Les avantages et les inconvénients du processus de moulage d'aluminium
En raison des différents éléments de chaque groupe d'alliages d'aluminium, les propriétés physiques et chimiques des alliages sont différentes. Le processus de cristallisation est également différent. Par conséquent, il doit viser les caractéristiques de l'alliage d'aluminium. Choix raisonnable de la méthode de coulée. Afin d'éviter ou de réduire l'apparition de défauts de coulée dans la plage autorisée, de manière à optimiser la coulée.
Performance du processus de moulage en alliage d'aluminium
Performances du processus de coulée en alliage d'aluminium. Il est généralement compris comme une combinaison des propriétés les plus importantes dans le processus de remplissage, de cristallisation et de refroidissement, telles que la fluidité, le retrait, l'étanchéité à l'air, la contrainte de coulée et l'absorption d'air. Ces caractéristiques de l'alliage d'aluminium dépendent de la composition de l'alliage. Mais il est également lié aux facteurs de coulée, à la complexité du moule de température de chauffage de l'alliage, au système de colonne montante et à la forme de la porte.
(1) Liquidité
La fluidité fait référence à la capacité des caractéristiques de remplissage de liquide d'alliage. La fluidité détermine si l'alliage peut couler des pièces moulées complexes. De nombreux facteurs influent sur la liquidité. Les principaux facteurs sont la composition, la température et les particules solides d'oxydes métalliques, de composés métalliques et d'autres polluants dans l'alliage liquide, mais les facteurs objectifs externes sont la température de coulée et la pression d'écoulement (communément appelée tête d'injection condensée).
(2) Contractilité
Le retrait est l'une des principales caractéristiques des alliages d'aluminium coulé. L'alliage est divisé en trois étapes, de la coulée du liquide à la solidification jusqu'à ce qu'il atteigne la température ambiante. Ce sont le retrait liquide, le retrait de solidification et le retrait à l'état solide. Le retrait de l'alliage a une influence décisive sur la qualité de la coulée. Il affecte la taille de la cavité de retrait de la pièce moulée, la formation de fissures de contrainte et le changement de taille. Le rétrécissement du berkelium constant rapide est divisé en rétrécissement corporel et rétrécissement linéaire. Dans la production réelle, le retrait linéaire est généralement utilisé pour améliorer le retrait des alliages d'or. Taille de retrait d'alliage d'aluminium. Généralement exprimé en pourcentage, appelé retrait.
contraction du corps
La contraction corporelle comprend la contraction de liquide et la contraction de solidification.
Liquide d'alliage de coulée de la coulée à la solidification. A la fin de la solidification, il y aura un retrait macroscopique ou microscopique du côté vietnamien. Ce type de rétrécissement macroscopique causé par le rétrécissement est visible à l'œil nu et se divise en rétrécissement concentré et rétrécissement partiel. Le diamètre des pores de la cavité de retrait concentré est grand et concentré. Et ils sont répartis dans la partie supérieure de la coulée ou dans les points chauds épais de la surface. Les cavités de retrait dispersives sont dispersées et fines. La plupart d'entre eux sont répartis dans l'axe de coulée et les joints chauds. Les cratères microscopiques sont difficiles à voir à l'œil nu. La plupart des cavités de retrait microscopiques sont réparties sous les joints de grains ou entre les dendrites des dendrites.
Le retrait et la porosité sont l'un des principaux défauts des moulages. La raison en est que la contraction liquide est supérieure à la contraction nationale. Au cours de la production, on constate que la plage de solidification de l'alliage d'aluminium coulé est plus petite. Plus les cristaux forment des cavités de retrait de Leizhong. Vérifiez la plage de coagulation. Plus les cristaux forment des cavités de retrait dispersives. donc. Dans la conception, l'alliage d'aluminium du joint de coulée doit être conforme au principe de la solidification séquentielle. Le rétrécissement du corps des pièces moulées imprimées lors de la solidification liquide à la main doit être complété par un alliage liquide. Les cavités de retrait et le jeu sont concentrés dans la colonne montante externe de la pièce moulée. Pour les pièces moulées en alliage d'aluminium susceptibles d'être dispersées et lâches. Le nombre d'installations à 100 ports est supérieur à celui des trous de retrait centralisés. Et installez un fer froid à l'endroit où les cristaux sont générés pour augmenter le taux de refroidissement local. Faites-le se solidifier en même temps ou rapidement.
Rétrécissement de ligne
La taille du retrait de ligne affectera directement la qualité de la coulée. Le système se rétrécit et invite les grands. La tendance des pièces moulées en aluminium à produire des fissures et des contraintes est également plus grande : la taille et la forme des pièces moulées deviennent plus grandes après refroidissement.
Pour différents alliages d'aluminium coulé, il existe différents taux de retrait des joints et le même alliage est imprimé. Le casting est différent. Le taux de retrait est également différent. Sur le même casting. Le taux de rétrécissement de sa longueur, de sa largeur et de sa hauteur est également différent. Il doit être déterminé en fonction de la situation spécifique.
(3) Fissuration à chaud
L'apparition de fissures à chaud dans les pièces moulées en aluminium est principalement due à la contrainte de retrait des pièces moulées dépassant la force de liaison entre les grains métalliques. La plupart d'entre eux se produisent le long des joints de grains. On peut voir à partir de la fracture des fissures que le métal au niveau des fissures est souvent oxydé et perd son éclat métallique. Les fissures s'étendent le long du joint de grain, avec une forme en zigzag, une surface large et un intérieur étroit, et certaines pénètrent toute la surface d'extrémité de la pièce moulée.
Différentes pièces moulées en alliage d'aluminium ont une tendance différente à se fissurer. En effet, plus la différence entre la température à laquelle une charpente cristalline complète se forme lors de la solidification de l'alliage d'aluminium coulé et la température de solidification est grande, plus le retrait de l'alliage est important et plus la tendance à la fissuration à chaud est grande. type d'alliage a une tendance à la fissuration à chaud différente en raison de la résistance du moule, de la structure de la coulée, du processus de coulée et d'autres facteurs. Des mesures telles que des moules de coulée régressive ou des systèmes de coulée améliorés en alliage d'aluminium sont souvent utilisées dans la production pour éviter les fissures dans les pièces moulées en aluminium. La méthode de l'anneau de fissure à chaud est généralement utilisée pour détecter les fissures à chaud dans les pièces moulées en aluminium.
(4) Etanchéité à l'air
L'étanchéité à l'air de l'alliage d'aluminium coulé fait référence au degré d'absence de fuite des pièces moulées en aluminium de type cavité sous l'action d'un gaz ou d'un liquide à haute pression. L'étanchéité à l'air caractérise en effet le degré de compacité et de pureté de la structure interne de la coulée.
L'étanchéité à l'air de l'alliage d'aluminium coulé est liée aux propriétés de l'alliage. Plus la plage de solidification de l'alliage est petite, plus la tendance à produire de la porosité est faible. En même temps, plus les pores de précipitation sont petits, plus l'étanchéité à l'air de l'alliage est élevée. L'étanchéité à l'air du même alliage d'aluminium coulé est également liée au processus de coulée. Par exemple, l'abaissement de la température de coulée de l'alliage d'aluminium coulé, le placement de fer froid pour accélérer la vitesse de refroidissement, la solidification et la cristallisation sous pression, etc., peuvent tous rendre l'étanchéité à l'air des pièces moulées en aluminium. améliorer. La méthode d'imprégnation peut également être utilisée pour boucher l'espace de fuite afin d'améliorer l'étanchéité à l'air de la pièce moulée.
(5) Contrainte de coulée
La contrainte de coulée comprend trois types de contrainte, la contrainte de transformation de phase et la contrainte de retrait. Les causes des différents stress ne sont pas les mêmes.
L'étanchéité à l'air de l'alliage d'aluminium coulé est liée aux propriétés de l'alliage. Plus la plage de solidification de l'alliage est petite. La tendance à produire du pin sulfureux est également plus faible. En même temps, il produit de petits stomates. Sinon, l'étanchéité à l'air de l'alliage sera élevée. L'étanchéité à l'air du même alliage d'aluminium coulé est également liée au processus d'inspection de la coulée. Tels que l'abaissement de la température de coulée de l'alliage d'aluminium coulé, le placement de fer froid pour accélérer la vitesse de refroidissement, la solidification et la cristallisation sous pression, etc., peuvent améliorer l'étanchéité à l'air des pièces moulées en aluminium. L'étanchéité au gaz de la coulée peut également être améliorée en comblant l'espace de fuite élevée grâce à la méthode de traitement.
- Contrainte thermique. La contrainte thermique est due à l'épaisseur inégale de la section à l'intersection des différentes formes géométriques de la pièce moulée. Le refroidissement n'est pas quelques raisons. La formation de contraintes de compression dans la pièce mince conduit à des contraintes résiduelles dans la coulée.
- Contraintes croisées. La contrainte de transformation de phase est due à la transformation de phase de certains alliages d'aluminium coulé pendant le processus de refroidissement après la solidification. La taille de la zone au fond de la cour change. Le membre principal est en aluminium. L'épaisseur de paroi de la coulée est inégale. Elle est causée par l'intersection de différentes parties à différents moments.
- Contrainte de retrait. Lorsque la pièce moulée en aluminium rétrécit, elle est gênée par le moule et le noyau, ce qui entraîne une contrainte de traction. Ce type de contrainte est temporaire et les pièces moulées en aluminium disparaîtront automatiquement lorsqu'elles seront sorties de la boîte. Cependant, un temps de déballage inapproprié provoque souvent des fissures à chaud, en particulier pour les alliages d'aluminium moulés en métal qui sont sujets aux fissures à chaud sous de telles contraintes. La contrainte résiduelle dans l'alliage d'aluminium moulé réduit les propriétés mécaniques de l'alliage et affecte la précision d'usinage de la pièce moulée. Les contraintes résiduelles dans les pièces moulées en aluminium peuvent être éliminées par recuit. L'alliage a une bonne conductivité thermique et aucun changement de phase pendant le processus de refroidissement. Tant que la structure de coulée est conçue de manière raisonnable, la contrainte résiduelle de la coulée d'aluminium est généralement faible.
(6) Inhalation
L'alliage d'aluminium absorbe facilement les gaz, ce qui est la principale caractéristique de l'alliage d'aluminium moulé. L'hydrogène produit par la réaction entre les composants de l'aluminium liquide et des alliages d'aluminium et l'humidité contenue dans la charge du four, les produits de combustion des matières organiques et les moules est absorbé par l'aluminium liquide.
Plus la température de l'alliage d'aluminium fondu est élevée, plus l'hydrogène est absorbé. A 700°C, la solubilité de l'hydrogène dans 100g d'aluminium est de 0.5 à 0.9. Lorsque la température monte à 850°C, la solubilité de l'hydrogène augmente de 2 à 3 fois. Lorsque des impuretés de métaux alcalins sont contenues, la solubilité de l'hydrogène dans l'aluminium fondu est considérablement augmentée.
En plus de l'inhalation de l'alliage d'aluminium coulé lors de la fusion, il produit également une inhalation lors du versement dans le moule. Le métal liquide entrant dans le moule diminue avec la température, la solubilité du gaz diminue, et l'excès de gaz est précipité, et il y a une partie du gaz qui ne peut pas s'échapper. Il est laissé dans la coulée pour former des pores, qui sont généralement appelés « trous d'épingle ». Le gaz se combine parfois avec la cavité de rétraction, et le gaz précipité dans l'aluminium fondu reste dans la cavité de rétraction. Si la pression générée par le chauffage des bulles est importante, la surface des pores est lisse et il y a une couche brillante autour des trous ; si la pression générée par les bulles est faible, la surface interne des pores est ridée, ce qui ressemble à des "pieds volants", et il y a des trous de rétrécissement à regarder de plus près. Caractéristiques.
Plus la teneur en argon du liquide d'alliage d'aluminium coulé est élevée, plus il y a de trous d'épingle produits dans la coulée. Les trous d'épingle dans les pièces moulées en aluminium réduisent non seulement l'étanchéité à l'air et la résistance à la corrosion des pièces moulées, mais réduisent également les propriétés mécaniques de l'alliage. Pour obtenir des pièces moulées en aluminium avec pas ou moins de pores, la clé réside dans les conditions de fusion. Si un agent de couverture est ajouté pour la protection pendant la fusion, la quantité d'inhalation de gaz de l'alliage est considérablement réduite. Le raffinage de l'aluminium fondu peut contrôler efficacement la teneur en hydrogène de l'aluminium fondu. La méthode de coulée qui utilise du sable, de l'argile et d'autres matériaux auxiliaires pour fabriquer un moule est appelée coulée au sable. Les matériaux des moules en sable sont collectivement appelés matériaux de moulage. Les moules en sable pour les applications de métaux non ferreux sont faits de sable, d'argile ou d'autres liants et d'eau.
Le processus de formage des pièces moulées en aluminium est un processus d'interaction entre le métal et le moule. Une fois le liquide d'alliage d'aluminium injecté dans le moule, la chaleur est transférée au moule et le moule en sable est soumis aux effets thermiques, mécaniques et chimiques du métal liquide. Par conséquent, afin d'obtenir des moulages de haute qualité, en plus de maîtriser strictement le processus de fusion, il est également nécessaire de concevoir correctement le rapport sable du moule (noyau), les processus de modélisation et de coulée.
3. Moulage de moules en métal
1. Introduction et processus technologique
Le moulage en moule métallique est également appelé moulage en moule dur ou moulage en moule permanent. C'est une méthode de coulée de l'alliage d'aluminium fondu dans un moule en métal pour obtenir des pièces moulées. La plupart des moulages de moules métalliques en alliage d'aluminium utilisent des noyaux métalliques, mais également des noyaux de sable ou des noyaux de coque. Méthode, comparée à la coulée sous pression, le moule en alliage d'aluminium a une longue durée de vie.
2. Avantages du casting
(1) Avantages
Le moule en métal a une vitesse de refroidissement plus rapide et une structure de moulage plus dense, qui peut être renforcée par un traitement thermique, et ses propriétés mécaniques sont environ 15 % plus élevées que celles du moulage au sable. Moulage de moules métalliques, la qualité des moulages est stable, la rugosité de surface est meilleure que le moulage au sable et le taux de déchets cristallins est faible. Les conditions de travail sont bonnes, la productivité est élevée et les ouvriers sont faciles à maîtriser.
(2) Inconvénients
Le type métallique a une grande conductivité thermique et une faible capacité de remplissage. Le type de métal lui-même n'a pas de perméabilité à l'air. Des mesures correspondantes doivent être prises pour épuiser efficacement. Le moule métallique n'a pas de recul et se fissure et se déforme facilement lors de la solidification.
3. Défauts courants et prévention des pièces moulées en métal
(1) trou d'épingle
Mesures pour éviter les trous d'épingle : Il est strictement interdit d'utiliser des matériaux en alliage d'aluminium moulé contaminé, des matériaux tachés de composés organiques et fortement oxydés et corrodés ; contrôler le processus de fusion, renforcer le dégazage et le raffinage ; contrôler l'épaisseur du revêtement de type métallique, trop épais est facile de produire des trous d'épingle; La température du moule ne doit pas être trop élevée, adoptez des mesures de refroidissement pour les pièces à paroi épaisse des pièces moulées, telles que l'incrustation de cuivre ou l'arrosage, etc. lors de l'utilisation de moules en sable, contrôlez strictement l'humidité et essayez d'utiliser des noyaux secs.
(2) Stomie
Mesures pour éviter les pores : modifier le système de coulée et de colonne montante déraisonnable pour stabiliser l'écoulement du liquide et éviter l'implication du gaz ; le moule et le noyau doivent être préchauffés, puis peints, et doivent être soigneusement séchés avant utilisation; concevoir le moule Des mesures d'échappement adéquates doivent être envisagées avec le noyau.
(3) Oxydation et inclusion de scories
Mesures pour empêcher l'oxydation et l'inclusion de scories : contrôlez strictement le processus de fusion, fusion rapide, réduisez l'oxydation et éliminez soigneusement les scories. A1- L'alliage Mg doit être fondu sous un agent de recouvrement ; le four et les outils doivent être propres, exempts d'oxydes et doivent être préchauffés, et le revêtement doit être séché pour être utilisé après avoir ralenti ;
Le système de coulée conçu doit avoir des capacités d'écoulement, de tamponnage et d'écumage des scories stables ; le système de coulée incliné permet de stabiliser le flux de liquide sans oxydation secondaire ; le revêtement sélectionné doit avoir une forte adhérence et ne s'écaillera pas pendant le processus de coulée et n'entrera pas dans la coulée pour former du laitier.
(4) Craquage thermique
Mesures pour empêcher la fissuration thermique : La surchauffe locale doit être évitée dans le système de coulée lui-même afin de réduire les contraintes internes ; l'inclinaison du moule et du noyau doit être supérieure à 2°, la colonne de coulée peut être dénoyautée pour ouvrir le moule une fois solidifié, et des noyaux de sable peuvent être utilisés si nécessaire Remplacer le noyau métallique contrôler l'épaisseur du revêtement pour rendre cohérente la vitesse de refroidissement de chaque partie de la coulée ; choisir la température de moule appropriée en fonction de l'épaisseur de la coulée ; affiner la structure de l'alliage pour améliorer la capacité de fissuration à chaud ; améliorer la structure de coulée pour éliminer les angles vifs et les mutations d'épaisseur de paroi, réduire la tendance à la fissuration à chaud.
(5) Lâche
Mesures de prévention de la porosité : réglages raisonnables des colonnes montantes pour assurer la solidification et la capacité d'alimentation ; abaisser de manière appropriée la température de travail du moule métallique; contrôler l'épaisseur du revêtement et réduire l'épaisseur de la paroi épaisse; ajustez la vitesse de refroidissement de chaque partie du moule en métal pour que la paroi épaisse de la coulée ait une plus grande capacité de stimulation; réduire de manière appropriée la température de coulée du métal.
Pages associées: Moulage d'aluminium
Articles connexes:
- Influence du film d'oxyde métallique sur la qualité des pièces moulées en alliage d'aluminium
- L'application du moulage en alliage d'aluminium dans l'automobile
Veuillez conserver la source et l'adresse de cet article pour réimpression:Les avantages et les inconvénients du processus de moulage d'aluminium
Minghé Société de moulage sous pression sont dédiés à la fabrication et à la fourniture de pièces de moulage de qualité et de haute performance (la gamme de pièces de moulage sous pression en métal comprend principalement Moulage sous pression à paroi mince,Chambre chaude coulée sous pression,Chambre froide coulée sous pression), Service rond (Service de moulage sous pression,Usinage CNC,Fabrication de moules,Traitement de surface). Tout moulage sous pression en aluminium personnalisé, moulage sous pression en magnésium ou en zamak/zinc et autres exigences en matière de moulages sont invités à nous contacter.
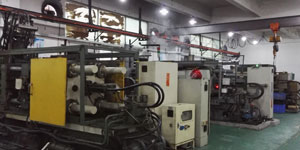
Sous le contrôle des normes ISO9001 et TS 16949, tous les processus sont effectués via des centaines de machines de moulage sous pression avancées, de machines à 5 axes et d'autres installations, allant des blasters aux machines à laver Ultra Sonic.Minghe dispose non seulement d'équipements de pointe, mais également de professionnels équipe d'ingénieurs, d'opérateurs et d'inspecteurs expérimentés pour réaliser la conception du client.
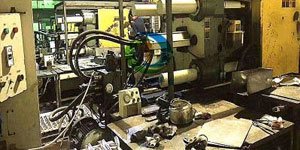
Fabricant sous contrat de moulages sous pression. Les capacités incluent des pièces de moulage sous pression en aluminium à chambre froide à partir de 0.15 lb. jusqu'à 6 lb, configuration à changement rapide et usinage. Les services à valeur ajoutée comprennent le polissage, la vibration, l'ébavurage, le grenaillage, la peinture, le placage, le revêtement, l'assemblage et l'outillage. Les matériaux travaillés comprennent des alliages tels que 360, 380, 383 et 413.
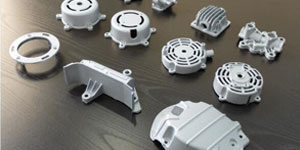
Assistance à la conception de moulage sous pression de zinc/services d'ingénierie simultanés. Fabricant sur mesure de pièces moulées en zinc de précision. Des moulages miniatures, des moulages sous pression à haute pression, des moulages en moules à glissières multiples, des moulages en moules conventionnels, des moulages sous pression unitaires et indépendants et des moulages à cavité scellée peuvent être fabriqués. Les pièces moulées peuvent être fabriquées dans des longueurs et des largeurs allant jusqu'à 24 po avec une tolérance de +/- 0.0005 po.
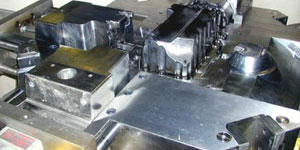
Fabricant certifié ISO 9001 : 2015 de magnésium moulé sous pression, les capacités incluent le moulage sous pression de magnésium sous pression jusqu'à une chambre chaude de 200 tonnes et une chambre froide de 3000 tonnes, la conception d'outillage, le polissage, le moulage, l'usinage, la peinture en poudre et liquide, une assurance qualité complète avec des capacités CMM , assemblage, emballage et livraison.
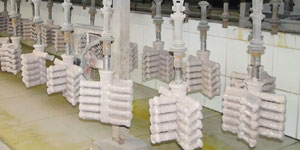
Certifié ITAF16949. Service de casting supplémentaire inclus coulée d'investissement,moulage en sable,Coulée par gravité, Coulée de mousse perdue,Coulée centrifuge,Coulée sous vide,Moulage de moule permanentLes capacités comprennent l'EDI, l'assistance technique, la modélisation solide et le traitement secondaire.
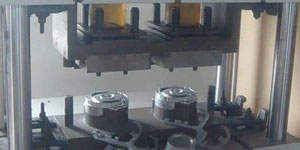
Industries de moulage Études de cas de pièces pour : voitures, vélos, avions, instruments de musique, motomarines, appareils optiques, capteurs, modèles, appareils électroniques, boîtiers, horloges, machines, moteurs, meubles, bijoux, gabarits, télécommunications, éclairage, appareils médicaux, appareils photographiques, Robots, Sculptures, Équipement de sonorisation, Équipement de sport, Outillage, Jouets et plus encore.
Que pouvons-nous vous aider à faire ensuite ?
∇ Aller à la page d'accueil pour Moulage sous pression Chine
→Pièces de fonderie-Découvrez ce que nous avons fait.
→Conseils à propos de Services de moulage sous pression
By Fabricant de moulage sous pression Minghe |Catégories : Articles utiles |Matières Mots clés: Moulage d'aluminium, Moulage de zinc, Coulée de magnésium, Moulage de titane, Fonderie en acier inoxydable, Coulée de laiton,Coulée de bronze,Vidéo de casting,Historique de l'entreprise,Moulage sous pression en aluminium |Commentaires fermés