Différences dans les caractéristiques de solidification de la fonte ductile
D'une manière générale, les pièces moulées en fonte ductile ont une tendance au retrait et à la porosité beaucoup plus grande que les pièces moulées en fonte grise. La prévention des défauts de retrait est souvent un problème très difficile dans la conception de processus. À cet égard, l'expérience résumée à partir de la production réelle est très incohérente, et chacun a ses propres opinions : certains pensent que le principe de la solidification séquentielle doit être suivi, et une grande colonne montante doit être placée en position de solidification finale pour compléter le volume générés pendant le processus de solidification de la coulée. Rétrécissement; Certaines personnes pensent que les pièces en fonte nodulaire n'ont besoin que de petites colonnes montantes, et parfois des pièces moulées saines peuvent être produites sans colonnes montantes.
Pour maximiser la cadence de production du procédé tout en garantissant la qualité des moulages, il ne suffit pas de contrôler la composition chimique de la fonte. Sur la base de la compréhension des caractéristiques de solidification de la fonte ductile, il est nécessaire de contrôler efficacement la fusion, la sphéroïdisation, l'inoculation et le traitement de la fonte. Dans l'ensemble du processus de coulée, la rigidité du moule doit être contrôlée efficacement.
1. Les caractéristiques de solidification de la fonte ductile
La plupart de la fonte nodulaire utilisée dans la production réelle est proche de la composition eutectique. Les moulages à paroi épaisse utilisent une composition hypoeutectique et les moulages à paroi mince utilisent une composition hypereutectique, mais ils ne sont pas loin de la composition eutectique.
Pour la fonte ductile avec des composants eutectiques et hypereutectiques, de petites billes de graphite sont d'abord précipitées de la phase liquide lors de la solidification eutectique. Même pour la fonte nodulaire à composition hypoeutectique, en raison de l'augmentation du degré de surfusion de la fonte fondue après le traitement de sphéroïdisation et d'inoculation, de petites billes de graphite seront d'abord précipitées à une température bien supérieure à la température de transition eutectique d'équilibre. Le premier lot de petites sphères de graphite a été formé à des températures de 1300°C ou plus.
Dans le processus de solidification ultérieur, à mesure que la température diminue, certaines des premières petites sphères de graphite se développent et certaines sont redissoutes dans le fer en fusion, et de nouvelles sphères de graphite seront également précipitées. La précipitation et la croissance des sphères de graphite s'effectuent dans une large gamme de températures.
Lorsque la boule de graphite grandit, la teneur en carbone du fer fondu qui l'entoure diminue et une coquille d'austénite entourant la boule de graphite se formera autour de la boule de graphite. Le temps de formation de la croûte d'austénite est lié à la vitesse de refroidissement de la coulée dans le moule : la vitesse de refroidissement est élevée, et le carbone dans la fonte en fusion n'a pas le temps de diffuser uniformément, et la croûte d'austénite se forme plus tôt ; la vitesse de refroidissement est faible, ce qui est bénéfique pour la vitesse de refroidissement dans la fonte en fusion. Le carbone diffuse uniformément et la croûte d'austénite se forme plus tard.
Avant que la coquille d'austénite ne soit formée, la bille de graphite entre directement en contact avec le fer fondu à haute teneur en carbone, et le carbone dans le fer fondu est facile à diffuser dans la bille de graphite, de sorte que la bille de graphite grandit. Une fois la coquille d'austénite formée, la diffusion du carbone dans le fer fondu vers les billes de graphite est entravée et le taux de croissance des billes de graphite chute fortement. Parce que la chaleur latente de cristallisation libérée lorsque le graphite est précipité à partir de fer fondu est importante, environ 3600 J/g, la chaleur latente de cristallisation libérée lorsque l'austénite est précipitée à partir de fer fondu est inférieure, environ 200 J/g, formant une coquille d'austénite autour la bille de graphite La croissance des billes de graphite est entravée, ce qui va considérablement ralentir le dégagement de la chaleur latente de cristallisation. Dans ces conditions, la progression de la solidification eutectique dépend d'un abaissement supplémentaire de la température pour produire de nouveaux noyaux cristallins. Par conséquent, la transformation eutectique de la fonte à graphite sphéroïdal doit être réalisée dans une plage de températures relativement large, et la plage de températures de solidification est deux fois ou plus que celle de la fonte grise, qui a des caractéristiques de solidification pâteuses typiques.
En bref, les caractéristiques de solidification de la fonte ductile ont principalement les aspects suivants.
1. Large plage de température de solidification
D'après le diagramme d'équilibre de l'alliage fer-carbone, la plage de températures de solidification n'est pas large près de la composition eutectique. En effet, après le traitement de sphéroïdisation et d'inoculation du fer en fusion, le processus de solidification s'écarte loin des conditions d'équilibre. A environ 150°C au-dessus de la température de transition eutectique (1150°C), les sphères de graphite commencent à précipiter, et la température à laquelle la transition eutectique se termine à nouveau Elle peut être d'environ 50°C inférieure à la température de transition eutectique d'équilibre.
Un alliage avec une plage de températures de solidification aussi large est solidifié d'une manière pâteuse, et il est difficile d'obtenir une solidification séquentielle des pièces moulées. Par conséquent, selon le principe de conception de la colonne montante des pièces moulées en acier, le plan de processus consistant à réaliser la solidification séquentielle des pièces moulées et à définir une grande colonne montante au dernier joint chaud solidifié n'est pas très approprié.
Étant donné que les sphères de graphite sont précipitées à des températures très élevées et qu'une transformation eutectique se produit, les deux phases liquide-solide coexistent pendant longtemps, et le retrait liquide et le retrait de solidification se produisent simultanément lors de la solidification du fer en fusion. Par conséquent, il est impossible de compléter complètement le retrait liquide à travers le système de déclenchement et la colonne montante comme les pièces moulées en acier.
2. La précipitation du graphite lors de la transformation eutectique entraîne une expansion volumique
Près de la température eutectique, la densité de l'austénite est d'environ 7.3 g/cm3, et la densité du graphite est d'environ 2.15 g/cm3. Lors de la solidification de la coulée, la précipitation du graphite va provoquer l'expansion volumique du système. Environ 1 % (fraction massique) du graphite précipité peut produire une expansion volumique de 3.4 %.
Une utilisation appropriée de l'expansion de graphitisation dans la fonte peut compenser efficacement le retrait de volume lors de la solidification. Sous certaines conditions, des moulages sonores peuvent être réalisés sans contremarches.
Il convient de souligner que la fonte grise et la fonte nodulaire précipitent le graphite au cours du processus de transformation eutectique et subissent une expansion volumique. Cependant, en raison de la morphologie du graphite et du mécanisme de croissance différents dans les deux fontes, l'effet de l'expansion de la graphitisation sur les performances de coulée de la fonte est également très différent.
Pour le graphite lamellaire dans l'amas eutectique de la fonte grise, la pointe qui est en contact direct avec la fonte en fusion croît préférentiellement. L'essentiel de l'expansion volumique provoquée par la croissance du graphite agit sur la fonte en fusion au contact de la pointe de graphite, ce qui est bénéfique pour la forcer à se remplir de branches d'austénite. L'écart entre eux rend la coulée plus dense.
Le graphite de la fonte nodulaire croît à condition d'être entouré d'une coquille d'austénite. L'expansion de volume qui se produit lorsque la bille de graphite grandit est principalement due à la coquille d'austénite agissant sur les amas eutectiques adjacents, ce qui peut être L'écrasement élargit l'espace entre les amas eutectiques et il est facile d'agir sur les parois du moule du moule à travers les amas eutectiques, provoquant le déplacement des parois du moule.
3. L'expansion de la graphitisation lors de la solidification de la coulée est facile à faire bouger le moule dans le mur
La fonte nodulaire se solidifie selon une méthode de solidification pâteuse. Lorsque la coulée commence à se solidifier, la couche de surface extérieure de la coulée à l'interface moule-métal est beaucoup plus fine que la fonte grise et elle croît lentement. Même après une longue période, la couche de surface est encore solide. Coque fine à faible rigidité. Lorsque l'expansion graphitée se produit à l'intérieur, la coque extérieure peut se déplacer vers l'extérieur si elle n'est pas assez solide pour résister à la force d'expansion. Si la rigidité du moule est faible, le mouvement de la paroi se produira et la cavité se dilatera. En conséquence, non seulement la précision dimensionnelle du moulage est affectée, mais le retrait après expansion par graphitisation ne peut pas être complété, et des défauts tels que la cavité de retrait et la porosité seront générés à l'intérieur du moulage.
4. La teneur en carbone de l'austénite eutectique est supérieure à celle de la fonte grise
Selon un rapport de recherche de RW Heine aux États-Unis, lors de la solidification eutectique de la fonte ductile, la teneur en carbone de l'austénite est supérieure à celle de la fonte grise.
Lorsque l'eutectique de fonte grise se solidifie, les paillettes de graphite de l'amas eutectique sont en contact direct avec l'austénite et la fonte en fusion à haute teneur en carbone. Le carbone dans la fonte fondue diffuse non seulement dans le graphite à travers l'austénite, mais se diffuse également directement dans les flocons de graphite, de sorte que la teneur en carbone de l'austénite à l'interface fer fondu-austénite est relativement faible, environ 1.55%.
Lorsque la fonte nodulaire est solidifiée en eutectique, les billes de graphite de l'amas eutectique n'entrent en contact qu'avec la coquille d'austénite, pas avec la fonte en fusion. Lorsque les billes de graphite grandissent, le carbone contenu dans le fer fondu se diffuse dans les billes de graphite à travers la coquille d'austénite. Par conséquent, la teneur en carbone de l'austénite à l'interface fer fondu-austénite est relativement élevée, atteignant environ 2.15 %.
Lors de la solidification eutectique de la fonte ductile, la teneur en carbone de l'austénite peut être plus élevée. Dans les mêmes conditions de teneur en carbone et en silicium, si la même vitesse de refroidissement est maintenue, la quantité de graphite précipité sera moindre. Par conséquent, lorsque l'eutectique se solidifie, le retrait volumique sera légèrement supérieur à celui de la fonte grise. C'est également l'une des raisons pour lesquelles les pièces moulées en fonte nodulaire sont plus sujettes au retrait et à la porosité. Le maintien d'une faible vitesse de refroidissement pendant le processus de solidification est un facteur propice à l'analyse de la charge du graphite.
Dans les conditions qui peuvent rendre la graphitisation suffisante, la teneur en carbone dans l'austénite eutectique (c'est-à-dire la solubilité solide maximale du carbone dans l'austénite) est liée à la teneur en silicium dans la fonte, et peut généralement être calculée par la formule suivante.
La solubilité solide maximale du carbone dans l'austénite CE=2.045 Si
2. Changement de volume lors de la solidification des pièces moulées en fonte ductile
A partir du moment où la fonte en fusion est coulée dans le moule, jusqu'à la fin de la solidification eutectique et la solidification complète de la coulée, la fonte dans la cavité subira un retrait liquide, une expansion de volume provoquée par la précipitation du graphite primaire, et une solidification retrait causé par la précipitation d'austénite eutectique , Plusieurs changements de volume tels que l'expansion de volume causée par la précipitation de graphite eutectique. Afin de faciliter la description de la variation de volume lors de la solidification de la fonte ductile, il est nécessaire de se référer au diagramme de phases simplifié représenté sur la figure 2 . XNUMX.
1. Retrait liquide du fer en fusion
Une fois que la fonte en fusion est entrée dans le moule, le volume diminue à mesure que la température diminue. La quantité de retrait liquide du fer fondu variera en raison de sa composition chimique et des conditions de traitement, mais cela est généralement ignoré. Généralement, le retrait de volume de 1.5% pour chaque baisse de température de 100°C est pris en compte. La plage de température où se produit le retrait liquide est calculée sur la base de la chute de la température de coulée à la température de transition eutectique d'équilibre (1150°C). Lorsque les pièces en fonte ductile sont coulées à plusieurs températures de coulée différentes, le retrait liquide est indiqué dans le tableau 1.
Tableau 1 Retrait liquide des pièces moulées en fonte ductile lors de la coulée à différentes températures
Température de coulée (℃) | 1400 | 1350 | 1300 |
Retrait liquide (%) | 3.75 | 3.00 | 2.25 |
2. Expansion volumique causée par la précipitation du graphite primaire
Bien que la fonte à graphite sphéroïdal hypoeutectique précipite de petites sphères de graphite au-dessus de la température de liquidus, la quantité est très petite et généralement négligeable.
Comme mentionné précédemment, chaque 1% (fraction massique) de graphite précipité peut produire une expansion de volume de 3.4%. Par conséquent, l'expansion volumique causée par la précipitation du graphite primaire est égale à 3.4G.
Le tableau 2 montre l'expansion volumique provoquée par la précipitation du graphite primaire de plusieurs fontes nodulaires avec différentes teneurs en carbone et en silicium.
Bien que le graphite primaire précipité puisse compenser le retrait liquide lors de la solidification de la fonte, pour les pièces moulées d'une épaisseur de paroi supérieure à 40 mm, des défauts tels que des inclusions de graphite ou un flottement de graphite sont susceptibles de se produire. Dans ce cas, une attention particulière doit être portée au contrôle de la teneur en carbone et en silicium.
Tableau 2 Expansion volumique causée par la précipitation du graphite primaire dans plusieurs fontes nodulaires
- Teneur en carbone de la fonte (%) : 3.6/3.5/3.6/3.7/3.6/3.7/3.8
- Teneur en silicium de la fonte (%) : 2.2/2.4/2.4/2.4/2.6/2.6/2.6
- Teneur en carbone eutectique CC (%)/3.54/3.47/3.47/3.47/3.40/3.40/3.40
- Quantité de précipitation de graphite primaire G initial (%)/0.06/0.03/0.13/0.24/0.21/0.31/0.41
- Expansion volumique causée par la précipitation du graphite primaire (%) : 0.21/0.10/0.44/0.82/0.71/1.05/1.39
3. Retrait de volume causé par la précipitation de l'austénite eutectique
Pour calculer le retrait volumique causé par la précipitation de l'austénite eutectique, la fraction massique de la phase liquide eutectique (ci-après dénommée "quantité de phase liquide eutectique"), la quantité de retrait liquide et l'austénite eutectique précipitée de l'eutectique unitaire la phase liquide doit être considérée. Volume et retrait de solidification. Le calcul du retrait liquide a été décrit ci-dessus. Le retrait de solidification de l'austénite précipitée de la phase liquide eutectique est généralement de 3.5 %.
Le tableau 3 montre le retrait volumique provoqué par la précipitation d'austénite eutectique dans plusieurs fontes nodulaires avec différentes teneurs en carbone et en silicium.
Tableau 3 Retrait volumique causé par la précipitation d'austénite eutectique dans plusieurs fontes nodulaires
- Teneur en carbone de la fonte (%) 3.6/3.5/3.6/3.7/3.6/3.7/3.8
- Teneur en silicium de la fonte (%)/2.2/2.4/2.4/2.4/2.6/2.6/2.6
- Quantité de phase liquide eutectique (%) 99.94/99.97/99.87/99.76/99.79/99.69/99.59
- La quantité d'austénite précipitée dans la phase liquide eutectique unitaire (%)~98.1
- Retrait volumique de l'austénite lors de la coulée à 1400℃ (%)/3.30/3.30/3.30/3.30/3.30/3.29/3.29
- Retrait volumique de l'austénite lors de la coulée à 1350℃ (%)/3.33/3.33/3.33/3.32/3.32/3.32/3.32
- Retrait volumique de l'austénite lors de la coulée à 1300℃ (%) 3.35/3.35/3.35/3.35/3.35/3.34/3.34
Pour plusieurs fontes nodulaires couramment utilisées, maintenez la température de coulée en dessous de 1350℃. Dans la condition d'absence de mouvement de paroi du moule, l'expansion de volume provoquée par la graphitisation pendant la solidification de la coulée peut compenser le retrait liquide et le retrait de solidification. Il est possible de réaliser des moulages sonores sans réglage de contremarches. Lorsque la température de coulée est de 1400 , si un équivalent carbone plus élevé est sélectionné pour la fonte, l'expansion de la graphitisation peut également compenser divers retraits de volume, mais cette méthode ne convient qu'aux pièces moulées à paroi mince, les pièces moulées à paroi plus épaisse sont sujettes à l'inclusion de graphite et laitier Défauts flottants de graphite.
Cependant, les informations répertoriées dans le tableau 5 sont obtenues à partir du diagramme d'équilibre et sont basées sur l'hypothèse que le « carbone potentiellement précipité » est complètement précipité par les cristaux de graphite pendant le processus de solidification. Dans la production réelle, bien sûr, elle doit être basée sur un traitement efficace de sphéroïdisation et d'inoculation, et une graphitisation suffisante est essentielle. Pour les pièces moulées avec des vitesses de refroidissement élevées et les pièces moulées à parois minces, en raison d'une graphitisation insuffisante lors de la solidification eutectique, l'expansion volumique causée par la précipitation du graphite eutectique est inférieure à la valeur calculée ci-dessus, et il est toujours facile de produire des défauts tels que cavités de retrait et porosité de retrait. .
Dans le même temps, la rigidité du moule est également un facteur très important. Si la rigidité du moule de coulée n'est pas élevée et que le mouvement de la paroi se produit pendant la graphitisation et l'expansion, le retrait après expansion ne peut pas être complété et il y aura des défauts tels que la cavité de retrait et la porosité de retrait à l'intérieur du moulage.
3. Conditions de réalisation du casting no-riser
De la fin de la coulée à la fin de la solidification, un retrait liquide et un retrait de solidification se produiront dans la coulée. De plus, comme la fonte ductile est solidifiée dans un procédé de solidification pâteux, il est difficile de compléter complètement le retrait liquide par le système de coulée pour obtenir une coulée sans colonne montante. Le retrait liquide et le retrait de solidification de la fonte doivent être compensés par l'expansion volumique lors de la précipitation des cristaux de graphite. Pour cela, les conditions suivantes doivent être remplies.
La qualité métallurgique du fer fondu est bonne
Dans des circonstances normales, l'équivalent carbone est préférable de choisir 4.3 ou 4.4, et l'équivalent carbone peut être augmenté de manière appropriée pour les moulages à paroi mince. Afin d'augmenter la quantité de graphite précipité, si l'équivalent carbone est maintenu le même, il est plus avantageux d'augmenter la teneur en carbone que d'augmenter la teneur en silicium.
L'opération de sphéroïdisation doit être strictement contrôlée. A condition d'assurer la globalisation du graphite, la quantité de magnésium résiduel doit être réduite au maximum, et la fraction massique de magnésium résiduel doit être maintenue à environ 0.06 %.
Le traitement d'inoculation doit être adéquat. En plus du traitement d'ensemencement réalisé en même temps que le traitement de sphéroïdisation, l'inoculation instantanée doit également être réalisée lors de la coulée. Il est préférable de pré-ensemencer les pièces moulées à paroi mince avant que la fonte en fusion ne soit libérée.
La vitesse de refroidissement lors de la solidification de la coulée ne doit pas être trop élevée
Si la vitesse de refroidissement de la coulée est trop élevée, le graphite ne peut pas être entièrement analysé pendant le processus de solidification, et l'expansion de graphitisation n'est pas suffisante pour compenser le retrait de la fonte, et donc une coulée sans colonne montante ne peut pas être réalisée.
Verser à basse température
Afin de réduire le retrait liquide, la température de coulée est mieux contrôlée en dessous de 1350℃, généralement 1320±20℃.
Utilisation de la porte intérieure en forme de flocon
Afin d'éviter d'expulser la fonte fondue de la grille intérieure pendant la graphitisation et l'expansion, la grille intérieure doit être solidifiée rapidement une fois que la fonte fondue est remplie du moule. Par conséquent, lorsque le schéma de coulée sans colonne montante est adopté, une porte intérieure mince et large doit être utilisée. , Le rapport entre la largeur et l'épaisseur est généralement de 4 à 5. Dans le choix de l'épaisseur de la porte intérieure, la température de coulée doit également être prise en compte et la porte intérieure ne doit pas se solidifier pendant le processus de coulée.
Améliorer la rigidité du moule
Afin d'éviter l'expansion de la cavité lors de l'expansion de graphitisation, l'amélioration de la rigidité du moule est l'une des conditions importantes pour assurer la qualité de la coulée. Indépendamment de l'utilisation du modelage de sable humide d'argile ou de divers modelages de sable auto-durcissables, peu importe l'accent mis sur le « pilonnage solide », il ne sera pas excessif.
Lors de la fabrication de pièces moulées plus grandes avec du sable autodurcissable, des blocs de fer ou de graphite refroidis doivent être placés sur la surface du moule correspondant à certaines parties épaisses de la pièce moulée. Les blocs de fer froid et de graphite ont bien sûr un effet refroidissant, mais ils doivent également avoir une compréhension correcte de leur rôle dans l'amélioration de la rigidité du moule. Dans certains cas, utiliser des briques réfractaires au lieu de blocs de fonte ou de graphite refroidis, dont la fonction principale est d'augmenter la rigidité du moule.
4.Le principe de réglage de la colonne montante lors de l'utilisation de moules à haute rigidité
Lors de l'utilisation de divers processus de moulage au sable auto-durcissable, de moulage de coque ou de processus de moulage d'assemblage de noyaux pour produire des pièces en fonte ductile, la rigidité du moule est relativement élevée, ce qui est pratique d'utiliser l'expansion de graphitisation pour compléter le retrait liquide et le retrait de solidification du fonte. S'il est correctement contrôlé, il est possible d'utiliser un procédé sans colonne montante pour produire des moulages sonores. Si le processus sans colonne montante ne convient pas pour diverses raisons, une colonne montante à col étroit peut être utilisée.
Processus de coulée sans colonne montante
Dans des conditions de rigidité élevée du moule et de bonne qualité métallurgique de la fonte en fusion, le maintien de la vitesse de refroidissement des pièces moulées à un faible niveau, de sorte que le graphite puisse complètement cristalliser, est une condition importante pour réaliser une coulée sans colonne montante.
Selon un rapport de recherche de Goto et al., le temps de solidification des pièces moulées en fonte ductile est supérieur à 20 minutes et la quantité de précipitation de graphite peut atteindre la valeur de saturation.
SI Karsay estime que : le module moyen des coulées n'est pas inférieur à 25 mm est l'une des conditions pour réaliser une coulée sans riser. Plus précisément, l'épaisseur de paroi moyenne des plaques moulées ne doit pas être inférieure à 50 mm.
Les opinions exprimées par Goto et al. et Karsay sont différents, et d'après l'analyse de la vitesse de refroidissement, ils sont en fait les mêmes.
À condition que la qualité métallurgique de la fonte en fusion soit bonne (comme l'utilisation d'un traitement de pré-inoculation ou d'un traitement d'inoculation dynamique et d'autres mesures), certaines pièces moulées à parois minces peuvent également être coulées sans colonnes montantes.
Lors de l'adoption du processus de coulée sans colonne montante, la conception du système de déclenchement peut se référer aux avis suivants.
(1) À propos du coureur
Le coureur doit être plus grand et plus grand. De manière générale, le rapport entre la section transversale de la carotte, la section transversale du canal et la section transversale de la porte intérieure peut être de 4:8:3. Le rapport entre la hauteur de la section transversale et la largeur du patin peut être pris comme (1.8):2.
De cette manière, le système de gating a un meilleur effet de compléter le retrait liquide de la coulée.
(2) À propos de la porte intérieure
Afin d'éviter que la pression générée par l'expansion volumétrique de la coulée dans la cavité ne provoque le retour de la fonte en fusion dans le système de coulée depuis la grille intérieure, une grille intérieure de forme mince doit être utilisée et son épaisseur est choisie pour assurez-vous que la porte intérieure ne sera pas empêchée pendant le processus de coulée. Le principe est de se solidifier et de se solidifier peu après le remplissage de la cavité. D'une manière générale, le rapport de l'épaisseur de la section à la largeur de la grille intérieure peut être de 1:4.
Étant donné que la porte intérieure est mince et que la section transversale est petite, afin de garantir que la cavité est remplie rapidement, plusieurs portes intérieures doivent être prévues pour les pièces moulées plus grandes. De cette façon, il y a aussi pour effet d'égaliser la température de la coulée et de réduire les points chauds.
2. Utilisez un rehausseur de cou mince
S'il existe les situations suivantes, l'utilisation d'un schéma de coulée sans riser ne peut garantir la qualité des coulées, vous pouvez envisager d'utiliser une riser à col étroit :
- L La paroi de la coulée est mince, et la graphitisation est insuffisante lors de la solidification ;
- L Il y a des nœuds chauds dispersés sur le moulage et aucun défaut de retrait n'est autorisé à l'intérieur ;
- L La température de coulée est plus élevée (plus de 1350℃).
La fonction principale de la colonne montante à col étroit est d'apporter un complément partiel au retrait liquide de la coulée, de manière à obtenir une coulée sans retrait ni porosité. Le col étroit relié à la coulée doit être solidifié avant que la coulée ne commence à se solidifier pour empêcher le fer fondu d'entrer dans la colonne montante pendant la graphitisation et l'expansion. L'épaisseur du joint entre le col de la colonne montante et la pièce moulée est la plus petite et l'épaisseur est progressivement augmentée au niveau de la section de transition menant à la colonne montante pour faciliter le réapprovisionnement en fer fondu de la pièce moulée.
L'épaisseur du col montant peut généralement être de 0.4 à 0.6 de l'épaisseur de la partie d'alimentation de la coulée.
Si possible, il est préférable de connecter le patin à la colonne montante et le fer en fusion est rempli par le col de la colonne montante sans porte intérieure.
5.Le principe de réglage de la colonne montante lors de l'utilisation du type de sable humide d'argile
La rigidité du moule de sable vert en argile est médiocre et il est facile d'élargir le volume de la cavité en raison du mouvement de la paroi du moule. L'expansion du volume de la cavité est affectée par de nombreux facteurs, tels que la qualité du sable de moulage, la compacité du moule, la température de coulée et le moule. La tête de pression statique de la fonte en fusion dans la cavité, etc., l'expansion volumique réelle peut être comprise entre 2 et 8 %.
L'expansion volumique de la cavité étant très variable, le principe de réglage du riser est bien entendu différent selon la situation spécifique.
Moulages à parois minces
Les pièces moulées avec une épaisseur de paroi inférieure à 8 mm n'ont généralement pas de mouvement de paroi évident, et le retrait du liquide après le remplissage de la fonte fondue avec le moule n'est pas trop important, et le processus de coulée sans colonne montante peut être utilisé. La conception du système de gating peut se référer à la section précédente.
Pièces moulées avec une épaisseur de paroi de 8 à 12 mm
Pour ce type de pièces moulées, si l'épaisseur de la paroi est uniforme et qu'il n'y a pas de gros points chauds, tant que la coulée à basse température est strictement contrôlée, le processus de coulée sans colonne montante peut également être utilisé.
S'il y a un joint chaud et que les trous de retrait et le retrait ne sont pas autorisés à l'intérieur, une colonne montante à col étroit doit être réglée en fonction de la taille du joint chaud.
Pièces moulées avec une épaisseur de paroi supérieure à 12 mm
Dans la production de telles pièces moulées avec des moules en sable vert d'argile, le mouvement de paroi est assez important et il est plus difficile de fabriquer des pièces moulées sans défauts internes. Lors de la formulation du plan de traitement, envisagez d'abord l'utilisation d'une colonne montante à col étroit et contrôlez strictement le versement à basse température. Si cette solution ne peut pas résoudre le problème, une colonne montante spéciale doit être conçue.
Utilisez du sable humide argileux pour produire des pièces en fonte ductile. Si vous souhaitez installer une colonne montante, il est préférable de faire :
- LA fine grille interne est utilisée pour la solidifier une fois le moule rempli. Une fois la porte intérieure solidifiée, le moulage et la colonne montante forment un tout, qui n'est pas connecté au système de porte ;
- L Lorsque la coulée subit un retrait liquide, la colonne montante reconstitue le fer fondu à la coulée ;
- L Lorsque la coulée est graphitée et expansée, la fonte en fusion s'écoule vers la colonne montante pour relâcher la pression dans la cavité. Réduire son effet sur la paroi du moule ;
- L Lorsque le corps de coulée subit un retrait secondaire après graphitisation et expansion, la colonne montante peut fournir du liquide de fer d'alimentation à la coulée.
Cela ne semble pas compliqué à dire, mais en fait, de nombreux facteurs d'influence doivent être pris en compte dans la conception de la colonne montante, et jusqu'à présent, aucun schéma spécifique efficace n'a été vu, et il n'y a pas d'ensemble complet facile à utiliser. de données. En production, il est nécessaire de prendre en compte la qualité des pièces moulées et le taux de rendement du procédé, et souvent d'explorer et d'expérimenter.
Veuillez conserver la source et l'adresse de cet article pour réimpression: Différences dans les caractéristiques de solidification de la fonte ductile
Minghé Société de moulage sous pression sont dédiés à la fabrication et à la fourniture de pièces de moulage de qualité et de haute performance (la gamme de pièces de moulage sous pression en métal comprend principalement Moulage sous pression à paroi mince,Chambre chaude coulée sous pression,Chambre froide coulée sous pression), Service rond (Service de moulage sous pression,Usinage CNC,Fabrication de moules,Traitement de surface). Tout moulage sous pression en aluminium personnalisé, moulage sous pression en magnésium ou en zamak/zinc et autres exigences en matière de moulages sont invités à nous contacter.
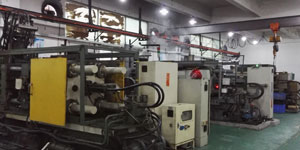
Sous le contrôle des normes ISO9001 et TS 16949, tous les processus sont effectués via des centaines de machines de moulage sous pression avancées, de machines à 5 axes et d'autres installations, allant des blasters aux machines à laver Ultra Sonic.Minghe dispose non seulement d'équipements de pointe, mais également de professionnels équipe d'ingénieurs, d'opérateurs et d'inspecteurs expérimentés pour réaliser la conception du client.
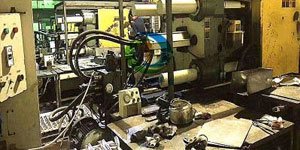
Fabricant sous contrat de moulages sous pression. Les capacités incluent des pièces de moulage sous pression en aluminium à chambre froide à partir de 0.15 lb. jusqu'à 6 lb, configuration à changement rapide et usinage. Les services à valeur ajoutée comprennent le polissage, la vibration, l'ébavurage, le grenaillage, la peinture, le placage, le revêtement, l'assemblage et l'outillage. Les matériaux travaillés comprennent des alliages tels que 360, 380, 383 et 413.
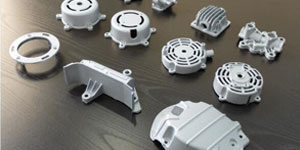
Assistance à la conception de moulage sous pression de zinc/services d'ingénierie simultanés. Fabricant sur mesure de pièces moulées en zinc de précision. Des moulages miniatures, des moulages sous pression à haute pression, des moulages en moules à glissières multiples, des moulages en moules conventionnels, des moulages sous pression unitaires et indépendants et des moulages à cavité scellée peuvent être fabriqués. Les pièces moulées peuvent être fabriquées dans des longueurs et des largeurs allant jusqu'à 24 po avec une tolérance de +/- 0.0005 po.
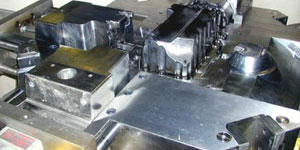
Fabricant certifié ISO 9001 : 2015 de magnésium moulé sous pression, les capacités incluent le moulage sous pression de magnésium sous pression jusqu'à une chambre chaude de 200 tonnes et une chambre froide de 3000 tonnes, la conception d'outillage, le polissage, le moulage, l'usinage, la peinture en poudre et liquide, une assurance qualité complète avec des capacités CMM , assemblage, emballage et livraison.
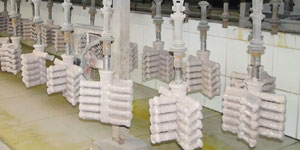
Certifié ITAF16949. Service de casting supplémentaire inclus coulée d'investissement,moulage en sable,Coulée par gravité, Coulée de mousse perdue,Coulée centrifuge,Coulée sous vide,Moulage de moule permanentLes capacités comprennent l'EDI, l'assistance technique, la modélisation solide et le traitement secondaire.
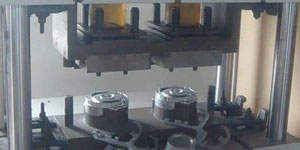
Industries de moulage Études de cas de pièces pour : voitures, vélos, avions, instruments de musique, motomarines, appareils optiques, capteurs, modèles, appareils électroniques, boîtiers, horloges, machines, moteurs, meubles, bijoux, gabarits, télécommunications, éclairage, appareils médicaux, appareils photographiques, Robots, Sculptures, Équipement de sonorisation, Équipement de sport, Outillage, Jouets et plus encore.
Que pouvons-nous vous aider à faire ensuite ?
∇ Aller à la page d'accueil pour Moulage sous pression Chine
→Pièces de fonderie-Découvrez ce que nous avons fait.
→Conseils à propos de Services de moulage sous pression
By Fabricant de moulage sous pression Minghe |Catégories : Articles utiles |Matières Mots clés: Moulage d'aluminium, Moulage de zinc, Coulée de magnésium, Moulage de titane, Fonderie en acier inoxydable, Coulée de laiton,Coulée de bronze,Vidéo de casting,Historique de l'entreprise,Moulage sous pression en aluminium |Commentaires fermés