L'application de la technologie de prototypage rapide dans le moulage de précision
Le Prototypage Rapide (RP) est une technologie de pointe développée dans les années 1990. Il peut rapidement transformer les concepts de conception dans l'esprit des gens en objets réels. Il est particulièrement intéressant de mentionner que l'ensemble du processus de développement de produits ne nécessite aucun moule ni équipement de traitement, ce qui raccourcit considérablement le cycle de production d'essai de prototypes et de nouveaux produits, et devient rapidement un moyen et un outil important pour améliorer la compétitivité des entreprises. L'enquête par questionnaire Internet publiée par l'INCAST 2004 (11) montre que plus de 93 % des plus de 400 fabricants de moulage de précision en Europe ont utilisé le prototypage rapide. Toutes les personnes interrogées conviennent que l'utilisation de cette nouvelle technologie est essentielle pour accélérer les nouveaux produits. Il est très important de développer et d'améliorer la capacité des entreprises à réagir rapidement au marché.
L'application des méthodes courantes de prototypage rapide dans le moulage de précision
L'application de la technologie de prototypage rapide dans le moulage de précision comprend principalement les aspects suivants :
1. Faire un investissement
Lors de la création de modèles, la machine de prototypage rapide peut non seulement saisir des modèles géométriques tridimensionnels établis par d'autres logiciels de CAO, mais également recevoir des fichiers de données numérisés par CT industriel (tomographie par ordinateur). Par exemple, scannez d'abord la pièce (hélice, Figure 12-1a) par CT pour obtenir une image en deux dimensions de sa section transversale (Figure 12-1b). Par la suite, le logiciel de traitement d'images combine les images bidimensionnelles de chaque section (Figure 12-1c) pour former un modèle géométrique tridimensionnel (Figure 12-1d). Envoyez-le ensuite à la machine de prototypage rapide pour réaliser un patron (Figure 12-1e) [2]. Cette méthode de restauration (reverse) engineering peut non seulement restaurer des pièces de machine, mais aussi imiter certains organes humains.
2. Fabrication de moules (moulage par compression) et d'autres équipements de traitement
Il existe deux méthodes pour fabriquer des moules de coulée de précision par prototypage rapide : l'une consiste à faire d'abord un moule maître, puis à refaire un profilage en époxy ou en caoutchouc de silicone ; l'autre méthode consiste à utiliser le bloc de profilage tridimensionnel généré dans le système de CAO. Le modèle géométrique est directement entré dans la machine de prototypage rapide pour effectuer le moulage en résine. Ce type de profilage est principalement adapté à la production de petites séries (des dizaines de pièces). Si une couche métallique d'environ 2 mm d'épaisseur est pulvérisée sur la surface du moule principal et que la résine époxy est ensuite remplie pour créer un profil composite métal-époxy, elle peut répondre aux exigences de production de centaines de pièces moulées de précision. Lors de l'utilisation de la méthode SLS, par exemple, l'objet de traitement passe de la poudre de résine à la poudre d'acier avec une fine couche de résine thermodurcissable à la surface, fritté au laser pour former un compact, puis cuit pour éliminer la résine, et enfin le cuivre liquide s'infiltre dans les pores du compact. Le profilage résultant est similaire au métal en termes de résistance et de conductivité thermique. De plus, la technologie de prototypage rapide peut également être utilisée pour fabriquer certains moules de forme irrégulière.
3. Production directe de pièces moulées
Au début des années 1990, le laboratoire national de Sandiana aux États-Unis a mené une étude spéciale appelée Fast Casting (FastCAST), qui a été baptisée Direct Shell Casting (DSPC). Malheureusement, il y a très peu de rapports plus tard.
En 1994, Z Corporation des États-Unis a développé avec succès la technologie d'impression 3D Impression 3D. La technologie a été inventée et brevetée à l'origine par le professeur Ely Sachs du Massachusetts Institute of Technology. Le principe de base est similaire à la méthode SLS. Tout d'abord, une couche de matériau réfractaire ou de poudre plastique est pulvérisée avec un rouleau. La différence avec le SLS est qu'au lieu de piloter une tête d'émission laser, il pilote une tête d'impression à jet d'encre pour pulvériser de la colle pour « imprimer » en fonction de la forme de la section transversale du produit. Répétez les actions ci-dessus jusqu'à ce que les pièces soient terminées, il s'appelle donc « technologie d'impression 3D ». Ses avantages sont des coûts d'exploitation et des coûts de matériaux faibles, ainsi qu'une vitesse élevée. Si la poudre pulvérisée est un mélange de poudre de gypse et de céramique, elle peut être directement et rapidement transformée en moule (moule de gypse) pour la coulée d'aluminium, de magnésium, de zinc et d'autres alliages non ferreux, appelé ZCast (Figure 12-2) .
La comparaison des effets d'application des méthodes de prototypage rapide couramment utilisées
À l'heure actuelle, les méthodes de prototypage rapide les plus populaires dans la production réelle comprennent la lithographie tridimensionnelle (SLA), le frittage laser sélectif (SLS), le dépôt par fusion (FDM), la fabrication de stratifiés (LOM) et le moulage direct par moulage (DSPC) Attendez. Ces dernières années, de nombreux instituts de recherche étrangers ont comparé les méthodes ci-dessus en termes de qualité des modèles de production et de performances dans le moulage de précision. Les résultats sont les suivants:
- 1) La méthode SLA a la plus grande précision dimensionnelle du motif, suivie par SLS et FDM, et la méthode LOM est la plus faible [4].
- 2) Rugosité de surface du motif La surface du motif est polie et finie et mesurée avec un mesureur de rugosité de surface. Les résultats sont présentés dans le tableau 12-1 [4]. On peut voir que la rugosité de surface est plus fine par les méthodes SLA et LOM, et la méthode FDM est la plus épaisse.
- 3) La capacité à reproduire des pièces fines La capacité de ces quatre méthodes à reproduire des pièces fines a été étudiée avec une crémaillère avec un pas de dent d'environ 3 mm comme objet. En conséquence, SLA est le meilleur et FDM est le pire [4].
- 4) Performance dans la coulée de précision Parmi les quatre méthodes ci-dessus, le produit lui-même est une méthode de moulage en cire (telle que FDM ou SLS), qui peut facilement s'adapter aux exigences du processus de coulée de précision et sans aucun doute de meilleures performances. Bien que les modèles en résine ou en papier puissent également être brûlés, ils ne sont pas aussi faciles à adapter aux exigences de la coulée de précision que les moules en cire. Des améliorations continues sont nécessaires pour éviter les inconvénients.
Comparaison de la rugosité de surface des motifs
Pièce de mesure | Lom | SLS | FDM | Contrat de niveau de service |
Plan de niveau | 1.5 | 5.6 | 14.5 | 0.6 |
Plan incliné | 2.2 | 4.5 | 11.4 | 6.9 |
Plan vertical | 1.7 | 8.2 | 9.5 | 4.6 |
D'un point de vue global, bien que la méthode SLA présente une certaine incompatibilité avec le procédé de moulage à la cire perdue, elle est populaire en raison de sa bonne précision dimensionnelle et de sa qualité de surface. Dans les pays étrangers, en particulier dans les industries aérospatiale et militaire, les entreprises de moulage de précision sont largement utilisées. Bien que la qualité de la méthode SLS soit légèrement inférieure à celle de la SLA, elle s'adapte facilement aux exigences du processus de moulage à la cire perdue. Par conséquent, de plus en plus d'applications sont utilisées dans le moulage de précision domestique. Bien que la méthode FDM soit la plus facile à adapter aux exigences du processus de moulage de précision, la précision dimensionnelle et la qualité de surface des moules en cire ne sont pas satisfaisantes ; tandis que la méthode LOM est de qualité acceptable, mais elle est difficilement adaptable à la coulée de précision. Par conséquent, il est difficile de s'adapter à la coulée de précision. La promotion et l'application des deux méthodes en moulage de précision sont soumises à certaines restrictions.
Nouveaux développements dans l'application des SLA et SLS dans le moulage de précision
1. Nouvelle résine photopolymérisable
La méthode SLA a été commercialisée dès 1987. Elle était à l'origine utilisée pour réaliser des modèles physiques et des prototypes avec certaines fonctions. Au début des années 1990, le logiciel QuickCast de 3D System Inc aux États-Unis a été développé avec succès, permettant à la machine de prototypage rapide SLA de produire une structure en forme de nid d'abeille (Figure 12-3a) tout en conservant un aspect lisse et dense (Figure 12 -3b), non seulement économise 90% des matériaux de moulage, mais également lorsque la coque est cuite, le motif s'effondre d'abord vers l'intérieur sans fissurer la coque. De plus, les gens ont progressivement découvert que les résines photopolymérisables pour la fabrication de moules devaient également répondre aux exigences particulières suivantes :
- Viscosité - si la viscosité de la résine est trop élevée, il sera difficile de drainer la résine restante dans la cavité une fois le motif réalisé. S'il y a trop de résine résiduelle, elle peut encore fissurer la coque pendant la cuisson, une séparation centrifuge est donc souvent nécessaire. Les mesures. De plus, la surface du motif fini est également difficile à nettoyer.
- Cendres résiduelles - c'est peut-être l'exigence la plus importante. Si les cendres résiduelles après la cuisson de la coque, elles provoqueront des inclusions non métalliques et d'autres défauts à la surface de la pièce moulée.
- · Teneur en éléments métalliques lourds - ceci est particulièrement important pour la coulée de superalliages. Par exemple, l'antimoine est un élément relativement courant dans les résines photopolymérisables SLA. S'il apparaît dans les cendres résiduelles après la cuisson de l'obus, il peut contaminer l'alliage et même provoquer la mise au rebut de la fonte.
- Stabilité dimensionnelle - la taille du motif doit rester stable pendant toute l'opération. Pour cette raison, la faible absorption d'humidité de la résine est également très importante.
Ces dernières années, DSM Somos aux États-Unis a développé avec succès un nouveau type de résine photopolymérisable Somos 10120, qui répond aux principales exigences susmentionnées et est très appréciée des fabricants de moulage de précision. Ce nouveau produit a été coulé dans trois usines de moulage de précision différentes en trois alliages (aluminium, titane et alliage cobalt-molybdène) et a obtenu des résultats satisfaisants.
2. Utilisez le modèle SLA pour la production de petits lots
Deux problèmes principaux doivent être pris en compte dans la production en petits lots de pièces moulées de précision utilisant des modèles SLA : l'un est la précision dimensionnelle que le modèle et le moulage peuvent atteindre, et l'autre est de savoir si le coût de production et le délai de livraison présentent des avantages. Plusieurs usines de moulage de précision aux États-Unis, telles que Solidiform, Nu-Cast, PCC et Uni-Cast, ont utilisé des modèles SLA pour couler des centaines de pièces moulées. Après mesure réelle de la taille de coulée, l'analyse statistique montre que la nouvelle résine photopolymérisable 11120 développée par DSM Somos est utilisée. Avec la technologie QuickCast, le modèle SLA résultant présente un écart de taille ne dépassant pas 50 % de la valeur de tolérance de coulée. La taille de la plupart des pièces moulées répond aux exigences de tolérance et le taux de réussite est supérieur à 95 % (Figure 12-4) [7].
Bien que le coût de fabrication d'un modèle SLA soit beaucoup plus élevé que celui de la fabrication du même moule en cire, cela prend plus de temps, mais il n'est pas nécessaire de concevoir et de fabriquer le profilage. Par conséquent, lorsqu'une pièce unique est produite en petits lots, le coût et le délai de livraison sont toujours des avantages. Plus le moulage est complexe, plus cet avantage est évident. Prenons comme exemple le moulage de précision d'aviation de forme complexe produit par Nu-Cast (Figure 12-5) [7], le coût de fabrication du moule est d'environ 85,000 4 dollars américains, 150 moules en cire sont produits chaque jour et le coût de chaque cire moule (y compris les matériaux et la main-d'œuvre) 2846 USD. Si la méthode SLA est adoptée, chaque modèle SLA coûte 32 dollars américains, mais il n'est pas nécessaire de concevoir et de fabriquer des moules. A partir de ce calcul, si la production est inférieure à 32 pièces, le coût d'utilisation des moules SLA est inférieur à celui des moules en cire ; si plus de 12 pièces, le coût est plus élevé que les moules en cire (Figure 6-14) ; en utilisant des moules en cire, il faut 16 à 87 semaines pour concevoir et fabriquer des moules, et le moule SLA ne nécessite pas de moule. Par conséquent, si la production est inférieure à 12 pièces, en utilisant des moules SLA, la livraison des pièces moulées est plus rapide que celle des moules en cire (Figure 7-87). Mais plus de 7 pièces, le moule en cire est plus rapide [XNUMX]. Un autre facteur à prendre en compte est que si un moule en cire est utilisé, lorsque le produit est mis à jour, le moule doit être refait, ce qui est coûteux ; alors qu'avec l'apparence SLA, il suffit de changer le modèle géométrique CAO, ce qui est beaucoup plus facile et rapide que de refaire le moule. .
3. Modèle de cire imprégné de poudre de polystyrène fritté SLS
SLS a initialement utilisé un laser pour fritter une poudre de cire spéciale dans un moule en cire, ce qui convient parfaitement aux caractéristiques du processus de moulage à la cire perdue. Dès la fin de 1990, il y avait plus de 50 fonderies aux États-Unis, produisant environ 3000 moules en cire et les coulant avec succès. Produire une variété de pièces moulées en métal. Cependant, la poudre de cire n'est pas le matériau de moulage le plus idéal. La résistance du moule en cire fabriqué à partir de celui-ci est insuffisante, et il est facile à ramollir et à se déformer lorsque la température est élevée, et il est facile à casser lorsque la température est basse. Par conséquent, au début des années 1990, certains utilisateurs de SLA aux États-Unis ont essayé de remplacer la poudre de cire par des poudres thermoplastiques telles que le polystyrène (PS) ou le polycarbonate (PC). Ce type de matériau prend une forme lâche et poreuse (la porosité est supérieure à 25 %), ce qui réduit les risques de gonflement et de fissuration de la coque lors du démoulage. Après la cuisson de l'obus, la teneur en cendres est moindre, mais la surface du motif est rugueuse. Par conséquent, une fois le motif réalisé, il doit être ciré et poli à la main pour rendre la surface lisse et dense. À l'heure actuelle, cette méthode a été largement utilisée dans le pays et à l'étranger.
Veuillez conserver la source et l'adresse de cet article pour réimpression:L'application de la technologie de prototypage rapide dans le moulage de précision
Minghe Casting Company se consacre à la fabrication et à la fourniture de pièces de moulage de qualité et de haute performance (la gamme de pièces de moulage sous pression en métal comprend principalement Moulage sous pression à paroi mince,Chambre chaude coulée sous pression,Chambre froide coulée sous pression), Service rond (Service de moulage sous pression,Usinage CNC,Fabrication de moules,Traitement de surface). Tout moulage sous pression en aluminium personnalisé, moulage sous pression en magnésium ou en zamak/zinc et autres exigences en matière de moulages sont invités à nous contacter.
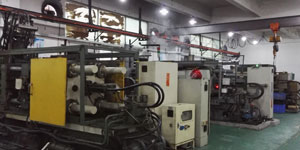
Sous le contrôle des normes ISO9001 et TS 16949, tous les processus sont effectués via des centaines de machines de moulage sous pression avancées, de machines à 5 axes et d'autres installations, allant des blasters aux machines à laver Ultra Sonic.Minghe dispose non seulement d'équipements de pointe, mais également de professionnels équipe d'ingénieurs, d'opérateurs et d'inspecteurs expérimentés pour réaliser la conception du client.
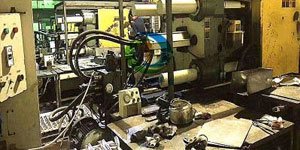
Fabricant sous contrat de moulages sous pression. Les capacités incluent des pièces de moulage sous pression en aluminium à chambre froide à partir de 0.15 lb. jusqu'à 6 lb, configuration à changement rapide et usinage. Les services à valeur ajoutée comprennent le polissage, la vibration, l'ébavurage, le grenaillage, la peinture, le placage, le revêtement, l'assemblage et l'outillage. Les matériaux travaillés comprennent des alliages tels que 360, 380, 383 et 413.
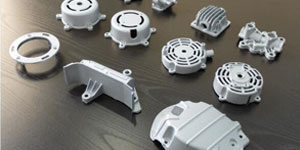
Assistance à la conception de moulage sous pression de zinc/services d'ingénierie simultanés. Fabricant sur mesure de pièces moulées en zinc de précision. Des moulages miniatures, des moulages sous pression à haute pression, des moulages en moules à glissières multiples, des moulages en moules conventionnels, des moulages sous pression unitaires et indépendants et des moulages à cavité scellée peuvent être fabriqués. Les pièces moulées peuvent être fabriquées dans des longueurs et des largeurs allant jusqu'à 24 po avec une tolérance de +/- 0.0005 po.
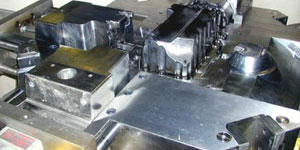
Fabricant certifié ISO 9001 : 2015 de magnésium moulé sous pression, les capacités incluent le moulage sous pression de magnésium sous pression jusqu'à une chambre chaude de 200 tonnes et une chambre froide de 3000 tonnes, la conception d'outillage, le polissage, le moulage, l'usinage, la peinture en poudre et liquide, une assurance qualité complète avec des capacités CMM , assemblage, emballage et livraison.
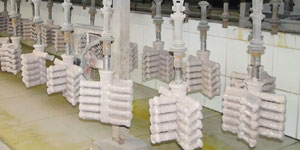
Certifié ITAF16949. Service de casting supplémentaire inclus coulée d'investissement,moulage en sable,Coulée par gravité, Coulée de mousse perdue,Coulée centrifuge,Coulée sous vide,Moulage de moule permanentLes capacités comprennent l'EDI, l'assistance technique, la modélisation solide et le traitement secondaire.
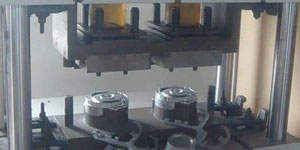
Industries de moulage Études de cas de pièces pour : voitures, vélos, avions, instruments de musique, motomarines, appareils optiques, capteurs, modèles, appareils électroniques, boîtiers, horloges, machines, moteurs, meubles, bijoux, gabarits, télécommunications, éclairage, appareils médicaux, appareils photographiques, Robots, Sculptures, Équipement de sonorisation, Équipement de sport, Outillage, Jouets et plus encore.
Que pouvons-nous vous aider à faire ensuite ?
∇ Aller à la page d'accueil pour Moulage sous pression Chine
→Pièces de fonderie-Découvrez ce que nous avons fait.
→Conseils à propos de Services de moulage sous pression
By Fabricant de moulage sous pression Minghe |Catégories : Articles utiles |Matières Mots clés: Moulage d'aluminium, Moulage de zinc, Coulée de magnésium, Moulage de titane, Fonderie en acier inoxydable, Coulée de laiton,Coulée de bronze,Vidéo de casting,Historique de l'entreprise,Moulage sous pression en aluminium |Commentaires fermés