Méthode du fil d'alimentation Processus de traitement de la fonte ductile
Grâce à la production réelle, la méthode de poinçonnage et la méthode d'alimentation sont utilisées pour produire de la fonte ductile, et les caractéristiques des deux processus sont analysées. Grâce à la comparaison, les performances globales des pièces moulées produites par la méthode d'alimentation sont plus stables que celles de la méthode de poinçonnage ; et le processus d'alimentation est sphéroïdisé. Pour partager certaines de ses expériences.
1. Contexte
Comme nous le savons tous, l'essieu est un élément porteur important du véhicule, et il est directement lié à la sécurité du véhicule. Le carter d'essieu est l'un des composants clés de l'essieu. Les performances du matériau du carter d'essieu déterminent directement la capacité de charge du véhicule. À l'heure actuelle, les carters d'essieu dans l'industrie des camions lourds sont généralement divisés en deux catégories : les carters d'essieu emboutis et soudés et les carters d'essieu moulés, et les carters d'essieu moulés peuvent être divisés en carters d'essieu en acier moulé et carters d'essieu en fonte.
Le carter d'essieu moulé a toujours occupé la position principale du carter d'essieu de camion lourd en raison de son poids porteur élevé et de son faible coût de production. En raison de l'environnement de travail difficile du carter d'essieu et du travail à long terme sous charge dynamique, cela nécessite des exigences élevées pour les propriétés matérielles du carter d'essieu. Tout en assurant la résistance, il doit également obtenir une plasticité et une ténacité plus élevées pour s'adapter au carter d'essieu. Caractéristiques du travail.
On sait que pour la fonte nodulaire, le procédé de sphéroïdisation est un maillon clé dans la production de fonte nodulaire, et la qualité du traitement de sphéroïdisation affecte directement la qualité de la fonte nodulaire. Au début, le processus de sphéroïdisation que nous avons utilisé était le processus de sphéroïdisation de la méthode de précipitation. Bien que cette méthode soit simple et facile à mettre en œuvre, elle présente de nombreux inconvénients, tels que : un faible rendement d'alliage ; grande fumée et environnement de travail médiocre; réaction La quantité de laitier produite à ce moment-là est importante; l'effet du traitement est facilement affecté par des facteurs externes, ce qui entraîne des fluctuations de la qualité des moulages et une sphéroïdisation souvent non qualifiée. Ces fluctuations de qualité affecteront les performances du carter d'essieu et affecteront même la sécurité du véhicule.
Le procédé de traitement de sphéroïdisation par méthode d'alimentation en fil a été appliqué à la production de fonte. Cela a commencé dans les années 1980 à l'étranger. Bien que la production nationale de fonte nodulaire ait commencé à appliquer cette technologie tardivement, la technologie a été popularisée et utilisée rapidement dans le pays, et elle est utile pour améliorer la production de graphite nodulaire. L'effet de stabilité de la qualité de la fonte est évident.
2. Processus de sphéroïdisation du fil d'alimentation
Le principe de base du processus de sphéroïdisation d'alimentation de fil est d'envelopper une certaine composition d'agent de sphéroïdisation en poudre et d'inoculant à travers la peau d'acier, et de l'envoyer dans l'emballage de traitement de sphéroïdisation à une certaine vitesse à travers l'équipement, de sorte que la sphéroïdisation au bas de le colis va exploser. Pour atteindre l'objectif du traitement d'inoculation de sphéroïdisation.
À l'heure actuelle, le processus de sphéroïdisation par dévidage que nous adoptons est le suivant : ajuster la composition chimique aux exigences du processus, chauffer jusqu'à 1510-1520℃ et laisser reposer, la température de taraudage est de 1480~1500℃, la sortie de fer est de 2t, et la température de traitement de sphéroïdisation est de 1420~1450℃. La température de coulée est de 1370~1380℃. Le taux d'ensemencement avec le flux est de 0.1%.
La longueur de la ligne de sphéroïdisation est de 39 à 46 m, ajustée en fonction de la teneur en soufre du fer fondu d'origine. Plus la teneur en soufre est élevée, plus la ligne de sphéroïdisation doit être longue, et vice versa. La longueur de la ligne d'inoculation est de 32 m.
3. Le processus de sphéroïdisation du fil d'alimentation améliore la qualité des pièces moulées
Après plus d'un an de production, la qualité de nos carters d'essieu a été considérablement améliorée par rapport à avant. En particulier, la stabilité de la composition, de la métallographie et des propriétés mécaniques a été grandement améliorée.
Comparaison de la structure métallographique Sélectionnez la même position de la pièce moulée à polir et observez la structure métallographique. L'image métallographique prise est illustrée à la figure 2. Par rapport à la méthode de poinçonnage, les billes de graphite de la coulée produites par la méthode d'alimentation sont plus nombreuses et plus fines, et la rondeur est meilleure.
4. Avantages du processus de sphéroïdisation du fil d'alimentation
Selon notre comparaison de production réelle, le processus de sphéroïdisation par alimentation de fil présente de nombreux avantages par rapport au processus de sphéroïdisation de la méthode de poinçonnage.
- Amélioration de l'environnement de production sur site. Lorsque l'agent de sphéroïdisation réagit avec le fer en fusion, une grande quantité de fumée et une forte lumière sont générées, ce qui aggrave l'environnement de travail sur site ; lorsque la méthode d'alimentation en fil est utilisée pour la sphéroïdisation, la station de traitement Il y a un couvercle pour couvrir le sac de sphéroïdisation, et le couvercle est connecté au système de dépoussiérage de la station de traitement, de sorte que la fumée soit traitée par le système de dépoussiérage à la place d'être directement libéré dans l'atelier.
- La quantité d'alliage ajoutée est réduite, et le coût de production est réduit. Après calcul, le traitement de 1 t de méthode d'alimentation en fer fondu peut économiser environ 78 yuans en matières premières par rapport à la méthode d'impulsion. Selon la capacité de production annuelle de 10,000 780,000 tonnes de carter d'essieu en fonte ductile de notre usine, l'économie annuelle est Le coût est de XNUMX XNUMX yuans et les avantages sont considérables.
- Réalisez l'automatisation des tâches et réduisez l'intensité du travail des travailleurs. Lorsque le processus de sphéroïdisation est effectué, les préparations préliminaires des travailleurs sont lourdes, notamment la pesée de l'agent de sphéroïdisation et de l'inoculant, l'ajout de l'agent de sphéroïdisation et de l'inoculant dans le sac, et des opérations de bourrage et de recouvrement sont nécessaires ; la quantité ajoutée des lignes de sphéroïdisation et d'inoculation de la méthode d'alimentation en fil est automatiquement ajoutée via l'armoire de commande, ce qui réduit beaucoup de travail.
- La qualité de sphéroïdisation est stable et l'effet de sphéroïdisation est meilleur. Selon les statistiques, depuis l'utilisation du processus de sphéroïdisation à alimentation par fil en 2013, le taux de réussite de la sphéroïdisation est supérieur à 99.5 %, tandis que le taux de réussite du processus de sphéroïdisation n'est que de 95, %.
5. Comment choisir correctement les paramètres de processus de sphéroïdisation du fil d'alimentation
En production réelle, comment sélectionner correctement les paramètres du processus de dévidage du fil nécessite un certain nombre de tests à vérifier. Nous avons subi de nombreux ajustements de processus depuis le début de l'organisation du test jusqu'à la production en série formelle. Ce qui suit partagera notre expérience avec des collègues.
Pour sélectionner correctement les paramètres de processus d'alimentation de la sphéroïdisation du fil, vous devez faire attention aux aspects suivants :
- (1) Le choix du fil fourré Certaines expériences étrangères ne recommandent pas l'utilisation de fil fourré à haute teneur en Mg. La teneur en Mg est trop élevée, la réaction de sphéroïdisation est intense, le Mg brûle beaucoup et la quantité de laitier est importante. En règle générale, il est recommandé de sélectionner une teneur en Mg d'environ 30 % et d'utiliser du fil d'inoculation contenant du Ba, qui peut empêcher efficacement le déclin de l'inoculation. Les principaux paramètres du fil fourré utilisé par notre société sont : l'épaisseur de la gaine extérieure en acier est de 0.4 mm et le diamètre du fil central est de 13 mm. Avant utilisation, vérifiez que l'aspect du fil fourré doit être rond et exempt de fissures, de fuites de poudre, etc. En production réelle, il est nécessaire d'ajuster en fonction de la température de traitement et de la hauteur de la fonte en fusion. Généralement, plus la température de traitement est élevée, plus la hauteur de la fonte en fusion est élevée et plus la vitesse d'alimentation du fil est rapide. En plus. Certains matériaux ont également introduit une méthode pratique et réalisable de mesure de la vitesse d'alimentation du fil optimale : mesurez d'abord la hauteur du fer fondu dans le sac de traitement, puis alimentez manuellement la machine à fil de sorte que le fil central touche juste la surface du liquide, puis effacer le compteur, la machine d'alimentation en fil manuelle effectue l'alimentation en fil. Lorsque vous entendez le son de réponse « boum », vérifiez immédiatement la longueur d'alimentation. Si cette longueur est fondamentalement égale à la hauteur de la fonte en fusion, la vitesse doit être appropriée. Après vérification, nous avons sélectionné la vitesse d'alimentation de 30m/min.
- Sélection de la quantité d'alimentation de fil La quantité d'alimentation de fil appropriée est d'alimenter le fil le moins fourré sous le principe d'assurer l'effet de sphéroïdisation. La quantité d'alimentation en fil doit être déterminée en fonction du volume de traitement de la fonte en fusion, de la température de traitement et de la teneur en soufre de la fonte en fusion. Selon nos exigences originales en matière de teneur en soufre de fer fondu et de traitement du produit, combinées à une vérification expérimentale, à condition de garantir la teneur résiduelle en magnésium, la longueur de la ligne de sphéroïdisation est de 39 à 46 m et la longueur de la ligne d'inoculation est de 32 m.
- Le choix de la température de mise en œuvre La température de mise en œuvre doit être réduite autant que possible sous le principe d'assurer la température de coulée. Plus la température de traitement est basse, plus le taux d'absorption du magnésium est élevé et moins la consommation de fil fourré est importante. Selon les tests de production réels, le temps entre le début du traitement de sphéroïdisation et le début de la coulée est de 4 à 5 minutes, au cours desquels la chute de température est de 40 à 50 °C et le temps de réaction de sphéroïdisation est de 80 à 90 secondes. Étant donné que le processus de sphéroïdisation doit être inversé, nous définissons la température de traitement à 1410~1450℃, la limite supérieure est prise lorsque la température ambiante est inférieure à 5℃ et la limite inférieure lorsque la température ambiante est supérieure à 25℃.
- Sélection de la teneur en magnésium résiduel dans le fer en fusion après traitement. La teneur résiduelle en magnésium doit être mise de côté pour une certaine quantité de magnésium en fonction des caractéristiques de la coulée elle-même. Au début, nous avons contrôlé la teneur en magnésium résiduel à 0.03 % à 0.06 %, mais après vérification de la production réelle, il est plus approprié de contrôler la teneur en magnésium résiduel à 0.05 % à 0.06 %, car nous avons constaté que lorsque le magnésium résiduel est inférieur à 0.04 %, son graphite La rondeur de la balle est légèrement moins bonne. Lorsqu'elle est supérieure à 0.07 %, la cémentite est susceptible d'apparaître et la tendance au retrait de la fonte en fusion devient plus importante.
- Résoudre le problème de bourrage de fil pendant l'utilisation Le phénomène de bourrage de fil se produira pendant le processus de convoyage du fil fourré, ce qui entraînera la mise au rebut de l'ensemble du paquet de fer en fusion. À cette fin, nous avons pris les mesures suivantes : l'une consiste à installer un anneau en acier au-dessus de la bobine de fil fourré, comme le montre la figure 5, ce qui peut réduire la flexion du fil fourré et le faire entrer en douceur dans le mécanisme de guidage ; la seconde consiste à connecter les deux bobines Lors du soudage, après soudage, polissez les bosses les plus grosses pour éviter que le fil ne se coince pendant le processus de convoyage ; troisièmement, évitez les coudes de diamètre inférieur à 1 m dans la canalisation de transport ou l'itinéraire du fil fourré pour empêcher le transport du fil fourré Une fuite de poudre ou un bourrage s'est produit pendant le processus
Conclusion 6
- Le processus de sphéroïdisation de la méthode du fil d'alimentation a une faible quantité d'ajout d'alliage, un taux d'absorption de Mg élevé et peut réduire efficacement la fumée et la forte pollution lumineuse dans l'atelier, créant de bons avantages économiques et environnementaux pour les entreprises de fonderie.
- Le processus de sphéroïdisation de la méthode d'alimentation par fil peut réduire efficacement le taux d'échec de sphéroïdisation, améliorer la qualité de la fonte nodulaire, améliorer ses propriétés mécaniques complètes et renforcer la compétitivité de l'entreprise sur le marché.
- Chaque fonderie doit sélectionner les paramètres de processus appropriés pour la sphéroïdisation du fil en fonction de ses propres conditions de production et exigences de processus de produit, combinées à l'expérience de production des pairs.
Le processus de sphéroïdisation de la ligne d'alimentation peut améliorer considérablement la stabilité de la qualité de la fonte nodulaire, réduire les coûts de production, améliorer l'environnement de production et réduire l'intensité du travail des travailleurs. C'est la tendance récente du développement du processus de sphéroïdisation.
Veuillez conserver la source et l'adresse de cet article pour réimpressionFMéthode de fil eeding Processus de traitement de la fonte ductile
Minghé Société de moulage sous pression sont dédiés à la fabrication et à la fourniture de pièces de moulage de qualité et de haute performance (la gamme de pièces de moulage sous pression en métal comprend principalement Moulage sous pression à paroi mince,Chambre chaude coulée sous pression,Chambre froide coulée sous pression), Service rond (Service de moulage sous pression,Usinage CNC,Fabrication de moules,Traitement de surface). Tout moulage sous pression en aluminium personnalisé, moulage sous pression en magnésium ou en zamak/zinc et autres exigences en matière de moulages sont invités à nous contacter.
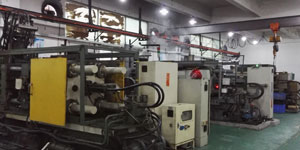
Sous le contrôle des normes ISO9001 et TS 16949, tous les processus sont effectués via des centaines de machines de moulage sous pression avancées, de machines à 5 axes et d'autres installations, allant des blasters aux machines à laver Ultra Sonic.Minghe dispose non seulement d'équipements de pointe, mais également de professionnels équipe d'ingénieurs, d'opérateurs et d'inspecteurs expérimentés pour réaliser la conception du client.
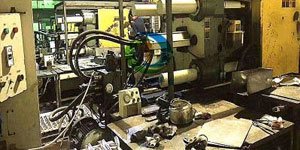
Fabricant sous contrat de moulages sous pression. Les capacités incluent des pièces de moulage sous pression en aluminium à chambre froide à partir de 0.15 lb. jusqu'à 6 lb, configuration à changement rapide et usinage. Les services à valeur ajoutée comprennent le polissage, la vibration, l'ébavurage, le grenaillage, la peinture, le placage, le revêtement, l'assemblage et l'outillage. Les matériaux travaillés comprennent des alliages tels que 360, 380, 383 et 413.
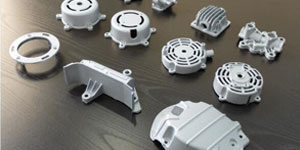
Assistance à la conception de moulage sous pression de zinc/services d'ingénierie simultanés. Fabricant sur mesure de pièces moulées en zinc de précision. Des moulages miniatures, des moulages sous pression à haute pression, des moulages en moules à glissières multiples, des moulages en moules conventionnels, des moulages sous pression unitaires et indépendants et des moulages à cavité scellée peuvent être fabriqués. Les pièces moulées peuvent être fabriquées dans des longueurs et des largeurs allant jusqu'à 24 po avec une tolérance de +/- 0.0005 po.
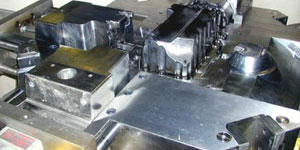
Fabricant certifié ISO 9001 : 2015 de magnésium moulé sous pression, les capacités incluent le moulage sous pression de magnésium sous pression jusqu'à une chambre chaude de 200 tonnes et une chambre froide de 3000 tonnes, la conception d'outillage, le polissage, le moulage, l'usinage, la peinture en poudre et liquide, une assurance qualité complète avec des capacités CMM , assemblage, emballage et livraison.
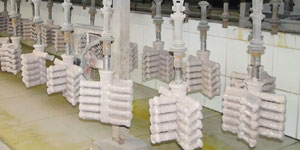
Certifié ITAF16949. Service de casting supplémentaire inclus coulée d'investissement,moulage en sable,Coulée par gravité, Coulée de mousse perdue,Coulée centrifuge,Coulée sous vide,Moulage de moule permanentLes capacités comprennent l'EDI, l'assistance technique, la modélisation solide et le traitement secondaire.
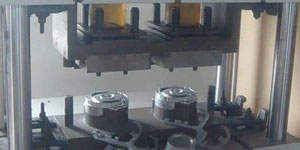
Industries de moulage Études de cas de pièces pour : voitures, vélos, avions, instruments de musique, motomarines, appareils optiques, capteurs, modèles, appareils électroniques, boîtiers, horloges, machines, moteurs, meubles, bijoux, gabarits, télécommunications, éclairage, appareils médicaux, appareils photographiques, Robots, Sculptures, Équipement de sonorisation, Équipement de sport, Outillage, Jouets et plus encore.
Que pouvons-nous vous aider à faire ensuite ?
∇ Aller à la page d'accueil pour Moulage sous pression Chine
→Pièces de fonderie-Découvrez ce que nous avons fait.
→Conseils à propos de Services de moulage sous pression
By Fabricant de moulage sous pression Minghe |Catégories : Articles utiles |Matières Mots clés: Moulage d'aluminium, Moulage de zinc, Coulée de magnésium, Moulage de titane, Fonderie en acier inoxydable, Coulée de laiton,Coulée de bronze,Vidéo de casting,Historique de l'entreprise,Moulage sous pression en aluminium |Commentaires fermés