Plusieurs problèmes auxquels il faut prêter attention dans la coulée de sable de silicate de sodium
1 Quels sont les facteurs qui affectent le "vieillissement" du verre soluble ? Comment éliminer le "vieillissement" du verre d'eau ?
Le verre d'eau fraîchement préparé est une véritable solution. Cependant, pendant le processus de stockage, l'acide silicique dans le verre soluble subira une polymérisation par condensation, qui se polycondensera progressivement de la vraie solution en une solution d'acide silicique macromoléculaire, et deviendra finalement un gel d'acide silicique. Par conséquent, le verre soluble est en fait un mélange hétérogène composé d'acide polysilicique avec différents degrés de polymérisation, qui est facilement affecté par son module, sa concentration, sa température, sa teneur en électrolyte et sa durée de stockage.
Pendant le stockage, les molécules de verre soluble subissent une polymérisation par condensation pour former un gel, et sa force de liaison diminue progressivement avec l'allongement de la durée de stockage. Ce phénomène est appelé "vieillissement" du verre d'eau.
Le phénomène de "vieillissement" peut s'expliquer par les deux séries de données d'essai suivantes : verre soluble à haut module (M=2.89, =1.44g/cm3) après 20, 60, 120, 180, 240 jours de stockage, le CO2 durcit le verre soluble est soufflé. La résistance à la traction à sec du sable chute de 9.9 %, 14 %, 23.5 %, 36.8 % et 40 % ; Le silicate de sodium à faible module (M=2.44, =1.41g/cm3) est stocké pendant 7, 30, 60 et 90 jours après avoir été séché. La résistance à la traction a diminué de 4.5%, 5%, 7.3% et 11% respectivement.
Le temps de stockage du verre soluble a peu d'effet sur la résistance initiale du sable auto-durcissant du verre soluble durci à l'ester, mais il a un effet significatif sur la résistance ultérieure. Selon les mesures, il est réduit d'environ 60 % pour le verre soluble à haut module et de 15 à 20 % pour le verre soluble à faible module. . La résistance résiduelle diminue également avec l'allongement de la durée de stockage.
Lors du stockage du verre soluble, la polycondensation et la dépolymérisation de l'acide polysilicique se déroulent en même temps, le poids moléculaire est disproportionné, et enfin un système multidispersé dans lequel coexistent de l'acide monoorthosilicique et des particules colloïdales se forme. C'est-à-dire que pendant le processus de vieillissement du verre soluble, le degré de polymérisation de l'acide silicique est disproportionné et la teneur en acide monoorthosilicique et en acide polysilicique élevé augmente avec l'allongement de la durée de stockage. En raison de la réaction de polymérisation par condensation et de dépolymérisation du verre soluble pendant le stockage, la force de liaison est réduite, c'est-à-dire que le phénomène de "vieillissement" se produit.
Les principaux facteurs affectant le "vieillissement" du verre soluble sont : le temps de stockage, le module et la concentration du verre soluble. Plus le temps de stockage est long, plus le module est élevé et plus la concentration est importante, plus le "vieillissement" est important.
Le verre à eau existant depuis longtemps peut être modifié de diverses manières pour éliminer le "vieillissement" et restaurer le verre à eau aux performances du verre à eau douce :
1. Modification physique
Le vieillissement du verre soluble est un processus spontané qui libère lentement de l'énergie. La modification physique du verre soluble "vieilli" consiste à utiliser un champ magnétique, des ultrasons, une haute fréquence ou un chauffage pour fournir de l'énergie au système de verre soluble et favoriser la haute polymérisation de la colle polysilicate. Les particules se re-dépolymérisent et favorisent l'homogénéisation de la masse moléculaire de l'acide polysilicique, éliminant ainsi le phénomène de vieillissement, mécanisme de modification physique. Par exemple, après traitement avec un champ magnétique, la force du sable de silicate de sodium est augmentée de 20-30%, la quantité de silicate de sodium ajoutée est réduite de 30-40%, le CO2 est économisé, la pliabilité est améliorée et il y a de bonnes bénéfices économiques.
L'inconvénient de la modification physique est qu'elle n'est pas durable et que la force de liaison diminue lorsqu'elle est stockée après le traitement, elle peut donc être utilisée dès que possible après le traitement en fonderie. Surtout pour le verre soluble avec M> 2.6, la concentration de molécules d'acide silicique est grande, et après modification physique et dépolymérisation, il se polycondensera relativement rapidement. Il est préférable de l'utiliser immédiatement après le traitement.
2. Modification chimique
La modification chimique consiste à ajouter une petite quantité de composés au verre soluble, ces composés contiennent tous des groupes carboxyle, amide, carbonyle, hydroxyle, éther, amino et autres groupes polaires, qui sont adsorbés sur des molécules d'acide silicique ou des particules colloïdales par des liaisons hydrogène ou statique électricité. Surface, modifie son énergie potentielle de surface et sa capacité de solvatation, améliore la stabilité de l'acide polysilicique, empêchant ainsi le "vieillissement" de se poursuivre.
Par exemple, l'ajout de polyacrylamide, d'amidon modifié, de polyphosphate, etc. au verre soluble peut obtenir de meilleurs résultats.
L'incorporation de matière organique dans du verre soluble ordinaire ou même du verre soluble modifié peut jouer diverses fonctions, telles que : changer les propriétés d'écoulement visqueux du verre soluble ; améliorer les performances de modélisation des mélanges de verre soluble ; augmenter la force de liaison pour rendre le verre d'eau absolument ajouté La quantité est réduite; la plasticité du gel d'acide silicique est améliorée ; la résistance résiduelle est réduite, de sorte que le sable de verre soluble convient mieux à la fonte et aux alliages non ferreux.
3. Modification physico-chimique
La modification physique convient au verre d'eau « vieilli » et peut être utilisé immédiatement après la modification. La modification chimique convient au traitement du verre d'eau douce et le verre d'eau modifié peut être stocké pendant une longue période. La combinaison d'une modification physique et d'une modification chimique peut faire en sorte que le verre d'eau ait un effet de modification durable. Par exemple, l'ajout de polyacrylamide à l'autoclave pour modifier le verre soluble "vieillissant" a un bon effet. Parmi elles, la pression et la pression de l'autoclave sont utilisées. L'agitation est une modification physique et l'ajout de polyacrylamide est une modification chimique.
2 Comment empêcher le soufflage de CO2 de farinage de surface de moule de sable de silicate de sodium durci (noyau)
Une fois que le sable de silicate de sodium soufflé est soufflé, durci au CO2 et laissé pendant un certain temps, parfois une substance comme du givre apparaîtra à la surface du moule inférieur (noyau), ce qui réduira considérablement la résistance de la surface de l'endroit et produira facilement du sable défauts de lavage lors de la coulée. Selon l'analyse, le composant principal de cette substance blanche est le NaHCO3, qui peut être causé par une humidité excessive ou du CO2 dans le sable de silicate de sodium. La réaction est la suivante :
NA2CO3 + H2O → NAHCO3 + NAOH
Na2O+2CO2+H2O→2NaHCO3
NaHCO3 migre facilement vers l'extérieur avec l'humidité, provoquant du givre pulvérulent à la surface du moule et du noyau.
La solution est la suivante:
1. Contrôlez la teneur en humidité du sable de silicate de sodium pour qu'elle ne soit pas trop élevée (surtout pendant la saison des pluies et l'hiver).
2. Le temps de soufflage du CO2 ne doit pas être trop long.
3. Le moule et le noyau durcis ne doivent pas être placés pendant une longue période et doivent être moulés et coulés à temps.
4. L'ajout d'environ 1% (fraction massique) du sirop d'une densité de 1.3 g/cm3 au sable de silicate de sodium peut empêcher efficacement la surface de se poudrer.
3 Comment améliorer la résistance à l'absorption d'humidité du moule à sable en verre soluble (noyau) ?
Le noyau de sable de verre d'eau de soude durci par CO2 ou par des méthodes de chauffage est assemblé dans le moule en argile humide. S'il n'est pas versé à temps, la résistance du noyau de sable diminuera fortement, non seulement pourra fluer, voire s'effondrer; il est stocké dans un environnement humide. La résistance du noyau de sable est également considérablement réduite. Le tableau 1 montre la valeur de résistance du noyau de sable de verre soluble au sodium durci au CO2 lorsqu'il est placé dans un environnement avec une humidité relative de 97% pendant 24 heures. La raison de la perte de résistance lorsqu'elle est stockée dans un environnement humide est due à la réhydratation du verre soluble sodique. Le Na+ et OH- dans la matrice de liant de silicate de sodium absorbent l'humidité et érodent la matrice, brisant finalement la liaison silicium-oxygène Si-O-Si, entraînant une diminution significative de la force de liaison du sable de silicate de sodium.
1. Du verre soluble au lithium est ajouté au verre soluble au sodium, ou Li2CO3, CaCO3, ZnCO3 et d'autres additifs inorganiques sont ajoutés au verre soluble au sodium, car des carbonates et des silicates relativement insolubles peuvent se former et les ions sodium libres peuvent être réduits Par conséquent, l'humidité la résistance à l'absorption du liant de verre soluble sodique peut être améliorée.
2. Ajoutez une petite quantité de matière organique ou de matière organique à fonction tensioactive dans le verre soluble au sodium. Lorsque le liant est durci, les ions hydrophiles Na+ et OH- dans le gel de verre soluble sodique peuvent être remplacés par des groupes hydrophobes organiques, ou Combinés les uns avec les autres, la base hydrophobe organique exposée améliore l'absorption d'humidité.
3. Améliorer le module du verre soluble, car la résistance à l'humidité du verre soluble à module élevé est plus forte que celle du verre soluble à faible module.
4. Ajouter l'hydrolysat d'amidon au sable de silicate de sodium. Une meilleure méthode consiste à utiliser de l'hydrolysat d'amidon pour modifier le verre soluble sodique.
4 Quelles sont les caractéristiques du procédé composite verre-résine phénolique alcaline-sable durci par soufflage de CO2 ?
Ces dernières années, afin d'améliorer la qualité des pièces moulées en acier, certaines petites et moyennes entreprises ont urgemment besoin d'adopter le procédé de sable de résine. Cependant, en raison de la capacité économique limitée, ils ne peuvent pas acheter d'équipement de régénération du sable de résine et le vieux sable ne peut pas être recyclé, ce qui entraîne des coûts de production élevés. Afin de trouver un moyen efficace d'améliorer la qualité des pièces moulées sans trop augmenter le coût, les caractéristiques de processus du sable de silicate de sodium durci soufflé au CO2 et du sable de résine phénolique alcaline durcie au CO2 peuvent être combinées, et du silicate de sodium durci au CO2 soufflé - alcalin la résine phénolique peut être utilisée. Le processus de mélange de sable de résine utilise du sable de résine phénolique alcalin comme sable de surface et du sable de verre soluble comme sable arrière, tout en soufflant du CO2 pour le durcissement.
La résine phénolique utilisée dans le sable de résine phénolique alcaline CO2 est fabriquée par polycondensation de phénol et de formaldéhyde sous l'action d'un catalyseur alcalin fort et en ajoutant un agent de couplage. Sa valeur PH est 13, et sa viscosité est ≤500mPa•s. La quantité de résine phénolique ajoutée au sable est de 3 à 4 % (fraction massique). Lorsque le débit de CO2 est de 0.8 à 1.0 m3/h, le meilleur temps de soufflage est de 30 à 60 s ; si le temps de soufflage est trop court, la résistance au durcissement du noyau de sable sera faible ; si le temps de soufflage est trop long, la résistance du noyau de sable n'augmentera pas et c'est du gaz gaspillé.
CO2 - Le sable de résine phénolique alcaline ne contient pas d'éléments nocifs tels que N, P, S, etc., de sorte que les défauts de coulée tels que les pores, les microfissures de surface, etc. causés par ces éléments sont éliminés ; les gaz nocifs tels que le H2S et le SO2 ne sont pas libérés lors de la coulée, ce qui est bénéfique pour la protection de l'environnement ; Bonne pliabilité, facile à nettoyer; haute précision dimensionnelle; haute efficacité de production.
Le procédé composite de sable de résine phénolique alcaline verre-eau durci par soufflage de CO2 peut être largement utilisé dans les moulages d'acier, les moulages de fer, les alliages de cuivre et les moulages d'alliages légers.
Le procédé composite est un procédé simple et pratique. Le processus est le suivant : mélangez d'abord le sable de résine et le sable de silicate de sodium séparément, puis mettez-les dans deux seaux de sable ; puis ajoutez le sable de résine mélangé comme sable de surface dans le bac à sable Et livrez, l'épaisseur de la couche de sable de surface est généralement de 30 à 50 mm; puis du sable de verre soluble est ajouté pour rendre le sable arrière à remplir et à compacter; enfin, du gaz CO2 est soufflé dans le moule pour le durcissement.
Le diamètre du tube de soufflage est généralement de 25 mm et la plage de durcissement est d'environ 6 fois le diamètre du tube de soufflage.
Le temps de soufflage dépend de la taille, de la forme, du débit de gaz et de la surface du bouchon d'échappement du moule en sable (noyau). Généralement, le temps de soufflage est contrôlé dans les 15 ~ 40 s.
Après avoir soufflé le moule en sable dur (noyau), le moule peut être pris. La résistance du moule en sable (noyau) augmente rapidement. Badigeonner la peinture dans la demi-heure après avoir pris le moule, et refermer la boîte pour verser au bout de 4 heures.
Le procédé composite est particulièrement adapté aux usines de moulage d'acier qui ne disposent pas d'équipement de régénération de sable de résine et doivent produire des moulages de haute qualité. Le processus est simple et facile à contrôler, et la qualité des moulages produits est équivalente à celle des autres moulages en sable de résine.
Le sable de silicate de sodium durci par soufflage de CO2 peut également être mélangé avec du sable de résine de polyacrylate de sodium durci par soufflage de CO2 pour la production de diverses pièces moulées de haute qualité.
5 Quels sont les avantages et les inconvénients du procédé de sable de silicate de sodium durci composite CO2-ester organique ?
Ces dernières années, le procédé de sable de silicate de sodium durci composite CO2-ester organique a eu tendance à étendre ses applications. Le processus est le suivant : ajouter une certaine quantité d'ester organique pendant le mélange du sable (généralement la moitié de la quantité normale requise ou 4 à 6 % du poids du verre soluble); une fois la modélisation terminée, soufflez du CO2 pour durcir à la résistance au démoulage (une résistance à la compression est généralement requise) La résistance est d'environ 0.5 MPa); après le démoulage, l'ester organique continue de durcir et la résistance du sable de moulage augmente plus rapidement ; une fois le CO2 soufflé et placé pendant 3 à 6 heures, le moule en sable peut être combiné et versé.
Le mécanisme de durcissement est :
Lorsque le sable de verre soluble souffle du CO2, sous l'action de la différence de pression du gaz et de la différence de concentration, le gaz CO2 essaiera de s'écouler dans toutes les directions du sable de moulage. Après que le gaz CO2 entre en contact avec le verre d'eau, il réagit immédiatement avec lui pour former un gel. En raison de l'effet de diffusion, la réaction se fait toujours de l'extérieur vers l'intérieur, et la couche externe forme d'abord un film de gel, ce qui empêche le gaz CO2 et le verre soluble de continuer à réagir. Par conséquent, en peu de temps, quelle que soit la méthode utilisée pour contrôler le gaz CO2, il est impossible de le faire réagir avec tout le verre soluble. Selon l'analyse, lorsque le sable de moulage atteint la meilleure résistance au soufflage, le verre soluble ayant réagi avec le gaz CO2 est d'environ 65%. Cela signifie que le verre soluble n'exerce pas pleinement son effet de liaison et qu'au moins 35 % du verre soluble ne réagit pas. Le durcisseur ester organique peut former un mélange uniforme avec le liant, et peut donner plein jeu à l'effet de liaison du liant. Toutes les parties du noyau de sable acquièrent de la résistance à la même vitesse.
L'augmentation de la quantité de verre soluble ajoutée augmentera la résistance finale du moule en sable, mais sa résistance résiduelle augmentera également, ce qui rendra difficile le nettoyage du sable. Lorsque la quantité ajoutée de verre soluble est trop faible, la résistance finale est trop faible et ne peut pas répondre aux exigences d'utilisation. Dans la production réelle, la quantité de verre soluble ajoutée est généralement contrôlée à environ 4 %.
Lors de l'utilisation d'ester organique seul pour durcir, la quantité générale d'ester organique ajoutée est de 8 à 15 % de la quantité de verre soluble. Lors de l'utilisation du durcissement composite, on estime qu'environ la moitié du verre soluble a été durci lorsque le CO2 est soufflé, et qu'environ la moitié du verre soluble n'a pas encore durci. Par conséquent, il est plus approprié que la quantité d'esters organiques représente 4 à 6 % de la quantité de verre soluble.
La méthode de durcissement composite peut tirer pleinement parti des doubles avantages du durcissement au CO2 et du durcissement des esters organiques, et peut pleinement exercer l'effet de liaison du verre soluble pour obtenir une vitesse de durcissement rapide, un démoulage précoce, une résistance élevée, une bonne pliabilité et un faible coût. Effet global.
Cependant, le processus de durcissement composite CO2-ester organique doit ajouter 0.5 à 1% de verre soluble en plus que la méthode de durcissement simple ester organique, ce qui augmentera la difficulté de la régénération du sable de verre soluble utilisé.
6 Pourquoi est-il facile de produire du sable collant lorsque le procédé de sable au silicate de sodium est utilisé pour produire des pièces moulées en fonte ? Comment l'empêcher?
Lorsque le moule en sable (noyau) en sable de silicate de sodium est utilisé pour couler des pièces moulées en fonte, un sable collant important est souvent produit, ce qui limite son application dans la production de fonte.
Le Na2O, le SiO2 dans le sable de silicate de sodium et l'oxyde de fer produit par le métal liquide pendant la coulée forment un silicate à bas point de fusion. Comme mentionné précédemment, si ce composé contient plus de verre amorphe fusible, la force de liaison entre cette couche de verre et la surface de la pièce moulée est très faible, et le coefficient de retrait est différent de celui du métal. Les contraintes importantes sont faciles à éliminer de la surface de la pièce moulée sans que le sable ne colle. Si le composé formé à la surface de la coulée a une teneur élevée en SiO2 et une faible teneur en FeO, MnO, etc., sa structure solidifiée a essentiellement une structure cristalline, qui sera fermement combinée avec la coulée, ce qui donnera un sable collant .
Lorsque le sable de silicate de sodium est utilisé pour produire des pièces moulées en fer, en raison de la faible température de coulée et de la teneur élevée en carbone des pièces moulées en fer, le fer et le manganèse ne sont pas facilement oxydés, et la couche de sable collante résultante a une structure cristalline, et il est difficile pour établir une couche appropriée entre les moulages de fer et la couche de sable collant. L'épaisseur de la couche d'oxyde de fer est différente de celle du sable de résine entre le moulage et la couche de sable collant, qui peut produire un film de carbone brillant par pyrolyse de résine lors de la production de moulages de fer, de sorte que la couche de sable collant n'est pas facile à enlever.
Afin d'empêcher la production de sable de verre soluble à partir de la production de pièces moulées en fonte, des revêtements appropriés peuvent être utilisés. Comme la peinture à base d'eau, la surface doit être séchée après la peinture, donc la peinture à séchage rapide à base d'alcool est la meilleure.
En général, les pièces moulées en fonte peuvent également ajouter une quantité appropriée de poudre de charbon (telle que 3% à 6%) (fraction massique) au sable de silicate de sodium, de sorte que la pyrolyse de la poudre de charbon entre la coulée et la couche de sable puisse produire un film de carbone brillant. Il n'est pas mouillé par les métaux et leurs oxydes, de sorte que la couche de sable collante se décolle facilement de la pièce moulée.
7 Le sable de silicate de sodium devrait-il devenir un sable de moulage respectueux de l'environnement sans rejet de sable résiduel ?
Le verre à eau est incolore, inodore et non toxique. Il ne causera pas de problèmes graves s'il touche la peau et les vêtements et se rince à l'eau, mais il faut éviter les éclaboussures dans les yeux. Le verre soluble n'a pas de gaz irritants ou nocifs libérés lors du mélange, du modelage, du durcissement et du coulage du sable, et il n'y a pas de pollution noire et acide. Cependant, si le processus est incorrect et que trop de silicate de sodium est ajouté, la capacité de pliage du sable de silicate de sodium ne sera pas bonne et la poussière s'envolera pendant le nettoyage du sable, ce qui entraînera également une pollution. Dans le même temps, il est difficile de régénérer le vieux sable et le rejet de sable résiduel provoque une pollution alcaline de l'environnement.
Si ces deux problèmes peuvent être surmontés, le sable de silicate de sodium peut devenir un sable de moulage respectueux de l'environnement sans pratiquement aucun rejet de sable résiduel.
La mesure fondamentale pour résoudre ces deux problèmes est de réduire la quantité de verre soluble ajoutée à moins de 2%, ce qui peut essentiellement secouer le sable. Lorsque la quantité de verre soluble ajoutée est réduite, le Na2O résiduel dans le vieux sable est également réduit. En utilisant une méthode de régénération sèche relativement simple, il est possible de maintenir le Na2O résiduel dans le sable en circulation en dessous de 0.25%. Ce sable récupéré peut répondre aux exigences d'application du sable de moulage unique pour les pièces moulées en acier de petite et moyenne taille. À l'heure actuelle, même si l'ancien sable de silicate de sodium n'utilise pas la méthode humide coûteuse et compliquée pour se régénérer, mais la méthode sèche relativement simple et bon marché est utilisée, il peut être entièrement recyclé, fondamentalement aucun sable résiduel n'est déchargé, et le rapport de sable au fer Il peut être réduit à moins de 1:1.
8 Comment régénérer efficacement le sable de silicate de sodium ?
Si le Na2O résiduel dans l'ancien sable de silicate de sodium est trop élevé, après avoir ajouté le silicate de sodium au sable, le sable de moulage n'aura pas assez de temps utilisable, et l'accumulation de trop de Na2O détériorera le caractère réfractaire du sable de quartz. Par conséquent, le Na2O résiduel doit être éliminé autant que possible lors de la régénération du sable de silicate de sodium utilisé.
Veuillez conserver la source et l'adresse de cet article pour réimpression:Plusieurs problèmes auxquels il faut prêter attention dans la coulée de sable de silicate de sodium
Minghé Société de moulage sous pression sont dédiés à la fabrication et à la fourniture de pièces de moulage de qualité et de haute performance (la gamme de pièces de moulage sous pression en métal comprend principalement Moulage sous pression à paroi mince,Chambre chaude coulée sous pression,Chambre froide coulée sous pression), Service rond (Service de moulage sous pression,Usinage CNC,Fabrication de moules,Traitement de surface). Tout moulage sous pression en aluminium personnalisé, moulage sous pression en magnésium ou en zamak/zinc et autres exigences en matière de moulages sont invités à nous contacter.
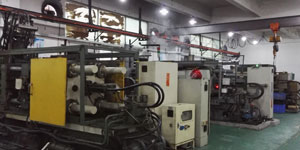
Sous le contrôle des normes ISO9001 et TS 16949, tous les processus sont effectués via des centaines de machines de moulage sous pression avancées, de machines à 5 axes et d'autres installations, allant des blasters aux machines à laver Ultra Sonic.Minghe dispose non seulement d'équipements de pointe, mais également de professionnels équipe d'ingénieurs, d'opérateurs et d'inspecteurs expérimentés pour réaliser la conception du client.
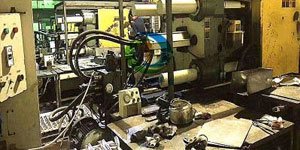
Fabricant sous contrat de moulages sous pression. Les capacités incluent des pièces de moulage sous pression en aluminium à chambre froide à partir de 0.15 lb. jusqu'à 6 lb, configuration à changement rapide et usinage. Les services à valeur ajoutée comprennent le polissage, la vibration, l'ébavurage, le grenaillage, la peinture, le placage, le revêtement, l'assemblage et l'outillage. Les matériaux travaillés comprennent des alliages tels que 360, 380, 383 et 413.
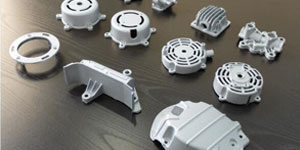
Assistance à la conception de moulage sous pression de zinc/services d'ingénierie simultanés. Fabricant sur mesure de pièces moulées en zinc de précision. Des moulages miniatures, des moulages sous pression à haute pression, des moulages en moules à glissières multiples, des moulages en moules conventionnels, des moulages sous pression unitaires et indépendants et des moulages à cavité scellée peuvent être fabriqués. Les pièces moulées peuvent être fabriquées dans des longueurs et des largeurs allant jusqu'à 24 po avec une tolérance de +/- 0.0005 po.
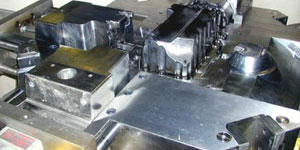
Fabricant certifié ISO 9001 : 2015 de magnésium moulé sous pression, les capacités incluent le moulage sous pression de magnésium sous pression jusqu'à une chambre chaude de 200 tonnes et une chambre froide de 3000 tonnes, la conception d'outillage, le polissage, le moulage, l'usinage, la peinture en poudre et liquide, une assurance qualité complète avec des capacités CMM , assemblage, emballage et livraison.
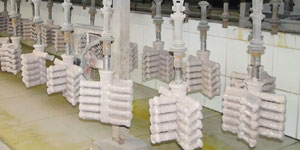
Certifié ITAF16949. Service de casting supplémentaire inclus coulée d'investissement,moulage en sable,Coulée par gravité, Coulée de mousse perdue,Coulée centrifuge,Coulée sous vide,Moulage de moule permanentLes capacités comprennent l'EDI, l'assistance technique, la modélisation solide et le traitement secondaire.
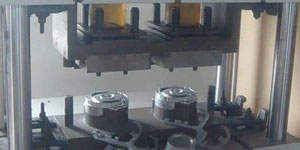
Industries de moulage Études de cas de pièces pour : voitures, vélos, avions, instruments de musique, motomarines, appareils optiques, capteurs, modèles, appareils électroniques, boîtiers, horloges, machines, moteurs, meubles, bijoux, gabarits, télécommunications, éclairage, appareils médicaux, appareils photographiques, Robots, Sculptures, Équipement de sonorisation, Équipement de sport, Outillage, Jouets et plus encore.
Que pouvons-nous vous aider à faire ensuite ?
∇ Aller à la page d'accueil pour Moulage sous pression Chine
→Pièces de fonderie-Découvrez ce que nous avons fait.
→Conseils à propos de Services de moulage sous pression
By Fabricant de moulage sous pression Minghe |Catégories : Articles utiles |Matières Mots clés: Moulage d'aluminium, Moulage de zinc, Coulée de magnésium, Moulage de titane, Fonderie en acier inoxydable, Coulée de laiton,Coulée de bronze,Vidéo de casting,Historique de l'entreprise,Moulage sous pression en aluminium |Commentaires fermés