La conception et l'application du canal chaud pour le moulage sous pression de zinc
Perte du coureur de casting
Quiconque connaît le moulage sous pression saura que le canal ou le matériau restant fait partie du moulage. Bien qu'il n'y ait pas de valeur de profit, il ne peut être évité dans le processus de production. Cette partie du coût n'est généralement calculée que comme un rapport fixe du coût de la coulée. Parallèlement, compte tenu de la recyclabilité des alliages de zinc, la méthode de traitement local la plus courante est le renvoi en temps réel au four de la machine pour la refusion. En raison de la nécessité de maîtriser les problèmes de qualité, l'utilisation de fours de fusion centraux pour recycler les canaux ou les déchets est progressivement acceptée par l'industrie (Figure 1). En ce qui concerne les scories, les grandes usines de moulage sous pression peuvent les recycler elles-mêmes et revendre généralement les matériaux restants aux fournisseurs de matières premières pour de nouveaux matériaux. Le prix de recyclage local des matériaux zinciques est généralement de 50 à 70 % de celui des matériaux neufs. Sans de bonnes conditions environnementales, la manipulation des scories peut facilement provoquer une pollution de l'air.
Prenons l'exemple d'une machine de moulage sous pression à chambre chaude de 160 tonnes. Chaque fois qu'il produit au moins 150 grammes de canaux (hors puits de débordement), en supposant trois équipes, le cycle de production est de 20 secondes, le taux d'utilisation de la machine est de 80% et la production annuelle est Le canal buccal peut atteindre 190 tonnes. Autre exemple : en utilisant une machine de 80 tonnes pour produire 100 grammes de patins à chaque fois, la même hypothèse est faite mais le cycle de production est passé à 12 secondes, et la production annuelle de patins dépasse les 210 tonnes.
On peut voir que la conception du canal affecte l'importance du coût.
Diverses méthodes de recyclage
Parmi les méthodes de recyclage, le renvoi direct de la roue dans le four est la méthode la plus simple et la plus économique. Le canal d'écoulement qui vient d'être produit par fusion par refusion n'a pas besoin d'être préchauffé et l'espace de stockage est réduit, mais il est difficile de contrôler la qualité du matériau fondu, y compris plus de laitier, la température du four est difficile à contrôler et l'alliage la composition ne peut pas être connue; plus important encore, il repose sur le savoir-faire du personnel d'exploitation, tel que la proportion de nouveaux matériaux, et l'observation des changements dans l'eau de la chaudière, tandis que le personnel met des puits de débordement et des flashes dans le four, non seulement aggravera la situation, cette méthode de faire fondre les déchets le cache aussi. Le taux de défauts élevé, l'instabilité de la conception des moules et les paramètres de moulage sous pression ont empêché les responsables d'apporter des améliorations efficaces. Cette méthode n'est pas adaptée à la production de pièces moulées avec des exigences de qualité de surface élevées, et il est difficile de calculer avec précision le coût de la perte de canal.
Les buses de récupération du four central et les produits défectueux sont devenus populaires dans les usines de moulage sous pression à grande production. Ses avantages sont très évidents, c'est-à-dire que le traitement centralisé des matériaux recyclés peut améliorer l'efficacité du four et contrôler la qualité des alliages. Si le métal en fusion est directement introduit dans le four depuis le four central, la température du matériau de la machine de coulée sous pression peut être maintenue stable et il y a moins de scories. S'il est équipé d'un contrôle d'alimentation automatique, le changement du niveau de liquide peut être minimisé. Les fours de fusion centraux actuellement populaires sont divisés en plusieurs catégories : les fours à creuset en fonte de plus grande capacité, les fours à creuset en acier inoxydable et les fours à fusion continue sans creuset. Le transport de liquide de zinc est également divisé en plusieurs catégories : il existe un transport de matériaux liquides de type pont roulant, un type de chariot au sol (sans rail ou sur chenilles) de maintien du four (avec dispositif d'alimentation) et un dispositif de transport par gravité de type auge, qui relie le four et la centrale Fournaise Connectée. Son inconvénient est que l'investissement est relativement important, il ne convient que pour un seul alliage (le petit four à creuset n'est pas abordé ici), et l'atelier occupe une grande surface, donc les petites usines de moulage sous pression (moins de cinq machines) ne sont pas convenable, et les anciens ateliers sont difficiles à transformer et à coopérer. Par conséquent, il n'est généralement replanifié que lorsqu'une nouvelle usine est construite. L'utilisation d'un petit four à creuset pour refondre le matériau de la carotte, en raison du manque d'économies d'échelle, coûtera plus cher que le four central, il n'est donc pas utilisé comme référence pour le calcul.
Calcul du coût de fusion
Il suffit d'utiliser le four de fusion central pour calculer le coût de fusion du canal comme référence. Prenons l'exemple d'une entreprise possédant cinq machines de moulage sous pression de 80 ou 160 tonnes. En supposant que l'investissement de l'équipement est de 500,000 1,000, il est divisé en dix ans. Environ XNUMX XNUMX tonnes de matériaux de recyclage des canaux sont traitées chaque année (la situation réelle devrait être fondue au prorata des nouveaux matériaux, et il est purement pratique de calculer le coût de la refusion).
Le coût de fusion par kilogramme de matériau de grille est de 0.93 $. Selon le calcul des cinq machines ci-dessus, la production annuelle de 1000 tonnes de buses à canaux représente près de 10 millions de yuans. Si le recyclage des produits défectueux est inclus, ce chiffre est encore plus alarmant (comme le poids moyen de coulée est de 100 grammes et le taux de produit défectueux est de 5%, le cycle est de 12 secondes, et la récupération annuelle des produits défectueux est d'environ 53 tonnes). Bien que plus la quantité de traitement est grande, plus le coût de fusion est bas, mais les coûts de protection de l'environnement et de contrôle de qualité strict ne sont pas calculés ici. On peut voir que le coût de la refusion à la porte est assez alarmant et que l'usine de moulage sous pression doit minimiser le coût. Par conséquent, comment réduire le poids de la porte est une clé importante pour contrôler les coûts.
- Loyer d'occupation du terrain 20.000 HKD
- Répartition des investissements en équipement de HKD 50.000
- Frais d'intérêt HKD 5.000
- Entretien et réparation HKD 25.000
- Taxe sur le mazout (100 litres de résidus de pétrole par tonne · 2 USD/litre) 200,000 XNUMX HKD
- Frais d'électricité (1 USD/kWh) 30.000 HKD
- Salaires (y compris les ouvriers d'exploitation, le personnel de direction, le personnel de contrôle de la qualité) 100.000 XNUMX dollars de Hong Kong
- Perte de métal 5% (10 USD/kg) 500,000 XNUMX HKD
- Total : 930.000 XNUMX HKD
Méthode de calcul de la répartition du coût du coureur
Le coût de raffinage de la buse doit être inclus dans le coût de production de la coulée. La méthode la plus courante consiste à multiplier le matériau utilisé par un pourcentage fixe. Par exemple, si le prix de la matière première est de 10 $/kg et que le coût de fusion de la buse est de 3 % du poids de la pièce moulée, 10.3 $ seront utilisés pour calculer le prix de la matière de la pièce moulée. Bien que cette méthode soit simple, elle peut entraîner des écarts dans le calcul des coûts et masquer le coût réel du recyclage des sorties d'eau. Vous pouvez maintenant utiliser l'exemple suivant à titre de comparaison :
- Le poids net de la coulée A est de 400 grammes et le poids du canal de buse est de 100 grammes.
- Le poids net de la coulée B est de 400 grammes et le poids du canal de buse est de 250 grammes.
Si calculé avec un pourcentage fixe :
- Le coût du casting A et du casting B devrait être le même (10.3 $ x 0.4) = 4.12 $.
Si calculé par le coût de récupération réel :
- Le casting A devrait être (10 $ x 0.4 + 0.93 $ x 0.1) = 4.093 $
- Le casting B devrait être (10 $ x 0.4 + 0.93 $ x 0.25) = 4.233 $
Cette différence peut sembler faible, mais avec 20 secondes comme cycle de production, le taux d'utilisation de la machine est de 80% et la production se fait en trois équipes, chaque machine produit 1,261,440 XNUMX XNUMX fois par an. La différence est la suivante :
- Coût des buses de coulée Coulée A Coulée B
- Différence Méthode du rapport fixe HKD 5.197.132 HKD 5.197.132 HKD 0
- Méthode du coût réel 5.163.074 HK$ 5.339.675 HK$ 176.601 HK$
- Différence 34.058 HK$ 142.543 HK$
Si la méthode du rapport fixe est utilisée, les coûts de coulée A et B sont les mêmes, mais en fait, le coût de coulée B est plus élevé. On peut voir dans ce cas que l'utilisation de la méthode du rapport fixe pour calculer la coulée B sous-estime non seulement le coût de production, mais encourage aussi indirectement les concepteurs à ne pas réduire le poids du canal de buse comme objectif, et devrait promouvoir l'application du réel méthode du coût (voir le tableau ci-dessous).
Pour réduire le poids de la porte, il est plus courant d'utiliser une conception de porte courte (buse courte) et de réduire l'épaisseur du gabarit. Il utilise une buse de machine plus longue (généralement 20 mm plus longue que la normale), combinée à une conception de moule de porte à cavité profonde pour réduire le poids de la porte. Ce qui suit est une nouvelle conception de canal de coulée sous pression à chambre chaude.
Conception de canaux de coulée sous pression à chambre chaude
Le canal de coulée sous pression est le chemin du métal en fusion s'écoulant de la buse dans la cavité du moule. Il est composé des branches de la grappe et de la gouttière. En raison de la nécessité de fixer les pièces moulées et de faciliter le démoulage, la carotte doit avoir une inclinaison. En même temps, le bloc séparateur sur le gabarit mobile peut réduire l'épaisseur de la carotte ; l'ajout d'un canal d'eau de refroidissement dans le bloc séparateur facilite l'équilibre de la chaleur du moule, raccourcit le temps de refroidissement, et retire le moulage et l'éjecte. Une étude menée par le CSIRO australien au début des années 1970 a révélé que, avec des erreurs acceptables, l'alliage de zinc liquide peut être résumé comme suit dans le cas du moulage sous pression :
Le liquide se comporte comme un fluide incompressible
Respecter les principes généraux de la mécanique des fluides
Le nombre de Reynold élevé indique que le processus d'écoulement est turbulent.
Selon les résultats de recherche ci-dessus, l'état d'écoulement idéal du métal en fusion devrait être :
1. La section de coureur est circulaire
Étant donné que le rapport circonférence/surface est le plus faible, la résistance de surface du tuyau à section transversale circulaire est la plus faible, de sorte que la perte de charge est également la plus faible. Par rapport à la même section transversale trapézoïdale, la périphérie est réduite de plus de 20 %.
2. Le tuyau d'écoulement est droit
Les tuyaux courbés généreront un écoulement biaisé, mélangeront des bulles dans la masse fondue et entraîneront une perte de pression. Surtout lorsque le rapport rayon de courbure/diamètre du tuyau est inférieur à 1, la perte de charge augmente rapidement.
3. Le profil du canal d'écoulement se rétrécit progressivement en termes de débit de liquide
Le changement rapide du profil du tuyau, qu'il devienne plus grand ou plus petit, entraînera une perte de pression élevée et des courants de Foucault. La meilleure solution est de réduire progressivement le profil pour compenser la perte de résistance causée par la surface du tuyau.
Veuillez conserver la source et l'adresse de cet article pour réimpression:La conception et l'application du canal chaud pour le moulage sous pression de zinc
Minghe Casting Company se consacre à la fabrication et à la fourniture de pièces de moulage de qualité et de haute performance (la gamme de pièces de moulage sous pression en métal comprend principalement Moulage sous pression à paroi mince,Chambre chaude coulée sous pression,Chambre froide coulée sous pression), Service rond (Service de moulage sous pression,Usinage CNC,Fabrication de moules,Traitement de surface). Tout moulage sous pression en aluminium personnalisé, moulage sous pression en magnésium ou en zamak/zinc et autres exigences en matière de moulages sont invités à nous contacter.
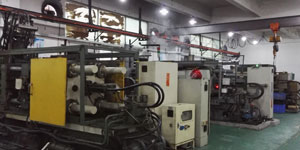
Sous le contrôle des normes ISO9001 et TS 16949, tous les processus sont effectués via des centaines de machines de moulage sous pression avancées, de machines à 5 axes et d'autres installations, allant des blasters aux machines à laver Ultra Sonic.Minghe dispose non seulement d'équipements de pointe, mais également de professionnels équipe d'ingénieurs, d'opérateurs et d'inspecteurs expérimentés pour réaliser la conception du client.
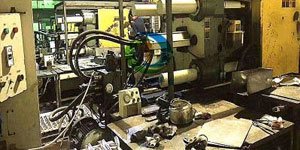
Fabricant sous contrat de moulages sous pression. Les capacités incluent des pièces de moulage sous pression en aluminium à chambre froide à partir de 0.15 lb. jusqu'à 6 lb, configuration à changement rapide et usinage. Les services à valeur ajoutée comprennent le polissage, la vibration, l'ébavurage, le grenaillage, la peinture, le placage, le revêtement, l'assemblage et l'outillage. Les matériaux travaillés comprennent des alliages tels que 360, 380, 383 et 413.
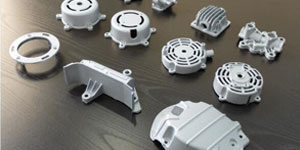
Assistance à la conception de moulage sous pression de zinc/services d'ingénierie simultanés. Fabricant sur mesure de pièces moulées en zinc de précision. Des moulages miniatures, des moulages sous pression à haute pression, des moulages en moules à glissières multiples, des moulages en moules conventionnels, des moulages sous pression unitaires et indépendants et des moulages à cavité scellée peuvent être fabriqués. Les pièces moulées peuvent être fabriquées dans des longueurs et des largeurs allant jusqu'à 24 po avec une tolérance de +/- 0.0005 po.
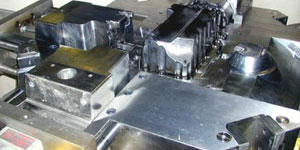
Fabricant certifié ISO 9001 : 2015 de magnésium moulé sous pression, les capacités incluent le moulage sous pression de magnésium sous pression jusqu'à une chambre chaude de 200 tonnes et une chambre froide de 3000 tonnes, la conception d'outillage, le polissage, le moulage, l'usinage, la peinture en poudre et liquide, une assurance qualité complète avec des capacités CMM , assemblage, emballage et livraison.
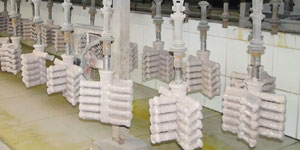
Certifié ITAF16949. Service de casting supplémentaire inclus coulée d'investissement,moulage en sable,Coulée par gravité, Coulée de mousse perdue,Coulée centrifuge,Coulée sous vide,Moulage de moule permanentLes capacités comprennent l'EDI, l'assistance technique, la modélisation solide et le traitement secondaire.
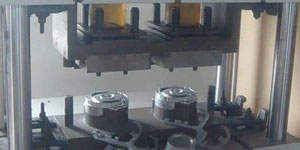
Industries de moulage Études de cas de pièces pour : voitures, vélos, avions, instruments de musique, motomarines, appareils optiques, capteurs, modèles, appareils électroniques, boîtiers, horloges, machines, moteurs, meubles, bijoux, gabarits, télécommunications, éclairage, appareils médicaux, appareils photographiques, Robots, Sculptures, Équipement de sonorisation, Équipement de sport, Outillage, Jouets et plus encore.
Que pouvons-nous vous aider à faire ensuite ?
∇ Aller à la page d'accueil pour Moulage sous pression Chine
→Pièces de fonderie-Découvrez ce que nous avons fait.
→Conseils à propos de Services de moulage sous pression
By Fabricant de moulage sous pression Minghe |Catégories : Articles utiles |Matières Mots clés: Moulage d'aluminium, Moulage de zinc, Coulée de magnésium, Moulage de titane, Fonderie en acier inoxydable, Coulée de laiton,Coulée de bronze,Vidéo de casting,Historique de l'entreprise,Moulage sous pression en aluminium |Commentaires fermés