Qu'est-ce que le moulage sous pression ? Qu'est-ce que le processus de moulage sous pression ?
La coulée à haute pression est une sorte de méthode de coulée spéciale avec moins de coupe et aucune coupe qui s'est développée rapidement dans la technologie moderne de traitement des métaux. C'est un processus dans lequel le métal en fusion est versé dans un moule sous haute pression et à grande vitesse, et cristallisé et solidifié sous haute pression pour former un moulage. Haute pression et haute vitesse sont les principales caractéristiques de la coulée haute pression. La pression couramment utilisée est de dizaines de mégapascals, la vitesse de remplissage (vitesse de la porte interne) est d'environ 16 à 80 m/s et le temps nécessaire au métal en fusion pour remplir la cavité du moule est extrêmement court, environ 0.01 à 0.2 seconde. Étant donné que les produits fabriqués par cette méthode présentent les avantages d'une efficacité de production élevée, de procédures simples, de niveaux de tolérance plus élevés pour les moulages, d'une bonne rugosité de surface et d'une résistance mécanique élevée, il peut économiser de nombreuses procédures et équipements d'usinage, économiser des matières premières, etc. , il est donc devenu un casting Une partie importante de l'industrie.
Les principaux paramètres de processus du processus de moulage sous pression
1. Introduction au processus de moulage sous pression
- R : Le processus de moulage sous pression est un processus de combinaison organique des trois éléments de la machine de moulage sous pression, du moule de moulage sous pression et de l'alliage de moulage sous pression.
- B : Le processus de remplissage du métal dans la cavité pendant le moulage sous pression est un processus d'équilibrage dynamique des facteurs de processus tels que la pression, la vitesse, la température et le temps.
- C : Ces facteurs de processus se limitent mutuellement et se complètent mutuellement. Ce n'est qu'en sélectionnant et en ajustant correctement ces facteurs pour les rendre coordonnés que les résultats attendus peuvent être obtenus. Dans le processus de moulage sous pression, non seulement l'aptitude au traitement de la structure de moulage, mais également la nature avancée du moule, peuvent être obtenues. Les performances et la structure de la machine de moulage sous pression sont excellentes, l'adaptabilité de la sélection de l'alliage de moulage sous pression et la standardisation du processus de fusion. Une plus grande attention devrait être accordée à l'effet important de la pression, de la vitesse et du temps sur la qualité des moulages.
2. Pression
L'existence de la pression est la principale caractéristique qui distingue le processus de moulage sous pression des autres méthodes de moulage. La pression est le facteur qui permet aux pièces moulées d'obtenir une structure compacte et un contour clair ; La pression peut être exprimée en force d'injection et en pression spécifique.
2.1 Force d'injection
La force d'injection est la force qui pousse le mouvement du piston d'injection dans le mécanisme d'injection du Moulage sous pression machine. La force d'injection est un paramètre principal reflétant la fonction de la machine de moulage sous pression. La taille de la force d'injection est déterminée par la section transversale du cylindre d'injection et la pression du fluide de travail dans la chambre d'injection. La formule de la force d'injection est la suivante : F pression = P liquide XA cylindre
2.2 Pression spécifique
La pression du métal en fusion dans la chambre de pression par unité de surface est appelée pression spécifique. La pression spécifique est le rapport de la force d'injection à la section transversale de la chambre de pression. La formule de calcul est la suivante : P ratio = P injection / A chambre
La pression spécifique est la méthode d'expression de la force réelle du métal en fusion à chaque étape du processus de remplissage et reflète le concept de la force du métal en fusion à chaque étape du remplissage et lorsque le métal s'écoule à travers différentes sections transversales. domaines. La pression spécifique pendant le remplissage est appelée pression spécifique de remplissage ou pression spécifique d'injection. La pression spécifique dans la phase de suralimentation est appelée pression spécifique de suralimentation. Les grandeurs des deux pressions spécifiques sont également déterminées en fonction de la force d'injection.
2.3 Le rôle et l'influence de la pression
- A: La pression spécifique de remplissage est de surmonter la résistance à l'écoulement dans le système de porte et la cavité, en particulier la résistance à la porte intérieure, de sorte que le flux de liquide métallique puisse atteindre la vitesse de porte intérieure requise.
- B : La pression de suralimentation et la pression spécifique déterminent la pression sur le métal solidifié et la force de gonflement formée à ce moment. L'influence de la pression spécifique sur les propriétés mécaniques de la coulée : pression spécifique accrue, cristaux fins et couches à grains fins accrues.
- C : Effet sur les conditions de remplissage : L'alliage fondu remplit la cavité sous haute pression spécifique, la température de l'alliage augmente et la fluidité s'améliore, ce qui est bénéfique pour l'amélioration de la qualité des pièces moulées.
3. La vitesse
Pendant le processus de moulage sous pression, la vitesse d'injection est directement affectée par la pression et, avec la pression, elle joue un rôle important dans la qualité interne, les exigences de surface et la clarté des contours de la pièce moulée. La pression est la représentation de base de la vitesse qui est divisée en deux types : la vitesse de poinçonnage et la vitesse d'entrée.
3.1 La relation entre la vitesse du coup de poing et la vitesse des rapports sexuels
Selon le principe de continuité, en même temps, le volume du flux de métal s'écoulant à travers le liquide d'alliage avec la section transversale de la chambre de pression F1 à la vitesse V1 doit être égal au volume du liquide d'alliage circulant à travers la grille intérieure avec la section transversale F2 à la vitesse V2 F1 tir de la chambre V1 = Dans F2 et dans V2. Par conséquent, plus la vitesse d'injection du marteau d'injection est élevée, plus le métal s'écoulant à travers la grille est élevé.
3.2 Vitesse d'injection
- R : La vitesse d'injection est divisée en deux niveaux. La vitesse d'injection de premier niveau est également appelée vitesse d'injection lente. Ce niveau de vitesse fait référence à la vitesse de déplacement du poinçon depuis le mouvement initial jusqu'à ce que le poinçon envoie le métal en fusion dans la pièce dans la porte intérieure. A ce stade, il est nécessaire de remplir la chambre de pression avec le métal en fusion dans la chambre de pression, selon le principe de ne pas trop réduire la température du liquide d'alliage, mais aussi d'aider à éliminer le gaz dans la chambre de pression.
- B : La vitesse d'injection secondaire est également appelée vitesse d'injection rapide. Cette vitesse est déterminée par les caractéristiques de la machine de moulage sous pression. La vitesse d'injection maximale donnée par la machine de coulée sous pression est généralement comprise entre 4 et 5 m/s.
3.3 Le rôle et l'influence de la vitesse d'injection rapide
L'effet et l'influence de la vitesse d'injection rapide sur les propriétés mécaniques des alliages, augmente la vitesse d'injection, convertit l'énergie cinétique en énergie thermique, améliore la fluidité de l'alliage fondu, aide à éliminer les défauts tels que les marques d'écoulement, les barrières froides et améliore les propriétés mécaniques et qualité de surface, mais lorsque la vitesse est trop rapide, l'alliage fondu sera brumeux et mélangé avec du gaz, entraînant un piégeage et une dégradation graves des propriétés mécaniques.
3.4 Vitesse de la porte intérieure
La vitesse linéaire lorsque le métal en fusion pénètre dans la grille interne et est introduit dans la cavité est appelée vitesse de grille interne; la plage habituelle de la vitesse de la porte intérieure est de 15 à 70 m/s. La vitesse de la grille intérieure a une grande influence sur les propriétés mécaniques de la coulée. Si la vitesse de la grille intérieure est trop faible, la résistance de la coulée diminue ; la vitesse augmente, la force augmente ; la vitesse est trop élevée et la force diminue.
4. Températures
Dans le processus de moulage sous pression, la température joue un rôle important dans l'état thermique du processus de remplissage et l'efficacité de l'opération. La température mentionnée dans le moulage sous pression fait référence à la coulée, à la température et à la température du moule. Le contrôle de la température est un facteur industriel important pour obtenir de bonnes pièces moulées. La température de coulée du métal en fusion fait référence à la température moyenne lorsqu'il pénètre dans la cavité depuis la chambre de pression. Parce qu'il n'est pas pratique de mesurer la température du métal en fusion dans la chambre de remplissage, elle est généralement exprimée comme la température du four de maintien.
4.1 Le rôle et l'influence de la température de coulée
L'influence de la température de l'alliage sur les propriétés mécaniques des pièces moulées. Au fur et à mesure que la température de l'alliage augmente. Les performances mécaniques se sont améliorées, mais après une certaine limite, les performances se détériorent, les principales raisons sont :
- R : La solubilité du gaz dans l'alliage augmente avec l'augmentation de la température. Bien que le gaz se soit dissous dans l'alliage, il est difficile de précipiter pendant le processus de moulage sous pression, ce qui affecte les propriétés mécaniques.
- B : La teneur en fer augmente avec l'augmentation de la température de l'alliage, ce qui réduit la fluidité, les cristaux grossiers et détériore les performances
- C : Les alliages d'aluminium et de magnésium s'oxydent davantage avec l'augmentation de la température, les inclusions oxydantes et la détérioration des propriétés de l'alliage.
4.2 Le rôle et l'influence de la température du moule
Pendant le processus de moulage sous pression, le moule nécessite une certaine température. La température du moule est un autre facteur important dans le processus de moulage sous pression, qui joue un rôle important dans l'amélioration de l'efficacité de la production et l'obtention de moulages de haute qualité.
Pendant le processus de remplissage, la température du moule a une grande influence sur la température du liquide métallique, la viscosité, la fluidité, le temps de remplissage, l'état du flux de remplissage direct, etc. Lorsque la température du moule est trop basse, la couche de surface est condensée et la vitesse élevée le flux de liquide s'interrompt à nouveau, ce qui entraîne une couche de surface. Défauts, même si la température de moulage est trop élevée, bien qu'il soit avantageux d'obtenir une surface lisse de la pièce moulée, il est facile de rétrécir et de bosseler
La température du moule a un effet significatif sur la vitesse de refroidissement, l'état cristallin et la contrainte de retrait de l'alliage fondu.
Si la température du moule est trop basse, la contrainte de retrait augmentera et le moulage est sujet aux fissures.
La température du moule a une grande influence sur la durée de vie du moule. Les changements de température intenses forment un état de contrainte complexe, et les changements de contrainte fréquents provoquent des fissures précoces.
La température du moule a un effet sur le niveau de tolérance dimensionnelle de la pièce moulée. Si la température du moule est stable, le retrait dimensionnel de la pièce moulée est également stable et le niveau de tolérance dimensionnelle est également amélioré.
5. temps
Le « temps » dans le processus de moulage sous pression est le temps de remplissage, le temps de montée en pression, le temps de maintien de la pression et le temps de rétention du moule. Ces "temps" sont tous les trois facteurs de pression, vitesse et température, ainsi que les propriétés physiques du métal en fusion. , Structure de coulée (en particulier épaisseur de paroi), structure de moule (en particulier système de coulée et système de trop-plein) et autres résultats complets.
5.1 Temps de remplissage
Le temps nécessaire pour que le métal en fusion pénètre dans la cavité sous pression jusqu'à ce qu'il soit rempli est appelé temps de remplissage. Le temps de remplissage des pièces galvanisées est de 0.02S et le temps de remplissage des pièces d'injection de carburant est de 0.04S.
5.2 Temps de remplissage
Le temps d'établissement de la pression de suralimentation fait référence à la phase de suralimentation du métal en fusion dans le processus de remplissage, à partir du moment où la cavité est remplie, jusqu'à ce que la pression de suralimentation atteigne une valeur prédéterminée, c'est-à-dire de l'augmentation de la pression spécifique d'injection à l'augmentation Le temps qu'il faut pour que la pression s'accumule
5.3 Temps de maintien
Une fois que le métal en fusion a rempli la cavité, la période de temps pendant laquelle le métal en fusion est solidifié sous l'action de la pression de suralimentation est appelée temps de maintien. La fonction du temps de maintien est de faire en sorte que le poinçon d'injection transfère la pression à travers le matériau restant non solidifié et le métal non solidifié dans la partie porte vers la cavité, de sorte que le métal solidifié cristallise sous la pression pour obtenir une coulée dense.
3. Conception de moulage sous pression
Afin d'éviter fondamentalement l'apparition de produits défectueux et de produire en série des pièces moulées sous pression à faible coût, la conception des pièces moulées sous pression doit être adaptée à la production par moulage sous pression. Une bonne conception de moulage sous pression peut assurer la durée de vie, la production et la fiabilité de la production du moule. Avec un bon taux de rendement, ce qui suit expliquera les principes de conception et les exigences de la structure et du processus de moulage sous pression.
1. Évitez le concave intérieur et minimisez le nombre de tractions latérales lors de la conception
2. Conception de l'épaisseur de paroi des pièces moulées sous pression
L'épaisseur de paroi des pièces moulées sous pression est généralement de 2 à 5 mm. On considère généralement qu'une épaisseur de paroi de 7 mm ou plus n'est pas bonne car sa résistance diminue avec l'augmentation de l'épaisseur de paroi. En outre, la conception de l'épaisseur de paroi doit autant que possible suivre le principe d'une épaisseur de paroi égale, principalement pour éviter que la grande différence entre la contrainte de retrait générée par les joints chauds locaux et différentes épaisseurs ne provoque des pores internes, des déformations, des fissures et d'autres défauts. .
3. Conception de coin rond de moulage sous pression
À l'exception des exigences d'appariement spéciales, toutes les parties du moulage doivent être conçues avec des coins arrondis. La fonction des coins arrondis est d'éviter la concentration des contraintes et la fissuration, tout en prolongeant la durée de vie du moule. De plus, lorsque les pièces ont des exigences de traitement de surface, les coins arrondis peuvent être uniformément revêtus. Étage.
4. Conception de l'angle de dépouille du moulage sous pression
Le rôle de l'angle de dépouille est de faciliter le démoulage du produit, de réduire la force de serrage des pièces et d'éviter que les pièces ne se tendent. L'inclinaison minimale des pièces moulées sous pression est indiquée dans le tableau suivant, et la plus grande inclinaison doit être prise si elle est autorisée. , La plage générale est de 1 à 3 degrés d'un côté.
5. La conception de la position d'éjection du processus de moulage sous pression
Une fois le moule ouvert lors du processus de moulage sous pression, le produit est enroulé sur le moule mobile et doit être éjecté par l'éjecteur du moule. Par conséquent, le produit doit avoir suffisamment d'espace pour placer la tige d'éjection. Le diamètre de la tige d'éjection du produit moulé sous pression est généralement supérieur à 5 mm et inférieur à 5 mm. Il est souvent cassé pendant la production, il n'est donc pas recommandé. Lors de la conception de produits moulés sous pression, déterminez s'il y a suffisamment d'espace et de position d'éjection. Essayez d'éviter d'utiliser un dé à coudre de forme spéciale et utilisez un dé à coudre rond. Dans le même temps, faites attention à la position du dé à coudre et du mur. Distance suffisante, généralement supérieure à 3 mm.
6. Réduire la conception du traitement ultérieur des pièces moulées sous pression
Les pièces moulées sous pression peuvent atteindre une précision dimensionnelle élevée, de sorte que la plupart des surfaces et des pièces ne nécessitent pas de traitement mécanique et peuvent être directement assemblées et utilisées. Dans le même temps, le traitement mécanique n'est pas pris en charge pour les deux raisons suivantes. La première est que la surface de la pièce moulée est dure et résistante à l'usure, et elle sera perdue après le traitement. Cette couche refroidie, la seconde est qu'il y a généralement des pores à l'intérieur du moulage sous pression. Les petits pores dispersés n'affectent pas l'utilisation. Après le traitement, les pores sont exposés pour affecter l'apparence et la fonction d'utilisation. Même s'il existe des exigences particulières nécessitant un traitement mécanique, il doit être utilisé. Contrôlez raisonnablement la surépaisseur d'usinage, réduisez le temps d'usinage et le risque de fuite de trous d'air. Généralement, la surépaisseur d'usinage est contrôlée en dessous de 0.8. Afin de minimiser le traitement mécanique, il est nécessaire de formuler la tolérance du dessin de manière raisonnable pour assurer l'installation des pièces. Une plage de tolérance inappropriée augmentera l'usinage ultérieur. Deuxièmement, une conception raisonnable réduit le rétrécissement et la déformation des pièces. Troisièmement, des trous de montage inclinés peuvent être envisagés pour les trous en forme de bout.
7. Conception intégrée dans la conception de moulage sous pression
Des inserts métalliques ou non métalliques peuvent être coulés dans des pièces moulées sous pression, principalement pour améliorer la résistance locale et la résistance à l'usure ou pour former des cavités internes difficiles à former. La partie où l'insert est noyé dans le métal doit être conçue pour empêcher la rotation et empêcher le mouvement axial. Considérez la commodité d'insérer l'insert dans le moule et la stabilité de résister à l'impact du métal en fusion
5. Cas de résolution des problèmes de qualité des moulages sous pression.
Le problème de ne pas voir la lumière dans le traitement de 100 visages de la coque
1.1 État des lieux
1.2 La raison pour laquelle le traitement ne voit pas la lumière
1.2.1 Lors du traitement de la coque, utilisez d'abord les faces d'extrémité B1, B2 et B3 comme surface de référence pour traiter la surface de matrice mobile, puis utilisez la surface de matrice mobile traitée comme surface de référence pour traiter la surface de matrice statique. Après avoir mesuré la partie invisible, on constate que la surface mobile du moule est un biseau après traitement (comme le montre la figure ci-dessous). Par rapport à la pièce traitée normale, la surface de moule mobile de la pièce invisible est traitée localement de 1 mm de plus. Cela est dû à un serrage incorrect du plan de référence B2 ou à une déformation du plan de référence pendant le traitement.
1.3. Raisons de la déformation du trou de référence B2
1.3.1 L'épaisseur de la fraise de type partiel fait que la face d'extrémité du trou de référence B2 devient plus haute. L'épaisseur de paroi de la partie invisible B2 est de 8 mm et les deux épaisseurs de paroi de la partie traitée normale B sont les mêmes. L'épaisseur du mur change peu. L'épaisseur de la bavure n'est pas la cause de l'augmentation de la surface d'extrémité du trou de référence B2.
1.3.2 Les noyaux des trous B1, B2 et B3 sur le moule ont été réparés et aucun retrait de noyau n'a été constaté. Le problème du retrait du noyau peut être éliminé.
1..3 La bosse au niveau du trou B2 provoque sa déformation. Observez la pièce défectueuse retournée. Il y a de sérieuses bosses au trou B2, et ce n'est pas une nouvelle bosse. La bosse est la cause principale de la déformation au niveau du trou B2.
Conclusion 1.4
Conclusion : En raison de la collision, le trou B2 est déformé du côté du moule statique, ce qui augmente le B2 lorsque la surface mobile du moule est traitée. La surface du moule mobile est transformée en un biseau et le traitement local est de 1 mm de plus; lors du traitement de la surface de moule statique, la surface de moule mobile est utilisée comme plan de référence, la partie de moule statique correspondant à la position de traitement multiple du moule mobile n'a pas de quantité de traitement, ce qui rend le traitement côté moule statique invisible.
1.5 Mesures d'amélioration
1.5.1 Lors du placement des pièces dans l'atelier de moulage sous pression et l'atelier de nettoyage, placez-les soigneusement et placez-les soigneusement pour éviter de heurter les pièces moulées et suivez strictement le processus. Mettez deux couches de carton entre chaque couche de moulages. Département de stockage et de transport. Pendant le retournement, empêchez le chariot élévateur de heurter les pièces et empêchez les pièces de se cogner en raison de méthodes de transport de fourche inappropriées et d'une vitesse de transport excessive.
1.5.2 Nettoyer les bavures de tronçonnage à temps pour éviter des bavures de tronçonnage trop épaisses.
2.2 Analyse des raisons
2.2.1 Le diamètre du trou de la partie où les pores apparaissent dans le trou 701# de Lishell est q26, le diamètre du trou après traitement est p27.9, la surépaisseur d'usinage est de 0.95 mm, la surépaisseur d'usinage est grande et les pores sont faciles apparaître.
Conclusion 2.3
Conclusion : La température du noyau 701# est trop élevée, elle se trouve dans la cavité profonde et l'échappement est médiocre, et la surépaisseur d'usinage est trop grande, ce qui rend le trou 701# sujet aux pores après le traitement.
2.4 Mesures d'amélioration
2.4.1 Le service technique a conçu pour ajouter de l'eau au trou 701# pour réduire la température à cœur ; changez le dessin du moule, ajoutez une rainure de trop-plein au trou 701 # pour renforcer l'effet d'échappement; modifiez le dessin de base et modifiez la surépaisseur d'usinage de trou 701 # Réduite de 0.9 mm à 0.7 mm.
Veuillez conserver la source et l'adresse de cet article pour réimpression: Qu'est-ce que le moulage sous pression ? Qu'est-ce que le processus de moulage sous pression ?
Minghé Société de moulage sous pression sont dédiés à la fabrication et à la fourniture de pièces de moulage de qualité et de haute performance (la gamme de pièces de moulage sous pression en métal comprend principalement Moulage sous pression à paroi mince,Chambre chaude coulée sous pression,Chambre froide coulée sous pression), Service rond (Service de moulage sous pression,Usinage CNC,Fabrication de moules,Traitement de surface). Tout moulage sous pression en aluminium personnalisé, moulage sous pression en magnésium ou en zamak/zinc et autres exigences en matière de moulages sont invités à nous contacter.
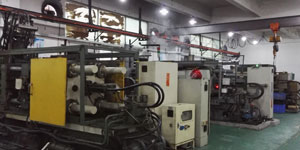
Sous le contrôle des normes ISO9001 et TS 16949, tous les processus sont effectués via des centaines de machines de moulage sous pression avancées, de machines à 5 axes et d'autres installations, allant des blasters aux machines à laver Ultra Sonic.Minghe dispose non seulement d'équipements de pointe, mais également de professionnels équipe d'ingénieurs, d'opérateurs et d'inspecteurs expérimentés pour réaliser la conception du client.
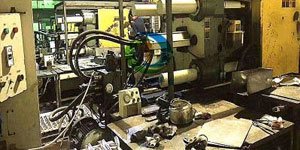
Fabricant sous contrat de moulages sous pression. Les capacités incluent des pièces de moulage sous pression en aluminium à chambre froide à partir de 0.15 lb. jusqu'à 6 lb, configuration à changement rapide et usinage. Les services à valeur ajoutée comprennent le polissage, la vibration, l'ébavurage, le grenaillage, la peinture, le placage, le revêtement, l'assemblage et l'outillage. Les matériaux travaillés comprennent des alliages tels que 360, 380, 383 et 413.
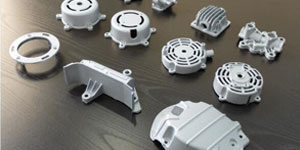
Assistance à la conception de moulage sous pression de zinc/services d'ingénierie simultanés. Fabricant sur mesure de pièces moulées en zinc de précision. Des moulages miniatures, des moulages sous pression à haute pression, des moulages en moules à glissières multiples, des moulages en moules conventionnels, des moulages sous pression unitaires et indépendants et des moulages à cavité scellée peuvent être fabriqués. Les pièces moulées peuvent être fabriquées dans des longueurs et des largeurs allant jusqu'à 24 po avec une tolérance de +/- 0.0005 po.
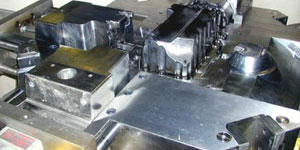
Fabricant certifié ISO 9001 : 2015 de magnésium moulé sous pression, les capacités incluent le moulage sous pression de magnésium sous pression jusqu'à une chambre chaude de 200 tonnes et une chambre froide de 3000 tonnes, la conception d'outillage, le polissage, le moulage, l'usinage, la peinture en poudre et liquide, une assurance qualité complète avec des capacités CMM , assemblage, emballage et livraison.
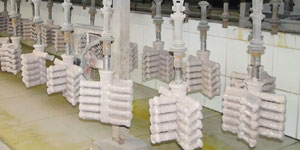
Certifié ITAF16949. Service de casting supplémentaire inclus coulée d'investissement,moulage en sable,Coulée par gravité, Coulée de mousse perdue,Coulée centrifuge,Coulée sous vide,Moulage de moule permanentLes capacités comprennent l'EDI, l'assistance technique, la modélisation solide et le traitement secondaire.
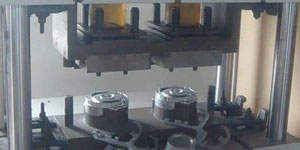
Industries de moulage Études de cas de pièces pour : voitures, vélos, avions, instruments de musique, motomarines, appareils optiques, capteurs, modèles, appareils électroniques, boîtiers, horloges, machines, moteurs, meubles, bijoux, gabarits, télécommunications, éclairage, appareils médicaux, appareils photographiques, Robots, Sculptures, Équipement de sonorisation, Équipement de sport, Outillage, Jouets et plus encore.
Que pouvons-nous vous aider à faire ensuite ?
∇ Aller à la page d'accueil pour Moulage sous pression Chine
→Pièces de fonderie-Découvrez ce que nous avons fait.
→Conseils à propos de Services de moulage sous pression
By Fabricant de moulage sous pression Minghe |Catégories : Articles utiles |Matières Mots clés: Moulage d'aluminium, Moulage de zinc, Coulée de magnésium, Moulage de titane, Fonderie en acier inoxydable, Coulée de laiton,Coulée de bronze,Vidéo de casting,Historique de l'entreprise,Moulage sous pression en aluminium |Commentaires fermés