Technologie de préparation de composite à matrice métallique renforcée de particules par méthode de coulée
Les composites à matrice métallique sont des matériaux multiphasiques avec une seconde phase spéciale dispersée dans une matrice métallique ou en alliage. La deuxième phase avec des propriétés physiques et mécaniques spéciales améliore considérablement la résistance, la dureté, la résistance à l'usure, la résistance à la chaleur et d'autres propriétés du matériau. Par conséquent, cette deuxième phase est également appelée phase de renforcement. La phase de renforcement est généralement divisée en une phase de renforcement de particules et une phase de renforcement en fibres (moustaches). Pour des raisons telles que le prix du renfort et la technologie composite, la plupart des matériaux composites fabriqués par la méthode de coulée sont renforcés de particules.
Ces dernières années, le procédé de préparation de matériaux composites renforcés de particules s'est continuellement amélioré dans la méthode physique d'ajout du renfort, et la synthèse de réaction in situ du procédé de renfort a été développée.
Quel que soit le type de méthode de moulage composite utilisé, pour préparer avec succès des produits composites avec d'excellentes performances et une qualité stable, les problèmes suivants doivent être résolus techniquement :
- Sélectionnez la matrice et le renforcement appropriés en fonction des différentes exigences du matériau,
- Améliorer la mouillabilité de la matrice fondue au renfort,
- contrôler la répartition raisonnable du ferraillage dans la matrice,
- Résoudre le problème du processus de formage par coulée causé par l'effet des particules de renforcement sur la viscosité de la masse fondue de la matrice.
Cet article résume les problèmes mentionnés ci-dessus sur la technologie de préparation de la coulée de matériaux composites à matrice métallique renforcée de particules, afin de promouvoir la production de matériau composite renforcé de particules.
- Sélection des renforts : les performances de la matrice, le renfort et la bonne combinaison du renfort et de la matrice déterminent les performances du matériau composite, de sorte que le renfort doit être sélectionné de manière raisonnable en fonction du type de substrat et des exigences de performance du matériau composite . Lors de la sélection d'un renfort, le module d'élasticité, la résistance à la traction, la dureté, la stabilité thermique, la densité, le point de fusion, le prix et d'autres facteurs du renfort doivent être pris en compte. Dans le même temps, le coefficient de dilatation linéaire et la réactivité chimique entre le renfort et la matrice doivent être adaptés. Réclamer. La matrice avec l'aluminium comme composant principal, les renforts couramment utilisés sont le graphite, l'Al2O3, le SiC, le TiC, l'Al3Ti, le TiB, l'Al3Zr, etc. La recherche sur les matériaux composites avec l'acier comme matrice n'est pas aussi mature que l'aluminium composites à matrice, et les renforts couramment utilisés sont plus matures. Moins, principalement WC, VC, TiC, TiN, Al2O3, SiC, etc. Une fois le type de renforcement sélectionné, la taille du renforcement et sa fraction volumique dans la matrice doivent également être déterminées par des expériences.
- Méthodes pour améliorer la mouillabilité du renfort/matrice : améliorer la mouillabilité du renfort par la masse fondue de la matrice, aider à réduire l'agglomération du renfort, aider à améliorer la force de liaison de l'interface matrice/renfort, et améliorer le matériau composite global Dans d'autres termes, il contribue également à la répartition uniforme du renforcement dans la matrice. Les mesures suivantes sont généralement utilisées pour améliorer la mouillabilité de la matrice fondue au renforcement.
- Traitement de revêtement de surface de renforcement : le revêtement d'un certain métal ou composé sur la surface de renforcement par des méthodes telles que le placage autocatalytique ou le dépôt en phase vapeur peut améliorer efficacement la mouillabilité de la matrice fondue sur le corps de renforcement. Des études ont montré que le revêtement de cuivre à la surface du graphite et le dépôt en phase vapeur de TiN à la surface des particules d'Al2O3 ont efficacement amélioré la mouillabilité de la matrice aux particules de renforcement.
- Tensioactifs supplémentaires : selon les rapports, l'ajout de blocs de magnésium tout en ajoutant de la poudre de graphite ou de silice à la fonte d'aluminium peut améliorer la mouillabilité de l'aluminium liquide au renforcement. Les recherches de ces dernières années ont également montré qu'en plus du Mg, Ca, RE, les éléments alcalins et les éléments du groupe VI et du groupe VIa ont tous pour effet d'améliorer la mouillabilité de l'aluminium fondu sur des renforts tels que l'Al2O3 et le SiC.
- Traitement thermique du renforcement : Le traitement thermique pour éliminer l'huile et l'eau à la surface des particules de renforcement peut augmenter l'énergie de surface du renforcement et augmenter la mouillabilité de la masse fondue au renforcement. Quelqu'un a préparé des matériaux composites graphite/aluminium en utilisant de la poudre de graphite traitée thermiquement sans revêtement en cuivre. La méthode de traitement thermique consiste à : chauffer la poudre de graphite à environ 600°C pendant 8 heures pour activer la surface, puis refroidir et réchauffer à 200°C avant d'ajouter le liquide d'aluminium pour éliminer l'humidité. Certaines personnes ont également utilisé la méthode de chauffage du renfort pour améliorer la mouillabilité du renfort et de la matrice pour produire des matériaux composites.
- Traitement par ultrasons à haute énergie de la fonte : quelqu'un a préparé un matériau composite SiC/ZA27 avec un traitement par ultrasons à haute énergie de la fonte. L'étude estime que l'effet de cavitation produit par les ultrasons à haute énergie lors de la propagation dans la masse fondue nettoie la surface des particules renforcées, augmente la tension superficielle des particules et réduit en même temps la tension superficielle de la masse fondue et améliore considérablement la relation entre les particules de SiC et le bain de fusion ZA27. Mouillabilité.
- Synthèse par réaction in situ du renforcement : l'application de la technologie de synthèse par réaction in situ pour préparer un alliage maître contenant des particules de renforcement, puis l'ajout de cet alliage maître à la matrice fondue pour préparer la technologie des matériaux composites est devenue un point chaud dans la recherche sur les matériaux composites au cours des dernières années. La méthode de synthèse par réaction in situ ajoute généralement des métaux purs, des alliages, des composés ou des substances salines à l'alliage maître, et le renforcement est obtenu par des réactions chimiques entre les additifs ou entre les additifs et les composants de l'alliage maître. Parce que le renforcement est généré par réaction in-situ, la surface est propre et sans pollution, et la stabilité thermique est bonne, ce qui résout bien le problème de la mouillabilité du renforcement par la masse fondue, et le renforcement et la matrice sont très fermement combiné avec un meilleur effet de renforcement. Certains scientifiques ont mélangé des poudres d'Al, de Ti et de C dans une certaine proportion, puis les ont pressés en petits morceaux. Les petites pièces ont été frittées sous vide dans un four à diffusion à haute température pour obtenir un alliage maître TiC/Al, et le composite TiC/2618 a été préparé à partir de l'alliage maître. Matériel. D'autres ont également préparé avec succès des matériaux composites avec une répartition uniforme des particules renforcées et d'excellentes propriétés par synthèse réactionnelle in situ.
- Technologie de contrôle de la répartition des renforts : Maîtriser la répartition des renforts dans la matrice et faire jouer pleinement le renforcement efficace de la matrice est la garantie fondamentale pour préparer des produits composites répondant à certaines exigences de performances.
- La méthode de contrôle de la distribution non uniforme des renforts : pour les matériaux résistants à l'usure/réducteurs d'usure, la surface de travail doit avoir des performances anti-usure élevées, tandis que les pièces restantes ont de meilleures propriétés mécaniques globales pour garantir que la surface de travail est effectivement pris en charge.
Par conséquent, de tels produits qui doivent être renforcés localement nécessitent que le renforcement soit réparti dans une certaine plage à proximité de la surface de travail du produit. Il existe plusieurs méthodes couramment utilisées :
- Méthode de pré-renforcement : La méthode de pré-renforcement est l'une des principales méthodes de préparation de matériaux composites renforcés en surface par la méthode additive. Il s'agit d'une application de la technologie de modification de surface de la méthode d'infiltration par coulée dans la préparation de matériaux composites. Convient principalement à la préparation de produits composites résistants à l'usure. La méthode spécifique est la suivante : pré-placer le renfort sous forme de bloc de peinture ou de pâte sur la partie où le produit doit être renforcé, puis le verser dans le liquide d'alliage de la matrice. Le liquide d'alliage de matrice pénètre dans l'espace du corps de renfort par l'effet de siphon capillaire et la pression du liquide d'alliage, et se solidifie. Ensuite, un produit composite renforcé en surface dans lequel le corps de renfort et la matrice sont étroitement combinés est formé. Les scientifiques ont mené des recherches approfondies sur cette technologie et pensent que la clé de la technologie des composites de surface pré-renforcés réside dans : une taille de particule de renfort appropriée et une bonne mouillabilité du renfort par la masse fondue matricielle ; ② sélection et revêtement du liant, processus de préparation et de brossage de la pâte, ③ contrôle de la température de coulée et processus de coulée ; la méthode de renforcement prédéfinie présente les caractéristiques d'un processus simple, d'un faible coût et d'un excellent effet. C'est une technologie de composite de surface qui a été appliquée avec succès à l'heure actuelle et a de très larges perspectives d'application.
- Méthode de contrôle centrifuge : sur la base de la différence de gravité spécifique du renfort et de la masse fondue de la matrice, la méthode de fabrication du renfort dans une distribution de ségrégation de gradient le long de la direction radiale à l'aide de la force centrifuge est appelée méthode de contrôle centrifuge. Une direction importante du développement des matériaux composites à gradient. Quelqu'un a utilisé une méthode de contrôle centrifuge pour préparer un matériau composite graphite/aluminium avec une distribution de gradient de graphite. Les scientifiques ont coulé par centrifugation l'alliage Al-Fe, qui ont obtenu le tuyau coulé composite à gradient auto-générant dans lequel la phase primaire de Fe est distribuée le long du gradient radial. Le matériau composite à gradient auto-généré en alliage Al-Fe coulé par centrifugation métallique revêtu de sable a souligné : Au fur et à mesure que le nombre de renforts augmente, le gradient de distribution des renforts dans la direction radiale diminue progressivement et la plage de distribution dans la direction radiale s'étend progressivement ; Dans la plage de 0~2000r/min, avec l'augmentation de la vitesse de rotation, le gradient de distribution du renfort le long de la direction radiale augmente progressivement, tandis que la plage de distribution dans la direction radiale diminue progressivement.
- Méthode de contrôle de l'agitation électromagnétique : les scientifiques ont appliqué une forte agitation électromagnétique CA à l'alliage fondu (Mg2Si)20Al80 pendant le processus de solidification pour préparer un matériau composite à gradient enrichi en Mg2Si sur la surface extérieure. Selon l'analyse, lorsqu'une agitation électromagnétique est effectuée, le métal en fusion sera soumis à une force électromagnétique dirigée vers l'axe dans le champ magnétique alternatif. En raison de la faible conductivité du renfort (Mg2Si naissant), il n'est fondamentalement pas affecté par la force électromagnétique dirigée vers l'axe, tandis que la force électromagnétique exercée sur la masse fondue est relativement importante, ce qui entraîne un champ de force déséquilibré autour du renfort, et le renfort est soumis à La force d'écrasement exercée par le métal en fusion loin du centre de l'arbre se déplace vers l'extérieur dans la direction radiale, obtenant ainsi un matériau composite à gradient avec une surface extérieure enrichie et renforcée. L'étude a montré que plus la tension du courant alternatif triphasé appliqué par l'agitateur électromagnétique est élevée, plus la force de cisaillement entre l'interface liquide/solide et le bain est importante et plus il est facile pour les particules primaires de Mg2Si d'être poussées. à la surface extérieure de l'échantillon, et la couche de ségrégation Le plus épais.
- Méthode de contrôle pour une répartition uniforme du renfort : Pour le matériau composite renforcé global, la répartition uniforme du renfort dans la matrice est très importante. Le renforcement du brassage de la masse fondue est le moyen fondamental pour atteindre l'objectif d'homogénéisation du renfort. Voici plusieurs méthodes de mélange efficaces :
- Agitation mécanique : L'agitation mécanique est la méthode la plus traditionnelle d'agitation de la masse fondue. En raison de la limitation du matériau des pales de l'agitateur, il existe peu d'exemples de la méthode d'agitation mécanique utilisée dans les alliages d'acier. Faites attention au brassage mécanique du bain de fusion : ① Choisissez judicieusement la matière et la forme de l'agitateur : l'agitateur est directement en contact avec le bain, ce qui peut facilement polluer l'alliage. Pour les alliages non ferreux, des lames non ferreuses doivent être utilisées ou des lames en acier doivent être recouvertes d'un revêtement externe (comme une couche d'argile blanche). Et le sens de rotation de la lame doit être sélectionné en fonction de la densité de particules du renfort. Bon mélange : la profondeur d'immersion des pales de l'agitateur doit être contrôlée de manière appropriée pour produire un vortex stable. L'agitation de la tige d'agitation ou des pales d'agitation inappropriées augmentera la probabilité que le renforcement soit repoussé par la masse fondue, détériorant ainsi la répartition du renforcement dans la matrice. ③Temps de mélange : Après avoir ajouté le renfort, le temps d'agitation doit être le plus long possible, et le temps d'attente pour verser après l'agitation doit être le plus court possible. Il existe un brevet américain pour "un dispositif pour mélanger des particules solides dans un liquide", qui stipule que le matériau composite produit par ce dispositif "surmonte les défauts courants des matériaux composites renforcés de particules, et a un temps de mélange court, une productivité élevée et à bas prix."
- Agitation de gaz : L'agitation de la masse fondue avec une grande quantité de gaz généré par le flux de gaz externe ou la réaction de fusion peut également atteindre l'objectif de répartir uniformément le renforcement dans la masse fondue. Les scientifiques ont utilisé une grande quantité de gaz généré par la réaction in situ pour agiter la masse fondue et ont préparé des composites Al3Zr(p).Al2O3(p)/A356 et (TiB2+TiAl3)/AlSi6Cu4 avec des renforts uniformément répartis.
- Traitement par ultrasons à haute énergie : les scientifiques ajoutent des particules de SiC à la surface de l'alliage ZA27 fondu à 600 °C et traitent la fonte avec des ultrasons à haute énergie pendant 60 à 90 s pour obtenir une suspension de particules fondues et la distribution globale des particules (comme -cast) est obtenu. Matériau composite SiCp/ZA27 uniforme. L'étude estime que l'atténuation d'amplitude finie des ultrasons à haute énergie dans le bain de fusion provoque un certain gradient de pression acoustique dans le bain de fusion pour former un jet de fluide, qui quitte directement la face d'extrémité du cornet à ultrasons et se forme dans l'ensemble du bain de fusion. Circulation (c'est-à-dire effet de courant acoustique), la vitesse du courant acoustique peut atteindre 10 à 103 fois la vitesse de convection du bain de fusion. Alors que le flux sonore élimine les impuretés de la surface des particules de renforcement, il envoie également les particules dans la partie profonde de la masse fondue et les disperse uniformément.
- Caractéristiques de performance de la fonte composite et points clés du processus de formage : La plus grande différence entre la fonte composite et la fonte ordinaire est l'introduction de particules solides de renforcement. En raison de l'introduction de particules solides, la viscosité de la masse fondue composite augmentera soudainement et de manière significative avec des traces de TiC et de TiB2, provoquant un changement soudain de la viscosité de la masse fondue d'aluminium. Les scientifiques ont souligné la théorie de la formation de coulée. La viscosité du métal liquide a un effet significatif sur les caractéristiques d'écoulement du métal dans le moule, le remplissage du moule, le flottement du gaz dans le métal liquide et l'alimentation du métal.
Afin d'obtenir un produit sain, le processus de mise en forme d'une masse fondue composite avec une augmentation soudaine de la viscosité doit faire face aux deux problèmes suivants :
- Améliorer la fluidité de la fonte et augmenter sa capacité de remplissage ;
- Empêcher la fonte d'inhaler du gaz et renforcer l'élimination du gaz dans la fonte.
Manchang Gui et d'autres ont développé un procédé de coulée sous vide à pression différentielle composé d'un tamis filtrant et d'une carotte. La masse fondue composite est directement introduite dans le moule après avoir traversé le filtre. Une fois le métal en fusion rempli, la carotte a toujours un effet de pression et elle est finalement solidifiée, de sorte qu'elle peut alimenter la coulée. Les caractéristiques de ce procédé de coulée se manifestent notamment dans :
- Éliminer essentiellement la source de gaz et éliminer essentiellement les défauts de pores générés lors du processus de coulée ;
- ②Simplifiez le système de coulée, le poids du système de coulée et le poids de la coulée sont réduits par rapport à la coulée sans vide (5-10):1 (0.5~1.5): 1 ;
- En surmontant les défauts de la faible fluidité de la masse fondue composite, il peut couler des pièces moulées composites complexes à paroi mince.
Outlook
La méthode de coulée est l'une des méthodes les plus prometteuses pour la préparation de matériaux composites. Les recherches futures devraient se concentrer sur les aspects suivants :
- ① Pour la matrice en métal ferreux, sélectionner des renforts en fonction des exigences de performance des matériaux composites ;
- ② Développer des méthodes de préparation plus faciles à réaliser et à appliquer à la production industrielle ;
- ③ Réduire de manière significative les coûts de matière et de fabrication des produits composites ;
- ④ Recherche sur la valorisation des matériaux composites Technologie de réutilisation.
Par conséquent, on pense que la méthode de coulée fera beaucoup dans la production de produits composites résistants à l'usure et à la chaleur.
Le matériau composite à matrice métallique est un matériau multiphasique avec une seconde phase spéciale dispersée dans une matrice métallique ou en alliage. La deuxième phase avec des propriétés physiques et mécaniques spéciales améliore considérablement la résistance, la dureté, la résistance à l'usure, la résistance à la chaleur et d'autres propriétés du matériau. Par conséquent, cette deuxième phase est également appelée phase de renforcement. La phase de renforcement est généralement divisée en une phase de renforcement de particules et une phase de renforcement en fibres (moustaches). Pour des raisons telles que le prix du renfort et la technologie composite, la plupart des matériaux composites fabriqués par la méthode de coulée sont renforcés de particules.
Veuillez conserver la source et l'adresse de cet article pour réimpression: Technologie de préparation de composite à matrice métallique renforcée de particules par méthode de coulée
Minghé Société de moulage sous pression sont dédiés à la fabrication et à la fourniture de pièces de moulage de qualité et de haute performance (la gamme de pièces de moulage sous pression en métal comprend principalement Moulage sous pression à paroi mince,Chambre chaude coulée sous pression,Chambre froide coulée sous pression), Service rond (Service de moulage sous pression,Usinage CNC,Fabrication de moules,Traitement de surface). Tout moulage sous pression en aluminium personnalisé, moulage sous pression en magnésium ou en zamak/zinc et autres exigences en matière de moulages sont invités à nous contacter.
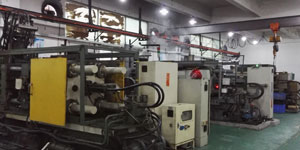
Sous le contrôle des normes ISO9001 et TS 16949, tous les processus sont effectués via des centaines de machines de moulage sous pression avancées, de machines à 5 axes et d'autres installations, allant des blasters aux machines à laver Ultra Sonic.Minghe dispose non seulement d'équipements de pointe, mais également de professionnels équipe d'ingénieurs, d'opérateurs et d'inspecteurs expérimentés pour réaliser la conception du client.
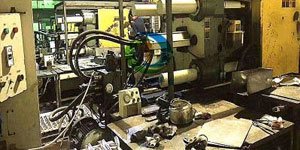
Fabricant sous contrat de moulages sous pression. Les capacités incluent des pièces de moulage sous pression en aluminium à chambre froide à partir de 0.15 lb. jusqu'à 6 lb, configuration à changement rapide et usinage. Les services à valeur ajoutée comprennent le polissage, la vibration, l'ébavurage, le grenaillage, la peinture, le placage, le revêtement, l'assemblage et l'outillage. Les matériaux travaillés comprennent des alliages tels que 360, 380, 383 et 413.
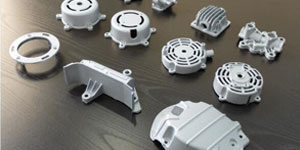
Assistance à la conception de moulage sous pression de zinc/services d'ingénierie simultanés. Fabricant sur mesure de pièces moulées en zinc de précision. Des moulages miniatures, des moulages sous pression à haute pression, des moulages en moules à glissières multiples, des moulages en moules conventionnels, des moulages sous pression unitaires et indépendants et des moulages à cavité scellée peuvent être fabriqués. Les pièces moulées peuvent être fabriquées dans des longueurs et des largeurs allant jusqu'à 24 po avec une tolérance de +/- 0.0005 po.
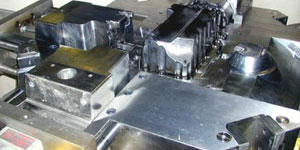
Fabricant certifié ISO 9001 : 2015 de magnésium moulé sous pression, les capacités incluent le moulage sous pression de magnésium sous pression jusqu'à une chambre chaude de 200 tonnes et une chambre froide de 3000 tonnes, la conception d'outillage, le polissage, le moulage, l'usinage, la peinture en poudre et liquide, une assurance qualité complète avec des capacités CMM , assemblage, emballage et livraison.
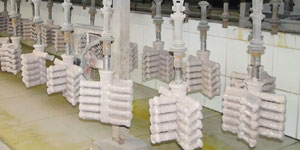
Certifié ITAF16949. Service de casting supplémentaire inclus coulée d'investissement,moulage en sable,Coulée par gravité, Coulée de mousse perdue,Coulée centrifuge,Coulée sous vide,Moulage de moule permanentLes capacités comprennent l'EDI, l'assistance technique, la modélisation solide et le traitement secondaire.
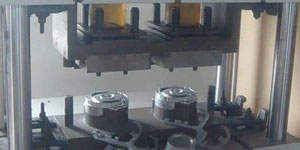
Industries de moulage Études de cas de pièces pour : voitures, vélos, avions, instruments de musique, motomarines, appareils optiques, capteurs, modèles, appareils électroniques, boîtiers, horloges, machines, moteurs, meubles, bijoux, gabarits, télécommunications, éclairage, appareils médicaux, appareils photographiques, Robots, Sculptures, Équipement de sonorisation, Équipement de sport, Outillage, Jouets et plus encore.
Que pouvons-nous vous aider à faire ensuite ?
∇ Aller à la page d'accueil pour Moulage sous pression Chine
→Pièces de fonderie-Découvrez ce que nous avons fait.
→Conseils à propos de Services de moulage sous pression
By Fabricant de moulage sous pression Minghe |Catégories : Articles utiles |Matières Mots clés: Moulage d'aluminium, Moulage de zinc, Coulée de magnésium, Moulage de titane, Fonderie en acier inoxydable, Coulée de laiton,Coulée de bronze,Vidéo de casting,Historique de l'entreprise,Moulage sous pression en aluminium |Commentaires fermés