Défauts de moulage typiques des billes de broyage en fonte ductile multiphasée
La boule de broyage en fonte ductile multiphasée est un produit de projet développé par l'usine de réparation et de montage électromécanique, et il s'agit d'un produit amélioré de la boule de broyage faiblement alliée d'origine. L'usine de réparation mécanique et électrique a une production annuelle de près de 10,000 XNUMX tonnes de ce type de boulets de broyage. Dans la production réelle, en raison de l'existence de différents types de défauts, les billes de broyage sont utilisées dans des conditions de travail réelles, et souvent la non-usure, le faux rond, etc. affectent l'utilisation des billes de broyage. Pour les facteurs défavorables de la qualité, il est nécessaire d'analyser tous les types de défauts un par un, et de formuler des méthodes de prévention correspondantes pour guider les pratiques de production.
Défauts et caractéristiques courants
Mauvaise sphéroïdisation et déclin de la sphéroïdisation
Une mauvaise sphéroïdisation signifie que le traitement de sphéroïdisation ne répond pas aux exigences de niveau de sphéroïdisation. Le déclin de la sphéroïdisation signifie que la quantité résiduelle d'éléments de sphéroïdisation dans la boule de broyage au stade ultérieur de la coulée est trop faible pour provoquer l'échec de la sphéroïdisation. Les deux ont les mêmes caractéristiques de défaut.
Caractéristiques macroscopiques : La cassure de la fonte est gris argent avec des taches de sésame noires réparties dessus. Le grand nombre et le grand diamètre indiquent un degré sérieux. Tous sont des grains grossiers gris foncé, indiquant aucune sphéroïdisation du tout.
Structure métallographique : un grand nombre de graphite lamellaire épais est concentré de manière concentrée. Plus la quantité et l'augmentation du rapport de surface, cela indique que le degré est grave, et celui sans sphéroïdisation est le graphite lamellaire.
Cause : la fonte brute en fusion contient une teneur élevée en soufre et la charge fortement oxydée contient des éléments de dé-sphéroïdation excessifs ; les teneurs résiduelles en magnésium et terres rares dans le fer fondu après traitement sont trop faibles. Une teneur élevée en oxygène dissous dans le fer fondu est une raison importante d'une mauvaise sphéroïdisation.
Choisissez du coke à faible teneur en soufre et une charge métallique à faible teneur en soufre, désulfurez si nécessaire, enlevez la rouille de la ferraille, augmentez la quantité d'éléments de terres rares dans l'agent de sphéroïdisation si nécessaire et contrôlez strictement le processus de sphéroïdisation.
2.2 Cavité de retrait et porosité de retrait
Caractéristiques et causes : Le rétrécissement se produit lorsque la température du fer en fusion baisse et rétrécit une fois. Si la pression atmosphérique fait couler la couche mince solide sur la surface, elle montrera des dépressions de surface et des dépressions locales des joints chauds. Sinon, le gaz contenu dans le fer fondu précipitera dans la coque supérieure et se rassemblera dans les trous de retrait sombres et lisses de la paroi interne des trous d'air, qui communiquent parfois avec le monde extérieur pour former des cavités lumineuses. Cavité de retrait, bien que la surface interne soit lisse, mais elle a été oxydée. Le temps de solidification eutectique de la fonte nodulaire est plus long que celui de la fonte grise, et elle se solidifie sous forme de bouillie. La coque solidifiée est plus faible. Lors de la seconde expansion, la coque se dilate sous l'action de la force d'expansion de graphitisation, ce qui relâche la pression interne. Par conséquent, dans le deuxième processus de rétraction, la pression interne du dernier joint chaud solidifié est inférieure à la pression atmosphérique et le petit bain fondu séparé par des dendrites devient une zone de vide. Après solidification complète, il devient un trou rugueux rempli de dendrites. C'est-à-dire des défauts de retrait. Ce qui est visible à l'œil nu est appelé rétrécissement macroscopique. Il se produit au stade précoce lorsque le fer fondu résiduel dans la zone chaude du joint commence à se solidifier en grande quantité. Il comprend le retrait primaire et secondaire du fer fondu résiduel, de sorte que la taille est légèrement plus grande et la paroi interne est pleine de dendrites, qui sont grises et sombres. Trous lâches ou points noirs comme des pieds de mouche. Ce qui est visible au microscope est appelé retrait microscopique. Il est produit à la fin de la contraction secondaire. Le fer fondu dans le groupe eutectique ou son groupe ne peut pas être alimenté sous pression négative. Il est formé par solidification et retrait, ce qui est courant dans les sections épaisses.
2.3 Stomates sous-cutanés
Caractéristiques morphologiques : trous lisses sphériques, elliptiques ou en forme de trous d'épingle sur la paroi interne de la surface de coulée de 2 à 3 mm uniformément ou en nid d'abeille, d'un diamètre de 0.5 à 3 mm, qui peuvent être trouvés après traitement thermique et grenaillage, exposition ou usinage , petit Il y en a plus.
Raisons de la formation : La tension superficielle du fer liquide contenant du magnésium est élevée et il est facile de former un film d'oxyde, qui empêche l'évacuation du gaz précipité et du gaz envahissant, et se forme en restant sous la peau. La température du film de formation augmente avec l'augmentation de la quantité de magnésium résiduel, ce qui intensifie son effet gênant. Les pièces à paroi mince (7-20 mm) refroidissent rapidement et forment le film tôt, ce qui est facile à former ce défaut. La source de gaz est principalement la vapeur de magnésium précipitée du fer fondu pendant le processus de refroidissement, et le fer fondu s'enroule pendant le processus de remplissage. Le magnésium dans le fer fondu réagit avec l'humidité du sable de moulage. Le magnésium agit comme un catalyseur pour favoriser la réaction entre le carbone et l'humidité du sable de moulage. Le magnésium fait réagir le fer avec une activité accrue avec l'humidité. La réaction de l'eau, du magnésium et des carbures pour produire la décomposition de l'acétylène peut produire de l'hydrogène. De plus, la charge humide et rouillée du four, le ferrosilicium humide et les alliages intermédiaires, ainsi que le souffle à haute température du cubilot peuvent apporter de l'hydrogène. Une petite quantité d'Al (0.02%-0.03%) peut augmenter considérablement les pores sous-cutanés. La fonte ductile moyenne au manganèse contient plus d'azote. Le liant résine à noyau de sable contient plus d'azote, et les facteurs mentionnés ci-dessus peuvent favoriser la formation de ce défaut. La solidification pâteuse caractéristique de la fonte ductile provoque un blocage plus précoce du passage du gaz et favorise également sa formation.
2.4 Déformation sous contrainte et fissures
Raisons de formation et caractéristiques morphologiques : pendant le processus de refroidissement de la coulée, la somme algébrique de la contrainte de retrait, de la contrainte thermique et de la contrainte de transformation de phase, c'est-à-dire que la contrainte de coulée dépasse la résistance à la rupture du métal de section, puis des fissures se forment. À haute température (1150-1000℃), des fissures thermiques se forment, montrant des fractures inégales brun foncé. Des fissures froides apparaissent dans le domaine élastique inférieur à 600°C, avec des fractures lisses et droites brun clair. Une déformation plastique peut se produire lorsque la contrainte de coulée dépasse la limite d'élasticité au-dessus de 600°C. Lorsque la composition de la fonte nodulaire est normale, il n'est pas facile de se fissurer.
Facteurs d'influence : Les facteurs qui augmentent la tendance à la bouche blanche, tels qu'une faible teneur en carbone et en silicium, une augmentation des éléments de formation de carbure, une incubation insuffisante et un refroidissement excessif, peuvent tous augmenter la contrainte de coulée et la tendance à la fissuration à froid. Le phosphore augmente la tendance à la fissuration à froid, et P>0.25 peut également provoquer une fissuration à chaud. L'épaisseur de paroi des pièces moulées varie considérablement, la forme est complexe et la déformation et les fissures sont faciles à se produire.
2.5 Inclusion de scories
Caractéristiques morphologiques : Réparties sur la surface supérieure de la position de coulée, sous le noyau et au coin mort de la coulée. Des inclusions noires foncées et mates de différentes profondeurs apparaissent sur la surface cassée, distribuées par intermittence. L'observation métallographique peut montrer des inclusions en forme de bande et en forme de bloc, et le graphite adjacent peut être en forme de paillettes ou de sphères. Lors de l'inspection par particules magnétiques, les marques magnétiques sont réparties en bandes, et les bandes sont épaisses et denses, indiquant une sérieuse inclusion de laitier. L'analyse par sonde électronique montre que le laitier contient du Mg, Si, O, S, C, A1, etc., et est composé de silicate de magnésium, de composés oxygène-soufre, de spinelle de magnésium, etc.
Processus de formation : Mg et RE réagissent avec O et S dans le fer fondu pour former des scories pendant la sphéroïdisation. Lorsque la température de la fonte en fusion est basse, l'effet de l'agent de laitier mince n'est pas bon, le flottement du laitier est insuffisant ou le laitier n'est pas nettoyé et reste dans la fonte en fusion, il s'agit d'un laitier primaire. Lorsque la fonte en fusion est transportée, coulée, coulée, remplie et laminée, le film d'oxyde est brisé et est aspiré dans le moule, flottant dans le moule, adsorbant le sulfure et s'accumulant sur la surface supérieure ou les coins morts, qui est le laitier secondaire . Généralement, le laitier secondaire est le pilier.
3. Mesures préventives
3.1 Causes du déclin de la sphéroïdisation et mesures préventives
Les scories de sulfure et d'oxyde formées après le traitement de sphéroïdisation de l'oxydation à haute teneur en soufre et à basse température de la fonte en fusion ne sont pas complètement flottées, les scories ne sont pas éliminées de manière adéquate et la fonte en fusion n'est pas bien recouverte. L'oxygène de l'air traverse la couche de scories ou pénètre directement dans la fonte en fusion. L'oxydation efficace des éléments de sphéroïdisation et l'augmentation de l'oxygène actif sont des raisons importantes du déclin de la sphéroïdisation. Le soufre contenu dans le laitier peut également réintégrer la fonte en fusion pour consommer les éléments de sphéroïdisation qu'il contient. Pendant le transport, l'agitation et le déversement de la fonte en fusion, le magnésium s'accumule, flotte et s'oxyde, réduisant ainsi les éléments de sphéroïdisation résiduels efficaces et provoquant le déclin de la sphéroïdisation. De plus, le déclin gestationnel réduit également le nombre de sphères de graphite et conduit à une détérioration de la morphologie du graphite. Les facteurs ci-dessus qui provoquent une mauvaise sphéroïdisation accélèrent également le déclin de la sphéroïdisation.
La teneur en soufre et en oxygène du fer fondu d'origine doit être réduite autant que possible et la température doit être contrôlée de manière appropriée. Un diluant à scories peut être ajouté pour faire flotter complètement les scories et éliminer complètement les scories. Après avoir enlevé les scories, ajoutez de la cendre d'herbe, de la poudre de cryolite, de la poudre de graphite ou d'autres agents de couverture pour isoler l'air. L'ajout d'un couvercle ou l'utilisation d'une poche de coulée scellée et l'utilisation d'une protection à l'azote ou à l'argon peuvent empêcher efficacement la sphéroïdisation de décliner. Le versement doit être accéléré et le temps de déchargement, de transport et de séjour doit être réduit au minimum. L'utilisation d'un agent de sphéroïdisation de magnésium de terres rares lourdes à base d'yttrium peut prolonger le temps de décroissance de 1.5 à 2 fois, et le temps de décroissance de l'agent de sphéroïdisation de magnésium de terres rares léger est légèrement plus long que celui de l'agent de sphéroïdisation de magnésium. Si nécessaire, la quantité ajoutée d'agent de sphéroïdisation peut également être augmentée de manière appropriée. La morphologie du graphite s'est détériorée en raison du déclin de l'incubation, qui peut être amélioré après supplémentation.
3.2 Facteurs d'influence et mesures préventives du retrait et de la porosité
Un équivalent à faible teneur en carbone augmente la tendance aux cavités de retrait et à la porosité. L'eutectique au phosphore affaiblit la résistance de la coque solidifiée et l'eutectique au phosphore ternaire réduit l'expansion de graphitisation, de sorte que la teneur élevée en phosphore augmente considérablement la tendance au retrait. Le molybdène augmente la stabilité des carbures, en particulier dans des conditions de forte teneur en phosphore, il est facile de former des composites eutectiques carbure-phosphore et il augmente également la tendance au retrait et au retrait. Un magnésium résiduel trop élevé augmente la tendance à la porosité de retrait et aux cavités de retrait, une quantité modérée de terres rares résiduelles peut réduire la porosité de retrait, et une trop forte augmentation de la tendance des deux. Par conséquent, l'équivalent carbone du fer fondu doit être augmenté, la teneur en phosphore doit être réduite, la quantité résiduelle de magnésium des terres rares doit être réduite autant que possible dans les conditions de sphéroïdisation garanties et le molybdène doit être utilisé de manière rationnelle. Améliorer la rigidité du moule, tel que le moulage à haute pression, le moule de sable de cire et le revêtement de sable de moule en métal peuvent réduire le retrait et le retrait, tout en augmentant l'équivalent carbone du fer fondu, en réduisant de manière appropriée la température de coulée et en utilisant un mince et large coureur intérieur pour le faire se dilater dans un deuxième temps. Avant la solidification et le scellement, l'expansion de graphitisation est utilisée pour compenser le retrait de la fonte liquide et le retrait de solidification, ce qui peut éliminer le retrait et la porosité.
3.3 Mesures préventives pour les pores sous-cutanés : La température de coulée ne doit pas être inférieure à 1300°C. Lorsque la teneur en magnésium résiduel est élevée, la température de coulée doit être augmentée en conséquence ; la teneur résiduelle en magnésium doit être réduite autant que possible dans la condition de sphéroïdisation garantie, et les terres rares doivent être utilisées de manière appropriée ; le système de coulée multicanal ouvert est adopté pour que le fer fondu s'écoule en douceur dans la cavité et évite la cavité Tournez vers l'intérieur pour contrôler la teneur en humidité du sable de moulage 4.5% une s. 5%, mélangé avec de la poudre de charbon 8%-15% peuvent être brûlés en CO, inhibent la réaction de la vapeur d'eau et du magnésium pour former H2 (la pulvérisation d'huile de broche sur la surface du moule peut également jouer le même rôle); la surface du moule est retirée de la poudre de cryolithe et réagit avec la vapeur d'eau à haute température. La formation de gaz HF protège la fonte fondue de la réaction et contrôle la faible teneur en aluminium de la fonte fondue. Contrôlez strictement le séchage de la charge du four et réduisez la rouille, la déshumidification du cubilot et l'alimentation en air, réduisez le gaz dans le fer en fusion et utilisez le sable de résine avec moins ou pas d'azote, etc.
3.4 Mesures pour prévenir les contraintes, les déformations et les fissures : augmenter de manière appropriée l'équivalent carbone, réduire la teneur en phosphore, renforcer l'inoculation et les mesures nécessaires au processus de coulée.
3.5 Facteurs d'influence de l'inclusion de scories et mesures préventives : La raison importante de la formation d'inclusions de scories est la teneur élevée en soufre du fer fondu d'origine et une oxydation importante. Les mesures préventives fondamentales consistent à réduire la teneur en soufre et en oxygène du fer fondu d'origine et à augmenter la température. La principale raison de la formation de laitier secondaire est que la quantité de magnésium résiduel est trop élevée, ce qui augmente la température de formation du film d'oxyde. La principale mesure est de minimiser la teneur en magnésium résiduel (pièces de petite et moyenne taille ne dépassant pas 0.055%) dans les conditions d'assurer la sphéroïdisation. L'ajout d'une quantité appropriée de terres rares peut réduire la température de formation du film ; ajouter 0.16% de cryolite pendant le traitement de sphéroïdisation, puis saupoudrer 0.3% sur la surface après traitement, utilisé pour diluer les scories et générer du gaz A1F3 et un film MgF2 pour réduire l'oxydation secondaire. Cette méthode est principalement utilisée pour empêcher l'inclusion de scories dans de grandes parties, et la température de coulée ne doit pas être inférieure à 1300 ℃, ce qui rend la température de coulée supérieure à la température de formation de film, ce qui peut empêcher la formation de scories secondaires. Le système de vannes doit être conçu de manière à ce que le remplissage soit stable et que la colonne montante d'évacuation des scories soit placée à l'emplacement sujet à l'inclusion de sable. L'installation d'un filtre peut empêcher le laitier primaire de pénétrer dans la cavité.
Veuillez conserver la source et l'adresse de cet article pour réimpression:Défauts de moulage typiques des billes de broyage en fonte ductile multiphasée
Minghé Société de moulage sous pression sont dédiés à la fabrication et à la fourniture de pièces de moulage de qualité et de haute performance (la gamme de pièces de moulage sous pression en métal comprend principalement Moulage sous pression à paroi mince,Chambre chaude coulée sous pression,Chambre froide coulée sous pression), Service rond (Service de moulage sous pression,Usinage CNC,Fabrication de moules,Traitement de surface). Tout moulage sous pression en aluminium personnalisé, moulage sous pression en magnésium ou en zamak/zinc et autres exigences en matière de moulages sont invités à nous contacter.
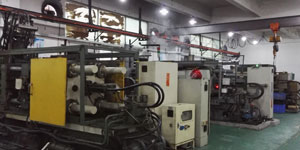
Sous le contrôle des normes ISO9001 et TS 16949, tous les processus sont effectués via des centaines de machines de moulage sous pression avancées, de machines à 5 axes et d'autres installations, allant des blasters aux machines à laver Ultra Sonic.Minghe dispose non seulement d'équipements de pointe, mais également de professionnels équipe d'ingénieurs, d'opérateurs et d'inspecteurs expérimentés pour réaliser la conception du client.
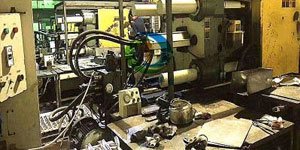
Fabricant sous contrat de moulages sous pression. Les capacités incluent des pièces de moulage sous pression en aluminium à chambre froide à partir de 0.15 lb. jusqu'à 6 lb, configuration à changement rapide et usinage. Les services à valeur ajoutée comprennent le polissage, la vibration, l'ébavurage, le grenaillage, la peinture, le placage, le revêtement, l'assemblage et l'outillage. Les matériaux travaillés comprennent des alliages tels que 360, 380, 383 et 413.
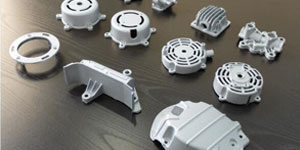
Assistance à la conception de moulage sous pression de zinc/services d'ingénierie simultanés. Fabricant sur mesure de pièces moulées en zinc de précision. Des moulages miniatures, des moulages sous pression à haute pression, des moulages en moules à glissières multiples, des moulages en moules conventionnels, des moulages sous pression unitaires et indépendants et des moulages à cavité scellée peuvent être fabriqués. Les pièces moulées peuvent être fabriquées dans des longueurs et des largeurs allant jusqu'à 24 po avec une tolérance de +/- 0.0005 po.
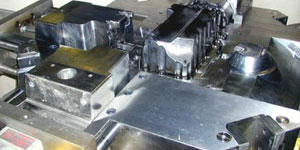
Fabricant certifié ISO 9001 : 2015 de magnésium moulé sous pression, les capacités incluent le moulage sous pression de magnésium sous pression jusqu'à une chambre chaude de 200 tonnes et une chambre froide de 3000 tonnes, la conception d'outillage, le polissage, le moulage, l'usinage, la peinture en poudre et liquide, une assurance qualité complète avec des capacités CMM , assemblage, emballage et livraison.
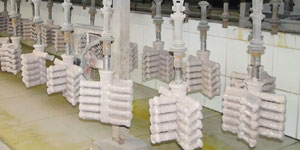
Certifié ITAF16949. Service de casting supplémentaire inclus coulée d'investissement,moulage en sable,Coulée par gravité, Coulée de mousse perdue,Coulée centrifuge,Coulée sous vide,Moulage de moule permanentLes capacités comprennent l'EDI, l'assistance technique, la modélisation solide et le traitement secondaire.
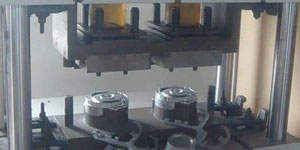
Industries de moulage Études de cas de pièces pour : voitures, vélos, avions, instruments de musique, motomarines, appareils optiques, capteurs, modèles, appareils électroniques, boîtiers, horloges, machines, moteurs, meubles, bijoux, gabarits, télécommunications, éclairage, appareils médicaux, appareils photographiques, Robots, Sculptures, Équipement de sonorisation, Équipement de sport, Outillage, Jouets et plus encore.
Que pouvons-nous vous aider à faire ensuite ?
∇ Aller à la page d'accueil pour Moulage sous pression Chine
→Pièces de fonderie-Découvrez ce que nous avons fait.
→Conseils à propos de Services de moulage sous pression
By Fabricant de moulage sous pression Minghe |Catégories : Articles utiles |Matières Mots clés: Moulage d'aluminium, Moulage de zinc, Coulée de magnésium, Moulage de titane, Fonderie en acier inoxydable, Coulée de laiton,Coulée de bronze,Vidéo de casting,Historique de l'entreprise,Moulage sous pression en aluminium |Commentaires fermés