Les mesures concrètes pour résoudre les défauts de moule collant du moulage sous pression
1 Raisons du collage des pièces moulées sous pression
Les risques de coller des défauts de moule aux pièces moulées sont les suivants : lorsque les pièces moulées sous pression sont collées au moule, la surface la plus claire est rugueuse, ce qui affecte la rugosité de l'apparence ; la surface de coulée lourde pèle, manque de viande, de souches et de fissures, et peut également provoquer des fuites de pièces moulées, ce qui entraîne la mise au rebut des pièces moulées par lots. Il existe de nombreux phénomènes de collage par moulage sous pression, et les raisons fondamentales du collage sont les suivantes.
1.1 L'affinité de l'alliage de moulage sous pression et de l'acier moulé
Plus l'affinité entre l'alliage de coulée sous pression et l'acier est grande, plus il est facile de fondre et de se lier les uns aux autres. Une fois que l'alliage de moulage sous pression est lié à la paroi du moule, il y aura une plus grande résistance au démoulage, et le moulage sera tendu lors du démoulage. Observez visuellement qu'il y a des traces de dessin telles que surface rugueuse, écaillage ou manque de matière au niveau de la partie collante du moulage (note : à distinguer du dépôt de carbone), et le moulage sera déchiré et endommagé en cas d'adhérence importante. La surface de la cavité du moule est visuellement collée à un alliage de coulée stratifié et la couleur est blanche.
Après que l'injection ou l'écoulement du liquide d'alliage de moulage sous pression ait impacté la paroi ou le noyau du moule, la température de la paroi ou du noyau du moule augmente. À des températures élevées, l'alliage liquide et l'acier du moule de la paroi du moule fondent et se soudent ensemble pour provoquer une adhérence mutuelle. Plus la température du liquide d'alliage est élevée, plus la vitesse d'injection est élevée, plus la température du moule est élevée et plus la dureté du moule est faible, plus l'affinité entre le liquide d'alliage d'aluminium et l'acier du moule est élevée, plus il est susceptible de fondre et de souder l'adhérence. Lorsque la surface de la matrice collée à l'alliage de coulée sous pression est démoulée, la surface de la cavité et la surface de coulée sont comprimées et déchirées, ce qui déchirera la surface de la coulée, et la surface de la coulée apparaîtra comme une contrainte de moule collante.
Plus la vitesse de remplissage du liquide d'alliage de coulée sous pression dans le canal interne est élevée, plus l'impact du flux de métal en fusion sur la paroi du moule est important. Le métal en fusion impacte directement le noyau ou la paroi, et la force d'impact est convertie en énergie thermique. Non seulement la température du liquide d'alliage augmentera, mais la température du moule au niveau de la partie impactée augmentera également beaucoup, ce qui augmente considérablement l'affinité entre le liquide d'alliage d'aluminium et l'acier du moule. Par conséquent, le collage du moule est le plus susceptible de se produire dans la partie du canal d'alimentation dans le moule qui est soumise à l'impact à grande vitesse du liquide d'alliage. S'il heurte le côté du moule fixe, la force de tassement du moulage du côté du moule fixe est augmentée.
La dureté du moule est insuffisante, et la surface du moule pendant le démoulage sera comprimée et déformée par l'alliage de moulage sous pression, ou le noyau du moule sera plié et déformé, augmentant ainsi la résistance du moule au démoulage de la pièce moulée.
Mauvaise utilisation des matériaux du moule, lorsque la température du moule est élevée, l'alliage de moulage sous pression adhère facilement à la surface du moule.
1.2 Angle de démoulage
La pente de démoulage du moule est trop faible (ou pas de pente de démoulage, ou pente de démoulage inversée), le côté du moule est irrégulier (érosion, écrasement, défaut, etc.), la surface est rugueuse, etc., et la coulée est entravée dans le sens de démoulage. La surface de la pièce moulée est sollicitée par le moule lorsque la pièce moulée est démoulée, et la surface de la pièce moulée présente des marques de contrainte linéaires le long de la direction d'ouverture du moule, c'est-à-dire que les cicatrices au début de la cavité profonde de la pièce moulée sont larges et profonde, tandis que les cicatrices à l'extrémité du moule deviennent progressivement plus petites voire disparaissent. Tendez tout le visage.
- (1) La conception et la fabrication du moule ne sont pas correctes et la pente de démoulage de la cavité du moule fixe ou de la surface de formation du noyau est trop petite ou présente une pente inverse, ce qui rend la résistance de coulée au démoulage très grande. Pour les pièces ne nécessitant pas d'inclinaison de démoulage de la coulée, il est préférable de laisser une surépaisseur d'usinage à la coulée pour réaliser l'inclinaison de démoulage, puis de laisser les pièces sans inclinaison de démoulage de la coulée se terminer par la suite.
- (2) La déformation par écrasement sur le noyau du moule ou la paroi du moule et la saillie sur le côté de la cavité affecteront le démoulage de la pièce moulée, et les rayures sur la surface de formage ou la fissuration du moule affecteront également le démoulage de la pièce moulée .
La surface de moulage fixe du moule est trop rugueuse, ou présente des traces de traitement et de fabrication, n'est pas assez lisse, ou les lignes des traces de traitement et de polissage sont incompatibles avec le sens de démoulage, ou la planéité dans le sens de démoulage est mauvaise, de telles mauvaises surfaces augmenteront en raison de La résistance au démoulage empêche le démoulage de la pièce moulée, ce qui fait que la surface de la pièce moulée présente des traces de polissage ou de rayure. De telles rayures sont des rainures linéaires dans le sens du démoulage, les moins profondes mesurent moins de 0.1 mm et les profondes mesurent environ 0.3 mm.
1.3 L'étanchéité de la coulée au moule
Le retrait global ou local de la pièce moulée a une force de serrage trop importante sur le moule, ou la répartition de la force de serrage est déséquilibrée et déraisonnable. À ce stade, la pièce moulée sera déformée, fissurée ou cassée en raison du collage du moule, et même la pièce moulée collera au moule fixe. Ou il peut y avoir un phénomène selon lequel le moulage colle au sommet du moule mobile et ne peut pas sortir.
- (1) La force de compactage globale ou partielle de la coulée vers le moule fixe est supérieure à la force de compactage du moule mobile, et la coulée restera collée lorsque le moule est ouvert.
- (2) Pendant le démoulage, si la force de serrage de chaque partie de la coulée sur les moules mobiles et fixes n'est pas uniforme, la coulée sera déviée, inclinée et inclinée lorsqu'elle est retirée, et la partie de la coulée avec un une grande force de serrage sur le moule fixe sera affectée. Il peut coller au moule fixe.
- (3) Si la température du moule fixe est trop basse ou si la température du moule mobile est trop élevée, la force d'emballage du moule fixe sera supérieure à celle du moule mobile lorsque le moulage se rétracte.
- (4) La concentration d'agent de démoulage est trop faible, les performances de démoulage de l'agent de démoulage ne sont pas bonnes, l'agent de démoulage pulvérisé sur le moule fixe n'est pas en place et la quantité d'agent de démoulage est insuffisante, ce qui affectera le performances de libération de la coulée. Si trop de peinture est pulvérisée sur le moule fixe pendant le moule chaud, la température du moule fixe est difficile à augmenter rapidement. Une fois que le moulage a refroidi et rétréci, la force de serrage du côté du moule fixe augmentera plus que le moule mobile.
- (5) Il existe également un phénomène de collage du moule : dans la première période de production de moulage sous pression, c'est-à-dire lorsque le moule chaud est injecté à faible vitesse, la fluidité du liquide d'alliage de moulage sous pression chutera rapidement en raison de la basse température du moule, entraînant le remplissage. Le métal en fusion se formant dans la cavité est très incomplet, la résistance de la pièce moulée formée est très faible et la connexion entre les différentes parties de la pièce moulée est très faible. Lorsque la pièce moulée est démoulée, la pièce avec une force de serrage plus élevée se brisera facilement avec d'autres pièces. Séparé et collé dans le moule. En particulier, il n'y a pas d'éjecteur sur le côté du moule fixe pour éjecter la coulée, il est donc plus facile de coller au moule fixe.
Pour le phénomène de collage qui se produit à chaque fois pendant le moulage sous pression, les raisons de son apparition doivent être analysées en détail. Par exemple, si la coulée colle au moule fixe lors de la coulée sous pression, il faut vérifier la raison de l'effort de serrage excessif de la coulée sur le moule fixe ; vérifier l'aspect du côté moule fixe de la coulée, suivre le sens de démoulage, et il y a des traces de la matrice sur la surface de la coulée. Lorsque le moule de collage est gravement rayé ou rayé, il y aura une grande résistance au démoulage, ce qui empêchera la partie de la coulée ou la totalité de la coulée de sortir dans la cavité, et la coulée restera collée et provoquera un collage; dans les cas graves, non seulement la pièce moulée sera déchirée et endommagée. Le phénomène de déformations, de fissures et de fractures peut également se produire dans le noyau et la cavité du moule. Le phénomène de collage des pièces moulées sous pression est le plus courant dans les alliages d'aluminium. Les mesures spécifiques pour résoudre les défauts de collage des pièces moulées sous pression sont les suivantes.
2 Mesures pour empêcher les pièces moulées de coller au moule fixe
2.1 Mesures pour empêcher les pièces moulées de coller aux moules fixes dans les moules de coulée sous pression
Dans le moule d'essai du moule nouvellement produit, ou lorsque la production de moulage sous pression démarre le moule chaud, le phénomène de collage du moulage sous pression se produit souvent. Lorsque le processus d'opération de moulage sous pression est normal, la principale raison du collage des pièces moulées n'est pas le processus de moulage sous pression, mais devrait être le problème de la conception de la structure de moulage, de la conception du moule ou de la fabrication. Bien que le processus de moulage sous pression et le débogage de pulvérisation puissent être corrigés, l'effet correctif est général et peu stable, et le phénomène de collage de moulage se produira toujours.
Si le moulage a tendance à coller au moule fixe, le moule doit être bien préchauffé avant le moulage sous pression et la cavité du moule doit être recouverte de pâte anti-adhésive et d'air comprimé avant de commencer l'injection à basse vitesse. Soufflez uniformément, appliquez une fois pour chaque moule de moulage sous pression, essayez de mouler environ 20 moules, si le moule est toujours fixe, cela signifie que le moule a un problème et doit être réparé.
Pour les pièces moulées qui ont été conçues, il est vrai que la force de serrage de la pièce moulée sur le moule fixe est supérieure à la force de serrage sur le moule mobile. Il faut laisser la coulée se déposer du côté du moule fixe pour éjecter la coulée, et laisser la surface de la coulée du côté du moule fixe. Laissez les marques de l'éjecteur ou faites en sorte que les marques de l'éjecteur soient faciles à enlever. De cette façon, lors de la conception du moule, le mécanisme d'éjection de la pièce moulée doit être conçu du côté du moule fixe.
Faites attention au calcul de la force de tassement des moules mobiles et fixes. Pour les pièces moulées dont la force de tassement du moule fixe est supérieure à la force de tassement du moule mobile, ou pour les pièces moulées avec la force de tassement du moule fixe et du moule mobile similaire à celle du moule mobile, il est possible de coller le le moule fixe peut coller à la coulée du moule mobile. Lors de la conception de la coulée ou du moule, il est nécessaire de modifier la structure de la coulée ou du moule, l'angle de dépouille, la rugosité de surface, etc., et essayer de rendre la force de coulée du moule mobile supérieure à la force de serrage du fixe mouler.
Pour les pièces moulées avec une force de compactage relativement importante sur un côté du moule fixe, lors de la conception d'un nouveau moule, la surface de séparation doit être choisie autant que possible du côté qui est sollicité par le moule fixe, et les pièces moulées doivent être placées dans la cavité du moule en mouvement autant que possible pour augmenter l'appariement des pièces moulées. La force de serrage du moule mobile. Afin de réduire l'effort de serrage sur le moule fixe, il est nécessaire de re-déterminer la pente de démoulage du moule fixe avec le fondeur, et la pente de démoulage du moule fixe doit être augmentée autant que possible ; prêter une attention particulière à la correction ou à l'augmentation de la coulée du côté du moule fixe. La pente de démoulage de la pièce sollicitée par l'adhérence du moule au moule. En même temps, réduisez de manière appropriée la pente de démoulage du moule mobile ; prêter une attention particulière à la correction ou à la réduction de la pente de démoulage du moule mobile à proximité de l'éjecteur. Essayez de placer le noyau sur le moule mobile ou augmentez la longueur du noyau sur un côté du moule mobile.
Il est nécessaire d'éviter que le moule fixe ne produise des contre-dépouilles ou des surfaces rugueuses qui affectent le démoulage lors de la fabrication et du polissage ; après l'essai du moule ou pendant le processus de moulage sous pression, il est nécessaire de corriger la déformation de la cavité du moule fixe due à l'écrasement et aux meurtrissures ; utiliser des agents de polissage ou de nettoyage chimiques pour éliminer l'alliage Si les marques d'adhérence sur la surface du moule fixe et les adhérents d'alliage sur le moule ne sont pas éliminés à temps, le phénomène de collage deviendra de plus en plus grave après une longue période ; mieux polir la surface rugueuse de la paroi latérale de la cavité du moule fixe. Mais une fois que le moule fixe est poli en une surface de miroir, il n'est pas propice à l'adhérence de la peinture. Lorsque le moule est ouvert, un espace de vide serré se produira entre la coulée et le moule, ce qui augmente la résistance au démoulage, de sorte que le fond de la cavité profonde du moule fixe ne peut pas être poli en une surface de miroir. . Pour les moules qui ont été nitrurés, le polissage doit être effectué avec soin pour éviter d'endommager la couche nitrurée à la surface, et éviter que plus le polissage est important, plus le moule collera.
Modifiez le canal de moulage, changez de manière appropriée la position, la taille et la direction d'écoulement de remplissage du canal pour éliminer ou réduire les défauts d'érosion et de collage du moule causés par l'impact du canal sur le moule fixe. Par example:
- Changez la direction du flux de remplissage de l'aluminium fondu pour minimiser l'impact violent du métal en fusion sur la cavité du moule fixe. Vous pouvez modifier l'impact direct du métal en fusion pour faire face au noyau ou à la paroi de manière oblique ;
- Augmentez de manière appropriée la section transversale de la glissière intérieure. Afin de réduire le débit du métal en fusion dans la rigole intérieure ;
- ③Changez la position de la glissière intérieure, placez la glissière intérieure dans la position large et épaisse de la coulée et évitez l'impact sur la paroi latérale du moule fixe ;
- Essayez de prendre l'alimentation au fond de la cavité profonde de la méthode de coulée ;
- Adopter un canal ouvert, l'évasement du canal fait face à la cavité pour agrandir la zone d'injection ;
- Pour la partie d'impact ou le noyau du canal, une machine de revêtement de tige de carbure de tungstène peut être utilisée pour appliquer de l'électricité à la surface du moule.
La méthode métallurgique par étincelles pulvérise la couche de microparticules de carbure de tungstène, les particules de tungstène métallique et le métal de base ne tomberont pas, ce qui peut améliorer la propriété anti-adhésive de la surface du moule, comme le dépôt d'un revêtement de 2 à 4 microns d'épaisseur sur la surface du moule de coulée sous pression, et sa dureté Il peut atteindre HV4 000~4 500, et la température de fonctionnement peut atteindre 800℃.
Afin de tirer le moulage sur le côté du moule mobile, un crochet barbelé en forme de coin peut être réparé à partir de la tête de la tige d'éjection (la longueur du crochet est de 5 à 8 mm et l'épaisseur de la pièce de moulage est de 1 à 2 mm , voir la figure 1), de sorte que le crochet barbelé moulé sous pression tire la pièce moulée sur le côté du moule mobile, puis retirez le crochet barbelé sur la pièce moulée. Afin d'augmenter la force de serrage de la coulée sur le moule mobile, la rugosité de surface des pièces de moule correspondantes peut être augmentée pour les pièces qui doivent être finies sur la coulée et les surfaces latérales des pièces qui n'affectent pas l'aspect qualité, de manière à augmenter l'effet de la coulée sur la force de serrage du moule mobile. Plus évident.
Afin d'augmenter la force de serrage du moule mobile, des barres de tension peuvent être utilisées de manière appropriée (voir Figure 2) :
- ①Dans le cas de ne pas affecter l'apparence de la coulée, plusieurs rainures peuvent être réalisées sur la surface latérale du moule mobile ou la surface du noyau, ou plusieurs bosses d'une profondeur d'environ 0.1 à 0.2 mm peuvent être meulées dans le moule . . Mais faites attention à ce que la rainure du crochet soit ouverte près de la tige d'éjection pour éviter une force d'éjection inégale ;
- ②Lors de l'ouverture du moule, si vous souhaitez utiliser le canal pour tirer le moulage sur le côté du moule mobile à travers le canal intérieur, vous pouvez réparer les nervures de tension sur le côté du canal du côté du moule mobile, ou moudre quelques profondeurs de 0.2. Point concave de ~0.3 mm pour augmenter la force de serrage de la glissière sur le moule mobile ;
- Vous pouvez également placer la goupille d'éjection sur la glissière près de la glissière intérieure, raccourcir la goupille d'éjection à 5-8 mm plus bas que la surface du moule et couper le côté où la goupille d'éjection est à 3 mm sous l'orifice du moule à une largeur de 2 à 3 mm, une rainure annulaire d'une profondeur de 0.3~0.5 mm. La nervure de tension annulaire formée après le moulage sous pression entraîne le canal, et le canal tire le moulage vers le côté du moule mobile à travers le canal interne. De meilleurs résultats ;
- Si c'est parce que la douille de coulée exerce une grande force de traction sur le gâteau et la carotte, la coulée est amenée au moule fixe, et les nervures de traction peuvent être réparées sur le côté du canal du moule mobile et la carotte de la fente cône. Lorsque le moule est ouvert Tirez le coureur et le gâteau sur le côté du moule mobile avec la barre de tension;
- ⑤ Pour les pièces moulées à parois relativement épaisses ou les pièces moulées avec des trous intérieurs qui doivent être finis, après réduction de la pente de démoulage du noyau de moule mobile, si le problème du moule fixe ne peut pas être résolu, il peut être au milieu du noyau longueur Une rainure annulaire d'une largeur de 2 à 3 mm et d'une profondeur de 0.2 à 0.5 mm est réparée pour former une nervure de tension, et la nervure de tension annulaire tire la pièce coulée sur le côté du moule mobile. Notez qu'il doit y avoir au moins 2 broches d'éjection pour éjecter la pièce moulée à proximité d'un tel noyau pour empêcher la pièce moulée de se déformer.
Pour les pièces moulées dont la force de compactage du côté du moule fixe est supérieure à la force de compactage du côté du moule mobile, afin de rendre la coulée en douceur hors du moule fixe, la plaque d'éjection, la tige d'éjection et la tige de réinitialisation sont conçues pour éjecter le coulée comme le moule mobile. Il est possible d'ajouter un cylindre à huile ou un ressort sur un côté du moule fixe pour pousser la plaque supérieure et la tige d'éjection sur le moule fixe pour éjecter la coulée lors de l'ouverture du moule. Il y a un ressort derrière la plaque d'éjection. Lorsque le moule est ouvert, l'éjecteur de moule fixe est éjecté du plan de joint. Lorsque le moule est fermé, la surface de séparation du moule mobile est utilisée pour pousser les quatre tiges de réinitialisation pour pousser la plaque de poussée du moule fixe et l'éjecteur pour se réinitialiser.
Afin d'utiliser la tige d'éjection pour éjecter la pièce moulée du moule fixe, la tige à crochet, le bloc d'impact et le mécanisme à rouleaux similaires au moule de séparation en deux parties à trois plaques peuvent également être utilisés (voir la figure 5, la pièce moulée, la tige d'éjection et la tige de réinitialisation ne sont pas représentées sur la figure), en s'appuyant sur l'action d'ouverture du moule pour entraîner la plaque de poussée de l'éjecteur de moule fixe pour éjecter les pièces moulées du moule fixe. La structure est la suivante : Concevez la structure d'éjection de la tige d'éjection pour éjecter la pièce moulée pour le moule donné, laissez la plaque d'éjection 5 du moule fixe sortir du modèle de moule fixe 6 et placez quatre (ou deux) crochets sur le moule mobile 1. Les quatre (ou deux) tiges de crochet 4 s'étendent du côté du moule fixe 6 lorsque le moule est fermé. La tige de crochet 4, le bloc d'impact 7, le ressort 3 et le mécanisme à rouleaux 8 sont utilisés pour fabriquer les quatre tiges de crochet 4 et le moule fixe. La plaque de poussée supérieure du moule est reliée par un crochet. Lorsque le moule est ouvert, la tige de traction de moule mobile 4 accroche le poussoir d'éjecteur de moule fixe 5, et le poussoir de moule fixe pousse l'éjecteur 5 pour déplacer la tige d'éjecteur afin d'éjecter la coulée du moule fixe. A ce moment, la coulée et le moule mobile se déplacent de manière synchrone. Après avoir atteint une certaine course, utilisez le bloc d'impact, le rouleau et le mécanisme à ressort pour désengager les crochets des quatre tiges de crochet de la plaque de poussée de l'éjecteur de moule fixe, la plaque de poussée de l'éjecteur de moule fixe s'arrête de bouger et la surface de séparation du moule mobile est également utilisé lorsque le moule est fermé. Poussez les quatre tiges de réinitialisation vers la plaque de poussée de l'éjecteur de moule fixe pour que l'éjecteur de moule fixe revienne à sa position.
2.2 Mesures pour empêcher les pièces moulées de coller au moule fixe en termes de processus de coulée sous pression
Le revêtement par pulvérisation sur le moule, la vitesse d'impact de l'écoulement du liquide d'alliage et la température du moule sont les principaux facteurs qui affectent le collage de la pièce moulée.
La variété, la qualité, la concentration, la position de pulvérisation, le temps de pulvérisation et la quantité d'agent de démoulage affectent l'adhérence de la pièce coulée Ⅲ. Utilisez la quantité d'agent de démoulage pulvérisé pour ajuster l'effet de démoulage de la coulée des deux côtés des moules mobiles et fixes. Afin d'empêcher le moulage de coller au moule fixe, le temps et la quantité d'agent de démoulage pulvérisé sur le moule mobile peuvent être réduits de manière appropriée. La peinture pulvérisée sur le moule mobile doit être fine et uniforme, mais la peinture ne doit pas être manquée. Augmentez la quantité d'agent de démoulage pulvérisé sur le moule fixe pour réduire la température de la surface du moule, en particulier pour la surface des pièces moulées tendues du moule fixe et la surface avec des marques de dessin, augmentez la quantité de pulvérisation. Lorsqu'il n'y a pas de position fixe sur le côté de la matrice fixe, ou qu'il n'y a aucune trace de la matrice, faites attention à augmenter de manière appropriée la quantité de revêtement pulvérisé.
Sur la surface du moule avec des marques de dessin, appliquez la pâte de moule antiadhésive avant que la peinture ne soit pulvérisée après le moulage sous pression, de sorte que la pâte de moule antiadhésive soit frittée sur la surface du moule à haute température, de sorte qu'un une formation se forme entre le liquide d'alliage et la surface du moule. Une couche de diaphragme plus épaisse peut jouer un meilleur rôle dans le démoulage.
Ajustez et contrôlez correctement la température du moule. Il est nécessaire d'analyser la contrainte de l'étanchéité de la coulée et du moule d'adhérence, la différence de température du moule et le retrait de la coulée, et la relation entre la température du moule et le retrait de l'alliage et l'étanchéité du moule. S'il y a une déformation collante sur la surface du moulage, essayez d'utiliser une température de moule plus basse tout en garantissant la qualité de surface du moulage. Si la pièce moulée elle-même a une force de serrage importante, essayez d'utiliser une température de moule plus élevée, ce qui peut réduire le retrait de la pièce moulée pendant le démoulage, c'est-à-dire que lorsque la pièce moulée n'a pas atteint une force de serrage élevée, elle commencera à se démouler.
L'abaissement relatif de la température du moule mobile et la promotion du retrait de la coulée peuvent augmenter l'étanchéité de la coulée au moule mobile ; l'augmentation relative de la température du moule fixe et la réduction du retrait de la coulée peuvent réduire l'étanchéité de la coulée au moule fixe. L'augmentation du débit de l'eau de refroidissement du moule mobile peut réduire la température du moule mobile ; la réduction ou la fermeture du débit de l'eau de refroidissement du moule fixe peut augmenter la température du moule du moule fixe. Généralement, pour le moulage sous pression de pièces moulées en alliage d'aluminium, mesurez la température de surface de la cavité du moule mobile dans les 1 à 3 secondes suivant l'ouverture du moule. La température de surface ne doit pas être supérieure à 300℃, de préférence (240±40)℃ ; et avant de fermer le moule après la pulvérisation Mesurez la température de surface de la cavité du moule fixe dans les 1 à 3 secondes, et elle ne doit pas être inférieure à 140 .
La température de coulée, comme la température du moule, peut modifier le retrait de la coulée et l'étanchéité de l'emballage. L'augmentation de la température de coulée et le raccourcissement du temps d'ouverture du moule peuvent réduire la force de tassement, mais augmenteront l'affinité entre le liquide d'alliage et l'acier du moule, et entraîneront la possibilité de coller dans la partie à paroi épaisse de la pièce moulée.
3 Mesures pour empêcher les pièces moulées de coller au moule en mouvement
3.1 Mesures pour empêcher les pièces moulées de coller au moule mobile en termes de moules de coulée sous pression
La principale raison pour laquelle les pièces moulées adhèrent au moule mobile est que les pièces moulées ont trop de force de serrage sur le moule mobile et que la force d'éjection de la tige d'éjection est insuffisante. Si la force d'éjection n'est pas assez importante, il est nécessaire d'augmenter la pression hydraulique ou la vitesse d'éjection du cylindre d'éjection de la machine de moulage sous pression. Si le diamètre de la goupille d'éjection est trop petit ou si le nombre de goupilles d'éjection est petit, la force de la goupille d'éjection n'est pas assez forte et la goupille d'éjection peut se plier ou se casser.
Si la force de la pièce moulée adhérant au moule mobile est faible, la contrainte est plus légère lorsque la pièce moulée est démoulée, ou la résistance causée par la surface rugueuse du moule est faible, mais la pièce moulée est déformée lorsqu'elle est éjectée, et le la partie collante du moule doit être polie, nitrurée ou augmentée. La quantité d'agent de démoulage pulvérisé réduit la résistance au démoulage. . Si la force de coulée adhère au moule mobile est importante, si la coulée est fortement sollicitée lorsque la coulée est démoulée, le dessus de la coulée est cassé ou déconnecté, ou la coulée est éjectée par l'éjecteur, l'angle de coulée doit être augmenté de manière appropriée. Améliorez la conception des pièces moulées ou des moules et éliminez les structures déraisonnables qui font que les pièces moulées collent aux moules et affectent le retrait.
Afin d'éviter la déformation du moule collante causée par la force d'éjection inégale du moulage, les quatre tiges de poussée de la machine de moulage sous pression poussant la plaque d'éjection du moule doivent avoir la même longueur et la différence ne doit pas être supérieure à 0.20 mm ; la tige de poussée de la machine et l'éjecteur La position de la tige d'éjection du moulage doit être équilibrée et raisonnable, et ne doit pas s'écarter du centre de la cavité du moule, et ne doit pas s'écarter du centre du cylindre éjecteur du moulage sous pression machine.
Si les réglages de tirage du noyau et d'éjection ne sont pas équilibrés, le moulage sera inégalement sollicité et sera dévié. Si la longueur de la tige de poussée du cylindre d'éjection hydraulique de la machine de moulage sous pression n'est pas la même, si la force d'éjection de la pièce moulée est inégale ou si la position de la tige de poussée est mal agencée, la pièce moulée sera déviée lors de l'éjection. . Les mesures d'amélioration sont les suivantes : modifier la structure du moule, ajuster le mécanisme de tirage du noyau et la position de la tige d'éjection, de sorte que la force de coulée soit uniformément éjectée, et s'assurer que la coulée est poussée parallèlement et uniformément ; ajustez le mécanisme d'éjection, la position et la quantité de la tige de poussée de la machine de coulée sous pression (les tiges de poussée les plus faciles à utiliser 4 à 6) pour que les tiges d'éjection et les pièces moulées du moule soient uniformément sollicitées; augmentez raisonnablement le nombre de tiges d'éjection, augmentez le diamètre des tiges d'éjecteur et arrangez les positions des tiges d'éjecteur pour assurer l'équilibre d'éjection.
Si la résistance à la déformation des pièces plates et des pièces moulées à parois minces est insuffisante, le nombre et le diamètre des tiges d'éjection doivent être augmentés. Vous pouvez également ajouter un petit bossage à la position de l'éjecteur pour laisser la goupille de l'éjecteur reposer sur le petit bossage de la pièce moulée. La grande zone de force d'éjection rend la force de la coulée uniforme.
Utilisez de l'acier à mouler de haute qualité, de sorte que lorsque la température du moule est élevée, l'alliage moulé sous pression n'adhère pas facilement à la surface. Avec l'acier à mouler de haute qualité, les microfissures ne se formeront pas prématurément sur la surface du moule, ce qui élimine également la base du collage de l'alliage.
Lorsque la dureté du moule est insuffisante ou fragile, le liquide d'alliage a tendance à coller au moule. Il est nécessaire de vérifier si la dureté du moule est raisonnable, ainsi que de vérifier le processus de traitement thermique pour éviter la fragilité de l'acier du moule. La dureté des modules, des inserts de moule et de tous les noyaux pouvant résister à l'impact de la glissière intérieure est HRc3~5 supérieure à la dureté du module d'empreinte du moule. Lorsque la conception du moule confirme qu'il n'y a pas de problème et que la contrainte de collage du moule de coulée est toujours difficile à éliminer, des mesures de traitement de surface telles que la nitruration, le KANI 7C, le revêtement de tungstène, le placage PVD nano titane, etc. doivent être utilisées pour améliorer la surface dureté du moule.
Pour la surface de la cavité du moule, elle est généralement polie avec de la pierre à huile et du papier de verre. Si vous utilisez un outil pneumatique pour polir la partie collante, vous devez faire attention à ne pas endommager le moule, afin de ne pas endommager la couche de nitrure à la surface du moule, sinon plus le moule est poli, plus le moule sera collant. Cas. Lorsque vous nettoyez la partie sans cavité du moule collant ou du drap collant, vous pouvez utiliser une spatule pour éliminer les bosses, puis polir légèrement avec du papier de verre. Ne pas creuser les noyaux, sinon cela provoquerait un collage plus important. Veillez à ne jamais utiliser de ciseau pour nettoyer le moule collant dans la cavité du moule, afin de ne pas creuser la cavité du moule.
3.2 Contre-mesures pour empêcher les pièces moulées de coller au moule en mouvement en termes de processus de moulage sous pression
Réduisez la vitesse d'injection à grande vitesse de la machine de coulée sous pression ou augmentez la surface du canal dans le moule pour réduire de manière appropriée la vitesse de remplissage du canal. Si la surface de la glissière intérieure est augmentée sans augmenter la vitesse de remplissage de la glissière intérieure, le temps de remplissage peut être raccourci, la chaleur totale générée par l'impact de la glissière intérieure peut être réduite et l'effet de réduction de l'impact du patin intérieur peut être atteint.
Réduisez la pression de moulage de manière appropriée : pour les pièces à paroi mince et les moulages sans pores, vous pouvez choisir une pression plus faible, telle que 40-55 MPa ; les moulages généraux choisissent 55-75 MPa; pour les pièces à paroi épaisse et les pièces moulées avec des exigences de pores, utilisez une pression plus élevée, telle que 75~100MPa; lorsqu'une pression élevée doit être utilisée, 100~140 MPa peuvent être sélectionnés. Plus la pression de coulée est élevée, meilleures sont les propriétés mécaniques de la coulée et plus l'étanchéité de la coulée au moule est grande. En cas de collage du moule, il est nécessaire de confirmer l'utilisation d'une pression de coulée appropriée. Réduisez de manière appropriée le temps d'ouverture du moule (temps de refroidissement du moule) afin que la pièce moulée puisse être démoulée à une température plus élevée et que la force de serrage du moule n'ait pas atteint la valeur maximale, ce qui peut réduire la force de serrage de la pièce moulée sur le moule et réduire le collage du moule. degré.
Si l'angle de démoulage de la pièce moulée est trop petit, il est fort probable que la pièce moulée adhère au moule. Par conséquent, il est nécessaire de sélectionner un angle de démoulage approprié en fonction du matériau d'alliage et de la structure dimensionnelle de la pièce moulée. Lorsque le moule se colle, une augmentation appropriée de l'angle de dépouille peut éliminer le phénomène de collage causé par le choc thermique et le retrait. Si la structure de moulage est déraisonnable, le retrait de chaque partie du moulage sera inégal pendant le processus de retrait et de refroidissement, et la résistance au retrait sera déséquilibrée. Si possible et nécessaire, améliorez la conception de la structure de la pièce moulée pour uniformiser l'épaisseur de la paroi, par exemple en changeant. Pour l'épaisseur de la section, essayez de concevoir les parties épaisses comme des structures creuses ou des nervures reliant les structures ; éviter les pièces de transition avec de grandes différences d'épaisseur; éliminer les bossages, ergots et nervures de renfort déraisonnables. L'augmentation du congé de coulée ou de l'angle de démoulage au coin concave de la coulée peut également empêcher le moule de coller.
À proximité du canal interne du moule et de la partie où le liquide d'alliage remplit la cavité d'impact, la partie du moule avec une épaisseur de paroi épaisse dans la coulée et le coin en retrait de la coulée, il est facile d'être affecté par l'alliage liquide pendant une longue période. Des bâtons de coulée et des déformations se produisent, de sorte que des tuyaux d'eau de refroidissement doivent être fournis pour ces parties du moule pour le refroidissement par eau. Pour le refroidissement du noyau mince, la pression de l'eau de refroidissement doit être augmentée. Ceux-ci peuvent ainsi réduire la température du moule et empêcher le moule de coller.
Si l'alliage de moulage sous pression adhère à la surface du moule à la surface du moulage, de petites bulles apparaissent à la surface. Pour ce phénomène, la surface du moule est polie avec de la toile émeri et de la pierre à huile et le moule est à nouveau collé à plusieurs reprises, ce qui ne peut pas résoudre complètement le problème. Une meilleure façon de résoudre ce type de collage est d'effectuer un grenaillage sur la surface du moule de collage, ou de faire la surface de la partie collante du moule avec une largeur de 0.2 ~ 0.5 mm et une profondeur de 0.2 ~ 0. Le motif net de 5 mm et l'intervalle de 2 à 5 mm permettent d'éliminer les défauts de collage à la surface de la coulée.
Le rétrécissement du canal provoque une déformation de la coulée et un collage du moule. La longueur du coureur de branche doit être allongée pour réduire la surface du coureur de branche; la largeur du patin doit être réduite, la longueur du patin doit être allongée et le patin doit être réduit. Le nombre de canaux ; augmenter le refroidissement des canaux du moule par l'eau de refroidissement, de manière à éliminer l'influence du retrait des canaux sur les pièces moulées.
Moins l'alliage d'aluminium moulé sous pression contient de fer (par exemple <0.6%), plus l'affinité entre l'alliage d'aluminium liquide et l'acier du moule est grande et plus il est susceptible de coller au moule. L'augmentation appropriée de la teneur en fer du liquide d'alliage d'aluminium peut mieux réduire l'adhérence de l'alliage d'aluminium au moule ; il est généralement nécessaire que la teneur en fer dans le liquide d'alliage d'aluminium de moulage sous pression soit contrôlée entre 0.6% et 0.95%. Il est nécessaire d'empêcher l'adhérence des moisissures causée par le mélange avec des métaux à bas point de fusion. Lors de l'utilisation d'un alliage principal pour ajuster la composition chimique, en plus des métaux individuels tels que le magnésium et le zinc, les métaux purs ne peuvent pas être ajoutés au liquide d'aluminium pour empêcher une ségrégation sévère de provoquer le collage du moule.
Plus le retrait de l'alliage de moulage sous pression est important, non seulement plus il est facile de coller au moule, mais aussi plus la résistance à haute température est mauvaise. Certains alliages ont un taux de retrait plus important ; plus la plage de températures des phases liquide et solide de l'alliage est large, plus le retrait de l'alliage est important. Selon la forme structurelle et la complexité de la pièce moulée, si le collage et la déformation du moule causés par le retrait sont difficiles à éliminer, envisagez de passer à un alliage avec un faible retrait du corps et un retrait linéaire et une résistance élevée à haute température ; ou ajuster la composition de l'alliage (comme l'aluminium). Lorsque la teneur en silicium dans l'alliage de silicium augmente, le taux de retrait de la pièce moulée devient plus petit) pour réduire le taux de retrait ; ou pour modifier l'alliage, ajoutez 0.15% à 0.2% de titane métallique et d'autres raffineurs de grains au liquide d'alliage d'aluminium pour réduire l'alliage La tendance à se rétracter.
Conclusion 4
Il existe de nombreuses raisons pour le collage des pièces moulées sous pression, et les mesures pour résoudre le collage sont également différentes. L'article propose spécifiquement des mesures pour résoudre les défauts de collage des pièces moulées sous pression. Nous devons observer et analyser attentivement les raisons du collage et prendre des mesures ciblées. Les contre-mesures correspondantes peuvent résoudre efficacement le problème de l'adhérence des moisissures.
Veuillez conserver la source et l'adresse de cet article pour réimpression: Les mesures concrètes pour résoudre les défauts de moule collant du moulage sous pression
Minghe Casting Company se consacre à la fabrication et à la fourniture de pièces de moulage de qualité et de haute performance (la gamme de pièces de moulage sous pression en métal comprend principalement Moulage sous pression à paroi mince,Chambre chaude coulée sous pression,Chambre froide coulée sous pression), Service rond (Service de moulage sous pression,Usinage CNC,Fabrication de moules,Traitement de surface). Tout moulage sous pression en aluminium personnalisé, moulage sous pression en magnésium ou en zamak/zinc et autres exigences en matière de moulages sont invités à nous contacter.
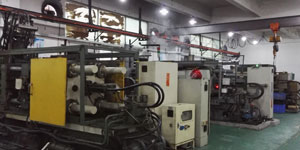
Sous le contrôle des normes ISO9001 et TS 16949, tous les processus sont effectués via des centaines de machines de moulage sous pression avancées, de machines à 5 axes et d'autres installations, allant des blasters aux machines à laver Ultra Sonic.Minghe dispose non seulement d'équipements de pointe, mais également de professionnels équipe d'ingénieurs, d'opérateurs et d'inspecteurs expérimentés pour réaliser la conception du client.
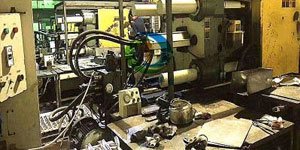
Fabricant sous contrat de moulages sous pression. Les capacités incluent des pièces de moulage sous pression en aluminium à chambre froide à partir de 0.15 lb. jusqu'à 6 lb, configuration à changement rapide et usinage. Les services à valeur ajoutée comprennent le polissage, la vibration, l'ébavurage, le grenaillage, la peinture, le placage, le revêtement, l'assemblage et l'outillage. Les matériaux travaillés comprennent des alliages tels que 360, 380, 383 et 413.
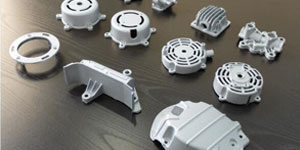
Assistance à la conception de moulage sous pression de zinc/services d'ingénierie simultanés. Fabricant sur mesure de pièces moulées en zinc de précision. Des moulages miniatures, des moulages sous pression à haute pression, des moulages en moules à glissières multiples, des moulages en moules conventionnels, des moulages sous pression unitaires et indépendants et des moulages à cavité scellée peuvent être fabriqués. Les pièces moulées peuvent être fabriquées dans des longueurs et des largeurs allant jusqu'à 24 po avec une tolérance de +/- 0.0005 po.
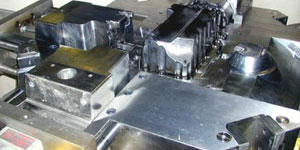
Fabricant certifié ISO 9001 : 2015 de magnésium moulé sous pression, les capacités incluent le moulage sous pression de magnésium sous pression jusqu'à une chambre chaude de 200 tonnes et une chambre froide de 3000 tonnes, la conception d'outillage, le polissage, le moulage, l'usinage, la peinture en poudre et liquide, une assurance qualité complète avec des capacités CMM , assemblage, emballage et livraison.
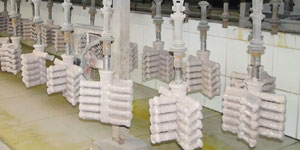
Certifié ITAF16949. Service de casting supplémentaire inclus coulée d'investissement,moulage en sable,Coulée par gravité, Coulée de mousse perdue,Coulée centrifuge,Coulée sous vide,Moulage de moule permanentLes capacités comprennent l'EDI, l'assistance technique, la modélisation solide et le traitement secondaire.
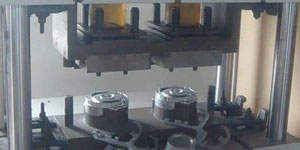
Industries de moulage Études de cas de pièces pour : voitures, vélos, avions, instruments de musique, motomarines, appareils optiques, capteurs, modèles, appareils électroniques, boîtiers, horloges, machines, moteurs, meubles, bijoux, gabarits, télécommunications, éclairage, appareils médicaux, appareils photographiques, Robots, Sculptures, Équipement de sonorisation, Équipement de sport, Outillage, Jouets et plus encore.
Que pouvons-nous vous aider à faire ensuite ?
∇ Aller à la page d'accueil pour Moulage sous pression Chine
→Pièces de fonderie-Découvrez ce que nous avons fait.
→Conseils à propos de Services de moulage sous pression
By Fabricant de moulage sous pression Minghe |Catégories : Articles utiles |Matières Mots clés: Moulage d'aluminium, Moulage de zinc, Coulée de magnésium, Moulage de titane, Fonderie en acier inoxydable, Coulée de laiton,Coulée de bronze,Vidéo de casting,Historique de l'entreprise,Moulage sous pression en aluminium |Commentaires fermés