Les causes des défauts courants dans les blocs-cylindres en fonte grise
L'émergence du verre soluble a une histoire de plus de 300 ans, mais en tant que liant pour la coulée et la fabrication de noyaux, ce n'est qu'en 1947 que le procédé de sable de verre soluble avec du CO2 comme agent de durcissement a été développé par le Dr L. Petrzela de la République tchèque. de.
Pendant plus d'un demi-siècle, les gens sont passés par quatre processus majeurs pour comprendre le mécanisme de durcissement du sable de silicate de sodium dans le cadre de recherches et d'explorations continues, à savoir :
- 1) La théorie du durcissement chimique au CO2 par le professeur Lias (Лясс AM) de l'ex-Union soviétique dans les années 1950. Il a divisé le processus de durcissement en décomposition du silicate, formation de gel de silice et perte partielle d'eau du gel de silice. Il croyait à tort que la précipitation de l'acide silicique et la formation de gel de silice étaient la force du sable de silicate de sodium durci au CO2. Source unique
- 2) Dans les années 1960, le processus de durcissement du sable de verre soluble au CO2 par Worthington R était considéré comme une combinaison de méthodes de durcissement chimiques et physiques, c'est-à-dire du silicate de sodium décomposé en acide silicique libre sous la catalyse du CO2, puis condensé en gel de silicone. La déshydratation du gel de silicone conduira à un "collage de gel de silicone", qui est une sorte de "durcissement chimique"; la déshydratation du verre soluble n'ayant pas réagi conduira à une "liaison vitreuse", qui appartient au "durcissement physique". Mais il croit à tort que le durcissement chimique est une mesure de durcissement efficace et rapide, tout en ignorant le rôle important du durcissement physique ;
- 3) Au début des années 1990, le verre d'eau durci au CO2 fabriqué par Zhu Chunxi et d'autres dans mon pays était essentiellement la théorie du "durcissement physique". Il pense que le verre soluble soufflant le durcissement au CO2 doit se faire dans des conditions très spéciales, c'est-à-dire que le verre soluble est enduit à la surface des particules de sable pour former un film d'une épaisseur de quelques microns seulement, ce qui peut créer de bonnes conditions de déshydratation et favorisent la solidification rapide du verre soluble. , On dit donc que "le durcissement du verre soluble est essentiellement un durcissement physique". L'inconvénient de ce point de vue est qu'il suit toujours le point de vue erroné selon lequel l'acide silicique libre est précipité lorsque le silicate de sodium réagit avec le CO2.
- 4) À la fin des années 1990, Zhu Chunxi et d'autres, basés sur la théorie selon laquelle le durcissement au CO2 appartient à la chimie physique dure, après des recherches plus approfondies, ils ont proposé que le verre soluble durci soit une sorte de "verre soluble déshydraté à module élevé" . La théorie, c'est-à-dire que l'acide silicique généré par la réaction ne peut pas être précipité à l'état libre, mais est redissous dans le verre soluble n'ayant pas réagi, augmentant le module de ce dernier pour réaliser le durcissement du verre soluble. Par exemple, lorsque du vinaigre organique est utilisé pour durcir le sable de silicate de sodium, un film de silicate de sodium durci à haut module avec un module uniforme de la surface et de l'intérieur peut être obtenu, ce qui est proche de M = 3.45. Lorsque le CO2 est utilisé pour durcir le verre soluble, un film de verre soluble à haut module durci avec un module progressivement décroissant depuis la surface et l'intérieur, avec un M moyen proche de 3.79 est obtenu.
Par conséquent, le verre soluble durci est une sorte de verre soluble à module élevé déshydraté, qui peut être solidifié par perte d'alcali et d'eau.
En 2008, German C. Wallenhorst et al. croyait que le mode de réaction de durcissement du sable de silicate de sodium peut être divisé en deux types suivants, comme le montre la figure 1.
1.1 Mode A
En présence d'une solution acide ou d'un agent de durcissement (CO2 ou ester organique), la vitesse de croissance des particules colloïdales dans le verre soluble est extrêmement lente, mais s'agrège directement en un gel de réseau tridimensionnel.
1.2 Mode B
Dans les conditions d'une solution alcaline sans agent de durcissement (sous chauffage), les particules colloïdales se développent d'abord et forment une structure de sol ; et les particules de sol individuelles ne peuvent former une structure de réseau tridimensionnel que sous l'action de réticulation de l'accélérateur.
Les particules individuelles d'acide silicique peuvent se développer en grosses particules colloïdales (mode B), ou elles peuvent s'agréger en structures de gel en chaîne et en réseau (mode A). Dans ces deux modes de réaction de durcissement, le mécanisme de réaction chimique est le même à travers la réaction de condensation entre des groupes fonctionnels silanol simples, la déshydratation et la connexion à un nouveau composé siloxane.
"On peut voir que le mode de réaction de durcissement du verre soluble dépend principalement de la valeur du pH de la solution de liant. Dans la solution aqueuse d'acide silicique à faible valeur de PH (en présence de CO2 ou d'un agent de durcissement ester organique), il est bénéfique de le mode de réaction de durcissement A. A ce moment, la vitesse de réaction de durcissement est très lente et les particules colloïdales s'agrègent les unes avec les autres pour former une structure de gel poreux ramifié.
Lorsque la valeur du pH de la solution aqueuse d'acide silicique>7 (pas de CO2 ou d'esters organiques et amorcée par la chaleur), le mode de réaction de durcissement B procède à la formation d'une structure de sol à grosses particules. Dans le cas d'une solution à pH élevé, les molécules croissent si vite que la réaction de durcissement est principalement due à la croissance continue de particules colloïdales en plus de la formation d'une structure de gel. En effet, le phénomène d'agrégation dans une structure en réseau est inhibé.
Lorsque le sable de verre soluble avec accélérateur est chauffé et durci, le mécanisme de réaction de durcissement est le suivant :
Une fois que le noyau de verre soluble est chauffé et stimulé, il procède selon le mode de réaction de durcissement B (voir Figure 1), et les particules colloïdales se développent et forment une structure de sol. A ce moment, au fur et à mesure que la réaction de durcissement progresse, soit une structure granulaire sensiblement uniforme soit une structure avec quelques défauts peut se former. Le nombre de défauts affectera directement ses performances d'utilisation ultérieures, telles que la résistance à l'humidité du noyau de sable.
Lorsque le noyau de sable de verre soluble est durci par le gaz CO2, ou lorsque l'ester organique est durci, un seul sol ion se déroulera selon le mode de réaction de durcissement A, et les particules colloïdales s'agrégeront et se lieront les unes aux autres pour former une structure de gel . S'il n'y a pas d'agent de durcissement dans la solution alcaline d'acide silicique, les particules de gel de silice peuvent exister de manière stable dans la solution alcaline. En effet, la surface des particules colloïdales a l'effet électrique de la double couche électrique d'ions sodium chargés positivement. Le résultat de particules colloïdales qui se repoussent et ne se combinent pas. S'il y a un accélérateur inorganique dans le processus de durcissement du sable de silicate de sodium, il peut agir comme un agent de réticulation entre les particules colloïdales, c'est-à-dire que l'accélérateur inorganique peut relier les particules de sol individuelles les unes aux autres via les groupes réactifs actifs à sa surface . Ensemble, un réseau tridimensionnel de squelette de silicate est formé, de sorte que le liant est rapidement solidifié et que les particules de sable sont liées et formées.
Si aucun accélérateur inorganique n'est ajouté, la formation du squelette de silicate de la structure du réseau est très lente pendant le processus de durcissement secondaire et le noyau de sable préparé présente des inconvénients tels qu'une faible résistance instantanée et une mauvaise résistance à l'humidité.
Grâce à l'analyse du mécanisme de durcissement du verre soluble ci-dessus, on peut voir que bien qu'il existe différentes méthodes de durcissement pour le sable de silicate de sodium, elles peuvent être classiquement divisées en durcissement physique et durcissement chimique, et le mécanisme de durcissement est cohérent et unifié. de. C'est-à-dire que la méthode de durcissement par ester organique du sable de silicate de sodium a exactement le même mécanisme de durcissement que la méthode de durcissement au CO2, qui est principalement basée sur le durcissement physique de la déshydratation du verre soluble n'ayant pas réagi, qui est la principale raison de la résistance du moule (noyau) sable; pour générer du silicium Le durcissement chimique du gel est complété par la solidification rapide du sable de silicate de sodium, l'établissement de la résistance initiale, l'amélioration de la résistance à l'humidité et la stabilité au stockage du sable, et le processus synergique de durcissement chimique et de durcissement physique .
Sur la base de l'analyse approfondie du mécanisme de durcissement du sable de silicate de sodium ci-dessus avec différentes méthodes de durcissement (méthode au CO2, méthode aux esters organiques et méthode de chauffage + accélérateur, etc.), et explorer l'influence de la force de liaison du verre soluble et de l'humidité résistance au niveau de la structure moléculaire Les principaux facteurs d'influence entre le verre soluble et les performances pliables, afin de modifier la structure et la morphologie du verre soluble d'un point de vue moléculaire, et de développer un nouveau procédé de durcissement thermique + accélérateur de verre soluble, de manière à améliorer la force de liaison du sable de verre soluble. L'objectif d'augmenter sa résistance à l'humidité et d'améliorer ses performances d'effondrement est d'améliorer et d'améliorer en permanence les performances du procédé de sable de silicate de sodium tout en surmontant en permanence ses défauts inhérents, devenant ainsi le moulage vert le plus prometteur du 21e siècle. Nettoyez l'adhésif.
2 Performances du procédé du nouveau sable de liant inorganique
2.1 Performance de force de liaison
En préparant du phosphate amorphe et en l'utilisant pour modifier le verre soluble, la force de liaison du liant inorganique est améliorée.
Afin d'améliorer encore la force de liaison du sable de silicate de sodium, un accélérateur organique a été développé. Grâce à la réticulation chimique et au durcissement, la résistance instantanée du sable de silicate de sodium peut être considérablement améliorée. Lorsque l'accélérateur organique est ajouté à 1.5%, la résistance à la traction instantanée La résistance peut atteindre 1.8 MPa.
2.2 Résistance à l'humidité du sable de noyau
D'une manière générale, la force du sable de verre soluble durci par l'air chaud diminuera progressivement dans un environnement humide. Afin d'améliorer la résistance à l'humidité du sable de silicate de sodium, d'une part, la teneur en humidité résiduelle dans le sable est complètement éliminée après durcissement et, d'autre part, la méthode de réticulation chimique et de durcissement est utilisée. Lorsque l'accélérateur est ajouté à 1.5%, la résistance à la traction du sable de silicate de sodium ne diminuera pas, mais augmentera légèrement après avoir été placé à 20°C et 80% d'humidité relative pendant 24 heures
2.3 Propriétés d'écoulement du sable de noyau
La tension superficielle du verre soluble lui-même est relativement grande, ce qui rend la mouillabilité entre le verre soluble et le sable de silice médiocre, et la viscosité du verre soluble pour la coulée est généralement trop grande, de sorte que la viscosité du sable de verre soluble après le mélange est très important et les particules de sable adhèrent au verre d'eau. La résistance au mouvement est très importante, ce qui entraîne une mauvaise fluidité du sable de silicate de sodium, et finalement réduit considérablement la compacité du noyau de grenaille. Dans cette expérience, des tensioactifs et des lubrifiants solides ont été ajoutés pour améliorer considérablement la fluidité du sable de moulage.
Basée sur l'utilisation de tensioactifs et de lubrifiants solides, cette expérience a développé un accélérateur sphérique, qui a grandement amélioré la fluidité du sable de verre soluble.
Veuillez conserver la source et l'adresse de cet article pour réimpression:Les causes des défauts courants dans les blocs-cylindres en fonte grise
Minghé Société de moulage sous pression sont dédiés à la fabrication et à la fourniture de pièces de moulage de qualité et de haute performance (la gamme de pièces de moulage sous pression en métal comprend principalement Moulage sous pression à paroi mince,Chambre chaude coulée sous pression,Chambre froide coulée sous pression), Service rond (Service de moulage sous pression,Usinage CNC,Fabrication de moules,Traitement de surface). Tout moulage sous pression en aluminium personnalisé, moulage sous pression en magnésium ou en zamak/zinc et autres exigences en matière de moulages sont invités à nous contacter.
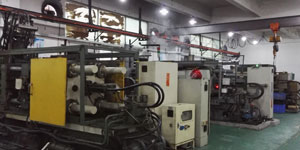
Sous le contrôle des normes ISO9001 et TS 16949, tous les processus sont effectués via des centaines de machines de moulage sous pression avancées, de machines à 5 axes et d'autres installations, allant des blasters aux machines à laver Ultra Sonic.Minghe dispose non seulement d'équipements de pointe, mais également de professionnels équipe d'ingénieurs, d'opérateurs et d'inspecteurs expérimentés pour réaliser la conception du client.
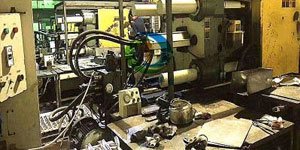
Fabricant sous contrat de moulages sous pression. Les capacités incluent des pièces de moulage sous pression en aluminium à chambre froide à partir de 0.15 lb. jusqu'à 6 lb, configuration à changement rapide et usinage. Les services à valeur ajoutée comprennent le polissage, la vibration, l'ébavurage, le grenaillage, la peinture, le placage, le revêtement, l'assemblage et l'outillage. Les matériaux travaillés comprennent des alliages tels que 360, 380, 383 et 413.
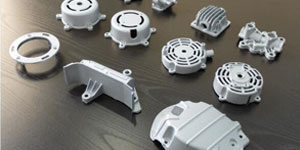
Assistance à la conception de moulage sous pression de zinc/services d'ingénierie simultanés. Fabricant sur mesure de pièces moulées en zinc de précision. Des moulages miniatures, des moulages sous pression à haute pression, des moulages en moules à glissières multiples, des moulages en moules conventionnels, des moulages sous pression unitaires et indépendants et des moulages à cavité scellée peuvent être fabriqués. Les pièces moulées peuvent être fabriquées dans des longueurs et des largeurs allant jusqu'à 24 po avec une tolérance de +/- 0.0005 po.
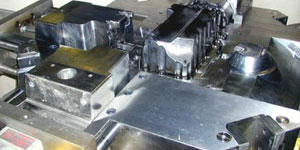
Fabricant certifié ISO 9001 : 2015 de magnésium moulé sous pression, les capacités incluent le moulage sous pression de magnésium sous pression jusqu'à une chambre chaude de 200 tonnes et une chambre froide de 3000 tonnes, la conception d'outillage, le polissage, le moulage, l'usinage, la peinture en poudre et liquide, une assurance qualité complète avec des capacités CMM , assemblage, emballage et livraison.
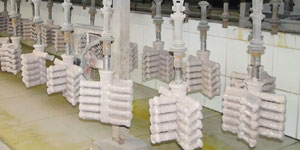
Certifié ITAF16949. Service de casting supplémentaire inclus coulée d'investissement,moulage en sable,Coulée par gravité, Coulée de mousse perdue,Coulée centrifuge,Coulée sous vide,Moulage de moule permanentLes capacités comprennent l'EDI, l'assistance technique, la modélisation solide et le traitement secondaire.
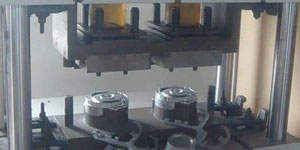
Industries de moulage Études de cas de pièces pour : voitures, vélos, avions, instruments de musique, motomarines, appareils optiques, capteurs, modèles, appareils électroniques, boîtiers, horloges, machines, moteurs, meubles, bijoux, gabarits, télécommunications, éclairage, appareils médicaux, appareils photographiques, Robots, Sculptures, Équipement de sonorisation, Équipement de sport, Outillage, Jouets et plus encore.
Que pouvons-nous vous aider à faire ensuite ?
∇ Aller à la page d'accueil pour Moulage sous pression Chine
→Pièces de fonderie-Découvrez ce que nous avons fait.
→Conseils à propos de Services de moulage sous pression
By Fabricant de moulage sous pression Minghe |Catégories : Articles utiles |Matières Mots clés: Moulage d'aluminium, Moulage de zinc, Coulée de magnésium, Moulage de titane, Fonderie en acier inoxydable, Coulée de laiton,Coulée de bronze,Vidéo de casting,Historique de l'entreprise,Moulage sous pression en aluminium |Commentaires fermés