Divers facteurs affectant la stabilité dimensionnelle des moulages de précision
L'amélioration continue de la précision dimensionnelle des moulages de précision et la réduction des déchets causés par les surdimensionnements ont toujours été l'un des principaux objectifs poursuivis par les travailleurs du moulage de précision au pays et à l'étranger.
1. Stabilité dimensionnelle des moulages de précision
1. Stabilité dimensionnelle du modèle en cire et ses facteurs d'influence
Dans la plupart des cas, la taille du moule en cire fluctue considérablement lorsque la taille du moulage fluctue, et il y a quelques exceptions. Dans l'ensemble, la fluctuation de taille du moule en cire représente 10 à 70 % de la fluctuation de taille de la pièce moulée.
Les paramètres du processus de moulage ont une influence décisive sur la stabilité dimensionnelle du moule en cire. Les principaux facteurs sont les suivants :
(1) Température de pressage de la cire
Différents matériaux de moulage ont des performances différentes en raison de l'influence de la température de pressage de la cire. Lorsque des matériaux de moulage à base de cire sont utilisés, la température de pressage de la cire est très sensible à l'influence de la stabilité dimensionnelle du moule en cire, tandis que les matériaux de moulage à base de résine ont moins d'influence.
(2) Pression d'injection
Lorsque la pression est faible, le taux de retrait du moule en cire diminue considérablement lorsque la pression augmente. Cependant, une fois la pression augmentée dans une certaine mesure (≥ 1.6 MPa), la pression n'a pratiquement aucun effet sur la taille du moule en cire. Il n'est pas étonnant que les résultats des tests étrangers concluent souvent que "la pression n'a rien à voir avec la taille du moule en cire", mais l'impression de nombreuses entreprises nationales n'est pas tout à fait la même.
(3) Débit
Le débit du matériau du moule peut être modifié des deux manières suivantes, mais l'influence sur la taille du moule en cire n'est pas la même :
·En modifiant le réglage de la vitesse d'écoulement de la presse à cire, cette méthode a peu d'effet sur le rétrécissement du moule en cire. Cependant, il a une influence importante sur le remplissage et la qualité de surface des pièces à parois minces aux formes complexes ou des moules en cire avec noyaux.
·Cette méthode a une grande influence en modifiant la section transversale du port d'injection de cire, car l'augmentation de la section transversale du port d'injection de cire peut non seulement réduire la température de pressage de la cire, mais également prolonger la solidification temps du matériau du moule au niveau de l'orifice d'injection de cire, augmentant ainsi le compactage du moule en cire Le degré de retrait et le retrait de surface sont réduits.
(4) Temps d'injection
Le temps dite d'injection comprend ici trois périodes de temps de remplissage, de compactage et de maintien. Le temps de remplissage fait référence au temps nécessaire au matériau de moulage pour remplir la cavité de moulage ; le compactage fait référence au temps écoulé entre le remplissage du moulage et la fermeture de la buse d'injection de cire ; et le maintien fait référence au temps écoulé entre la fermeture de la buse d'injection de cire et l'éjection du moule.
Le temps d'injection a un effet significatif sur le taux de retrait du moule en cire. En effet, plus de matériau de moule peut être pressé dans la cavité en augmentant le temps d'injection, et le moule en cire sera plus compacté, réduisant ainsi le taux de retrait. Le poids du modèle en cire augmente avec le temps de compactage prolongé. Le temps de compactage doit être approprié. Si le temps de compactage est trop long, le matériau du moule au niveau de l'orifice d'injection de cire s'est complètement solidifié et le compactage ne fonctionnera pas. On peut également voir sur la figure 4 que lorsque le temps d'injection est court (15-25 s), la température de pressage de la cire augmente et le taux de retrait augmente ; mais lorsque le temps d'injection est étendu à 25-35s (sous l'hypothèse que le temps de remplissage reste constant, le réel ci-dessus est d'étendre le temps de compactage) L'influence de la température de pressage de la cire devient plus petite; lorsque le temps d'injection augmente à plus de 35 s, la situation inverse se produira, c'est-à-dire que lorsque la température de pressage de la cire augmente, le taux de retrait du moule en cire diminuera à la place. Ce phénomène peut s'expliquer par le fait que l'augmentation de la température du matériau du moule et l'allongement du temps de compactage ont le même effet que l'augmentation du degré de compactage du moule en cire.
(5) température de moulage et équipement de pressage de cire
La température de moulage est élevée, le moule en cire se refroidit lentement et le taux de retrait augmente. En effet, le moule en cire est toujours dans le moulage par compression avant que le moule ne soit éjecté et le retrait est limité, mais une fois le moule éjecté, il devient libre de se rétracter. Par conséquent, si la température du moule en cire est élevée lorsque le moule est libéré, le taux de retrait final sera important et vice versa, le taux de retrait sera faible.
De la même manière, le système de refroidissement de la presse à cire peut avoir un impact d'environ 0.3% sur la taille du moule à cire.
Enfin, il convient de souligner que lors de l'utilisation de matériaux de moulage à base de cire, la pâte de cire est un système de coexistence à trois phases de solide, liquide et gaz. Le rapport volumique entre les trois phases a une grande influence sur la taille du moule en cire. La relation proportionnelle entre ces trois éléments ne peut pas être contrôlée dans la production réelle, ce qui est également une raison importante de la mauvaise stabilité dimensionnelle des moules en cire utilisant des matériaux de moulage à base de cire.
2. L'influence du matériau de la coque et du processus de fabrication de la coque sur la stabilité dimensionnelle des pièces moulées
L'influence de la coquille du moule sur la taille de la pièce moulée est principalement causée par la dilatation thermique et la déformation thermique (fluage à haute température) de la coquille du moule pendant la cuisson, et la restriction (obstruction) de la coquille du moule sur le retrait de refroidissement de la fonderie.
(1) Dilatation thermique de la coque
Dépend principalement du matériau de la coque. Différents matériaux réfractaires ont des taux d'expansion différents. Parmi les réfractaires couramment utilisés, la silice fondue a le taux d'expansion le plus faible, suivi du silicate d'aluminium, et la silice est la plus grande et inégale. Après les tests, il est déterminé que la coque en silicate d'aluminium peut être chauffée de la température ambiante à 1000 ℃, la coque peut produire une expansion d'environ 0.25%, ce qui représente une petite proportion du retrait global de la taille de la coulée. Par conséquent, si de tels matériaux réfractaires sont utilisés, la coque Il a une meilleure stabilité dimensionnelle, telle que la silice fondue, sera sans aucun doute meilleure. Cependant, si de la silice est utilisée, la taille de l'enveloppe fluctue considérablement.
(2) Déformation thermique (fluage à haute température)
Par exemple, une coque utilisant du verre soluble comme liant a un degré de fluage significativement plus élevé à des températures élevées supérieures à 1000°C que celui des coques de sol de silice et de silicate d'éthyle. Bien que le corindon fondu lui-même ait une réfractarité élevée, en raison de la présence d'impuretés telles que l'oxyde de sodium, la température de cuisson de la coque supérieure à 1000 ℃ peut également provoquer un fluage, entraînant une mauvaise stabilité dimensionnelle.
(3) La retenue de la coquille du moule sur le retrait de la pièce moulée - le retrait et l'affaissement de la coquille du moule Cela dépend aussi principalement du matériau de la coquille du moule.
En résumé, les matériaux réfractaires jouent un rôle majeur dans l'influence de l'enveloppe sur la fluctuation de taille de la coulée, mais le rôle du liant ne peut être ignoré. En revanche, l'impact du processus de fabrication de la coquille est faible.
3. L'influence des contraintes causées par un refroidissement inégal des pièces moulées sur la stabilité dimensionnelle
La vitesse de refroidissement de chaque partie de la pièce moulée (y compris le système d'injection) est différente, ce qui génère des contraintes thermiques et déforme la pièce moulée, affectant ainsi la stabilité dimensionnelle. Ceci est souvent rencontré dans la production réelle. La réduction de la vitesse de refroidissement des pièces moulées et l'amélioration de la combinaison des canaux sont des mesures préventives efficaces.
2. La clé pour améliorer la précision du taux de retrait du moule est attribuée correctement
La "stabilité dimensionnelle" mentionnée ci-dessus est différente de la "précision dimensionnelle" et de la "précision (précision)". La stabilité dimensionnelle (c'est-à-dire la précision) est synonyme de cohérence dimensionnelle, reflétant le degré de fluctuation ou de dispersion dimensionnelle, et est généralement mesurée par l'écart type σ. La principale cause d'instabilité dimensionnelle est un contrôle de processus laxiste, qui est une erreur aléatoire. La précision fait référence au degré auquel la moyenne arithmétique de nombreuses valeurs mesurées s'écarte de la taille nominale pour une certaine taille sur le moulage, c'est-à-dire la taille de l'écart moyen. Pour la coulée de précision, la raison principale de la faible précision dimensionnelle est l'affectation incorrecte du taux de retrait lors de la conception du profilage, ce qui est une erreur systématique, qui est généralement ajustée en réparant à plusieurs reprises le moule. La précision dimensionnelle (précision) est une combinaison des deux ci-dessus. Par conséquent, pour améliorer la précision dimensionnelle des pièces moulées et résoudre le problème des tolérances de taille du produit, non seulement le processus doit être strictement contrôlé pour réduire les fluctuations dimensionnelles, mais également le taux de retrait de chaque dimension de la pièce moulée doit être correctement attribué lors de la conception du profil. .
Il est bien connu que le retrait total final des pièces moulées de précision est une combinaison de moule en cire, de retrait d'alliage et d'une petite quantité d'expansion de la coque. La coquille gonfle d'environ 0.25% et son effet est limité. Bien que le taux de retrait linéaire de l'alliage soit souvent supérieur à celui du moule en cire, la fluctuation dimensionnelle provoquée par le processus de pressage de la cire a un impact plus important. Afin de réduire le coût de réparation du moule et de réduire la fluctuation de la taille de la coulée, il est très important de contrôler le taux de retrait du moule en cire.
1. Rétrécissement de moule de cire
Le retrait du moule en cire doit être mesuré une fois que la taille du moule en cire est complètement stabilisée. En effet, le retrait du moule en cire ne s'arrête pas complètement après l'éjection du moule. La taille du moule en cire se stabilise parfois seulement quelques jours après l'éjection du moule. Cependant, la plus grande partie du rétrécissement du matériau du moule est pratiquement terminée en une à plusieurs heures après l'éjection du moule. Le taux de retrait du moule en cire a principalement les facteurs d'influence suivants :
(1) Type de matériau du moule ;
(2) Taille en coupe du modèle en cire ;
Il convient de souligner que la taille de la section transversale du moule en cire a un effet significatif sur le taux de retrait. Par exemple, le taux de retrait d'un matériau de moule non rempli typique lors du pressage de moules en cire de différentes épaisseurs. L'épaisseur de la section du moule en cire ne doit généralement pas dépasser 13 mm. Lorsque l'épaisseur est supérieure à 13 mm, l'épaisseur de la paroi peut être réduite en utilisant des blocs de cire froide ou des noyaux métalliques pour atteindre l'objectif de réduire le retrait, ce qui est particulièrement important pour les matériaux de moule sans remplissage.
Remarque : 1. Le taux de retrait du matériau de moule soluble dans l'eau est d'environ 0.25 % ;
2. Lors de l'utilisation de noyaux solubles, de noyaux en céramique ou de tubes en verre de quartz, il n'y a pas de retrait linéaire du moule en cire en contact avec le noyau ;
(3) Types de noyau
La taille de la cavité du moule en cire est sans aucun doute cohérente avec la forme du noyau. Par conséquent, l'utilisation de noyaux est devenue un moyen d'améliorer la précision dimensionnelle de la cavité du moule en cire.
2. retrait de l'alliage
Le retrait de l'alliage dépend principalement des facteurs suivants :
· Type d'alliage coulé et composition chimique;
· Géométrie de moulage (y compris l'état de contrainte et la taille de la section);
· Paramètres de coulée, tels que la température de coulée, la température de la coque, la vitesse de refroidissement de la coulée, etc. ;
· Utilisation de noyaux en céramique, de tubes en verre de quartz, etc.
Étant donné que la température de coulée, la température de la coque, la vitesse de refroidissement de la coulée et d'autres paramètres de processus sont généralement strictement contrôlés par des cartes de processus standard pendant le processus de production, les fluctuations de taille causées par cela ne sont pas importantes entre les différents lots de production. Même si la température de coulée dépasse la plage requise par les spécifications du procédé, la fluctuation de la taille de coulée n'est généralement pas importante. Comme pour le moule en cire, la taille de la section de la coulée et les contraintes de la coquille du moule sont les principaux facteurs qui affectent le retrait de l'alliage. L'expérience montre que le taux de retrait de la taille entièrement contrainte est de 85 % à 89 % du taux de retrait libre ; la taille semi-contrainte est de 94% à 95%.
3. Le nombre minimum du premier lot d'échantillons à mesurer
Le taux de retrait indiqué ci-dessus est une donnée empirique basée sur l'expérience passée, et non le taux de retrait réel. Concevoir et fabriquer des moules selon ces données, la réparation est inévitable. Afin d'améliorer la précision et le taux de réussite des réparations, et de réduire le nombre de réparations, un lien clé consiste à vérifier soigneusement la taille d'un nombre suffisant d'échantillons de moulage d'essai. Parce que la taille des pièces moulées que nous produisons ne peut pas être exactement la même, donc seulement lorsque le nombre d'échantillons mesurés est suffisamment grand, la valeur moyenne obtenue peut être proche de la vraie moyenne arithmétique. À partir de là, il n'est pas difficile de voir que le nombre minimum d'échantillons de mesure est directement lié à la capacité du processus de production à contrôler la cohérence de la taille du produit (Capacité du processus). Si les pièces moulées sont complètement de la même taille, alors un seul échantillon doit être testé ; Inversement, si la taille de coulée fluctue fortement,
Il est nécessaire de mesurer un grand nombre d'échantillons pour obtenir des données de retrait plus précises. Comme mentionné précédemment, la capacité du processus de production à contrôler la taille peut être représentée par les 6 de la taille de coulée produite par ce processus. Du niveau technologique actuel de la plupart des fonderies d'investissement, Hp est généralement supérieur à 0.5, de sorte que le premier lot d'échantillons de mesure nécessite généralement au moins 11 échantillons.
Trois. Analyse du système de mesure
Lors de l'analyse et de la résolution de problèmes de taille de produit, nous devons prêter attention à la précision et à la fiabilité du système de mesure utilisé. En plus de l'étalonnage fréquent des instruments et équipements de mesure eux-mêmes, il est également important de minimiser les erreurs de mesure. Si le système de mesure (y compris l'opérateur et la méthode de fonctionnement) comporte une erreur importante, non seulement les rejets peuvent être jugés comme des produits qualifiés, mais également de nombreux produits qualifiés peuvent être mal évalués comme des rejets, ce qui peut provoquer des accidents majeurs ou des coûts économiques inutiles pertes. Le moyen le plus simple de déterminer si un système de mesure est adapté à une tâche de mesure spécifique est d'effectuer des tests de qualification de reproductibilité et de répétabilité. La répétabilité signifie que le même inspecteur utilise le même instrument (ou équipement) et la même méthode pour inspecter la même pièce et obtenir la cohérence des résultats. La reproductibilité fait référence à la cohérence des résultats obtenus par différents opérateurs utilisant différents instruments pour vérifier la même pièce. L'American Automotive Industry Action Group (Automotive Industry Action Group) stipule que le pourcentage de l'écart-type intégré de la répétabilité et de la reproductibilité R&R dans l'écart-type des fluctuations de taille de moulage mesurées est ≤30 % comme norme pour que le système de mesure réponde aux exigences [5]. Lors de la mesure de certaines pièces moulées de grande taille et de forme complexe, tous les systèmes de mesure ne peuvent pas répondre à cette exigence. L'erreur de mesure admissible lors de la mesure des moules doit être plus petite, généralement 1/3.
quatre. Structure du moule et niveau de traitement
Il est bien connu que la structure du moule et la qualité du traitement ont une influence importante sur la taille et la géométrie du moule en cire. Par exemple, si le mécanisme de positionnement et de serrage est précis et fiable, si le jeu correspondant des pièces mobiles (telles que les blocs mobiles, les boulons, etc.) est approprié, si la méthode d'étirage est bénéfique pour assurer la précision dimensionnelle des pièces moulées , etc. Il va sans dire que pour un nombre considérable d'usines nationales de moulage de précision, le niveau de conception et de fabrication des moules doit encore être amélioré de toute urgence.
Cinq. en conclusion
D'après l'analyse ci-dessus, il n'est pas difficile de voir que l'amélioration de la précision dimensionnelle des moulages de précision est un projet systématique impliquant tous les aspects du processus de production de moulage de précision. Les principaux points peuvent être résumés comme suit :
1) Contrôler strictement les paramètres du processus de moulage, en particulier les paramètres qui ont un impact significatif sur la taille de la pièce moulée.
2) Choisissez le matériau de coque approprié.
3) Recueillir, compter et analyser les données liées au retrait selon une méthode correcte conforme aux principes statistiques afin d'améliorer la précision de l'attribution du retrait.
4) Surveiller fréquemment le système de mesure (y compris l'équipement, le personnel d'inspection et la technologie) pour s'assurer que les erreurs de répétabilité et de reproductibilité répondent aux exigences spécifiées.
5) Améliorer continuellement le niveau de conception et de fabrication des moules.
6) Des mesures telles que la correction de coulée et le traitement thermique de stabilisation sont toujours indispensables dans de nombreuses occasions
Veuillez conserver la source et l'adresse de cet article pour réimpression: Divers facteurs affectant la stabilité dimensionnelle des moulages de précision
Minghé Société de moulage sous pression sont dédiés à la fabrication et à la fourniture de pièces de moulage de qualité et de haute performance (la gamme de pièces de moulage sous pression en métal comprend principalement Moulage sous pression à paroi mince,Chambre chaude coulée sous pression,Chambre froide coulée sous pression), Service rond (Service de moulage sous pression,Usinage CNC,Fabrication de moules,Traitement de surface). Tout moulage sous pression en aluminium personnalisé, moulage sous pression en magnésium ou en zamak/zinc et autres exigences en matière de moulages sont invités à nous contacter.
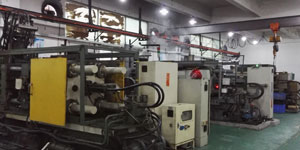
Sous le contrôle des normes ISO9001 et TS 16949, tous les processus sont effectués via des centaines de machines de moulage sous pression avancées, de machines à 5 axes et d'autres installations, allant des blasters aux machines à laver Ultra Sonic.Minghe dispose non seulement d'équipements de pointe, mais également de professionnels équipe d'ingénieurs, d'opérateurs et d'inspecteurs expérimentés pour réaliser la conception du client.
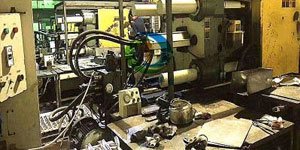
Fabricant sous contrat de moulages sous pression. Les capacités incluent des pièces de moulage sous pression en aluminium à chambre froide à partir de 0.15 lb. jusqu'à 6 lb, configuration à changement rapide et usinage. Les services à valeur ajoutée comprennent le polissage, la vibration, l'ébavurage, le grenaillage, la peinture, le placage, le revêtement, l'assemblage et l'outillage. Les matériaux travaillés comprennent des alliages tels que 360, 380, 383 et 413.
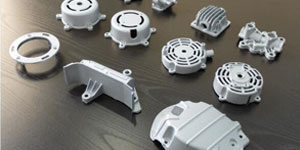
Assistance à la conception de moulage sous pression de zinc/services d'ingénierie simultanés. Fabricant sur mesure de pièces moulées en zinc de précision. Des moulages miniatures, des moulages sous pression à haute pression, des moulages en moules à glissières multiples, des moulages en moules conventionnels, des moulages sous pression unitaires et indépendants et des moulages à cavité scellée peuvent être fabriqués. Les pièces moulées peuvent être fabriquées dans des longueurs et des largeurs allant jusqu'à 24 po avec une tolérance de +/- 0.0005 po.
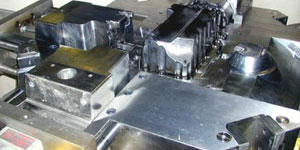
Fabricant certifié ISO 9001 : 2015 de magnésium moulé sous pression, les capacités incluent le moulage sous pression de magnésium sous pression jusqu'à une chambre chaude de 200 tonnes et une chambre froide de 3000 tonnes, la conception d'outillage, le polissage, le moulage, l'usinage, la peinture en poudre et liquide, une assurance qualité complète avec des capacités CMM , assemblage, emballage et livraison.
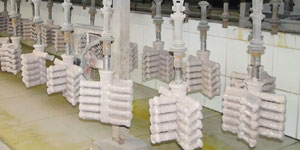
Certifié ITAF16949. Service de casting supplémentaire inclus coulée d'investissement,moulage en sable,Coulée par gravité, Coulée de mousse perdue,Coulée centrifuge,Coulée sous vide,Moulage de moule permanentLes capacités comprennent l'EDI, l'assistance technique, la modélisation solide et le traitement secondaire.
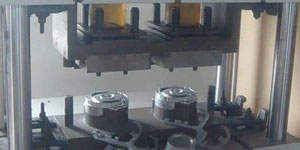
Industries de moulage Études de cas de pièces pour : voitures, vélos, avions, instruments de musique, motomarines, appareils optiques, capteurs, modèles, appareils électroniques, boîtiers, horloges, machines, moteurs, meubles, bijoux, gabarits, télécommunications, éclairage, appareils médicaux, appareils photographiques, Robots, Sculptures, Équipement de sonorisation, Équipement de sport, Outillage, Jouets et plus encore.
Que pouvons-nous vous aider à faire ensuite ?
∇ Aller à la page d'accueil pour Moulage sous pression Chine
→Pièces de fonderie-Découvrez ce que nous avons fait.
→Conseils à propos de Services de moulage sous pression
By Fabricant de moulage sous pression Minghe |Catégories : Articles utiles |Matières Mots clés: Moulage d'aluminium, Moulage de zinc, Coulée de magnésium, Moulage de titane, Fonderie en acier inoxydable, Coulée de laiton,Coulée de bronze,Vidéo de casting,Historique de l'entreprise,Moulage sous pression en aluminium |Commentaires fermés