Le processus de fusion de la ferraille ductile trempée
Dans le processus de production traditionnel de la fonte ductile, environ 10 % des déchets de carbone sont généralement utilisés pour les ingrédients. Cet article ne traite que de certaines questions auxquelles il convient d'accorder une attention particulière dans le processus de production après avoir augmenté la proportion de déchets de carbone utilisés dans la production de fonte ductile dans un four à induction. Selon la pratique de production, l'auteur fait valoir ses propres vues pour la référence de ses collègues.
Le choix de la recharge
(1) ferraille
Les déchets utilisés dans la production de fonte ductile doivent être des déchets de carbone. Il ne doit pas contenir d'éléments qui gênent la graphitisation, comme le chrome. Il ne doit pas contenir d'éléments d'alliage anti-sphéroïdisation. Les morceaux de ferraille doivent être d'environ 30 % sous forme d'écailles épaisses, qui peuvent être déposées à plat dans le four.
(2) Recarburateur
- ① Coca de haute qualité. La teneur en soufre doit être faible, la granulation est de 60 à 80 mm et sa résistance est élevée. Il ne peut pas être écrasé après avoir été brûlé.
- ②Bloc d'électrode usé. Il est préférable d'avoir une certaine longueur pour faciliter la découpe dans le fer en fusion.
(3) Fonte
Il est principalement utilisé pour ajuster la teneur en carbone du fer en fusion. J'espère utiliser de la fonte brute à haute teneur en carbone et à faible teneur en soufre avec wC> 4%. La teneur en silicium de la fonte brute est plus élevée de manière appropriée et la production de fonte nodulaire peut être moins riche en ferrosilicium.
(4) Sphéroïdisation
L'agent de sphéroïdisation et l'inoculant sont utilisés selon les techniques traditionnelles, et sont déterminés en fonction des conditions réelles de chaque usine.
Sentait
Processus de fusion : bloc de coke + ferraille → bloc d'électrodes → augmentation de la température → retirer le bloc de coke et le bloc d'électrodes → échantillonner et analyser la teneur en carbone → fonte brute → matériau de retour → échantillonner et analyser Si, Mn → augmentation de la température → ferromanganèse + ferrosilicium → décharge →Inoculation + sphéroïdisation → coulage.
Les précautions pendant le processus de fusion sont les suivantes :
- Le bloc de coke est installé en bas du four, le but est de créer un temps de trempage plus long du bloc de coke dans la fonte en fusion. La quantité de bloc de coke est d'environ 5% de la ferraille. Environ 50 % de la ferraille est fondue et le coke doit être recouvert de ferraille en flocons épais. Il est également possible d'utiliser des blocs d'électrodes usagées de 60-80 mm à la place du coke à installer en fond de four comme recarburateur, à plus faible teneur en soufre, ce qui est plus avantageux pour obtenir une fonte ductile de haute qualité.
- La proportion de ferraille utilisée est principalement déterminée par l'efficacité de l'augmentation du carbone. Pour les fabricants qui commencent à utiliser cette méthode pour produire de la fonte ductile, environ 30% c'est mieux. Après avoir amélioré l'efficacité d'augmentation du carbone, augmentez progressivement la proportion de ferraille. L'utilisation excessive de ferraille d'acier, si l'efficacité d'augmentation du carbone n'est pas élevée, affectera l'équivalent carbone-silicium du produit final.
- Une fois la ferraille fondue, insérez la tige d'électrode pour augmenter de manière appropriée la température dans le four et augmenter l'efficacité du carbone. Cependant, la température du four est trop élevée, ce qui augmente la consommation d'énergie et nuit également au revêtement du four.
- Une fois que la teneur en carbone est estimée suffisamment élevée, retirez le bloc de coke et la tige d'électrode, puis échantillonnez et analysez la teneur en carbone.
- Selon les résultats de l'analyse, calculez la quantité de fonte ajoutée et la quantité de fonte ductile recyclée utilisée.
- Déterminez si la quantité totale de fer fondu peut être constituée avec le matériau remis à neuf en fonction de l'estimation de la teneur en silicium.
- Une fois le matériau de réchauffage fondu, prélevez un échantillon et analysez la teneur en Si, Mn et autres éléments d'alliage.
- Augmentez correctement la température de la fonte en fusion, complétez les éléments d'alliage en fonction des résultats d'analyse et ajoutez du ferrosilicium avant que le four n'atteigne la température du four.
- Le ferrosilicium est fondu jusqu'à l'état fondu et est immédiatement libéré du four.
- La sphéroïdisation, l'inoculation et la coulée sont effectuées comme d'habitude.
Calcul de l'ajustement de la composition
Comme nous le savons tous, les propriétés mécaniques de la fonte ductile dépendent principalement de la composition chimique, de la vitesse de refroidissement (fonte ductile brute) et du processus de traitement thermique. La composition chimique est la cause interne, la racine et la variable, presque chaque four est différent. Par conséquent, il est nécessaire de renforcer la détection des composants chimiques et de procéder à des ajustements minutieux, et il n'est pas approprié d'adopter une "production à rapport fixe". Dans la composition chimique, l'équivalent carbone est particulièrement important. En particulier, la fonte nodulaire produite en utilisant de la ferraille d'acier comme charge principale, car l'efficacité de l'augmentation du carbone est difficile à contrôler et l'équivalent carbone fluctue considérablement, une attention particulière doit donc être accordée à l'ajustement de l'équivalent carbone.
- Calculez la quantité de fonte ajoutée. Calculer la quantité de fonte ajoutée en fonction de l'analyse de la teneur en carbone. En fait, il s'agit d'ajuster l'équivalent carbone de la fonte nodulaire de sorte que l'équivalent carbone de la masse fondue formée à la fois par la fonte brute et la ferraille atteigne l'équivalent carbone requis pour la fonte nodulaire. La quantité de fonte ajoutée = la quantité de ferraille ajoutée × (la teneur en carbone requise de la fonte nodulaire - analyse de la teneur en carbone) / (la teneur en carbone de la fonte brute - la teneur en carbone requise de la fonte nodulaire)
- Calcul de la quantité ajoutée de fonte ductile recyclée L'équivalent carbone de la fonte ductile recyclée est fondamentalement normal, et la quantité ajoutée n'est pas importante. Par conséquent, après l'ajout de la fonte réchauffée, la teneur en carbone de la fonte en fusion dans l'ensemble du four est qualifiée. La quantité de fonte nodulaire ajoutée au four = la quantité totale de charge - la quantité de ferraille - la quantité de racleur fer ajouté
- Estimation de la teneur en silicium La formule de calcul est la suivante : Teneur en silicium ≈ ((quantité d'ajout de ferraille + fonte brute + fonte nodulaire) × teneur en silicium / charge totale] × 100 % ≤ teneur en silicium admissible de la fonte contenu est trop élevé, ajoutez une petite quantité de fonte ductile recyclée et utilisez la même quantité de fonte brute et de ferraille avec un rapport de 9:1 pour compenser la charge totale.
- Calcul de l'ajout de ferrosilicium La formule de calcul est la suivante :La quantité de ferrosilicium ajouté = [quantité totale de charge × (teneur en silicium requise de la fonte ductile-teneur en silicium augmentée par inoculation-teneur en silicium augmentée par sphéroïdisation-analyse de la teneur en silicium)] / teneur en silicium du ferrosilicium
- La quantité de manganèse et d'autres éléments d'alliage ajoutés est calculée comme suit : La quantité de fer allié ajoutée = la quantité totale de charge × (la teneur en alliage requise de la teneur en fer ductile d'analyse)/la teneur en élément d'alliage dans le fer allié La perte par combustion n'est pas inclus dans les calculs ci-dessus.
En effet, la fonte nodulaire est fondue dans le four à induction et les éléments ne brûlent pas beaucoup, et le fer est également brûlé dans une certaine mesure. Si vous rencontrez des circonstances particulières, vous devez faire attention à la combustion.
Exemple d'application de réglage de la composition :
- En utilisant un four électrique à induction de 1 t pour produire de la fonte ductile perlitique QT800-2, le poids de la coulée est de 1000 kg.
- « La composition chimique de contrôle est : wC=3.5 %, wSi=2.5 %, wMn=0.5 %, wP<0.07 %, wS<0.02 %, wMg=0.03%0.06%, wRE=0.02%~0.04%.
- Après la recarburation, la teneur en carbone des "ferrailles d'acier fondu" dans le four est de 2.5%.
- La quantité de fonte ajoutée = 300 × (3.5%-2.5%) / (4%-3.5%) = 600 (kg)
- La quantité de fonte nodulaire utilisée dans le four = 1000-300-600=100 (kg)
- Teneur en silicium estimée = (300×0.3%+600×1.8%+100×2.5%)×100%=1.42%
- Si la teneur en silicium du noduliseur est de 0.6% et la teneur en silicium de l'inoculant est de 0.4%, la teneur en silicium du fer fondu d'origine doit être de 1.5%, ce qui est supérieur à la teneur en silicium estimée. Pour cela, la fonte Z18 peut être utilisée pour ajuster l'équivalent carbone, et la fonte ductile recuite peut être utilisée pour compléter la quantité totale de charge.
- La teneur en silicium est de 1.38% et la teneur en manganèse est de 0.15% avant la sortie du four.
- Quantité de ferrosilicium ajouté = [1000 (2.5%-0.6%-0.4%-1.38 %)] / 75% = 1.6kg
- Quantité ajoutée de ferromanganèse = [1000 (0.5%-0.15%)] / 65% = 5.4kg
4. Conclusions
Dans la production de four électrique à induction, nous utilisons de la ferraille pour produire QT800-2, la résistance est de 800~1000MPa et l'allongement est supérieur à 4%.
À l'heure actuelle, il y a beaucoup de ferraille sur le marché, la fonte est chère et la fonte de haute qualité est encore plus rare. Par conséquent, nous suggérons que les fabricants ayant des tâches de production de fonte nodulaire puissent se référer à l'hypothèse mentionnée ci-dessus et à « substituer l'acier au fer » pour produire de la fonte nodulaire.
Veuillez conserver la source et l'adresse de cet article pour réimpression:Le processus de fusion de la ferraille ductile trempée
Minghé Société de moulage sous pression sont dédiés à la fabrication et à la fourniture de pièces de moulage de qualité et de haute performance (la gamme de pièces de moulage sous pression en métal comprend principalement Moulage sous pression à paroi mince,Chambre chaude coulée sous pression,Chambre froide coulée sous pression), Service rond (Service de moulage sous pression,Usinage CNC,Fabrication de moules,Traitement de surface). Tout moulage sous pression en aluminium personnalisé, moulage sous pression en magnésium ou en zamak/zinc et autres exigences en matière de moulages sont invités à nous contacter.
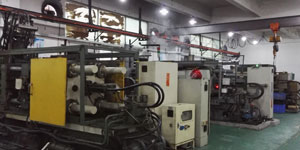
Sous le contrôle des normes ISO9001 et TS 16949, tous les processus sont effectués via des centaines de machines de moulage sous pression avancées, de machines à 5 axes et d'autres installations, allant des blasters aux machines à laver Ultra Sonic.Minghe dispose non seulement d'équipements de pointe, mais également de professionnels équipe d'ingénieurs, d'opérateurs et d'inspecteurs expérimentés pour réaliser la conception du client.
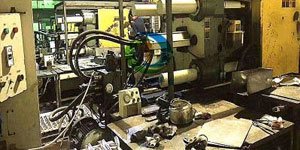
Fabricant sous contrat de moulages sous pression. Les capacités incluent des pièces de moulage sous pression en aluminium à chambre froide à partir de 0.15 lb. jusqu'à 6 lb, configuration à changement rapide et usinage. Les services à valeur ajoutée comprennent le polissage, la vibration, l'ébavurage, le grenaillage, la peinture, le placage, le revêtement, l'assemblage et l'outillage. Les matériaux travaillés comprennent des alliages tels que 360, 380, 383 et 413.
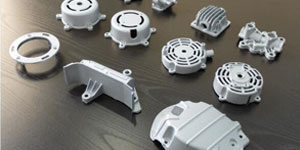
Assistance à la conception de moulage sous pression de zinc/services d'ingénierie simultanés. Fabricant sur mesure de pièces moulées en zinc de précision. Des moulages miniatures, des moulages sous pression à haute pression, des moulages en moules à glissières multiples, des moulages en moules conventionnels, des moulages sous pression unitaires et indépendants et des moulages à cavité scellée peuvent être fabriqués. Les pièces moulées peuvent être fabriquées dans des longueurs et des largeurs allant jusqu'à 24 po avec une tolérance de +/- 0.0005 po.
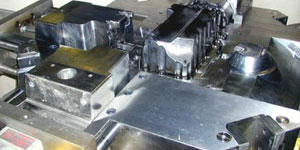
Fabricant certifié ISO 9001 : 2015 de magnésium moulé sous pression, les capacités incluent le moulage sous pression de magnésium sous pression jusqu'à une chambre chaude de 200 tonnes et une chambre froide de 3000 tonnes, la conception d'outillage, le polissage, le moulage, l'usinage, la peinture en poudre et liquide, une assurance qualité complète avec des capacités CMM , assemblage, emballage et livraison.
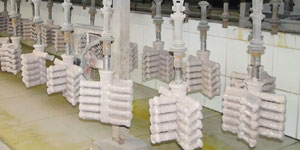
Certifié ITAF16949. Service de casting supplémentaire inclus coulée d'investissement,moulage en sable,Coulée par gravité, Coulée de mousse perdue,Coulée centrifuge,Coulée sous vide,Moulage de moule permanentLes capacités comprennent l'EDI, l'assistance technique, la modélisation solide et le traitement secondaire.
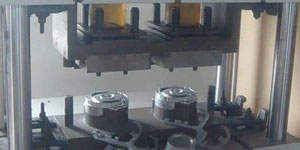
Industries de moulage Études de cas de pièces pour : voitures, vélos, avions, instruments de musique, motomarines, appareils optiques, capteurs, modèles, appareils électroniques, boîtiers, horloges, machines, moteurs, meubles, bijoux, gabarits, télécommunications, éclairage, appareils médicaux, appareils photographiques, Robots, Sculptures, Équipement de sonorisation, Équipement de sport, Outillage, Jouets et plus encore.
Que pouvons-nous vous aider à faire ensuite ?
∇ Aller à la page d'accueil pour Moulage sous pression Chine
→Pièces de fonderie-Découvrez ce que nous avons fait.
→Conseils à propos de Services de moulage sous pression
By Fabricant de moulage sous pression Minghe |Catégories : Articles utiles |Matières Mots clés: Moulage d'aluminium, Moulage de zinc, Coulée de magnésium, Moulage de titane, Fonderie en acier inoxydable, Coulée de laiton,Coulée de bronze,Vidéo de casting,Historique de l'entreprise,Moulage sous pression en aluminium |Commentaires fermés