwich et méthode de couverture), méthode de sphéroïdisation interne de type, méthode de flux, processus de traitement au magnésium pur (y compris méthode de sous-emballage et méthode de carottage) Méthode en ligne). Les avantages et les inconvénients de ces méthodes de sphéroïdisation sont brièvement présentés ci-dessous.
- Méthode de traitement dans l'emballage : Il s'agit du processus de sphéroïdisation le plus courant et il a un large éventail d'applications. Ce processus peut être utilisé pour des pièces automobiles aussi petites que quelques kilogrammes et des pièces d'énergie éolienne aussi grosses que des dizaines de tonnes. Le taux d'absorption du magnésium est le plus élevé dans la méthode de couverture, suivie de la méthode sandwich. L'inconvénient est que le degré d'automatisation actuel n'est pas élevé et que certaines usines d'équipements domestiques développent des systèmes d'alimentation automatique.
- Type méthode de sphéroïdisation interne : Il n'y a pas beaucoup de fonderies utilisant ce procédé, car les défauts de ce procédé sont évidents. Le laitier produit par le processus de sphéroïdisation pénètre parfois dans la cavité, provoquant des défauts d'inclusion de laitier et produisant des déchets. De plus, ce processus de sphéroïdisation a des exigences plus élevées sur la température et le débit du fer en fusion, sinon la sphéroïdisation sera inégale.
- Méthode d'écoulement : Comme son nom l'indique, la méthode d'écoulement est la sphéroïdisation en faisant couler du fer en fusion à travers une chambre de sphéroïdisation remplie d'un agent de sphéroïdisation. À l'heure actuelle, ce procédé n'est pas trop utilisé. L'avantage est que le degré d'automatisation est relativement élevé ; l'inconvénient est qu'il a des exigences strictes sur la température et le débit de la fonte en fusion.
- Procédé de sphéroïdisation au magnésium pur : parfois appelé procédé de sphéroïdisation à haute teneur en magnésium, il existe actuellement deux formes principales, la méthode de sous-traitance et la méthode du fil fourré. L'avantage de cette méthode est qu'elle a un degré d'automatisation plus élevé et qu'elle est également propice à la protection de l'environnement ; l'inconvénient est que le taux d'absorption du magnésium est faible et qu'il produit plus de fumée et de scories.
L'image ci-jointe compare divers processus de sphéroïdisation en termes de taux d'absorption de fumée, de scories et de magnésium.
Précautions pour la production de fonte ductile
Résumez maintenant brièvement les questions nécessitant une attention particulière dans la production de fonte ductile.
- La teneur en soufre et autres oligo-éléments du liquide de fer brut ne doit pas être trop élevée. Si la teneur en soufre et la teneur en autres oligo-éléments dans le fer fondu d'origine sont trop élevées, plus d'agent de sphéroïdisation est requis ou un agent de sphéroïdisation avec une teneur en terres rares plus élevée est requis, de sorte que le coût de l'agent de sphéroïdisation augmentera, et sphéroïdisation excessive L'agent provoquera plus de laitier, ce qui n'est pas favorable à la stabilité de la qualité de la coulée. Une teneur trop élevée en terres rares produira facilement du graphite fragmenté sur des pièces moulées de grande section.
- La stabilité de la sphéroïdisation. Le processus de sphéroïdisation est un processus clé dans la production de fonte nodulaire. Ce n'est que lorsque le processus de sphéroïdisation est stable que la qualité des pièces moulées peut être stable. Pour différents produits, différentes teneurs en soufre liquide de fer brut, la quantité d'agent de sphéroïdisation, d'inoculant, etc. à ajouter, doivent être écrites dans les instructions de travail et strictement mises en œuvre.
- Évitez les longs délais d'attente. Après le traitement d'inoculation par sphéroïdisation, le coulage doit être effectué immédiatement. Car avec le temps, le magnésium résiduel brûlera et l'effet d'inoculation diminuera.
- Éviter une teneur en magnésium résiduel trop élevée. Une teneur en magnésium résiduel plus élevée augmentera la tendance au retrait des pièces moulées. Pour la fonte ductile générale, la teneur en magnésium résiduel (fraction massique) doit être contrôlée entre 0.035% et 0.045%, et pour la fonte ductile à haute teneur en nickel, la teneur en magnésium résiduel doit être contrôlée entre 0.06 % et 0.07 %.
- Utilisez de meilleurs inoculants pour les moulages avec des exigences plus élevées. Pour les pièces d'énergie éolienne et les pièces de rail à grande vitesse avec des exigences plus élevées, l'inoculant de flux à fort effet d'inoculation (tel que Ultraseed/Ce breveté) doit être sélectionné. Sa caractéristique est qu'il peut augmenter considérablement le nombre de sphères de graphite, et les sphères de graphite sont arrondies.
Veuillez conserver la source et l'adresse de cet article pour réimpression:Processus de traitement de la fonte nodulaire et questions nécessitant une attention particulière
Minghé Société de moulage sous pression sont dédiés à la fabrication et à la fourniture de pièces de moulage de qualité et de haute performance (la gamme de pièces de moulage sous pression en métal comprend principalement Moulage sous pression à paroi mince,Chambre chaude coulée sous pression,Chambre froide coulée sous pression), Service rond (Service de moulage sous pression,Usinage CNC,Fabrication de moules,Traitement de surface). Tout moulage sous pression en aluminium personnalisé, moulage sous pression en magnésium ou en zamak/zinc et autres exigences en matière de moulages sont invités à nous contacter.
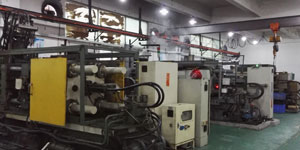
Sous le contrôle des normes ISO9001 et TS 16949, tous les processus sont effectués via des centaines de machines de moulage sous pression avancées, de machines à 5 axes et d'autres installations, allant des blasters aux machines à laver Ultra Sonic.Minghe dispose non seulement d'équipements de pointe, mais également de professionnels équipe d'ingénieurs, d'opérateurs et d'inspecteurs expérimentés pour réaliser la conception du client.
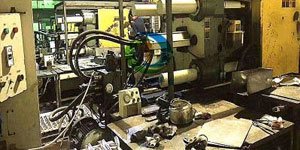
Fabricant sous contrat de moulages sous pression. Les capacités incluent des pièces de moulage sous pression en aluminium à chambre froide à partir de 0.15 lb. jusqu'à 6 lb, configuration à changement rapide et usinage. Les services à valeur ajoutée comprennent le polissage, la vibration, l'ébavurage, le grenaillage, la peinture, le placage, le revêtement, l'assemblage et l'outillage. Les matériaux travaillés comprennent des alliages tels que 360, 380, 383 et 413.
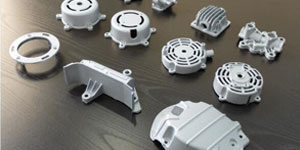
Assistance à la conception de moulage sous pression de zinc/services d'ingénierie simultanés. Fabricant sur mesure de pièces moulées en zinc de précision. Des moulages miniatures, des moulages sous pression à haute pression, des moulages en moules à glissières multiples, des moulages en moules conventionnels, des moulages sous pression unitaires et indépendants et des moulages à cavité scellée peuvent être fabriqués. Les pièces moulées peuvent être fabriquées dans des longueurs et des largeurs allant jusqu'à 24 po avec une tolérance de +/- 0.0005 po.
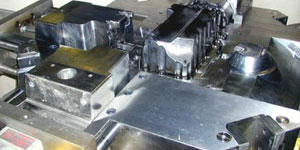
Fabricant certifié ISO 9001 : 2015 de magnésium moulé sous pression, les capacités incluent le moulage sous pression de magnésium sous pression jusqu'à une chambre chaude de 200 tonnes et une chambre froide de 3000 tonnes, la conception d'outillage, le polissage, le moulage, l'usinage, la peinture en poudre et liquide, une assurance qualité complète avec des capacités CMM , assemblage, emballage et livraison.
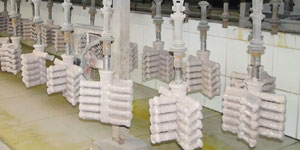
Certifié ITAF16949. Service de casting supplémentaire inclus coulée d'investissement,moulage en sable,Coulée par gravité, Coulée de mousse perdue,Coulée centrifuge,Coulée sous vide,Moulage de moule permanentLes capacités comprennent l'EDI, l'assistance technique, la modélisation solide et le traitement secondaire.
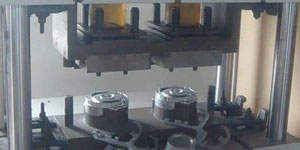
Industries de moulage Études de cas de pièces pour : voitures, vélos, avions, instruments de musique, motomarines, appareils optiques, capteurs, modèles, appareils électroniques, boîtiers, horloges, machines, moteurs, meubles, bijoux, gabarits, télécommunications, éclairage, appareils médicaux, appareils photographiques, Robots, Sculptures, Équipement de sonorisation, Équipement de sport, Outillage, Jouets et plus encore.
Que pouvons-nous vous aider à faire ensuite ?
∇ Aller à la page d'accueil pour Moulage sous pression Chine
→Pièces de fonderie-Découvrez ce que nous avons fait.
→Conseils à propos de Services de moulage sous pression
By Fabricant de moulage sous pression Minghe |Catégories : Articles utiles |Matières Mots clés: Moulage d'aluminium, Moulage de zinc, Coulée de magnésium, Moulage de titane, Fonderie en acier inoxydable, Coulée de laiton,Coulée de bronze,Vidéo de casting,Historique de l'entreprise,Moulage sous pression en aluminium |Commentaires fermés