Les moyens de résoudre les problèmes particuliers des grandes pièces moulées en fonte ductile
Il existe de nombreux types de grandes pièces en fonte ductile, telles que: grand bloc moteur diesel, grand moyeu de roue, grand couvercle d'extrémité de broyeur à boulets, douelle de refroidissement de haut fourneau, grand cadre de laminoir, grand gabarit de machine de moulage par injection, grand siège de roulement de turbine à vapeur, moyeu de roue dans les équipements éoliens et Bases et réservoirs de déchets de scories dans les équipements nucléaires, etc. En plus des propriétés mécaniques spécifiées dans les normes, ces composants ont également des exigences de performances particulières, telles que la résistance aux chocs à basse température requise pour l'énergie éolienne moulages, et de nombreuses autres normes d'acceptation spéciales pour les réservoirs de scories nucléaires. Par conséquent, la production de ces pièces moulées doit être soigneusement étudiée à l'avance.
1) La première chose à considérer est de savoir comment obtenir une coulée de taille saine, dense et qualifiée
Le processus technique de production de grandes pièces en fonte à graphite sphéroïdal est fondamentalement le même que celui des pièces en fonte grise, à condition que le choix de l'échelle et la conception du ballon soient légèrement modifiés en fonction des caractéristiques de la fonte à graphite sphéroïdal le fer.
2) Deuxièmement, un travail correspondant doit être effectué pour les caractéristiques communes des grandes pièces moulées en fonte ductile
La caractéristique commune des pièces moulées en fonte ductile à grande échelle est qu'elles sont extrêmement lourdes. La plupart d'entre eux nécessitent une matrice de ferrite, les propriétés mécaniques doivent répondre aux données standard et parfois des exigences de performance d'impact à basse température sont ajoutées.
Problèmes particuliers dans la production de grandes pièces moulées en fonte ductile
En raison de la vitesse de refroidissement lente des pièces en fonte ductile à grande échelle, la période de solidification eutectique peut atteindre plusieurs heures. Pendant cette période, la structure principale de la fonte ductile sera formée. Par conséquent, une série de problèmes propres aux pièces en fonte ductile de grande section ou en fonte ductile de grande taille apparaissent. :Petit nombre d'encre nodulaire, grand diamètre d'encre nodulaire, distorsion de l'encre nodulaire, flottement du graphite, ségrégation de la composition chimique, carbures intercristallins et graphite en morceaux (Chunky Graphite), etc. Ces problèmes ont longtemps attiré l'attention. Bien que le mécanisme de formation ne soit pas unifié, des mesures préliminaires ont été prises pour résoudre des problèmes spécifiques.
Une autre question importante est de savoir comment répondre et résoudre les exigences de résistance aux chocs à basse température ? La coïncidence du problème est que les directions et les mesures pour résoudre ces deux problèmes sont à peu près les mêmes.
Façons de résoudre les problèmes uniques des grandes pièces moulées en fonte ductile
1) Refroidissement intensifié pour accélérer la solidification
Il existe deux théories généralement acceptées sur la cause du graphite fragmenté : l'une est causée par l'écrasement du graphite sphéroïdal ; l'autre est que la stabilité de la coquille d'austénite est réduite en raison du flux de chaleur ou de la ségrégation de certains éléments d'alliage, en particulier Ce et La. Provoque le changement et la formation du modèle de croissance de l'encre sphéroïdale. Quelle que soit la théorie ou la théorie, il est certain qu'un temps de solidification trop long (ie refroidissement lent) au stade eutectique est un facteur direct et objectif de formation de graphite fragmenté. Par conséquent, quelle que soit la méthode adoptée, tant que la durée de l'étape de solidification peut être raccourcie, l'apparition de graphite fragmenté peut être efficacement évitée.
Il est également souligné dans la littérature qu'il existe une vitesse de refroidissement critique (0.8 /min) pour la distorsion de l'encre sphéroïdale. La déformation du graphite est parfois un processus brutal, donc accélérer le refroidissement, raccourcir le temps de solidification, en particulier raccourcir le temps de solidification de l'étape eutectique, trouver des moyens de raccourcir l'étape de solidification eutectique à moins de 2 h, ce qui a un effet significatif. Il existe de nombreuses mesures autour de ce principe : refroidissement forcé ; type de sable suspendu en métal; utilisation de fer froid et ainsi de suite.
La conductivité thermique élevée du fer froid, en particulier la forte capacité de stockage de chaleur, est largement considérée comme une mesure puissante pouvant être appliquée. La conductivité thermique du graphite est supérieure à celle de la fonte refroidie sur sable (respectivement 45W/m•℃ et 17 W/m•℃), mais sa capacité de stockage de chaleur est inférieure à celle de la fonte refroidie. S'il y a un refroidissement forcé, le graphite est utilisé à titre de comparaison. qui convient. Pour les grandes ou très grandes pièces moulées en fonte ductile, le refroidissement forcé reste une mesure efficace. Généralement, des dispositifs refroidis par air, par brouillard ou par eau peuvent être utilisés, et même un refroidissement à l'azote liquide peut être utilisé pour accélérer la vitesse de solidification des pièces moulées. Les données montrent que lorsque le moulage du conteneur usé en fonte ductile de 20 t est solidifié, l'effet de transfert de chaleur est le suivant : l'absorption de chaleur de type métal représente 58 %, l'absorption de chaleur du moule en graphite et en sable (partie centrale) représente 3.5 %, et le moule en sable et d'autres appareils absorbent en partie la chaleur. La chaleur représentait 3.5% et la conduction thermique refroidie à l'eau 3.5%. On peut voir que le moule métallique peut conduire plus de 50% de la chaleur de la coulée, tandis que la partie centrale transfère peu de chaleur. Évidemment, un refroidissement forcé est nécessaire.
2) Améliorer la technologie des processus
(1) Sélectionner soigneusement les matières premières
Afin de produire des pièces en fonte ductile à grande échelle de haute qualité, il vaut la peine de sélectionner la charge du four, peu importe comment. Les éléments d'interférence des matières premières doivent être aussi faibles que possible. Une attention particulière doit être accordée à la source de la fonte brute, au type de ferraille et au choix des recarburateurs.
(2) Conception de la composition chimique
CE ne doit pas être trop élevé (4.2 % ~ 4.3 %), si w(C) est de 3.6 % 3.7 %, w(Si) doit être aussi bas que 1.8 % 2.0 % ; de plus, w(Mn)<0.3%, w(P) et w(S) doivent également être strictement limités. Sauf circonstances particulières, les alliages ne sont généralement pas utilisés, la ferraille doit donc être rigoureusement sélectionnée.
Un faible w(Si) doit être atteint, sinon du graphite fragmenté apparaîtra facilement et les performances à basse température ne répondront pas aux exigences. Le problème réside dans le faible w(Si) ou faible w(Si) Et les maux qui en découlent. La composition des conteneurs de combustible usé de 100 tonnes au Japon est la suivante : w(C) 3.6 %, w(Si) 2.01 %, w(Mn) 0.27 %, w(P) 0.025 %, w(S) 0.004 %, w( Ni) 0.78 %, p(Mg) 0.065%.
(3) Choisissez la fusion duplex
La fusion duplex peut tirer pleinement parti de la forte capacité de nucléation de la fonte en fusion du cubilot et du rendement thermique élevé du four électrique. Le fer en fusion doit être déchargé à haute température, et S peut être retiré lorsque cela est possible, et le temps dans le four électrique ne doit pas être trop long. La température de sphéroïdisation est déterminée en fonction de la situation, et ne peut être ni trop élevée ni trop basse.
L'auteur préconise de ne pas utiliser la méthode de rinçage pour la sphéroïdisation de gros morceaux car elle prend trop de temps. Utilisez au moins la méthode de couverture, de préférence la méthode spéciale ou la méthode d'alimentation en soie. La soie est nourrie dans un endroit fixe, et elle peut même être nourrie avec la soie fertile. N'utilisez pas d'agents de sphéroïdisation couramment utilisés. Il est préférable de mélanger des agents de sphéroïdisation de terres rares lourds et des agents de sphéroïdisation de terres rares légers. Si l'agent de sphéroïdisation est utilisé, w (Mg) 6 % et w (RE) 1.0 % à 1.5 % sont suffisants ; si la fonte est relativement pure, w (RE) 0.5% à 1.0% est également acceptable. Si la méthode d'alimentation en fil est utilisée, un agent de sphéroïdisation avec une quantité élevée de w (Mg) peut être utilisé, mais w (RE) doit être faible, avec un peu de Ca.
La température de coulée doit être appropriée (1300~1350 ℃), pas trop élevée, sinon le retrait du liquide sera trop important; il est conseillé d'utiliser le canal interne dispersé pour la coulée à vitesse moyenne et d'utiliser autant que possible des moules à haute rigidité pour tirer pleinement parti de l'expansion de graphitisation pour l'auto-alimentation de la fonte ductile. , Pour réduire la charge sur la colonne montante et assurer la compacité intérieure de la coulée.
(4) Faites attention au problème de la grossesse
L'inoculation est l'une des mesures technologiques les plus importantes. Ce n'est qu'en résolvant ce problème qu'il sera possible d'assurer une faible teneur en w (Si) sans problème et d'assurer des performances à basse température. Le problème de l'inoculation n'est rien d'autre que le choix des inoculants et des méthodes de traitement de l'inoculation. Vous pouvez choisir un inoculant avec un temps d'inoculation long, tel qu'un agent contenant du Ba (l'agent contenant du Sr est plus efficace pour la fonte grise et le Ca inférieur), un inoculant contenant du graphite ou un mélange approprié de RESiFe dans l'inoculant .
À l'heure actuelle, de nombreuses entreprises ont des inoculants fabriqués par elles-mêmes, et je suppose qu'elles suivent ce principe. Bref, l'incubation "doit être retardée, mais instantanée", non seulement l'effet est bon, mais le dosage peut être fortement réduit. L'ancienne méthode, telle que la couverture pendant le traitement, a un effet très faible, mais w(Si) est abaissé. Le problème maintenant est que si w (Si) doit être faible et que l'effet doit être bon, la seule issue est de changer de méthode. Les faits ont prouvé que 2.0% de w (Si) est réalisable, et le signe du succès est que le graphite doit être plus petit et plus gros. S'il est plus petit, le taux de sphéroïdisation sera plus élevé. S'il est plus petit, aucune cémentite ne sera produite. S'il est plus petit, le degré de ségrégation sera plus léger. Pour les grandes pièces, si le nombre de billes de graphite est de 200 pièces/mm2 ou plus, et la taille est de 5-6, le taux de sphéroïdisation et la quantité de ferrite ne seront naturellement pas un problème. En un mot, la principale méthode pour lutter contre le graphite et lutter pour du graphite plus petit et plus est l'inoculation. Le w(Si) est faible, et il n'y a pas de cémentite libre, la plasticité et la ténacité aux chocs à température ambiante et à basse température sont faciles à passer. Pour les grandes coulées, il est facile d'effectuer un grand processus d'ensemencement dans le godet verseur et de mettre un bloc d'ensemencement dans la goulotte. Le problème est qu'il doit y avoir un concept correct.
(5) Utilisation d'alliages et d'oligo-éléments
Le seul élément d'alliage qui peut être envisagé pour une utilisation dans les pièces moulées en fonte ductile extra-large est le Ni, en raison de son effet unique. D'un point de vue technique, w(Ni)<1% est bénéfique, mais son utilisation ou non dépend de circonstances spécifiques et de considérations économiques.
Les microéléments ont une expérience d'utilisation mature dans les gros articles sont Bi et Sb. On pense qu'en ajoutant w(Bi) 0.008%~0.010 %, de sorte que le rapport w(RE)/w(Bi)=1.4~1.5, pour augmenter le nombre de billes, il est bénéfique de réduire le risque de fragmentation du graphite. Sb peut également être utilisé dans des pièces épaisses et volumineuses. Certaines personnes pensent que cela augmentera la quantité de perlite, mais certaines personnes l'utilisent dans la fonte ductile ferritique. Cela peut être un problème avec la quantité, et la quantité de 50 ppm ne devrait pas poser de problème. Le professeur Zhou Jiyang a souligné une fois que l'utilisation de w(Sb) 0.005% 0.007% peut également inhiber les effets nocifs d'un excès de Ti et de RE dans le fer en fusion.
Bien que les avis de l'industrie sur le rôle et le mécanisme de l'ajout de Bi et Sb ne soient toujours pas unifiés, un consensus s'est formé sur l'ajout de Ni.
(6) Le rôle du prétraitement est essentiel
Le prétraitement de la solution mère de fer nodulaire avec un agent de prétraitement au graphite avant la sphéroïdisation a un effet positif sur l'amélioration et la stabilisation de la qualité des pièces moulées [3]. Méthodes comme ci-dessous :
Après ajustement de la composition [le prétraitement augmentera w(C) de 0.2%] → de-S → retour au four électrique → ajouter 0.2% à 0.25% d'agent de prétraitement lorsque 1/4 de volume est ajouté → retour au four électrique et puis augmenter légèrement la température à 1 470 ~1 480 ℃ → traitement de sphéroïdisation → traitement d'inoculation (Ultraseed disponible) → coulée.
(7) Utilisation de l'agent anti-cratère QKS
L'inventeur pense qu'il y a une inclusion étrangère de 1 µm au centre de l'encre sphéroïdale, formant un noyau double couche ; la couche interne est en MgS, CaS (0.5 µm) et la couche externe est en MgO, SiO et silicate. Par conséquent, l'inventeur a ajouté une certaine quantité d'O et de S à l'inoculant pour se combiner avec les éléments métalliques de l'inoculant pour produire plus de sulfures et d'oxydes, formant ainsi plus de noyaux de graphite, ce qui produit un inoculant ferrosilicium de Ca, Ce et S, O. Cet inoculant peut augmenter de manière significative le nombre de sphères de graphite, et il précipite au dernier stade de la cristallisation, et la dernière période d'expansion de la graphitisation peut compenser efficacement le retrait au dernier stade de la solidification. En particulier, il est plus efficace pour la porosité de retrait des joints chauds locaux [4]. L'expérience a souligné : pour le bloc d'essai étagé de 5-40 mm, lorsque SrSiFe est utilisé, les billes de graphite sont réduites de 300/mm2 à 150/mm2 ; lorsque l'agent Ca-Ce-OS est utilisé, le nombre de billes de graphite n'est pas affecté par l'épaisseur de la paroi. Par rapport à BaSiFe et 75SiFe. Le défaut de retrait sur les joints chauds du bloc d'essai croisé montre qu'il y a des trous de retrait au niveau des joints chauds de la section transversale avec l'inoculant contenant Ba et Sr, contrairement à l'agent Ca-Ce-OS.
Veuillez conserver la source et l'adresse de cet article pour réimpression: Les moyens de résoudre les problèmes particuliers des grandes pièces moulées en fonte ductile
Minghe Casting Company se consacre à la fabrication et à la fourniture de pièces de moulage de qualité et de haute performance (la gamme de pièces de moulage sous pression en métal comprend principalement Moulage sous pression à paroi mince,Chambre chaude coulée sous pression,Chambre froide coulée sous pression), Service rond (Service de moulage sous pression,Usinage CNC,Fabrication de moules,Traitement de surface). Tout moulage sous pression en aluminium personnalisé, moulage sous pression en magnésium ou en zamak/zinc et autres exigences en matière de moulages sont invités à nous contacter.
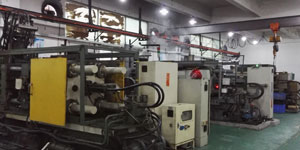
Sous le contrôle des normes ISO9001 et TS 16949, tous les processus sont effectués via des centaines de machines de moulage sous pression avancées, de machines à 5 axes et d'autres installations, allant des blasters aux machines à laver Ultra Sonic.Minghe dispose non seulement d'équipements de pointe, mais également de professionnels équipe d'ingénieurs, d'opérateurs et d'inspecteurs expérimentés pour réaliser la conception du client.
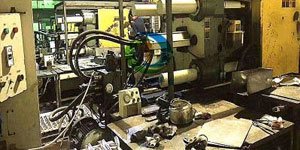
Fabricant sous contrat de moulages sous pression. Les capacités incluent des pièces de moulage sous pression en aluminium à chambre froide à partir de 0.15 lb. jusqu'à 6 lb, configuration à changement rapide et usinage. Les services à valeur ajoutée comprennent le polissage, la vibration, l'ébavurage, le grenaillage, la peinture, le placage, le revêtement, l'assemblage et l'outillage. Les matériaux travaillés comprennent des alliages tels que 360, 380, 383 et 413.
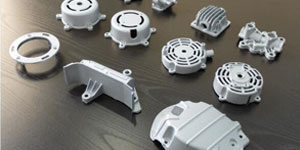
Assistance à la conception de moulage sous pression de zinc/services d'ingénierie simultanés. Fabricant sur mesure de pièces moulées en zinc de précision. Des moulages miniatures, des moulages sous pression à haute pression, des moulages en moules à glissières multiples, des moulages en moules conventionnels, des moulages sous pression unitaires et indépendants et des moulages à cavité scellée peuvent être fabriqués. Les pièces moulées peuvent être fabriquées dans des longueurs et des largeurs allant jusqu'à 24 po avec une tolérance de +/- 0.0005 po.
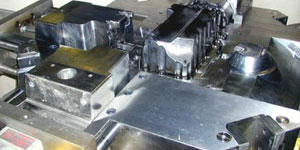
Fabricant certifié ISO 9001 : 2015 de magnésium moulé sous pression, les capacités incluent le moulage sous pression de magnésium sous pression jusqu'à une chambre chaude de 200 tonnes et une chambre froide de 3000 tonnes, la conception d'outillage, le polissage, le moulage, l'usinage, la peinture en poudre et liquide, une assurance qualité complète avec des capacités CMM , assemblage, emballage et livraison.
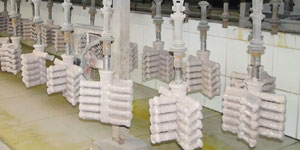
Certifié ITAF16949. Service de casting supplémentaire inclus coulée d'investissement,moulage en sable,Coulée par gravité, Coulée de mousse perdue,Coulée centrifuge,Coulée sous vide,Moulage de moule permanentLes capacités comprennent l'EDI, l'assistance technique, la modélisation solide et le traitement secondaire.
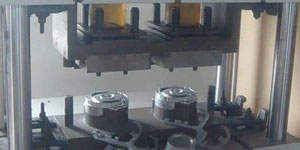
Industries de moulage Études de cas de pièces pour : voitures, vélos, avions, instruments de musique, motomarines, appareils optiques, capteurs, modèles, appareils électroniques, boîtiers, horloges, machines, moteurs, meubles, bijoux, gabarits, télécommunications, éclairage, appareils médicaux, appareils photographiques, Robots, Sculptures, Équipement de sonorisation, Équipement de sport, Outillage, Jouets et plus encore.
Que pouvons-nous vous aider à faire ensuite ?
∇ Aller à la page d'accueil pour Moulage sous pression Chine
→Pièces de fonderie-Découvrez ce que nous avons fait.
→Conseils à propos de Services de moulage sous pression
By Fabricant de moulage sous pression Minghe |Catégories : Articles utiles |Matières Mots clés: Moulage d'aluminium, Moulage de zinc, Coulée de magnésium, Moulage de titane, Fonderie en acier inoxydable, Coulée de laiton,Coulée de bronze,Vidéo de casting,Historique de l'entreprise,Moulage sous pression en aluminium |Commentaires fermés