Comment améliorer les mesures du processus de coulée du taux de sphéroïdisation
Le niveau de sphéroïdisation des pièces moulées en fonte à graphite sphéroïdal ordinaire domestique doit atteindre le niveau 4 ou supérieur (c'est-à-dire que le taux de sphéroïdisation est de 70 %), le taux de sphéroïdisation atteint par la fonderie générale est d'environ 85 %. Au cours des dernières années, avec le développement de la production de fonte nodulaire, en particulier dans les industries ayant des exigences élevées en matière de production de coulée éolienne et de qualité de coulée, le niveau de sphéroïdisation doit atteindre le niveau 2, c'est-à-dire que le taux de sphéroïdisation atteint plus de 90%. La société de l'auteur a analysé et amélioré le processus de sphéroïdisation et d'inoculation utilisé dans QT400-15, ainsi que l'agent de sphéroïdisation et l'inoculant, de sorte que le taux de sphéroïdisation de la fonte nodulaire a atteint plus de 90 %.
1. Le processus de production d'origine
Processus de fabrication d'origine :
- L'équipement de fusion adopte un four à fréquence intermédiaire 2.0T et un four à fréquence industrielle 1.5T ;
- La composition du liquide de fer brut QT400-15 est ω(C)=3.75%~3.95%, ω(Si)=1.4%~1.7%, ω(Mn)≤0.40%, ω(P)≤0.07%, ω( S) ) 0.035 % ;
- L'agent de sphéroïdisation utilisé dans le traitement de sphéroïdisation est de 1.3 % à 1.5 % d'alliage RE3Mg8SiFe ;
- L'inoculant utilisé dans le traitement d'inoculation est de 0.7% ~ 0.9% d'alliage 75SiFe-C. Le traitement de sphéroïdisation adopte deux méthodes de taraudage et de rinçage :
Tout d'abord, 55% ~ 60% de fer sont produits, puis la sphéroïdisation est effectuée, puis l'inoculant est ajouté, puis le reste du fer liquide est ajouté.
En raison de la méthode traditionnelle de sphéroïdisation et d'inoculation, le taux de sphéroïdisation détecté par un seul bloc d'essai en coin coulé d'une épaisseur de 25 mm est généralement d'environ 80%, c'est-à-dire que le niveau de sphéroïdisation est le 3ème.
2. Plan de test pour améliorer le taux de sphéroïdisation
Afin d'augmenter le taux de sphéroïdisation, le processus de sphéroïdisation et d'inoculation d'origine a été amélioré. Les principales mesures sont : l'augmentation de la quantité d'agent de sphéroïdisation et d'inoculant, la purification du fer en fusion et le traitement de désulfuration. Le taux de sphéroïdisation est encore testé avec un seul bloc d'essai en coin coulé de 25 mm. Le plan spécifique est le suivant :
- (1) Analysez la raison du faible taux de sphéroïdisation du processus d'origine. On pensait que la quantité d'agent de sphéroïdisation était faible, de sorte que la quantité d'agent de sphéroïdisation ajoutée a été augmentée de 1.3 % à 1.4 % à 1.7 %, mais le taux de sphéroïdisation ne répondait pas aux exigences. . (2) Une autre hypothèse est que le faible taux de sphéroïdisation peut être causé par une mauvaise gestation ou un déclin de la fertilité. Par conséquent, l'expérience a augmenté la dose d'inoculation de 0.7% à 0.9% à 1.1%, et le taux de sphéroïdisation n'a pas satisfait aux exigences.
- (3) Continuez à analyser et pensez qu'il y a plus d'inclusions dans le fer fondu et que des éléments d'interférence à haute sphéroïdisation peuvent être la cause du faible taux de sphéroïdisation. Par conséquent, une purification à haute température du fer en fusion est effectuée. La température de purification à haute température est généralement contrôlée à 1500±10°C, mais son taux de sphéroïdisation n'a pas dépassé 90 %.
- (4) La quantité élevée de (S) consomme sérieusement la dose de sphéroïdisation et accélère le déclin de la sphéroïdisation. Par conséquent, le traitement de désulfuration est augmenté pour réduire la quantité de fer liquide d'origine ω(S) de 0.035% à moins de 0.020%, mais le taux de sphéroïdisation est également atteint seulement 86%. Les résultats d'essai des quatre schémas ci-dessus sont présentés dans le tableau 1. La structure et les propriétés mécaniques du bloc d'essai en forme de coin ne répondaient pas aux exigences.
3. Le dernier plan d'amélioration adopté
3.1 Mesures d'amélioration spécifiques
- Les matières premières sont la fonte brute, les ferrailles inoxydables ou moins rouillées et les matériaux de réchauffage ;
- Désulfuration de la fonte brute en fusion par ajout de carbonate de sodium (Na2CO3) dans le four ;
- Utilisez l'agent de prétraitement Foseco 390 pour pré-désoxyder dans le sac ;
- Traitement de sphéroïdisation avec Fozco Nodulizer;
- Utilisation d'une inoculation combinée de carbure de silicium et de ferrosilicium.
Le contrôle original de la composition du fer fondu du nouveau procédé : ω (C) = (3.70 % ~ 3.90 %, ω (Si) = 0.80 % ~ 1.20 % [coulée ω (Si final) = 2.60 % ~ 3.00 %], ω ( Mn) 0.30 %, ω(P),0.05%, ω(S)≤0.02%. Lorsque le fer fondu d'origine ω(S) dépasse 0.02%, le carbonate de sodium industriel est utilisé pour la désulfuration devant le four, car le la réaction de désulfuration est une réaction endothermique, la température de désulfuration doit être contrôlée à environ 1500°C, et la quantité de carbonate de sodium ajoutée est contrôlée à 1.5% ~ 2.5% selon la quantité de (S) lors de la fusion dans le four .
En même temps, l'ensemble de traitement de sphéroïdisation adopte un ensemble de traitement de type barrage ordinaire. Tout d'abord, ajoutez 1.7% d'agent de sphéroïdisation de marque Foseco NODALLOY7RE sur le côté du barrage au bas de l'emballage, aplatissez et compactez, et utilisez 0.2% de carbure de silicium en poudre et 0.3% de petit Le 75SiFe en vrac est recouvert d'une couche l'une après l'autre , et après tassage, il est recouvert d'un fer à repasser et 0.3% d'inoculant Foseke 390 est ajouté de l'autre côté de la poche de fer en fusion. Lors du taraudage du fer, 55 % ~ 60 % du volume total de fer fondu est d'abord rincé. Une fois la réaction de sphéroïdisation terminée, 1.2% d'inoculant 75SiFe-C est ajouté et le fer fondu restant est rincé, et le laitier est versé.
3.2 Résultats des tests
La composition du fer fondu d'origine avant et après la désulfuration, les propriétés mécaniques et la structure métallographique du bloc d'essai en forme de coin coulé unique de 25 mm et la méthode d'évaluation du taux de sphéroïdisation dans la structure métallographique sont automatiquement détectées par le système d'analyse d'images métallographiques .
4. Analyse des résultats
4.1 L'influence des principaux éléments sur le taux de sphéroïdisation
- C, Si : C peut favoriser la graphitisation et réduire la tendance à la bouche blanche, mais une quantité élevée de (C) rendra le CE trop élevé et fera facilement flotter le graphite, généralement contrôlé à 3.7% ~ 3.9%. Si peut renforcer la capacité de graphitisation et éliminer la cémentite. Lorsque Si est ajouté comme inoculant, il peut réduire considérablement la capacité de surfusion du fer fondu. Afin d'améliorer l'effet d'inoculation, la quantité de (Si) dans le fer fondu d'origine a été réduite de 1.3 % à 1.5 % à 0.8 %. à 1.2 %, et la quantité de (Si final) a été contrôlée à 2.60 % à 3.00 %.
- Mn : Au cours du processus de cristallisation, le Mn augmente la tendance de la fonte à trop refroidir et favorise la formation de carbures (FeMn) 3C. Dans le processus de transformation eutectoïde, le Mn réduit la température de transformation eutectoïde, stabilise et affine la perlite. Mn n'a pas beaucoup d'influence sur le taux de sphéroïdisation. En raison de l'influence des matières premières, contrôler généralement ω(Mn)<0.30 %.
- P : Lorsque ω(P)<0.05%, il est soluble dans le solide dans Fe, et il est difficile de former un eutectique au phosphore, ce qui a peu d'effet sur le taux de sphéroïdisation de la fonte ductile.
- S : S est un élément desphéroïdisant. S consomme Mg et RE dans l'agent de sphéroïdisation pendant la réaction de sphéroïdisation, ce qui entrave la graphitisation et réduit la vitesse de sphéroïdisation. Le laitier sulfuré redeviendra également du soufre avant que le fer en fusion ne se solidifie, consommant à nouveau des éléments de sphéroïdisation, accélérant le déclin de la sphéroïdisation et affectant davantage la vitesse de sphéroïdisation. Afin d'atteindre un taux de sphéroïdisation élevé, la quantité de (S) dans le fer brut doit être réduite à moins de 0.02 %.
4.2 Traitement de désulfuration
Une fois la charge fondue, prélevez des échantillons et analysez la composition chimique. Lorsque la quantité de (S) est supérieure à 0.02 %, une désulfuration est requise.
Le principe de la désulfuration du carbonate de sodium est : mettre une certaine quantité de carbonate de sodium dans la poche, utiliser un flux de fer fondu pour rincer et remuer, le carbonate de sodium se décompose à haute température, la formule de réaction est Na2CO3=Na2O+CO2↑ : le Na2O généré est dans le fer en fusion à nouveau Sulfuration et formation de Na2S, (Na2O) + [FeS] = (Na2S) + (FeO).
Na2CO3 sépare et résout le CO2, provoquant une violente agitation du fer en fusion, ce qui favorise le processus de désulfuration. Les scories de carbonate de sodium s'écoulent facilement et flottent rapidement, et le temps de réaction de désulfuration est très court. Après la désulfuration, le laitier doit être éliminé à temps, sinon il redeviendra du soufre. 4.3 Traitement de pré-désoxydation, traitement de sphéroïdisation et traitement d'inoculation L'agent de prétraitement Foseke 390 joue le rôle de traitement de pré-désoxydation dans le sac et augmente en même temps le noyau de nucléation du graphite et le nombre de sphères de graphite par unité de surface, et peut également augmenter le taux d'absorption de Mg. Améliore considérablement la capacité à résister à la récession et augmente le taux de sphéroïdisation. L'inoculant Fochke contient ω (Si) = 60 % ~ 70 %, ω (Ca) = 0.4 % ~ 2.0 %, ω (Ba) = 7 % ~ 11 %, dont Ba peut prolonger le temps d'incubation effectif. Le grade NODALLOY7RE de Fozco Nodulizer est sélectionné, et son ω(Si)=40%~50%, ω(Mg)=7.0%~8.0%, ω(RE)=0.3%~1.0%, ω(Ca)=1.5 %~2.5%, ω(Al)<1.0%. Étant donné que la fonte en fusion subit des traitements de désulfuration et de pré-désoxydation, les éléments qui consomment les noduliseurs dans la fonte en fusion sont considérablement réduits, donc un noduliseur avec une faible quantité de (RE) est sélectionné pour réduire la détérioration de la morphologie du graphite sphéroïdal par RE ; Le principal élément d'action est le Mg; Ca et Al peuvent jouer un rôle dans le renforcement de l'incubation. En utilisant un traitement d'inoculation combiné au carbure de silicium et au ferrosilicium, le point de fusion du carbure de silicium est d'environ 1600°C, et le noyau de cristal de graphite est augmenté pendant la solidification, et de grandes doses de ferrosilicium sont utilisées pour l'inoculation, ce qui peut empêcher la sphéroïdisation de décliner.
Conclusion 5
Dans la production de fonte nodulaire ferritique, lorsque le taux de sphéroïdisation doit atteindre plus de 90 %, les mesures suivantes peuvent être adoptées :
- (1) Choisissez une charge de haute qualité pour réduire les éléments de désphéroïdisation dans la charge.
- (2) Choisir un agent de sphéroïdisation avec une faible quantité de ω (RE) pour réduire l'effet détériorant de RE sur la morphologie du graphite sphéroïdal.
- (3) La teneur en (S) du fer fondu d'origine doit être inférieure à 0.020%, ce qui peut réduire la consommation de noduliseurs, en particulier les éléments nodulisés consommés par la sulfuration secondaire du laitier sulfuré.
- (4) Pré-désoxyder le fer fondu, augmenter le nombre de sphères de graphite par unité de surface, augmenter le taux de sphéroïdisation, améliorer considérablement la capacité de résister à la récession et prolonger le temps d'incubation effectif.
- (5) Réduire la quantité de (Si) dans le fer fondu d'origine, augmenter la quantité d'agent de sphéroïdisation, d'inoculant et de divers agents de prétraitement, et renforcer le traitement d'inoculation.
Veuillez conserver la source et l'adresse de cet article pour réimpression: Comment améliorer les mesures du processus de coulée du taux de sphéroïdisation
Minghé Société de moulage sous pression sont dédiés à la fabrication et à la fourniture de pièces de moulage de qualité et de haute performance (la gamme de pièces de moulage sous pression en métal comprend principalement Moulage sous pression à paroi mince,Chambre chaude coulée sous pression,Chambre froide coulée sous pression), Service rond (Service de moulage sous pression,Usinage CNC,Fabrication de moules,Traitement de surface). Tout moulage sous pression en aluminium personnalisé, moulage sous pression en magnésium ou en zamak/zinc et autres exigences en matière de moulages sont invités à nous contacter.
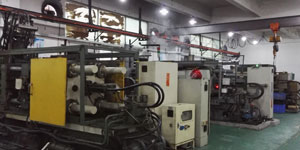
Sous le contrôle des normes ISO9001 et TS 16949, tous les processus sont effectués via des centaines de machines de moulage sous pression avancées, de machines à 5 axes et d'autres installations, allant des blasters aux machines à laver Ultra Sonic.Minghe dispose non seulement d'équipements de pointe, mais également de professionnels équipe d'ingénieurs, d'opérateurs et d'inspecteurs expérimentés pour réaliser la conception du client.
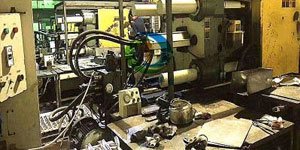
Fabricant sous contrat de moulages sous pression. Les capacités incluent des pièces de moulage sous pression en aluminium à chambre froide à partir de 0.15 lb. jusqu'à 6 lb, configuration à changement rapide et usinage. Les services à valeur ajoutée comprennent le polissage, la vibration, l'ébavurage, le grenaillage, la peinture, le placage, le revêtement, l'assemblage et l'outillage. Les matériaux travaillés comprennent des alliages tels que 360, 380, 383 et 413.
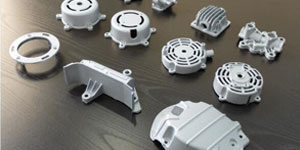
Assistance à la conception de moulage sous pression de zinc/services d'ingénierie simultanés. Fabricant sur mesure de pièces moulées en zinc de précision. Des moulages miniatures, des moulages sous pression à haute pression, des moulages en moules à glissières multiples, des moulages en moules conventionnels, des moulages sous pression unitaires et indépendants et des moulages à cavité scellée peuvent être fabriqués. Les pièces moulées peuvent être fabriquées dans des longueurs et des largeurs allant jusqu'à 24 po avec une tolérance de +/- 0.0005 po.
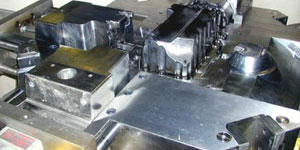
Fabricant certifié ISO 9001 : 2015 de magnésium moulé sous pression, les capacités incluent le moulage sous pression de magnésium sous pression jusqu'à une chambre chaude de 200 tonnes et une chambre froide de 3000 tonnes, la conception d'outillage, le polissage, le moulage, l'usinage, la peinture en poudre et liquide, une assurance qualité complète avec des capacités CMM , assemblage, emballage et livraison.
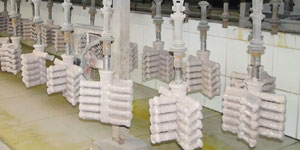
Certifié ITAF16949. Service de casting supplémentaire inclus coulée d'investissement,moulage en sable,Coulée par gravité, Coulée de mousse perdue,Coulée centrifuge,Coulée sous vide,Moulage de moule permanentLes capacités comprennent l'EDI, l'assistance technique, la modélisation solide et le traitement secondaire.
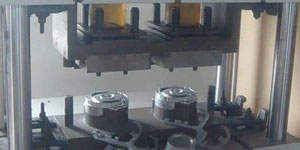
Industries de moulage Études de cas de pièces pour : voitures, vélos, avions, instruments de musique, motomarines, appareils optiques, capteurs, modèles, appareils électroniques, boîtiers, horloges, machines, moteurs, meubles, bijoux, gabarits, télécommunications, éclairage, appareils médicaux, appareils photographiques, Robots, Sculptures, Équipement de sonorisation, Équipement de sport, Outillage, Jouets et plus encore.
Que pouvons-nous vous aider à faire ensuite ?
∇ Aller à la page d'accueil pour Moulage sous pression Chine
→Pièces de fonderie-Découvrez ce que nous avons fait.
→Conseils à propos de Services de moulage sous pression
By Fabricant de moulage sous pression Minghe |Catégories : Articles utiles |Matières Mots clés: Moulage d'aluminium, Moulage de zinc, Coulée de magnésium, Moulage de titane, Fonderie en acier inoxydable, Coulée de laiton,Coulée de bronze,Vidéo de casting,Historique de l'entreprise,Moulage sous pression en aluminium |Commentaires fermés