La relation entre le problème de moisissure collante et l'agent de démoulage
Le collage est l'impact répété à haute pression et à grande vitesse du liquide métallique de remplissage, qui provoque une réaction chimique entre la surface de l'acier du moule et l'alliage de coulée, et une couche de réaction chimique est formée sur la surface du moule, qui conduit au phénomène de collage de la coulée. Généralement, l'adhérence de moule la plus grave est le noyau.
Lorsque les pièces moulées sous pression collent au moule, la surface la plus claire est rugueuse, ce qui affecte la rugosité de l'apparence; la surface la plus épaisse pèle, manque de viande, de souches, de larmes et provoque même une fuite de la coulée. La formation et l'expansion du moule collant non seulement réduit la qualité de surface et la précision dimensionnelle de la coulée, détruit la couche dense de la surface du moule, en particulier la position de la glissière du moule, mais augmente également les heures de travail et les coûts de réparation du moule , et conduit même à des déchets de moulage et à une défaillance précoce du moule.
L'état de la surface de contact entre le métal en fusion et le moule sous haute température et haute pression est très compliqué. Bien que la recherche des gens sur le problème de collage dans le moulage sous pression passe progressivement de la macro surface à la micro surface, de l'analyse qualitative à l'établissement d'une analyse de modèle mathématique, de la recherche à un facteur à plusieurs facteurs La recherche complète se développe de la recherche statique à la recherche dynamique, mais la plupart d'entre eux restent encore sur l'analyse qualitative intuitive. Selon les conditions spécifiques de la moisissure collante, certains facteurs qui affectent sa formation et son expansion sont résumés et des mesures préventives sont prises en conséquence. À l'heure actuelle, le consensus est que : les paramètres du processus de moulage sous pression, la conception du moule, la température du moule, la qualité de la surface du moule, la température de remplissage, la composition chimique et la qualité de l'agent de démoulage, le processus de pulvérisation, etc., ont tous un impact important sur le collage du moule, plutôt que de coller. Le moule est simplement lié intuitivement à l'agent de démoulage. Cependant, la qualité et le mode d'utilisation de l'agent de démoulage sont en effet indissociables du moule collant de coulée sous pression. Pour les ouvriers du moulage sous pression, comprendre et connaître la relation entre eux, se connaître soi-même et l'ennemi, peut contrôler le processus de moulage sous pression avec plus de précision.
L'agent de démoulage lui-même est un produit chimique, et c'est un domaine de connaissance différent des matériaux métalliques et des procédés de moulage. Cependant, le croisement interdisciplinaire a toujours été l'orientation inévitable de l'innovation et du développement. L'auteur essaie de se concentrer sur "quelle force produit la moisissure collante? Quels facteurs sont principalement affectés par la moisissure collante Comment éviter?" et d'autres questions sont analysées et résumées. Sur cette base, prenons l'exemple du moulage sous pression en alliage d'aluminium, puis parlez de la relation entre l'agent de démoulage et le moule de moulage sous pression.
Les propriétés physicochimiques de la moisissure collante
La théorie de la moisissure collante est une théorie complète basée sur la science des métaux, la chimie et la mécanique. Fondamentalement, le moule collant est l'interaction physique et chimique entre les molécules ou atomes du matériau d'interface entre la coulée et le moule, dont la plus importante est l'adhérence.
L'aluminium, le zinc, le magnésium, le cuivre et d'autres matériaux métalliques moulés sous pression et les matériaux de moulage ont une structure polycristalline et les molécules de surface ont une énergie potentielle supérieure à celle des molécules internes, c'est-à-dire l'énergie de surface. Ils ont tous l'instinct qui tend vers l'énergie de surface la plus basse, c'est-à-dire l'instinct d'équilibrer la disposition des atomes sur la surface libre. Si les deux surfaces métalliques sont très proches l'une de l'autre, afin de réduire l'énergie de surface, les réseaux entre eux vont se combiner, provoquant une adhérence. Comme nous le savons tous, il existe une force gravitationnelle entre les solides en contact les uns avec les autres. La force gravitationnelle est formée par une liaison métallique, une liaison covalente et une liaison ionique, qui appartient à la force de liaison à courte portée. Il y a aussi la Von Der Wools Force à longue portée (Von Der Wools Force). Lorsque la distance de contact est de quelques nanomètres, toutes les forces de van der Waals fonctionnent. À moins de 1 nanomètre, diverses forces à courte portée entrent en jeu. Pour estimer la force de la liaison d'adhérence, déterminez d'abord la cohésion du métal, puis calculez la force de surface de la surface de contact. Cependant, en raison de la structure électronique complexe des métaux, il n'est pas possible de résoudre théoriquement la force de cohésion à l'heure actuelle.
Du point de vue du phénomène, le collage n'est rien de plus qu'une combinaison chimique ou une occlusion mécanique. Les principaux facteurs liés à la force d'adhérence sont : le type de métal, la solubilité mutuelle du métal, l'orientation du réseau cristallin, le mode de déformation élastoplastique lors du contact, la récupération élastique, la ségrégation et l'oxydation, la dislocation et la microfissuration, la température de contact , etc. Le durcissement de la surface du moule lui-même, la rugosité de la surface, la pression de contact, etc. sont également des facteurs importants. La capacité de liaison des différents atomes est différente et les alliages de différentes compositions présentent des tendances d'adhérence différentes. Par conséquent, le choix du matériau de moule et de la formule d'agent de démoulage appropriés peut minimiser l'adhérence entre la coulée et le moule.
Les causes du collage de l'aluminium dans les moules de coulée sous pression
L'aluminium adhésif lui-même est une réaction de diffusion chimique entre les métaux.
1) Composition chimique
Plus l'affinité entre l'alliage de coulée sous pression et l'acier est grande, plus il est facile de fondre et de se lier les uns aux autres. Lorsque la teneur en fer dans l'alliage d'aluminium est inférieure à 0.7%, les atomes de fer à la surface du moule peuvent pénétrer plus rapidement dans l'aluminium liquide en raison du gradient de concentration, et il est facile de former du fer-aluminium ou du fer-aluminium. composés intermétalliques de silicium et collent au moule. De toute évidence, la tendance au collage de l'aluminium pur est la plus grave, tandis que la tendance au collage de l'alliage eutectique aluminium-silicium couramment utilisé dans le moulage sous pression est plus faible. Le nickel a pour effet de favoriser la croissance des composés intermétalliques, et les inclusions dans l'aluminium liquide et le chrome et le nickel peuvent augmenter les chances d'adhérence de l'aluminium. Une teneur élevée en silicium et une augmentation du manganèse peuvent ralentir la vitesse de croissance de la phase métallique intermédiaire et réduire l'adhérence du moule. Une petite quantité de strontium (0.004%) et de titane (0.125%) peut également réduire l'adhérence de l'aluminium.
En bref, contrôlez strictement la composition de l'alliage dans une plage raisonnable et respectez la propreté du liquide d'alliage d'aluminium, ce qui est la base pour éviter le collage du moule.
2) Matériau du moule
Les matériaux de moulage représentaient environ 10 % du coût total des moules. Dans les années 1950, l'acier moulé à chaud 3Cr2W8V importé de l'ex-Union soviétique était largement utilisé en Chine. Lors du moulage sous pression de 10,000 20,000 à 1990 13 moules, des fissures capillaires ont commencé à apparaître dans la cavité et le moule n'était pas collant. éviter de. Dans les années 15, l'excellente nuance d'acier H200,000 a été introduite des États-Unis. En tant qu'acier à matrice de travail à chaud durcissant refroidi à l'air avec à la fois une ténacité et une ténacité, sa durée de vie peut atteindre 61 à 61 13 fois la matrice. Une variété de nuances d'acier similaires ont été étendues en utilisant cette nuance d'acier comme matrice, telles que : Japon SKDXNUMX de (JIS) ; STDXNUMX de Corée du Sud (KS) ; BHXNUMX de Grande-Bretagne (BS), etc. Si la qualité du matériau de moule sélectionné est faible, sa trempabilité, sa ténacité, sa résistance à l'usure, la stabilité du traitement thermique sont médiocres, la dureté du moule est insuffisante, la surface du moule est comprimée par le moulage sous pression alliage pendant le démoulage, ou le noyau est plié et déformé, ce qui augmente l'appariement des moules. La partie collante du moule de la coulée présente souvent des marques d'emboutissage telles que surface rugueuse, écaillage ou manque de matière. En cas d'adhérence sévère, le moulage sera déchiré et endommagé. La surface de la cavité du moule adhérera à un alliage de coulée stratifié et la couleur sera blanche, comme indiqué sur l'image.
La raison pour laquelle le collage se produit facilement au point chaud du moule ou directement en face de la grille est que la couche de composé intermétallique est facile à former ici, et la couche de composé intermétallique formée Al4FeSi et le moule H13 ont une forte force de liaison. La fine couche de composé intermétallique formée est provoquée par la fonte à grande vitesse qui récure à plusieurs reprises la surface du moule pendant le remplissage, provoquant le décollement de la couche de composé intermétallique de la surface du moule. Le matériau résistant à l'usure Cr23C6 peut empêcher efficacement l'impact chimique de la fonte de l'alliage d'aluminium et réduire la perte de matériaux de moule et l'apparition de collage de moule.
3) Conception de moule
Lorsque le processus de moulage sous pression est normal, mais qu'un nouveau moule colle au moule, le débogage du processus de moulage sous pression et la pulvérisation peuvent être corrigés, mais s'il est instable, cela signifie que la raison principale est le problème de la structure de moulage conception, conception de moules ou fabrication.
Le premier est la conception de la porte interne, telle qu'un contrôle incorrect de la direction d'écoulement, de la section transversale, de la vitesse d'injection, etc., le métal en fusion érode directement le noyau ou la paroi, ce qui est le plus susceptible de coller au moule. S'il heurte le côté du moule fixe, la force d'emballage du moulage sur le côté du moule fixe augmentera. Lorsque le retrait global ou partiel de la pièce moulée présente une répartition déséquilibrée et raisonnable de la force de serrage du moule, la pièce moulée apparaîtra déviée, asymétrique, inclinée, déformée, fissurée, cassée en raison du collage du moule, et même collera à le moule fixe, ou coller au sommet du moule mobile. . Si la pente de démoulage de la cavité de moule fixe ou de la surface de formation du noyau est trop petite ou présente une pente inversée, la résistance au moulage augmentera, provoquant des rayures lors de l'extraction du noyau et du retrait des pièces. De plus, la conception du moule n'est pas assez rigide pour perdre prématurément la précision qu'elle devrait être ; la finition de surface du moule et le traitement de renforcement de surface font défaut ; la conception du système de refroidissement sur les moules mobiles et fixes est déraisonnable, ce qui rend la température de fonctionnement du moule déséquilibrée et stable ; il y a des nœuds chauds, etc. Conduire à la moisissure collante.
4) Traitement des moules
La chaleur de friction générée pendant le processus de meulage du moule provoquera des fissures de meulage sur la surface. La présence de contraintes de meulage réduira également la résistance à la fatigue thermique du moule. La surface de la cavité du moule, en particulier la surface rugueuse de la glissière ou l'endroit avec une petite quantité de rayures et de rayures sur la surface du moule, sont des sources potentielles de fissures. La température locale élevée de l'usinage de finition EDM forme la zone trempée sous la surface. La structure et la composition chimique de cette zone sont différentes de celles de la matrice. La dureté de cette zone est élevée. En plus de l'existence de contraintes résiduelles sur la surface, le traitement de polissage peut ne pas être en place, et il peut se former des microfissures au début de l'utilisation du moule. Conduire à la moisissure collante.
5) Processus de moulage sous pression
Si la température de remplissage du liquide d'alliage est trop élevée, la diffusion et la réaction du fer seront accélérées. Plus le film lubrifiant sera détruit facilement, plus la surface du moule sera recuite facilement et plus elle sera sensible à l'érosion et à l'adhérence de l'aluminium. Si la vitesse et la pression d'injection sont trop élevées, la température du moule est trop élevée et la dureté du moule est faible, la fusion, l'adhérence du soudage et le collage du moule se produiront facilement.
6) Agent de libération
La fonction principale de l'agent de démoulage est de protéger le moule et de former un film lubrifiant solide pour réduire l'impact thermique de l'aluminium fondu à grande vitesse sur le moule.
Les agents de démoulage inférieurs n'ont pas pour fonction de protéger le moule, car sa composition chimique détermine qu'il est impossible de former rapidement un film lubrifiant ferme, lisse, retenant la chaleur, moins gazeux, sans résidu et propice à l'écoulement de liquide d'alliage dans la plage de température de moule requise par le processus. Quelle que soit la manière dont le processus de pulvérisation est ajusté, ses caractéristiques essentielles ne peuvent pas être modifiées, de sorte que le danger caché d'adhérence des moisissures est inévitable.
Les moyens de résoudre le problème de la moisissure collante
Le problème de l'adhérence des moisissures est une réaction globale de nombreux facteurs. Par conséquent, pour résoudre le problème de la moisissure collante, nous devons analyser et juger sous plusieurs angles, en permettant des essais et des erreurs, mais sans porter de jugement subjectif. Les éléments suivants résumés par l'auteur sont des compétences purement empiriques basées sur la théorie de la boîte noire, c'est-à-dire que le moule est considéré comme une boîte noire, et les changements internes du processus de remplissage ne sont pas étudiés, et seules les deux extrémités de la boîte noire box sont les paramètres d'entrée et les effets de moulage. Pour résoudre fondamentalement le mode collant, il a besoin de l'aide de résultats de recherche micro-théoriques approfondis, et il a encore un long chemin à parcourir.
- Vérifiez les facteurs qui affectent la vitesse de la porte : vitesse du poinçon, taille du poinçon, pression spécifique, taille de la porte, réduisez autant que possible la vitesse de la porte ou ajustez la direction de la porte pour contacter la surface de la cavité à un angle plus petit pour éviter l'angle de contact Près de 180 degrés pour réduire l'érosion de la cavité et éviter l'impact sur le noyau. Réduisez le temps de remplissage pour réduire la fenêtre de choc thermique.
- Ajustez le canal de refroidissement du moule, en particulier le nœud chaud et le noyau faciles à coller au moule, ajoutez un refroidisseur si nécessaire. Ajoutez un deuxième spray ou insérez un matériau de moule à haute conductivité thermique dans la partie collante pour réduire la température du moule de la partie collante et obtenir une température de moule stable et équilibrée.
- Dans la plus petite zone d'éjection de la coulée, une pression de remplissage élevée peut favoriser le collage du moule. Dans le but de satisfaire la qualité des pièces moulées, réduisez autant que possible la pression de remplissage. La pression statique et la pressurisation sont toutes deux importantes. Dans le même temps, le réglage de la pression doit être calculé et ajusté selon le diagramme PQ2.
- Une température de moule et une température de coulée élevées augmenteront la tendance au collage du moule. Lorsque plusieurs facteurs affectent le collage du moule, abaisser la température du moule ou la température de coulée est le meilleur moyen de le corriger.
- Des matériaux spéciaux à haute résistance, tels que le Mo-785, le Ti-6AI-4V et l'Anviloy 1150, peuvent être utilisés là où le moulage est susceptible de se produire. Diverses méthodes de traitement de surface du moule peuvent réduire considérablement l'adhérence des moules. Tels que le traitement de nitruration et de carbonitruration, couche dense de dépôt physique en phase vapeur telle que {TiAl} N et CrC et film d'aluminium, etc., traitement de renforcement de la surface du moule, revêtement du moule --- CVD, PVD, TD, etc. Le moule collant existant doit être éliminé au plus vite. Si on le laisse se développer, de plus en plus de difficultés et de répétitions apparaîtront.
- Utilisez des agents de démoulage de haute qualité avec une température de résistance à la chaleur de formation de film élevée, une qualité de moule élevée et un bon effet lubrifiant. Appliquez de la pâte à mouler lorsque vous essayez de nouveaux moules pour éviter les tensions. Pour les zones à haute température où les moules sont faciles à coller, la pâte de cire anti-adhésive peut être appliquée régulièrement ou partiellement pulvérisée avec un liquide de cire anti-adhésive.
- Surveillez attentivement l'angle d'éjection du moule et sa valeur maximale admissible doit être conforme à la norme du moule de moulage sous pression.
- La conception de la composition de l'alliage de moulage sous pression doit prendre en compte les facteurs susceptibles de provoquer le collage du moule. Par exemple, dans la plage admissible, il est conseillé de contrôler la teneur en fer dans l'alliage d'aluminium à pas moins de 0.7%. Il est nécessaire d'empêcher l'adhérence des moisissures causée par le mélange avec des métaux à bas point de fusion. Lors de l'utilisation d'un alliage principal pour ajuster la composition chimique, en plus des métaux individuels tels que le magnésium et le zinc, les métaux purs ne peuvent pas être ajoutés au liquide d'aluminium pour empêcher une ségrégation sévère de provoquer le collage du moule. Le liquide d'alliage purifié a une bonne fluidité et peut se dilater la fenêtre de processus pour éviter le collage de moule.
- Plus le retrait de l'alliage de coulée sous pression est important, plus il est facile de coller au moule et plus la résistance à haute température est mauvaise. Certains alliages ont un taux de retrait plus important. Plus la plage de température liquide et solide de l'alliage est large, plus le retrait de l'alliage est important. Selon la forme structurelle et la complexité de la coulée, si le collage et la déformation provoqués par le retrait sont difficiles à éliminer, il est nécessaire d'envisager de passer à un alliage à faible retrait volumique et retrait linéaire et à haute résistance à haute température ; ou ajuster la composition de l'alliage (tel que l'aluminium silicium Lorsque la teneur en silicium dans l'alliage augmente, le taux de retrait de la pièce moulée devient plus petit) réduire son taux de retrait ; ou modifier l'alliage, par exemple en ajoutant 0.15% à 0.2% de titane et d'autres raffineurs de grains au liquide d'alliage d'aluminium pour réduire la tendance des alliages à rétrécir.
La relation entre l'agent de démoulage et la moisissure collante
Le moulage sous pression est un processus thermodynamique dynamique. Les alliages tels que l'aluminium et le zinc ont une forte tendance à adhérer à la surface de la cavité. L'agent de démoulage pulvérisé peut agir comme un agent de séparation entre la cavité et le métal liquide pour empêcher le métal d'adhérer à la surface de la cavité. Sélection minutieuse de l'agent de démoulage (composition, température conjonctivale, volume d'air, résidu, force conjonctivale, influence sur le revêtement de surface ultérieur, etc.) .) sont des facteurs importants pour empêcher le collage de moisissures.
Depuis plus d'un demi-siècle, avec les progrès de la technologie de moulage sous pression, les agents de démoulage se sont également améliorés en conséquence. Ces améliorations comprennent la composition de l'agent de démoulage, la formation de film, la résistance à la température, le pouvoir lubrifiant, la prévention du collage et du soudage des moules, et le respect des exigences de protection de l'environnement, qui sont inoffensifs et sans danger pour le corps. Des premiers revêtements d'huile + graphite aux revêtements à base d'eau, de la série d'émulsions de savon à base d'huile ordinaire à la série d'agents de démoulage à base d'eau actuellement largement utilisés, des agents de démoulage concentrés anhydres (pour la micro-pulvérisation), et développer vers des revêtements semi-permanents réactifs et des revêtements inorganiques en poudre. Mais jusqu'à présent, il n'y a pas eu d'agent de démoulage qui puisse fournir toutes les propriétés possibles sans limitations ou inconvénients. La peinture semi-permanente a été testée pour le moulage sous pression d'alliages de zinc. Il est chimiquement lié à la surface du moule. Le revêtement est stable à 698 °C, mais il s'use facilement, il est donc nécessaire d'essayer d'étendre sa durabilité. Pour la coulée sous pression d'alliages d'aluminium et de magnésium, il s'agit principalement d'améliorer la stabilité thermique du revêtement. Du point de vue de la protection de l'environnement et de la sécurité, il faut également envisager de réduire ou d'éliminer les solvants nocifs. Ces dernières années, de nombreux travaux de recherche ont été consacrés aux moules semi-permanents et aux moules permanents. En développant de nouveaux revêtements, en surmontant le soudage et le collage et en abandonnant enfin les agents de démoulage, il s'agit d'une innovation de rupture. Cependant, les résultats obtenus jusqu'à présent ne peuvent pas être utilisés dans des applications industrielles. Les principaux problèmes sont la durabilité du revêtement, la méthode de revêtement et le prix.
Dans un avenir prévisible, le développement et la recherche de divers agents de démoulage resteront indispensables. Il existe une pression de contact considérable entre la surface de moulage de la pièce de moulage sous pression et la surface du moule. La pièce moulée est soumise à une contrainte de compression tridirectionnelle non uniformément répartie pendant le moulage sous pression. Par conséquent, le film lubrifiant formé par pulvérisation d'agent de démoulage est facile à rompre, et une température élevée provoque également des changements chimiques dans le film lubrifiant. . Au cours de la deuxième extrusion, une petite quantité de nouvelle surface métallique apparaîtra. La nouvelle surface a des propriétés physiques et chimiques différentes de la surface métallique d'origine. Il n'y a pas de protection lubrifiante, et il est facile d'adhérer au moule et de provoquer l'usure du moule. Dans le même temps, les contraintes supplémentaires et les contraintes résiduelles provoquées par la répartition inégale de la déformation interne de la pièce moulée augmentent également la difficulté de prendre la pièce jusqu'au collage du moule.
Pour le moule, en raison du changement du processus de moulage sous pression et du champ de température du moule, le processus de formage est une sorte de frottement intermittent et instable, et différentes parties du moule sont différentes. Le mécanisme de lubrification dans cet état ne peut pas être analysé et décrit par le théorème de frottement de Coulomb en physique générale. Des experts nationaux et étrangers ont successivement avancé la théorie du frottement mécanique-moléculaire, la théorie du frottement adhérence-ligou, le frottement limite, le frottement mixte, la théorie du frottement visqueux élastique, etc., tout en étudiant des lubrifiants de compositions chimiques complexes diverses.
Les agents de démoulage de graphite utilisés pour réduire l'adhérence de l'aluminium aux moules ne sont plus utilisés en raison de l'impact environnemental. Le mécanisme de l'agent de démoulage consiste à former un film protecteur entre le moulage et le moule, tout en empêchant le liquide d'alliage d'aluminium d'entrer directement en contact avec la surface du moule. Cela nécessite que l'agent de démoulage ait une résistance suffisante pour résister à la séparation et à l'impact du liquide d'alliage d'aluminium. La température de la surface du moule est généralement contrôlée à 35 % à 45 % de la température de coulée de l'alliage, de sorte que l'agent de démoulage peut être entièrement absorbé sur la surface du moule et protéger le moule. Le moule près de la porte et les rainures profondes sont sujettes au collage de l'aluminium. La forme de la surface du moule où se produit le collage de l'alliage d'aluminium est illustrée sur la figure. Le diamètre initial de ces petites fosses irrégulières est d'environ 0.6 micron, et finalement elles se développent progressivement en petites fosses d'un diamètre de 3.6 microns. Au fur et à mesure que la tendance à former un moule collant augmente, le diamètre de ces petits creux peut atteindre 15 µm, et des fissures se forment éventuellement. Ces petites piqûres et fissures sont éventuellement remplies d'aluminium, et une liaison mécanique peut également se produire.
Le rôle de l'agent de démoulage est de séparer la surface du moule et du moulage sous pression, de réduire les dommages du moule, de rendre la surface du moulage lisse et en même temps de jouer un rôle dans le refroidissement, l'ajustement et le contrôle du moule. . L'agent de démoulage et la surface du moule peuvent produire un film d'adsorption physique non polaire ou polaire, un film d'adsorption chimique et un film de réaction chimique. Lorsqu'il n'y a pas de molécules polaires dans l'agent de démoulage, l'agent de démoulage ne peut produire qu'un film d'adsorption physique non polaire sur la surface du moule ; sinon, il peut produire un film d'adsorption physique polaire. La résistance de cette dernière est supérieure à celle de la membrane d'adsorption physique non polaire. Lorsque les atomes dans le composant agent de démoulage et les atomes sur la surface du moule partagent des électrons communs, un film d'adsorption chimique sera produit sur la surface du moule. Sa résistance est supérieure à celle du film d'adsorption physique polaire. Sous une certaine pression et température de contact, l'agent extrême pression dans l'agent de démoulage peut également réagir chimiquement avec la surface du moule pour produire un film de réaction chimique. Sa résistance est supérieure à celle de la membrane d'adsorption chimique. D'une manière générale, plus la résistance du film d'adsorption de l'agent de démoulage est élevée, meilleur est l'effet d'empêchement du collage. Par conséquent, selon les différentes pièces de moulage sous pression, il est très important de choisir l'agent de démoulage correspondant pour former un film d'adsorption à haute résistance.
L'agent de démoulage à base d'eau préparé avec de l'huile minérale générale est un composé organique hydrocarboné non polaire (CnH2n+1). Le film formé a une faible force d'adsorption sur la surface du moule et la cohésion des molécules elles-mêmes, et la résistance du film est très faible. Agent de démoulage à base d'eau préparé à partir d'huiles animales et végétales, telles que des acides gras, des savons de sodium d'acides gras, des acides (ROH), etc., avec un groupe hydrocarboné non polaire à une extrémité et une extrémité polaire à l'autre extrémité. Cette molécule a un dipôle permanent Lorsqu'elle est en contact avec la surface du moule, l'extrémité polaire attire la surface du moule, tandis que l'extrémité non polaire est tournée vers l'extérieur et alignée sur la surface métallique. La couche de molécules adsorbées n'a que quelques nanomètres d'épaisseur. Lorsque des additifs polarisants sont ajoutés, la polymérisation forme un film solide à la surface du moule et renforce en même temps la force d'adsorption latérale des molécules. La résistance et le pouvoir lubrifiant de ce film d'adsorption physique sont beaucoup plus élevés que ceux du film d'adsorption physique à molécules non polaires.
Le film d'adsorption physique est très sensible à la température et les molécules polaires adsorbées à la surface du moule sont dans un état d'équilibre dynamique d'adsorption et de désorption continues. La température augmente, la désorption augmente, l'épaisseur du film d'adsorption diminue et la résistance du film d'adsorption limite diminue, provoquant la désorption des molécules, une direction chaotique et même la fonte du film, et vice versa. Le film d'adsorption physique n'est efficace que dans des conditions de faible pression de contact et de basse température, de sorte que ce type d'agent de démoulage ne peut fonctionner qu'à de basses températures de moule. L'adsorption physique n'a pas de sélectivité, tandis que l'adsorption chimique a une sélectivité évidente, c'est-à-dire qu'un certain adsorbant ne peut adsorber que certaines substances. Par conséquent, différents agents de démoulage doivent être sélectionnés en fonction du moule et du matériau de moulage sous pression, des conditions du processus de moulage sous pression (telles que la température du moule, l'épaisseur de la paroi de moulage, la température de remplissage, la pression, etc.) afin d'obtenir l'effet souhaité.
L'agent de démoulage à base d'eau préparé avec un polymère de haute masse moléculaire d'huile de silicone modifiée comme corps principal, ses molécules polaires sont chimiquement combinées avec la surface du moule, qui appartient à l'adsorption chimique formée par la combinaison de la force de liaison chimique et de la surface. Par conséquent, le film a une bonne résistance à la chaleur, une stabilité thermique élevée, un film d'adsorption irréversible, une forte adhérence et un bon effet de libération. Bien que le prix soit légèrement plus élevé, il présente des avantages évidents dans la prévention du collage du moule pour le moulage sous pression qui nécessite une température de moule élevée, une pression élevée et des pièces complexes de grande taille et à paroi mince.
Le processus de pulvérisation est très important pour éviter que les moisissures ne collent. Lorsque l'opérateur constate que le moule colle, il est naturel de penser que c'est parce que la concentration est faible ou que le dosage est faible et que le film est trop fin pour résister à la contrainte thermique et à l'impact turbulent du métal en fusion, puis pulvériser plus d'agent de démoulage sur le moule collant. Le résultat est souvent une accumulation locale ou des résidus de peinture, provoquant des pores et compliquant le problème. La bonne méthode devrait être d'appliquer une sorte de pâte anti-adhésive --- de la cire anti-adhésive sur la zone où le collage s'est produit, et d'effectuer un traitement spécial. La cire anti-adhésive est une pommade anti-soudure facile à brosser, qui est préparée à partir de matières premières semi-synthétiques à haute température. Le composant efficace ne contient pas de substances nocives. Le composé à base de tungstène résistant aux hautes températures ou la teneur en composé à base de molybdène dans la pâte peut efficacement éviter l'effet d'interface de l'alliage d'aluminium et empêcher le collage du moule.
La température du moule est un facteur important qui affecte l'effet d'adsorption de l'agent de démoulage. Trop basse (inférieure à 150 °C), la température du moule chute rapidement en dessous du point de vaporisation de l'eau, l'agent de démoulage ne peut pas être déposé sur la surface du moule, mais se précipite à travers la surface du moule, et l'eau porteuse est trop tard pour se vaporiser, ce qui peut provoquer des pores diffus; température du moule Trop élevée (supérieure à 398 °C), l'agent de démoulage est repoussé par la couche de vapeur sur la surface du moule et la capacité d'adsorption de l'agent de démoulage est considérablement réduite. Ce n'est que lorsque la température de mouillage requise par les caractéristiques de l'agent de démoulage est atteinte, qu'il peut réellement entrer en contact avec la surface du moule pour former un compact Le revêtement joue un rôle d'isolement.
Le processus de pulvérisation affecte également directement l'effet d'adsorption. Généralement, lorsque la pression du tuyau de pulvérisation est de 0.35 à 0.70 bar supérieure à la pression de l'agent de démoulage (1.05 bar peut être nécessaire pour une pulvérisation sur de grandes surfaces), l'effet d'atomisation est bon ; pour la micro-pulvérisation et la pulvérisation pulsée, l'effet d'atomisation est meilleur. Est important. Quant au temps de pulvérisation, aussi court que 0.10 à 2.0 secondes est suffisant pour former un film d'isolation suffisamment épais. Le temps de pulvérisation pulsée se situe dans cette plage, mais comme l'agent de démoulage est actuellement utilisé en grande quantité pour refroidir la cavité, cela prend généralement entre 5.0 et 120 secondes. De toute évidence, une partie de l'agent de démoulage ne fait que traverser la surface du moule et est gaspillée. Avec l'avènement de dispositifs de pulvérisation automatiques plus complexes et plus précis, l'angle et la distance de pulvérisation n'ont qu'à être ajustés et fixés avant la production.
Je pense que pour les ingénieurs de moulage sous pression qui utilisent des agents de démoulage, l'important n'est pas d'épuiser les connaissances professionnelles des agents de démoulage et de les choisir ensuite en fonction de leurs propres jugements, mais d'apprendre des industries de moulage sous pression européennes et américaines. et laissez les fabricants se spécialiser dans la production d'agents de démoulage. Selon le schéma de structure de moulage sous pression fourni par le fabricant de moulage sous pression, le tonnage de la machine de moulage sous pression, les exigences de performance des pièces moulées et les exigences du processus de post-traitement, le modèle d'agent de démoulage le plus approprié et la méthode de sont recommandées jusqu'à l'obtention de résultats satisfaisants. Parce que les fabricants qui se spécialisent vraiment dans la production d'agents de démoulage doivent connaître au mieux les caractéristiques de performance des agents de démoulage et interagir avec eux pour se débarrasser de la cécité et maintenir un cycle vertueux de production.
Le collage de moule correctement géré
Le cœur de la production de moulage sous pression est la qualité de la fusion des alliages et des moules. Parmi tous les facteurs qui empêchent et traitent les moisissures collantes, le choix de matériaux de moulage de haute qualité est la base, la conception et le traitement des moules et le traitement thermique standardisé sont la clé, et une maintenance rapide et efficace pendant l'utilisation est le principal moyen. Lorsque le moule se colle, la partie qui exécute le processus de moulage sous pression et le fabricant du moule se blâment souvent. C'est compréhensible, car les facteurs qui induisent le collage sont divers, et il est difficile de porter un jugement précis pour le moment. Mais dans tous les cas, la propriété intrinsèque tombe sur le moule, donc pour les moules qui ont été collés, il faut d'abord analyser et traiter le moule lui-même.
- Le polissage de surface du moule de coulée sous pression doit répondre aux exigences. Polir soigneusement pour enlever la couche dure d'EDM, et la surface ne doit pas être très polie.
- Nettoyez l'aluminium collé sur le moule de coulée sous pression à temps et effectuez un traitement de surface et un soulagement des contraintes sur le moule à temps. S'il y a une adhérence d'aluminium sur la surface du moule et qu'il y a de petites bulles sur la surface, utilisez de la toile émeri et de la pierre à huile pour polir la surface, puis collez le moule à plusieurs reprises. La meilleure méthode de traitement consiste à grenailler la surface du moule du moule collant, ou le moule en position collante Sur la surface, un motif de maille d'une largeur de 0.2-0.5 mm, d'une profondeur de 0.2-0.5 mm et d'un intervalle de 2 à 5 mm peuvent être produites, ce qui peut éliminer les défauts d'adhérence du moule sur la surface de la coulée.
- Essayez de minimiser la température où le moule est facile à coller à l'aluminium.
- Utilisez des matériaux spéciaux avec un point de fusion plus élevé pour effectuer un traitement de surface sur le moule, et il peut être collé à la position où le moule est collé sur la surface du moule pour éviter que le moule ne colle. Nouveaux matériaux tels que les alliages de molybdène, les alliages de tungstène, les alliages de titane, les nitrures spéciaux ou les composés de carbone et d'azote à basse température. L'énergie d'activation entre l'aluminium et le molybdène est relativement élevée, de sorte que l'utilisation d'infiltration de molybdène sur la surface du moule peut améliorer efficacement les performances anti-adhésives.
- Pour les nouveaux moules et les moules susceptibles de coller au moule fixe, le moule doit être bien préparé avant le moulage sous pression. Préchauffer, chauffer le moule à l'aide d'un pistolet à flamme. Il n'est pas permis de verser directement le liquide d'alliage dans le moule pour le chauffage, et la température de préchauffage est contrôlée à 180~220ºC. Et avant de commencer l'injection à basse vitesse, appliquez la pâte de moulage sur la cavité du moule et soufflez-la uniformément avec de l'air comprimé. Il est appliqué une fois par moule de coulée sous pression, et le test de coulée sous pression est d'environ 20 moules, ce qui est très efficace pour éviter de forcer le moule. Si le moule est toujours coincé, cela signifie qu'il y a un problème avec le moule et que le moule doit être réparé
- Lors du démontage de la partie mobile du moule ou du petit noyau, seuls le cuivre doux, l'aluminium, les tiges de plomb ou les marteaux en caoutchouc sont autorisés à taper légèrement pour éviter d'endommager la cavité.
- Après la coulée sous pression dans un certain nombre de moules, le moule doit être soumis à un traitement de détente de façon régulière.
Il existe de nombreuses raisons au collage du moulage sous pression, et les mesures pour résoudre le collage sont également différentes. Les raisons du collage doivent être soigneusement observées et analysées, et les mesures correspondantes doivent être prises de manière ciblée. À l'heure actuelle, la recherche sur le mécanisme de formation du phénomène de collage est encore au stade de l'analyse qualitative. Différents matériaux d'alliage présentent des tendances d'adhérence différentes ; il est nécessaire de trouver des méthodes d'essai plus efficaces et sous la direction des résultats de la recherche théorique quantitative. , Pour effectuer d'autres recherches expérimentales.
Avec l'émergence continue de nouveaux matériaux et de nouvelles technologies de processus, de nouvelles idées et de nouvelles méthodes pour résoudre le problème du collage des moules et même des technologies innovantes perturbatrices ont un impact sur les règles traditionnelles existantes qui reposent sur la prévention du collage. Par exemple, le moulage sous pression nord-américain développe un moule permanent auto-développé avec une fonction de cicatrisation et aucun agent de démoulage peut entraîner le renversement ou l'élimination de la technologie de traitement existante à l'avenir. Par conséquent, nous devons continuer à absorber la technologie de moulage sous pression de pointe, tout en maintenant la patience dans la recherche scientifique, de manière constante et constante, un nouveau saut dans le moulage sous pression en Chine est imminent.
Minghé Société de moulage sous pression Est un fabricant personnalisé de pièces moulées sous pression de précision et non ferreuses. Les produits incluent l'aluminium et moulages sous pression de zinc. Moulages sous pression en aluminium sont disponibles en alliages, y compris 380 et 383. Les spécifications incluent des tolérances de plus /- 0.0025 et un poids de moulage maximum de 10 lb. Zinc pièces moulées sous pression sont disponibles dans des alliages standard tels que le Zamak no. 3, Zamak non. 5 & Zamak non. 7 & alliages hybrides tels que ZA-8 & ZA-27. Les spécifications incluent plus /- 0.001 tolérances et un poids de moulage maximum de 4.5 lb.
Veuillez conserver la source et l'adresse de cet article pour réimpression: La relation entre le problème de moisissure collante et l'agent de démoulage
Minghé Société de moulage sous pression sont dédiés à la fabrication et à la fourniture de pièces de moulage de qualité et de haute performance (la gamme de pièces de moulage sous pression en métal comprend principalement Moulage sous pression à paroi mince,Chambre chaude coulée sous pression,Chambre froide coulée sous pression), Service rond (Service de moulage sous pression,Usinage CNC,Fabrication de moules,Traitement de surface). Tout moulage sous pression en aluminium personnalisé, moulage sous pression en magnésium ou en zamak/zinc et autres exigences en matière de moulages sont invités à nous contacter.
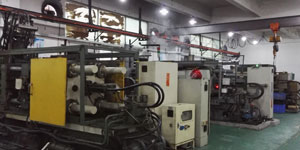
Sous le contrôle des normes ISO9001 et TS 16949, tous les processus sont effectués via des centaines de machines de moulage sous pression avancées, de machines à 5 axes et d'autres installations, allant des blasters aux machines à laver Ultra Sonic.Minghe dispose non seulement d'équipements de pointe, mais également de professionnels équipe d'ingénieurs, d'opérateurs et d'inspecteurs expérimentés pour réaliser la conception du client.
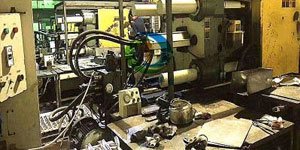
Fabricant sous contrat de moulages sous pression. Les capacités incluent des pièces de moulage sous pression en aluminium à chambre froide à partir de 0.15 lb. jusqu'à 6 lb, configuration à changement rapide et usinage. Les services à valeur ajoutée comprennent le polissage, la vibration, l'ébavurage, le grenaillage, la peinture, le placage, le revêtement, l'assemblage et l'outillage. Les matériaux travaillés comprennent des alliages tels que 360, 380, 383 et 413.
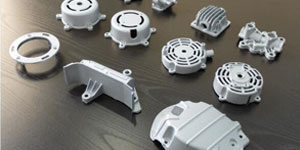
Assistance à la conception de moulage sous pression de zinc/services d'ingénierie simultanés. Fabricant sur mesure de pièces moulées en zinc de précision. Des moulages miniatures, des moulages sous pression à haute pression, des moulages en moules à glissières multiples, des moulages en moules conventionnels, des moulages sous pression unitaires et indépendants et des moulages à cavité scellée peuvent être fabriqués. Les pièces moulées peuvent être fabriquées dans des longueurs et des largeurs allant jusqu'à 24 po avec une tolérance de +/- 0.0005 po.
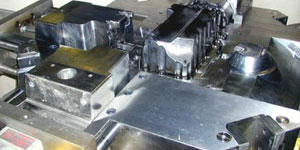
Fabricant certifié ISO 9001 : 2015 de magnésium moulé sous pression, les capacités incluent le moulage sous pression de magnésium sous pression jusqu'à une chambre chaude de 200 tonnes et une chambre froide de 3000 tonnes, la conception d'outillage, le polissage, le moulage, l'usinage, la peinture en poudre et liquide, une assurance qualité complète avec des capacités CMM , assemblage, emballage et livraison.
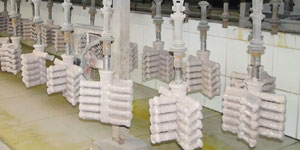
Certifié ITAF16949. Service de casting supplémentaire inclus coulée d'investissement,moulage en sable,Coulée par gravité, Coulée de mousse perdue,Coulée centrifuge,Coulée sous vide,Moulage de moule permanentLes capacités comprennent l'EDI, l'assistance technique, la modélisation solide et le traitement secondaire.
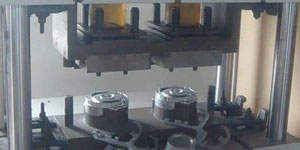
Industries de moulage Études de cas de pièces pour : voitures, vélos, avions, instruments de musique, motomarines, appareils optiques, capteurs, modèles, appareils électroniques, boîtiers, horloges, machines, moteurs, meubles, bijoux, gabarits, télécommunications, éclairage, appareils médicaux, appareils photographiques, Robots, Sculptures, Équipement de sonorisation, Équipement de sport, Outillage, Jouets et plus encore.
Que pouvons-nous vous aider à faire ensuite ?
∇ Aller à la page d'accueil pour Moulage sous pression Chine
→Pièces de fonderie-Découvrez ce que nous avons fait.
→Conseils à propos de Services de moulage sous pression
By Fabricant de moulage sous pression Minghe |Catégories : Articles utiles |Matières Mots clés: Moulage d'aluminium, Moulage de zinc, Coulée de magnésium, Moulage de titane, Fonderie en acier inoxydable, Coulée de laiton,Coulée de bronze,Vidéo de casting,Historique de l'entreprise,Moulage sous pression en aluminium |Commentaires fermés