Usinage de coupe de pièces de métallurgie des poudres (P/M)
L'utilisation du procédé de métallurgie des poudres (P/M) pour fabriquer des pièces pour les systèmes d'alimentation automobile continue de croître. Les pièces fabriquées par procédé P/M présentent de nombreux avantages importants et uniques. La structure poreuse résiduelle laissée intentionnellement dans ces pièces est bonne pour l'autolubrification et l'isolation acoustique. Des alliages complexes difficiles ou impossibles à fabriquer par le procédé de moulage traditionnel peuvent être produits en utilisant la technologie P/M. Les pièces fabriquées par cette technologie ont généralement peu ou pas de capacité de traitement, ce qui les rend moins chères et moins de déchets de matériaux. Malheureusement, derrière l'attrait de ces caractéristiques, les pièces P/M sont difficiles à usiner.
Bien que l'une des intentions initiales de l'industrie P/M soit d'éliminer tout traitement, cet objectif n'a pas encore été atteint. La plupart des pièces ne peuvent être que « proches de la forme finale » et nécessitent encore une finition.
Cependant, par rapport aux pièces moulées et forgées, une petite quantité de matériau qui doit être retirée des pièces P / M est un matériau typique résistant à l'usure.
La structure poreuse est l'une des caractéristiques qui font que les pièces p / M ont un large éventail d'utilisations, mais la durée de vie de l'outil sera également endommagée par la structure poreuse. La structure poreuse peut stocker de l'huile et du son, mais elle conduit également à une micro-coupe intermittente. Lors des allers-retours entre le trou et les particules solides, la pointe de l'outil est continuellement impactée, ce qui peut entraîner une très faible déformation par rupture de fatigue et un effondrement du bord fin le long du bord de coupe. Pour aggraver les choses, les particules sont généralement très dures. Même si la macrodureté du matériau mesuré est comprise entre 20 et 35 degrés, la granulométrie du composant atteint 60 degrés. Ces particules dures provoquent une usure sévère et rapide des bords. De nombreuses pièces p/M sont traitables thermiquement, et la dureté et la résistance du matériau sont plus élevées après traitement thermique. Enfin, en raison de la technologie de frittage et de traitement thermique et des gaz utilisés, la surface du matériau contiendra des oxydes et/ou des carbures durs et résistants à l'usure.
Performances des pièces P/M
La plupart des propriétés des pièces P/M, y compris l'usinabilité, sont liées non seulement à la composition chimique de l'alliage, mais aussi au niveau de porosité de la structure poreuse. La porosité de nombreuses pièces structurelles peut atteindre 15 % ± 20 %. La porosité des pièces utilisées comme dispositifs de filtration peut atteindre 50 %. A l'autre extrémité de la série, la porosité des pièces forgées ou de hanche n'est que de 1% ou moins. Ces matériaux deviennent particulièrement importants dans les applications automobiles et aéronautiques, car ils peuvent atteindre des niveaux de résistance plus élevés.
La résistance à la traction, la ténacité et la ductilité de l'alliage P/M augmenteront avec l'augmentation de la densité, et l'usinabilité peut également être améliorée, car la porosité est nocive pour la pointe de l'outil.
L'augmentation du niveau de porosité peut améliorer les performances d'isolation acoustique des pièces. L'amortissement des oscillations dans les pièces standard est considérablement réduit dans les pièces P/M, ce qui est très important pour les machines-outils, les chalumeaux de climatisation et les outils pneumatiques. Une porosité élevée est également nécessaire pour les engrenages autolubrifiants.
Difficultés d'usinage
Bien que l'un des objectifs du développement continu de l'industrie P/M soit d'éliminer l'usinage, et que l'un des principaux attraits du processus P/M soit que seule une petite quantité de traitement est nécessaire, de nombreuses pièces nécessitent encore un post-traitement pour obtenir une plus grande précision ou une meilleure finition de surface. Malheureusement, l'usinage de ces pièces est extrêmement difficile. La plupart des problèmes rencontrés sont dus à la porosité. La porosité entraîne une micro fatigue du tranchant. Le tranchant coupe constamment dedans et dehors. Il passe entre les particules et les trous. Un petit impact répété entraîne de petites fissures sur le tranchant.
Ces fissures de fatigue se développent jusqu'à ce que le tranchant s'effondre. Ce type de bord micro-écaillé est généralement très petit et présente généralement une usure abrasive normale.
La porosité réduit également la conductivité thermique des pièces P/M, ce qui entraîne une température élevée sur l'arête de coupe et provoque une usure en cratère et une déformation. La structure poreuse connectée à l'intérieur fournit un chemin pour l'évacuation du fluide de coupe de la zone de coupe. Cela peut provoquer des fissures à chaud ou des déformations, en particulier lors du perçage.
L'augmentation de surface provoquée par la structure poreuse interne entraîne également une oxydation et/ou une carbonisation lors du traitement thermique. Comme mentionné précédemment, ces oxydes et carbures sont durs et résistants à l'usure.
La structure poreuse donne également l'échec de la lecture de la dureté de la pièce, ce qui est extrêmement important. Lorsque la macro dureté d'une pièce P/M est mesurée intentionnellement, elle inclut le facteur de dureté du trou. La structure poreuse conduit à l'effondrement de la structure et donne une fausse impression de pièces relativement molles. Les particules sont beaucoup plus dures. Comme décrit ci-dessus, la différence est dramatique.
L'existence d'inclusions dans les pièces PM est également désavantageuse. Lors de l'usinage, ces particules seront arrachées de la surface et des rayures ou des rayures se formeront à la surface de la pièce lorsqu'elle sera frottée devant l'outil. Ces inclusions sont généralement de grande taille, laissant des trous visibles à la surface de la pièce.
La différence de teneur en carbone conduit à l'incohérence de l'usinabilité. Par exemple, la teneur en carbone de l'alliage fc0208 varie de 0.6% à 0.9%. Un lot de matériaux avec une teneur en carbone de 0.9% est relativement dur, ce qui entraîne une durée de vie de l'outil réduite. L'autre lot de matériaux à 0.6 % de carbone a une excellente durée de vie. Les deux alliages sont dans la plage admissible.
Le problème d'usinage final est lié au type de découpe qui se produit sur la pièce P/M. Comme la pièce est proche de la forme finale, la profondeur de coupe est généralement très faible. Cela nécessite un tranchant libre. L'accumulation de copeaux sur l'arête de coupe entraîne souvent des micro-écaillages.
Technologie de traitement
Pour surmonter ces problèmes, plusieurs technologies (uniques à l'industrie) sont appliquées. La structure poreuse de surface est souvent scellée par infiltration. Une coupe libre supplémentaire est généralement nécessaire. Récemment, des techniques améliorées de production de poudre conçues pour augmenter la propreté de la poudre et réduire les oxydes et les carbures pendant le traitement thermique ont été utilisées.
La structure poreuse à surface fermée est réalisée par infiltration de métal (généralement du cuivre) ou de polymère. Il a été supposé que l'infiltration agit comme un lubrifiant. La plupart des données expérimentales montrent que le véritable avantage réside dans la fermeture de la structure poreuse en surface et donc dans la prévention de la micro fatigue de l'arête de coupe. La réduction du broutage améliore la durée de vie de l'outil et l'état de surface. L'utilisation la plus spectaculaire de l'infiltration montre une augmentation de 200 % de la durée de vie de l'outil lorsque la structure poreuse est fermée.
Les additifs tels que MNS, s, MoS2, MgSiO3 et BN sont connus pour augmenter la durée de vie de l'outil. Ces additifs améliorent l'usinabilité en facilitant la séparation des copeaux de la pièce, en cassant les copeaux, en empêchant l'accumulation de copeaux et en lubrifiant l'arête de coupe. L'augmentation de la quantité d'additifs peut améliorer l'usinabilité, mais réduire la résistance et la ténacité.
La technologie d'atomisation des poudres pour contrôler les gaz du four de frittage et de traitement thermique permet de produire des poudres et des pièces propres, ce qui minimise l'apparition d'inclusions et de carbures d'oxyde de surface.
Matériel d'outil
Les outils les plus largement utilisés dans l'industrie P / M sont les matériaux résistants à l'usure, aux fissures des bords et sans éclats dans des conditions de bonne finition de surface. Ces caractéristiques sont utiles pour toute opération d'usinage, notamment pour les pièces P/M. Les matériaux d'outils inclus dans cette catégorie sont les outils en nitrure de bore cubique (CBN), les cermets non revêtus et revêtus et les carbures cémentés frittés améliorés revêtus.
Les outils CBN sont attrayants en raison de leur dureté élevée et de leur résistance à l'usure. Cet outil est utilisé depuis de nombreuses années dans le traitement de l'acier et de la fonte avec une dureté Rockwell de 45 et plus. Cependant, en raison des propriétés uniques de l'alliage P/M et de la différence significative entre la microdureté et la macrodureté, les outils CBN peuvent être utilisés pour les pièces P/M avec une dureté Rockwell de 25. Le paramètre clé est la dureté des particules. Lorsque la dureté des particules dépasse 50 degrés Rockwell, les outils CBN sont disponibles quelle que soit la valeur de la macro dureté. La limitation évidente de ces outils est leur manque de ténacité. En cas de coupe intermittente ou de porosité élevée, un renforcement des bords comprenant un chanfreinage négatif et un rodage lourd est nécessaire. Une coupe légère simple peut être effectuée avec un tranchant aiguisé.
Il existe plusieurs matériaux de CBN qui sont efficaces. Le matériau avec la meilleure ténacité est principalement composé du CBN entier. Ils ont une excellente ténacité, ils peuvent donc être utilisés pour l'ébauche. Leurs limites sont généralement liées à la finition de surface. Il est largement déterminé par les particules individuelles de CBN qui composent l'outil. Lorsque les particules tombent du bord de coupe, elles affectent la surface du matériau de la pièce. Cependant, il n'est pas si grave que l'outil à particules fines tombe d'une particule.
Le matériau CBN habituellement utilisé a une teneur élevée en CBN et une taille de particule moyenne. La lame de finition CBN est à grain fin et la teneur en CBN est faible. Ils sont plus efficaces lorsqu'une coupe légère et une finition de surface sont nécessaires ou lorsque l'alliage à traiter est particulièrement dur.
Dans de nombreuses applications de coupe, la durée de vie de l'outil est indépendante du type de matériau. En d'autres termes, n'importe quel matériau CBN peut atteindre une durée de vie d'outil similaire. Dans ces cas, le choix du matériau est principalement basé sur le coût le plus bas de chaque arête de coupe. Une lame ronde a une surface supérieure entière en CBN et peut fournir quatre arêtes de coupe ou plus, ce qui est moins cher que quatre lames CBN incrustées.
Lorsque la dureté des pièces P / M est inférieure à Rockwell 35 degrés et que la dureté des particules se situe dans la plage, le cermet est généralement l'un des choix. Les cermets sont très durs, peuvent empêcher efficacement l'accumulation de copeaux et peuvent résister à une vitesse élevée. De plus, comme les cermets ont toujours été utilisés pour l'usinage à grande vitesse et de finition de l'acier et de l'acier inoxydable, ils ont généralement des rainures géométriques idéales adaptées aux pièces proches de la forme.
Les cermets d'aujourd'hui sont complexes en métallurgie, avec jusqu'à 11 éléments d'alliage. Ils sont généralement frittés à partir de particules de TiCN et d'adhésif Ni Mo. Le TiCN offre une dureté, une résistance à l'accumulation de copeaux et une stabilité chimique qui sont importantes pour l'utilisation réussie des cermets. De plus, ces outils ont généralement une forte teneur en adhésif, ce qui signifie qu'ils ont une bonne ténacité. En un mot, ils présentent toutes les caractéristiques de traitement efficace de l'alliage P/M. Plusieurs types de cermets sont efficaces, tout comme le carbure de tungstène fritté en carbure cémenté, plus la teneur en liant est élevée, meilleure est la ténacité.
Un développement relativement nouveau connu est que le dépôt chimique en phase vapeur à température moyenne (mtcvd) offre également un avantage pour l'industrie P/M. Mtcvd conserve toute la résistance à l'usure et à l'usure en cratère du dépôt chimique en phase vapeur traditionnel (CVD), mais améliore également la ténacité de manière objective. L'augmentation de la ténacité provient principalement de la diminution des fissures. Le revêtement est déposé à haute température puis refroidi dans le four. Le revêtement contient des fissures lorsque l'outil atteint la température ambiante en raison d'une dilatation thermique irrégulière. Semblables aux rayures sur le verre plat, ces fissures réduisent la résistance du tranchant. La température de dépôt inférieure de mtcvd conduit à une fréquence de fissure plus faible et à une meilleure ténacité de l'arête de coupe.
Lorsque le substrat du revêtement CVD et du revêtement mtcvd ont les mêmes caractéristiques et le même revêtement de bord, la différence de leur ténacité peut être démontrée. Lorsqu'il est utilisé dans des applications où la ténacité des bords est requise, les performances du revêtement mtcvd sont meilleures que celles du revêtement CVD. Grâce à l'analyse, lors de l'usinage de pièces P/M à structure poreuse, la ténacité des bords est importante. Le revêtement Mtcvd est meilleur que le revêtement CVD.
Le revêtement de dépôt physique en phase vapeur (PVD) est plus mince et moins résistant à l'usure que le revêtement mtcvd ou CVD. Cependant, le revêtement PVD peut résister à des impacts importants lors de l'application. Le revêtement PVD est efficace lorsque la coupe est une usure abrasive, le CBN et les cermets sont trop cassants et nécessitent une excellente finition de surface.
Par exemple, le tranchant du carbure cémenté C-2 peut être usiné fc0205 à une vitesse de ligne de 180 m/min et une avance de 0.15 mm/tour. Après l'usinage de 20 pièces, l'accumulation de copeaux peut provoquer un micro-effondrement. Lorsque le revêtement PVD en nitrure de titane (TIN) est utilisé, l'accumulation de copeaux est limitée et la durée de vie de l'outil est prolongée. Lorsqu'un revêtement en étain est utilisé pour ce test, les caractéristiques d'usure abrasive des pièces P/M devraient être plus efficaces avec le revêtement TiCN. Le TiCN a presque la même résistance à l'accumulation de copeaux que l'étain, mais il est plus dur et plus résistant à l'usure que l'étain.
La structure poreuse est importante et affecte l'usinabilité de l'alliage fc0208. Lorsque la structure poreuse et les caractéristiques changent, différents matériaux d'outils offrent des avantages correspondants. Lorsque la densité est faible (6.4 g/cm3), la macrodureté est faible. Dans ce cas, le carbure cémenté revêtu mtcvd offre la meilleure durée de vie de l'outil. La micro fatigue du tranchant est très importante, et la ténacité du tranchant est très importante. Dans ce cas, une lame cermet de bonne ténacité assure une durée de vie maximale de l'outil.
Lors de la production du même alliage avec une densité de 6.8 g/cm3, l'usure abrasive devient plus importante que la fissure des bords. Dans ce cas, le revêtement mtcvd offre la meilleure durée de vie de l'outil. Le carbure cémenté revêtu de PVD est utilisé pour tester les deux types de pièces extrêmement dures, et il se brise lorsqu'il touche l'arête de coupe.
Lorsque la vitesse augmente (la vitesse linéaire est supérieure à 300 mètres par minute), les cermets et même les cermets revêtus produiront une usure en cratère. Le carbure cémenté revêtu est plus approprié, en particulier lorsque la ténacité de l'arête de coupe du carbure cémenté revêtu est bonne. Le revêtement Mtcvd est particulièrement efficace pour le carbure cémenté avec une zone riche en cobalt.
Les cermets sont le plus souvent utilisés pour le tournage et l'alésage. Les carbures cémentés revêtus de PVD sont idéaux pour l'usinage de filetage car des vitesses plus faibles et une plus grande attention à l'accumulation peuvent être attendues.
Veuillez conserver la source et l'adresse de cet article pour réimpression:Usinage de coupe de pièces de métallurgie des poudres (P/M)
Minghe Casting Company se consacre à la fabrication et à la fourniture de pièces de moulage de qualité et de haute performance (la gamme de pièces de moulage sous pression en métal comprend principalement Moulage sous pression à paroi mince,Chambre chaude coulée sous pression,Chambre froide coulée sous pression), Service rond (Service de moulage sous pression,Usinage CNC,Fabrication de moules,Traitement de surface). Tout moulage sous pression en aluminium personnalisé, moulage sous pression en magnésium ou en zamak/zinc et autres exigences en matière de moulages sont invités à nous contacter.
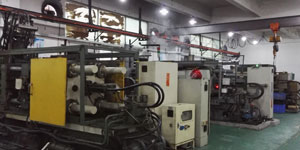
Sous le contrôle des normes ISO9001 et TS 16949, tous les processus sont effectués via des centaines de machines de moulage sous pression avancées, de machines à 5 axes et d'autres installations, allant des blasters aux machines à laver Ultra Sonic.Minghe dispose non seulement d'équipements de pointe, mais également de professionnels équipe d'ingénieurs, d'opérateurs et d'inspecteurs expérimentés pour réaliser la conception du client.
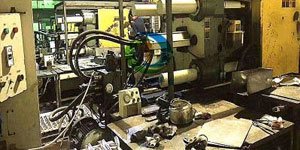
Fabricant sous contrat de moulages sous pression. Les capacités incluent des pièces de moulage sous pression en aluminium à chambre froide à partir de 0.15 lb. jusqu'à 6 lb, configuration à changement rapide et usinage. Les services à valeur ajoutée comprennent le polissage, la vibration, l'ébavurage, le grenaillage, la peinture, le placage, le revêtement, l'assemblage et l'outillage. Les matériaux travaillés comprennent des alliages tels que 360, 380, 383 et 413.
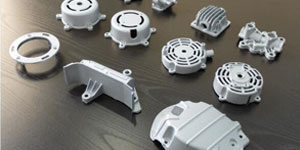
Assistance à la conception de moulage sous pression de zinc/services d'ingénierie simultanés. Fabricant sur mesure de pièces moulées en zinc de précision. Des moulages miniatures, des moulages sous pression à haute pression, des moulages en moules à glissières multiples, des moulages en moules conventionnels, des moulages sous pression unitaires et indépendants et des moulages à cavité scellée peuvent être fabriqués. Les pièces moulées peuvent être fabriquées dans des longueurs et des largeurs allant jusqu'à 24 po avec une tolérance de +/- 0.0005 po.
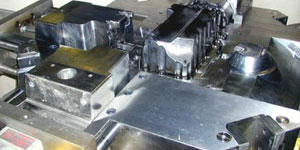
Fabricant certifié ISO 9001 : 2015 de magnésium moulé sous pression, les capacités incluent le moulage sous pression de magnésium sous pression jusqu'à une chambre chaude de 200 tonnes et une chambre froide de 3000 tonnes, la conception d'outillage, le polissage, le moulage, l'usinage, la peinture en poudre et liquide, une assurance qualité complète avec des capacités CMM , assemblage, emballage et livraison.
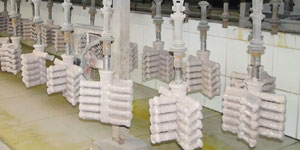
Certifié ITAF16949. Service de casting supplémentaire inclus coulée d'investissement,moulage en sable,Coulée par gravité, Coulée de mousse perdue,Coulée centrifuge,Coulée sous vide,Moulage de moule permanentLes capacités comprennent l'EDI, l'assistance technique, la modélisation solide et le traitement secondaire.
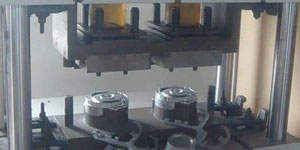
Industries de moulage Études de cas de pièces pour : voitures, vélos, avions, instruments de musique, motomarines, appareils optiques, capteurs, modèles, appareils électroniques, boîtiers, horloges, machines, moteurs, meubles, bijoux, gabarits, télécommunications, éclairage, appareils médicaux, appareils photographiques, Robots, Sculptures, Équipement de sonorisation, Équipement de sport, Outillage, Jouets et plus encore.
Que pouvons-nous vous aider à faire ensuite ?
∇ Aller à la page d'accueil pour Moulage sous pression Chine
→Pièces de fonderie-Découvrez ce que nous avons fait.
→Conseils à propos de Services de moulage sous pression
By Fabricant de moulage sous pression Minghe |Catégories : Articles utiles |Matières Mots clés: Moulage d'aluminium, Moulage de zinc, Coulée de magnésium, Moulage de titane, Fonderie en acier inoxydable, Coulée de laiton,Coulée de bronze,Vidéo de casting,Historique de l'entreprise,Moulage sous pression en aluminium |Commentaires fermés