La méthode et l'application de la fonte en fonte enduite de sable
Qu'est-ce que le moulage en fonte enduit de sable
La coulée de sable dans un moule en fer est un processus de coulée dans lequel une fine couche de sable est recouverte sur la cavité interne d'un moule en métal (appelé moule en fer) pour former un moule. Étant donné que la couche de revêtement de sable est relativement mince (4~8 mm), il est économiquement raisonnable d'utiliser des matériaux de modélisation de haute qualité plus chers. En conséquence, la qualité des pièces moulées est grandement améliorée et les déchets sont considérablement réduits ; en raison de la rigidité du moule de coulée en fer recouvert de sable Très bonne, améliorant ainsi considérablement la précision dimensionnelle et la compacité de la coulée.
L'Allemagne, l'ex-Union soviétique et d'autres pays ont commencé à utiliser le moulage revêtu de sable de fer dans la production de moulage vers les années 1960, principalement pour la production de vilebrequins en fonte ductile, de moyeux de frein, de disques de frein, de chemises de cylindre, d'obus de bombe, de chenilles de char et de bases de moteur , etc. Type de moulages. La recherche d'applications de la Chine sur la fonte en fonte revêtue de sable a commencé au début des années 1970. En 1979, l'Institut de conception mécanique et électrique du Zhejiang et l'usine de tracteurs de Yongkang ont coopéré pour utiliser ce procédé pour la première fois dans la production de moulage en masse d'ébauches de vilebrequin S195. Parallèlement, l'évaluation des performances du vilebrequin en fonte ductile produit par ce procédé a été achevée, en termes de résistance à la fatigue (comparaison de la contrainte limite de fatigue σ-1), de résistance à la rupture (comparaison de la valeur seuil ΔKth et comparaison de la ténacité K1C ) et la durée de vie (Comparaison du test d'endurance du banc de 10000h), etc., par rapport au vilebrequin de moulage au sable, c'est mieux que le moulage au sable. Au cours des 10 années suivantes, le processus a été continuellement amélioré dans son application. Au début des années 1990, sept entreprises avaient appliqué le procédé, en particulier le procédé de coulée de sable de fer pour les vilebrequins monocylindre et les vilebrequins à quatre cylindres. Un grand succès. Les entreprises représentatives au cours de cette période sont l'usine de tracteurs Yongkang, l'usine de machines électriques Shangyu, l'usine de vilebrequins et de bielles Wangdu, l'usine de vilebrequins Wanbei, l'usine de pièces de moteurs à combustion interne Jinhua, l'usine de moteurs diesel de Changzhou, etc. En 1991, la Commission nationale de planification a approuvé le fer mouler le moulage au sable en tant que projet clé de promotion des nouvelles technologies du « huitième plan quinquennal » du pays et a fait de l'Institut de conception mécanique et électrique du Zhejiang l'unité de soutien technique du projet. Il s'agit d'une amélioration significative de la technologie de moulage au sable de moule en fer de mon pays. Le développement a joué un rôle énorme dans la promotion. Après que notre institut ait entrepris le projet de promotion, au cours des 5 à 6 années suivantes, une série de problèmes de moulage au sable revêtu de fer pour la production en série ont été fondamentalement résolus.
Surtout:
- ①Conception et finalisation de la machine de moulage à revêtement sablé, qui a résolu le problème de longue date du réaménagement et du remplacement des carottiers ;
- ②La ligne de production de moulage au sable de type fer standard a été finalisée et standardisée, et la ligne de production de moulage au sable de type fer relativement simple d'origine a été améliorée et appliquée dans des entreprises telles que l'usine de fonte nodulaire de Shanghai ;
- L'application de la fonte enrobée de sable est étendue à certaines pièces moulées avec des processus de coulée plus difficiles, telles que les vilebrequins à six cylindres et les vilebrequins à trois cylindres ;
- Introduction du sable enrobé dans la production de moulage en sable revêtu de fer, améliorant considérablement la qualité du moulage enrobé de sable ;
- La conception du processus de coulée enrobée de sable de moule en fer a été davantage normalisée et le niveau de conception a également été considérablement amélioré. Le logiciel de simulation informatique du processus de moulage au sable de moule en fer et le logiciel de conception assistée par ordinateur du processus de moulage au sable de moule en fer ont été développés.
À l'heure actuelle, près d'une centaine d'entreprises à travers le pays ont appliqué un procédé de coulée enduite de sable pour produire plus de 30 types de pièces moulées telles que des vilebrequins en fonte ductile, des arbres à cames, des arbres d'équilibrage, des corps de soupape résistant à la pression, des chemises de cylindre et résistant à l'usure. disques d'engrenage. La production annuelle est estimée à des moulages. Environ 10×104t. Les entreprises typiques incluent Shanghai Automobile Foundry General Ductile Iron Factory, Shenyang No. 1 Crankshaft Factory, Guangxi Baikuang Group, Yixing Machinery General Factory, Shandong Jiuyang Group, Zhejiang Shuguang Crankshaft Factory, Benxi Tianyuan Crankshaft Factory, Baoding Film Machinery Factory, Shanxi Lucheng Crankshaft Factory , Hebei Xinji Crankshaft Factory, etc. Cependant, ces entreprises ont différentes manières d'introduire le procédé : certaines ont confié à notre institut la conception ou la construction, et d'autres l'ont imité et développé par elles-mêmes. Par conséquent, leur maîtrise du processus de coulée de sable en moule de fonte est très différente. En ne prenant comme exemple que le taux de déchets de moulage en fonte revêtus de sable, de nombreuses entreprises qui ont une meilleure compréhension peuvent le stabiliser à environ 3% et ont obtenu de très bons avantages économiques. Cependant, il existe également quelques entreprises dont le taux de déchets de moulage en fonte recouverts de sable atteint environ 20 %, ce qui compense grandement les avantages économiques de ce procédé. La raison en est que ces entreprises n'ont pas pleinement saisi les éléments essentiels de la conception et de la production du processus, et la gestion de la production est négligée.
Les principales solutions pour la conception et la production réelle du procédé de moulage au sable de moule en fonte :
- ①L'épaisseur de la paroi en fer et l'épaisseur de la couche de revêtement de sable et la combinaison des deux peuvent répondre aux différentes exigences de solidification et de refroidissement des pièces moulées avec différentes épaisseurs de paroi et différents matériaux ;
- ②Méthode de moulage de revêtement de sable pratique et économique pour répondre aux exigences de différentes pièces moulées en matière de qualité de surface et de précision dimensionnelle ;
- Paramètres de processus. Tels que la détermination du système de blocage, du système de tir au sable, du système d'échappement, etc.
- ④ La réalisation de la production en série. Par exemple, la conception et la forme de la chaîne de production et de l'équipement hôte et auxiliaire revêtu de sable ;
- La formulation des règles de process, telles que les règles de coulée, de refroidissement et de déballage, ainsi que l'ajustement de la composition de coulée.
Caractéristiques d'échange thermique de la fonte revêtue de sable de type fer
Une fois que le métal liquide a été versé dans le moule de coulée revêtu de sable de fer, le "moule de revêtement de fer revêtu de sable de coulée" est un système d'échange de chaleur instable. Afin de simplifier le problème, on suppose que la coulée est semi-limitée ; et on suppose que le champ de température de chaque composant du système est distribué en ligne droite. La figure 1 montre une partie du système. De toute évidence, le même flux de chaleur spécifique q traverse chaque composant du système :
Deux critères de transfert thermique représentant respectivement l'intensité d'échange thermique entre la coulée et la couche sablée, et la lingotière en fer et la couche sablée. k1 est le rapport de la résistance thermique de la pièce moulée à la résistance thermique du revêtement de sable ; k2 est le rapport de la résistance thermique du type fer à la résistance thermique du revêtement de sable. Compte tenu de la combinaison de k1 et k2, avec le changement de l'épaisseur du revêtement de sable, les trois situations de transfert de chaleur suivantes entre "coulée-sable revêtement-moule de fer" peuvent réellement se produire :
- Lorsque k≤1 et k2≤1, la couche de revêtement de sable est dans l'épaisseur normale, et la vitesse de refroidissement de la coulée augmente à mesure que l'épaisseur de la couche de revêtement de sable diminue.
- ②Lorsque l'épaisseur de la couche enrobée de sable dépasse une certaine épaisseur, le moule en fer n'a aucun effet sur le refroidissement de la coulée. À ce stade, cela équivaut à un moulage au sable ordinaire ou à un moulage au sable de résine. Étant donné que la conductivité thermique de la couche enrobée de sable est beaucoup plus faible que celle du type de fer, la coulée se refroidit lentement.
- Lorsque k≧1 et k2≧1, l'épaisseur du revêtement de sable est trop mince, ce qui équivaut à la coulée de moules métalliques.
Les caractéristiques d'échange de chaleur ci-dessus ont été confirmées par des expériences. Lorsque l'épaisseur de la couche de revêtement de sable du vilebrequin (CTЦ-14) coulée enduite de sable de type fer passe progressivement de 4 à 32 mm, la quantité de cémentite dans la structure du vilebrequin est continuellement réduite, et la quantité de perlite et de quantité de ferrite continue d'augmenter. Lorsque l'épaisseur de la couche sablée est inférieure à 4 mm, la résistance au refroidissement de la pièce moulée est similaire à celle du type métal (peinture épaisse); lorsque la couche de sable est supérieure à 32 mm, la force de refroidissement est équivalente à celle du moulage au sable de résine ordinaire.
Lorsque la fonte enduite de sable de fer est utilisée dans la production de diverses pièces moulées, c'est par des expériences ou une analogie empirique pour déterminer l'épaisseur de la couche enduite de sable et l'épaisseur de la fonte pour contrôler la vitesse de solidification de la coulée. Par exemple, dans la conception du processus de moulage au sable de moule en fonte de vilebrequin en fonte ductile 490Q, l'épaisseur de la couche de revêtement de sable est de 5 à 8 mm et l'épaisseur de la paroi du moule en fer est de 20 à 30 mm, ce qui produit une haute qualité comme -fonte ductile sans colonnes montantes. La raison principale est :
- ① La couche enrobée de sable régule efficacement la vitesse de refroidissement de la coulée, d'une part, elle rend la coulée moins susceptible d'apparaître blanche et, d'autre part, la vitesse de refroidissement est supérieure à celle de la coulée en sable. Comme le montre la figure 2, lorsque le fer fondu est versé dans le moule en fer recouvert de sable, la température de la coulée chute à environ 930°C après 8 minutes, et il faut 24 minutes pour que le moule en sable tombe à la même température. , et la vitesse de refroidissement est augmentée d'environ 3 fois. En conséquence, les propriétés mécaniques des pièces moulées sont considérablement améliorées.
- ②Le moule en fer n'a aucune concession, mais le mince revêtement de sable peut réduire de manière appropriée la résistance au retrait du moule ; et la rigidité du moule en fer utilise efficacement l'expansion de graphitisation de la fonte ductile pendant le processus de solidification pour obtenir aucune coulée de colonne montante ; en raison du mince revêtement de sable, la cavité n'est pas facile à déformer et la précision de la coulée est grandement améliorée par rapport à celle du moule en sable.
Deux critères de transfert thermique représentant respectivement l'intensité d'échange thermique entre la coulée et la couche sablée, et la lingotière en fer et la couche sablée. k1 est le rapport de la résistance thermique de la pièce moulée à la résistance thermique du revêtement de sable ; k2 est le rapport de la résistance thermique du type fer à la résistance thermique du revêtement de sable. Compte tenu de la combinaison de k1 et k2, avec le changement de l'épaisseur du revêtement de sable, les trois situations de transfert de chaleur suivantes entre "coulée-sable revêtement-moule de fer" peuvent réellement se produire :
- Lorsque k≤1 et k2≤1, la couche de revêtement de sable est dans l'épaisseur normale, et la vitesse de refroidissement de la coulée augmente à mesure que l'épaisseur de la couche de revêtement de sable diminue.
- ②Lorsque l'épaisseur de la couche enrobée de sable dépasse une certaine épaisseur, le moule en fer n'a aucun effet sur le refroidissement de la coulée. À ce stade, cela équivaut à un moulage au sable ordinaire ou à un moulage au sable de résine. Étant donné que la conductivité thermique de la couche enrobée de sable est beaucoup plus faible que celle du type de fer, la coulée se refroidit lentement.
- Lorsque k≧1 et k2≧1, l'épaisseur du revêtement de sable est trop mince, ce qui équivaut à la coulée de moules métalliques.
Les caractéristiques d'échange de chaleur ci-dessus ont été confirmées par des expériences. Lorsque l'épaisseur de la couche de revêtement de sable du vilebrequin (CTЦ-14) coulée enduite de sable de type fer passe progressivement de 4 à 32 mm, la quantité de cémentite dans la structure du vilebrequin est continuellement réduite, et la quantité de perlite et de quantité de ferrite continue d'augmenter. Lorsque l'épaisseur de la couche sablée est inférieure à 4 mm, la résistance au refroidissement de la pièce moulée est similaire à celle du type métal (peinture épaisse); lorsque la couche de sable est supérieure à 32 mm, la force de refroidissement est équivalente à celle du moulage au sable de résine ordinaire.
Lorsque la fonte enduite de sable de fer est utilisée dans la production de diverses pièces moulées, c'est par des expériences ou une analogie empirique pour déterminer l'épaisseur de la couche enduite de sable et l'épaisseur de la fonte pour contrôler la vitesse de solidification de la coulée. Par exemple, dans la conception du processus de moulage au sable de moule en fonte de vilebrequin en fonte ductile 490Q, l'épaisseur de la couche de revêtement de sable est de 5 à 8 mm et l'épaisseur de la paroi du moule en fer est de 20 à 30 mm, ce qui produit une haute qualité comme -fonte ductile sans colonnes montantes. La raison principale est :
- ① La couche enrobée de sable régule efficacement la vitesse de refroidissement de la coulée, d'une part, elle rend la coulée moins susceptible d'apparaître blanche et, d'autre part, la vitesse de refroidissement est supérieure à celle de la coulée en sable. Comme le montre la figure 2, lorsque le fer fondu est versé dans le moule en fer recouvert de sable, la température de la coulée chute à environ 930°C après 8 minutes, et il faut 24 minutes pour que le moule en sable tombe à la même température. , et la vitesse de refroidissement est augmentée d'environ 3 fois. En conséquence, les propriétés mécaniques des pièces moulées sont considérablement améliorées.
- ②Le moule en fer n'a aucune concession, mais le mince revêtement de sable peut réduire de manière appropriée la résistance au retrait du moule ; et la rigidité du moule en fer utilise efficacement l'expansion de graphitisation de la fonte ductile pendant le processus de solidification pour obtenir aucune coulée de colonne montante ; en raison du mince revêtement de sable, la cavité n'est pas facile à déformer et la précision de la coulée est grandement améliorée par rapport à celle du moule en sable.
Taux de refroidissement des pièces moulées enduites de sable de fer
Les facteurs affectant la vitesse de refroidissement des pièces moulées revêtues de sable de fer comprennent l'épaisseur de la paroi de coulée, le matériau de coulée, la température de coulée, l'épaisseur du revêtement de sable, le matériau de revêtement de sable, l'épaisseur du moule en fer, le matériau du moule en fer et la température du moule. Ici, seule l'influence de l'épaisseur de la paroi de coulée (bc), de l'épaisseur du revêtement de sable (bm) et de l'épaisseur du fer (bi) est discutée.
L'influence de bc, bm et bi sur le refroidissement de la coulée
Différentes épaisseurs de paroi de coulée (10 mm, 20 mm, 40 mm, 80 mm, respectivement), différentes épaisseurs de revêtement de sable (4 mm et 32 mm, respectivement) et différentes épaisseurs de paroi de type fer (32 mm et 8 mm, respectivement) réalisées dans les conditions expérimentales suivantes L'influence de la vitesse de refroidissement des pièces moulées revêtues de sable de type fer : la composition chimique de la pièce moulée est de 3.52 %C, 2.46 % Si, 0.80 % Mn, 0.18 % P, 0.031% S, et la composition chimique de la couche revêtue de sable est : 90% sable de quartz, 8% d'argile, poudre de charbon 2%, humidité 3%
- L'épaisseur de la paroi de la coulée, l'épaisseur du revêtement de sable et l'épaisseur de la paroi en fer affectent la vitesse de refroidissement de la coulée. Par conséquent, dans la production réelle, l'épaisseur appropriée du moule en fer et l'épaisseur du revêtement de sable doivent être sélectionnées en fonction des différentes épaisseurs de paroi de coulée pour obtenir la vitesse de refroidissement requise.
- ② Des moulages de différentes épaisseurs peuvent être obtenus en sélectionnant l'épaisseur de revêtement de sable et l'épaisseur de paroi de fer appropriées pour obtenir le même taux de refroidissement. Par exemple, sur la figure 3, la zone I signifie que l'épaisseur est de 10 mm et 20 mm, la zone II signifie 20 mm et 40 mm et la zone III signifie 40 mm. Et le chevauchement entre la plage de refroidissement des pièces moulées de 80 mm.
- ③Bien que bm et bi puissent être modifiés pour obtenir la même vitesse de refroidissement pour des pièces moulées d'épaisseurs différentes, toutes les épaisseurs de pièces moulées ne peuvent pas obtenir la même vitesse de refroidissement. Dans les conditions expérimentales, des coulées d'une épaisseur de 10 mm et d'une épaisseur de 40 mm ne peuvent pas être obtenues La même vitesse de refroidissement (il n'y a pas de chevauchement entre les courbes).
Sélection de l'épaisseur du revêtement de sable (bm) et de l'épaisseur de la paroi en fer (bi)
Bm et bi sont généralement déterminés sur la base de l'expérience ou de l'expérience. Voici une méthode graphique, qui convient pour une épaisseur de coulée (bc) de 10 à 80 mm et une température de déballage de 600 ℃. L'ordonnée est le temps de refroidissement. L'abscisse de la courbe de droite est marquée avec l'épaisseur du revêtement de sable, qui peut être déterminée à partir du temps nécessaire pour que la coulée connue refroidisse à 600°C et de l'épaisseur des différentes coulées, et dans l'épaisseur de paroi de coulée requise (10, 20, 40, 80 mm) est connu, il est alors très pratique de déterminer l'épaisseur du revêtement de sable et l'épaisseur du moule en fer. Trouvez le bc correspondant (par exemple, bc=20mm) à partir de l'axe horizontal de la moitié gauche de la courbe et tracez une ligne horizontale.
Si les deux lignes se coupent dans la plage de la courbe hachurée, cela indique que ce moulage convient au moulage de revêtement de sable de fer. Prolongez cette ligne horizontale vers la droite, et elle s'étendra dans la zone de bc = 20 mm, et tracez une ligne verticale vers le bas dans cette zone pour obtenir l'épaisseur de revêtement de sable requise. Cependant, cette ligne verticale doit être tracée autant que possible vers la droite afin d'obtenir la plus petite épaisseur de revêtement de sable et l'épaisseur de la lingotière en fer. Si l'épaisseur de la couche de revêtement de sable qui doit être déterminée n'est pas dans cette plage, vous pouvez la trouver de la même manière à partir de la plage de courbes adjacente.
- L'épaisseur de la paroi de la coulée, l'épaisseur du revêtement de sable et l'épaisseur de la paroi en fer affectent la vitesse de refroidissement de la coulée. Par conséquent, dans la production réelle, l'épaisseur appropriée du moule en fer et l'épaisseur du revêtement de sable doivent être sélectionnées en fonction des différentes épaisseurs de paroi de coulée pour obtenir la vitesse de refroidissement requise.
- ② Des moulages de différentes épaisseurs peuvent être obtenus en sélectionnant l'épaisseur de revêtement de sable et l'épaisseur de paroi de fer appropriées pour obtenir le même taux de refroidissement. Par exemple, sur la figure 3, la zone I signifie que l'épaisseur est de 10 mm et 20 mm, la zone II signifie 20 mm et 40 mm et la zone III signifie 40 mm. Et le chevauchement entre la plage de refroidissement des pièces moulées de 80 mm.
- ③Bien que bm et bi puissent être modifiés pour obtenir la même vitesse de refroidissement pour des pièces moulées d'épaisseurs différentes, toutes les épaisseurs de pièces moulées ne peuvent pas obtenir la même vitesse de refroidissement. Dans les conditions expérimentales, des coulées d'une épaisseur de 10 mm et d'une épaisseur de 40 mm ne peuvent pas être obtenues La même vitesse de refroidissement (il n'y a pas de chevauchement entre les courbes).
Veuillez conserver la source et l'adresse de cet article pour réimpression: La méthode et l'application de la fonte en fonte enduite de sable
Minghé Société de moulage sous pression sont dédiés à la fabrication et à la fourniture de pièces de moulage de qualité et de haute performance (la gamme de pièces de moulage sous pression en métal comprend principalement Moulage sous pression à paroi mince,Chambre chaude coulée sous pression,Chambre froide coulée sous pression), Service rond (Service de moulage sous pression,Usinage CNC,Fabrication de moules,Traitement de surface). Tout moulage sous pression en aluminium personnalisé, moulage sous pression en magnésium ou en zamak/zinc et autres exigences en matière de moulages sont invités à nous contacter.
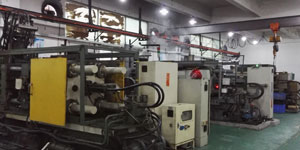
Sous le contrôle des normes ISO9001 et TS 16949, tous les processus sont effectués via des centaines de machines de moulage sous pression avancées, de machines à 5 axes et d'autres installations, allant des blasters aux machines à laver Ultra Sonic.Minghe dispose non seulement d'équipements de pointe, mais également de professionnels équipe d'ingénieurs, d'opérateurs et d'inspecteurs expérimentés pour réaliser la conception du client.
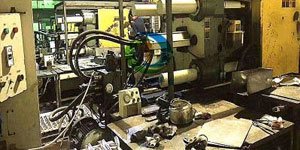
Fabricant sous contrat de moulages sous pression. Les capacités incluent des pièces de moulage sous pression en aluminium à chambre froide à partir de 0.15 lb. jusqu'à 6 lb, configuration à changement rapide et usinage. Les services à valeur ajoutée comprennent le polissage, la vibration, l'ébavurage, le grenaillage, la peinture, le placage, le revêtement, l'assemblage et l'outillage. Les matériaux travaillés comprennent des alliages tels que 360, 380, 383 et 413.
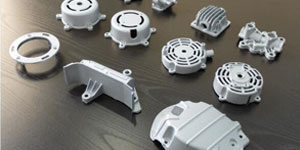
Assistance à la conception de moulage sous pression de zinc/services d'ingénierie simultanés. Fabricant sur mesure de pièces moulées en zinc de précision. Des moulages miniatures, des moulages sous pression à haute pression, des moulages en moules à glissières multiples, des moulages en moules conventionnels, des moulages sous pression unitaires et indépendants et des moulages à cavité scellée peuvent être fabriqués. Les pièces moulées peuvent être fabriquées dans des longueurs et des largeurs allant jusqu'à 24 po avec une tolérance de +/- 0.0005 po.
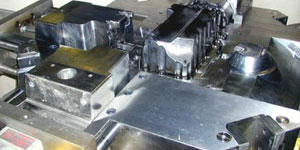
Fabricant certifié ISO 9001 : 2015 de magnésium moulé sous pression, les capacités incluent le moulage sous pression de magnésium sous pression jusqu'à une chambre chaude de 200 tonnes et une chambre froide de 3000 tonnes, la conception d'outillage, le polissage, le moulage, l'usinage, la peinture en poudre et liquide, une assurance qualité complète avec des capacités CMM , assemblage, emballage et livraison.
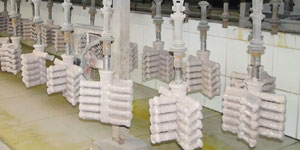
Certifié ITAF16949. Service de casting supplémentaire inclus coulée d'investissement,moulage en sable,Coulée par gravité, Coulée de mousse perdue,Coulée centrifuge,Coulée sous vide,Moulage de moule permanentLes capacités comprennent l'EDI, l'assistance technique, la modélisation solide et le traitement secondaire.
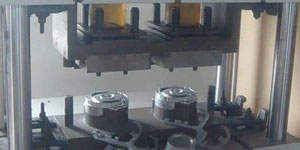
Industries de moulage Études de cas de pièces pour : voitures, vélos, avions, instruments de musique, motomarines, appareils optiques, capteurs, modèles, appareils électroniques, boîtiers, horloges, machines, moteurs, meubles, bijoux, gabarits, télécommunications, éclairage, appareils médicaux, appareils photographiques, Robots, Sculptures, Équipement de sonorisation, Équipement de sport, Outillage, Jouets et plus encore.
Que pouvons-nous vous aider à faire ensuite ?
∇ Aller à la page d'accueil pour Moulage sous pression Chine
→Pièces de fonderie-Découvrez ce que nous avons fait.
→Conseils à propos de Services de moulage sous pression
By Fabricant de moulage sous pression Minghe |Catégories : Articles utiles |Matières Mots clés: Moulage d'aluminium, Moulage de zinc, Coulée de magnésium, Moulage de titane, Fonderie en acier inoxydable, Coulée de laiton,Coulée de bronze,Vidéo de casting,Historique de l'entreprise,Moulage sous pression en aluminium |Commentaires fermés