La fonte et le traitement de l'ADC12
1. Les caractéristiques de base de l'alliage d'aluminium
L'alliage aluminium-silicium Japon ADCI2 a de bonnes performances de moulage, et le moulage a une résistance élevée, un faible coefficient de dilatation thermique, une résistance élevée à la corrosion et de bonnes performances d'écaillage. Par conséquent, il est largement utilisé dans la production de carburateurs automobiles, de blocs-cylindres, de culasses et de réducteurs de locomotive.
Vibrateurs, boîtes de vitesses de moteurs, boîtes de vitesses de machines agricoles, boîtiers de caméras, boîtiers d'outils électriques et autres pièces. Ces dernières années, avec le développement rapide des industries de l'automobile et de la moto, ils ont été plus largement utilisés dans la production de boîtiers de pompe de frein pour petites voitures et de coques d'amortisseur de moto et d'autres pièces de petite et moyenne taille produites en série avec des formes complexes et haute précision de résistance.
Si | Fe | Cu | Mn | Mg | Ni | Zn | Sn | Pb |
9.6-12.0 | 1.8-3.5 |
Dans les moulages en alliage d'aluminium ADC12, la phase a-Al est la structure la plus importante. A l'état brut de coulée, la phase a-Al est dendritique et relativement grossière, et son orientation n'a pas de régularité certaine et est assez brouillonne, ce qui rend ses performances peu bonnes. ; Si dans l'alliage est principalement utilisé pour améliorer les performances de coulée, la résistance à l'usure, la résistance à la corrosion et les propriétés mécaniques. Cu et Mg forment des phases CuAl2 et Mg2Si pour renforcer l'alliage, mais si la teneur est trop élevée, la plasticité sera réduite, et Cu peut également augmenter les performances à haute température, mais cela réduira la résistance à la corrosion ; Le Mn forme principalement la phase AIFeMnS, réduit les effets nocifs des impuretés Fe et peut améliorer la résistance à la chaleur des pièces moulées. Fe est généralement considéré comme l'élément d'impureté le plus nocif dans les alliages d'aluminium. La phase Fe est une phase a-Fe (AlgSiFez) et une phase B-Fe (AIsSiFe). La phase aciculaire β-Fe dure et cassante détruira la résistance de connexion de la matrice métallique et réduira considérablement les propriétés mécaniques de l'alliage (telles que la résistance à la traction), le Fe dans l'alliage Al en tant qu'élément nocif réduira considérablement : les propriétés mécaniques de l'alliage, affectent la rugosité de fracture et ainsi de suite.
2.Le processus des matières premières en alliage d'aluminium à contrôler
De nos jours, la plupart de l'industrie du moulage sous pression achète des lingots d'alliage d'aluminium auprès d'usines de production de lingots d'alliage d'aluminium. Les lingots d'alliage d'aluminium préparés de ce type sont principalement des produits d'aluminium secondaires recyclés en tant que matériau principal, et la composition est ajustée (des lingots d'aluminium pur et certains intermédiaires sont ajoutés). Alliage). Par conséquent, le coût et le prix de vente de ce lingot d'aluminium allié sont inférieurs à ceux du lingot d'aluminium pur en tant que matériau principal, mais la teneur en impuretés est plus élevée. Compte tenu de cette situation, il est nécessaire d'inspecter la composition chimique des lingots d'alliage d'aluminium achetés et de procéder aux ajustements appropriés lors de la signature des exigences techniques avec le fabricant de lingots d'alliage d'aluminium selon GB/T8733, puis de progresser conformément aux exigences. en alliage d'aluminium moulé sous pression - Réglage par paliers. En raison des exigences de la teneur en gaz et des points durs dans l'alliage d'aluminium, l'usine de production de lingots d'aluminium doit effectuer le raffinage, le dégazage et le scorification pour empêcher la teneur élevée en gaz et de nombreuses impuretés dans le lingot d'aluminium d'être héritées dans le moulage sous pression. liquide d'aluminium. Le lingot d'aluminium est nécessaire. La surface est lisse (après élimination de l'écume), la fracture est fine et il n'y a pas de grain cristallin brillant de silicium cristallin. Les bulles d'air à la surface du lingot d'aluminium sont dues au fait que la peinture de la lingotière contient une grande quantité d'eau et n'a pas été séchée. La surface n'est pas brillante car l'écume n'a pas été grattée. La fracture du lingot d'aluminium présente des grains cristallins brillants car la température de coulée est trop élevée et il y a des cristaux de silicium. Dans la production de moulage sous pression, il y a 30 à 60 % de matière recyclée. Si le matériau recyclé est huileux, il doit être brûlé puis pressé dans l'aluminium liquide. Les scories d'aluminium broyées doivent être tamisées et dépoussiérées, et le sable et les graviers doivent être retirés avant de retourner au four. Où le matériau recyclé est utilisé La quantité d'aluminium fondu, d'agent d'affinage et d'éliminateur de laitier doit être augmentée de manière appropriée et généralement contrôlée en fonction du rapport de limite supérieure. Lors de la fusion, le lingot d'aluminium ajouté doit être sec.
3. La fonte de l'alliage d'aluminium
Le four de fusion utilisé par l'entreprise est l'ATM-1500. L'entreprise exige que le four de fusion soit cuit chaque fois que le quart est ouvert afin d'éliminer l'humidité dans le four, et le four après la cuisson doit répondre aux exigences de processus spécifiées. Pendant le processus de fusion, la température de fusion est requise : (680~750) C ; la température du four d'affinage : (730+10) C. Pendant tout le processus de fusion de l'alliage d'aluminium, la charge commence à fondre lorsqu'elle est chauffée, réalisant la transformation de solide en liquide. Au cours de ce processus de transformation, le métal sera oxydé, brûlé et dégagera du gaz. L'oxydation et la combustion du métal affecteront non seulement la composition chimique de l'alliage, mais également l'inclusion de scories causée par l'oxydation est l'un des défauts les plus nocifs des lingots d'alliage d'aluminium. L'inhalation du métal rendra le lingot trop tard ou impossible pendant le processus de solidification. Il s'échappe et existe dans le lingot sous forme de lâches et de pores. Par conséquent, l'exactitude du processus de fusion de l'alliage d'aluminium est directement liée à la qualité de la fusion. Il affecte non seulement sa composition chimique, mais affecte également la qualité du lingot et même la finale. La qualité des produits transformés est étroitement liée. L'aluminium est très actif, sauf pour les gaz inertes, il réagit avec presque tous les gaz :
De plus, ces réactions sont irréversibles. Une fois réagi, le métal ne peut pas être réduit, ce qui provoque la perte du métal. De plus, les produits (oxydes, carbures, etc.) entrant dans la masse fondue vont contaminer le métal et provoquer des défauts dans la structure interne du lingot. Par conséquent, dans le processus de fusion des alliages d'aluminium, il existe une sélection stricte des équipements de traitement (tels que le type de four, la méthode de chauffage, etc.), ainsi qu'une sélection et des mesures strictes pour le flux de processus, telles que le raccourcissement du temps de fusion et le contrôle de la vitesse de fusion appropriée. Utilisez du flux pour couvrir et ainsi de suite.
- En raison de l'activité de l'aluminium, à la température de fusion, il réagira chimiquement avec l'humidité de l'atmosphère et l'humidité, le pétrole, les hydrocarbures, etc. dans une série de processus. D'une part, la teneur en gaz dans la masse fondue est augmentée, provoquant un relâchement et des pores, et d'autre part, le produit peut tacher le métal. Par conséquent, toutes les mesures doivent être prises pour minimiser l'humidité pendant le processus de fusion, et l'équipement de traitement, les outils et les matières premières doivent être strictement maintenus au sec et tachés d'huile.
- L'entreprise utilise une méthode de fusion continue, cette méthode alimente en continu et décharge par intermittence. Pour la fusion d'alliages d'aluminium, en raison de la structure du four, le temps de séjour de la masse fondue doit être aussi court que possible. Parce que le temps de séjour de la masse fondue est prolongé, en particulier à des températures de fusion plus élevées, un grand nombre de noyaux cristallins non spontanés sont désactivés, provoquant des grains de cristal de lingot grossiers, entraînant des déchets de coulée de lingots et une aspiration accrue du métal, rendant la masse fondue non- inclusions métalliques et La teneur en gaz augmente.
- Le gaz dans l'atmosphère dans le four de fusion du métal est l'une des sources de gaz les plus importantes. Selon le type et la structure du four de fusion utilisé, et la méthode de combustion ou de chauffage du combustible utilisé, l'atmosphère du four contient souvent diverses proportions d'hydrogène (H2), d'oxygène (O2), de vapeur d'eau (H2O), de dioxyde de carbone ( CO2) et monoxyde de carbone. (CO), azote (N2), dioxyde de soufre (SO2) en plus de divers hydrocarbures. Ces résultats sont bien entendu incomplets, et la gamme de composition est très large. Ceci est dû au fait que le produit de combustion dans le gaz du four change considérablement et est très instable. Ici, nous présentons principalement le processus d'absorption d'hydrogène (H) dans un alliage d'aluminium liquide, qui comprend principalement trois processus : adsorption, diffusion et dissolution.
Parce que l'hydrogène est un gaz unitaire avec une structure relativement simple, ses atomes ou molécules sont très petits, il est plus facile à dissoudre dans les métaux et il est facile à diffuser rapidement à haute température. Par conséquent, l'hydrogène est un gaz qui se dissout facilement dans les métaux.
Le processus de dissolution de l'hydrogène dans l'aluminium fondu : adsorption physique + adsorption chimique →> diffusion
L'hydrogène ne réagit pas chimiquement avec l'aluminium mais existe dans les interstices du réseau cristallin à l'état ionique, formant une solution solide interstitielle. En l'absence de film d'oxyde à la surface du métal liquide, la vitesse de diffusion du gaz dans le métal est inversement proportionnelle à l'épaisseur du métal, proportionnelle à la racine carrée de la pression du gaz, et augmente avec l'augmentation de la température
Où : v vitesse de diffusion n-constante d-épaisseur du métal E-énergie d'activation p-gaz pression partielle R-gaz constant T-température K Par conséquent, avant d'atteindre la solubilité à saturation du gaz, plus la température de fusion est élevée, plus la dissociation de l'hydrogène est élevée. molécules Plus la vitesse est rapide, plus la vitesse de diffusion est rapide, donc plus la teneur en gaz dans la masse fondue est élevée.
Dans les conditions de production, quel que soit le type de four de fusion utilisé pour produire un alliage d'aluminium, la masse fondue est directement en contact avec l'air, c'est-à-dire avec l'air
L'oxygène contenu dans le gaz est en contact avec l'azote. L'aluminium est un métal relativement actif. Après avoir été en contact avec l'oxygène, il produira inévitablement une forte oxydation pour former de l'alumine.
Une fois que l'aluminium est oxydé, il devient un laitier oxydé et devient une perte irréversible. L'alumine est une substance solide très stable, si elle est mélangée à la masse fondue, elle deviendra du laitier oxydé. En raison de la forte affinité de l'aluminium et de l'oxygène, la réaction entre l'oxygène et l'aluminium est très intense. Cependant, l'aluminium de surface réagit avec l'oxygène pour produire de l'Al2O3, et le volume moléculaire de l'Al2O est supérieur à celui de l'aluminium, de sorte que la couche de surface de l'aluminium est oxydée pour former A12O ; le film est dense, ce qui peut empêcher les atomes d'oxygène de se diffuser vers l'intérieur à travers le film d'oxyde. En même temps, il peut également empêcher les ions aluminium de se diffuser vers l'extérieur, empêchant ainsi une oxydation supplémentaire de l'aluminium.
4.Traitement de l'alliage d'aluminium
Le traitement de l'alliage d'aluminium comprend principalement l'élimination des scories et l'affinage.
- (1) Dans le processus de fusion des alliages d'aluminium de scorification, en raison de l'élimination et de la purification inefficaces des scories, une petite quantité de scories est dissoute dans la fonte, ce qui entraîne la formation de taches de neige à la surface de l'alliage d'aluminium, ce qui affecte sérieusement la qualité de l'alliage d'aluminium. Si l'élimination des scories n'est pas propre, cela provoquera des inclusions de scories et d'autres pièges, et le moulage sera mis au rebut. L'aluminium est une sorte de métal actif. Il est facile de produire des oxydes d'aluminium pendant le processus de fusion. Certaines inclusions non métalliques sont également faciles à pénétrer dans la masse fondue. Les inclusions sont très nocives pour les produits en aluminium. L'élimination des inclusions est devenue la tâche principale de la purification de l'aluminium fondu. Dans la pratique de la production, les inclusions courantes dans les fusions d'alliages d'aluminium sont Al203, SiO2, MgO, etc. Cela provoquera l'impureté du métal en fusion, les inclusions affecteront la fluidité de la masse fondue, la polymérisation produira des bulles pendant le processus de solidification, ce qui affectera le degré de retrait. Étant donné que la densité des fines particules d'oxyde est similaire à celle de l'aluminium, elles sont généralement en suspension dans de l'aluminium fondu et il est difficile de les éliminer en restant immobile. L'oxyde retiré contient généralement beaucoup d'aluminium. Bien que le fondant ait de nombreuses autres utilisations, la réduction de l'oxydation de l'aluminium et l'élimination des inclusions oxydées sont les principales raisons d'utiliser le fondant. Le principe du laitier dans le four de fusion : scories et de l'eau, et retirez les scories séparées du four, car l'agent de scories contient du NajAIF. (Ou KzSiFg), ce sel a la capacité d'adsorber fortement Al2O3, ainsi que Na2SiF. La première réaction peut manger une partie de Al2O3, et la troisième réaction sépare le laitier et l'eau, et tire le laitier du four pour atteindre le but de l'élimination des scories. Dans le même temps, il génère également du NaAlF%, ce qui a pour effet d'adsorber fortement le r-Al2O3, ce qui rend le laitier et l'aluminium. Le liquide est séparé. Le but du processus d'élimination des scories de l'alliage d'aluminium est d'éliminer les impuretés et les scories d'oxyde qui pénètrent dans l'aluminium fondu. Souvent, le laitier contient de l'aluminium fondu pendant l'élimination du laitier. Par conséquent, on espère que l'aluminium fondu contenu dans le laitier devrait être aussi faible que possible et que le laitier devrait être à nouveau brouillé. Le but de la friture est de faire sortir l'aluminium fondu dans le laitier et de le couler au fond du wok, de sorte que le laitier soit doucement cassé et dispersé sur la partie supérieure, de sorte que le laitier et l'aluminium fondu soient séparés. Pour y parvenir, un bon flux d'élimination des scories doit être sélectionné. . La méthode d'élimination des scories est basée sur la quantité d'aluminium fondu dans le four de fusion, uniformément mise dans l'éliminateur de scories selon la proportion requise, et remuer à une vitesse constante, puis retirer le laitier du filtre après s'être arrêté pendant 8- 10 minutes. Le laitier nécessite que la température de l'aluminium fondu soit de 720-740C.
- (2) Raffinage : Les propriétés chimiques de l'aluminium sont 17 fois plus actives. Par conséquent, même si la teneur en hydrogène dans l'alliage liquide est très faible, une grande quantité d'hydrogène précipitera lors de la solidification, formant des trous d'épingle et des inclusions dans les pièces moulées, ce qui affectera sérieusement les propriétés mécaniques de l'alliage d'aluminium. L'amélioration de la qualité de la fonte des alliages d'aluminium et la purification du liquide de l'alliage sont l'un des problèmes clés de la fusion des alliages d'aluminium. Processus de raffinage déraisonnable, le dégazage de l'alliage n'est pas propre, les pièces moulées sont sujettes aux pores. Afin d'augmenter l'effet de dégazage, il est nécessaire d'augmenter la quantité d'agent d'affinage ajouté. Cependant, si la quantité est trop importante, il est facile de provoquer la combustion de l'oxydation du magnésium. Al, Ti et d'autres éléments, et la formation de scories d'oxydation. Pour cela, un processus clé d'affinage des alliages d'aluminium est essentiel. Des études ont montré que plus la distance nécessaire à l'hydrogène pour atteindre la bulle est courte, plus le taux de dégazage est rapide. Notre société a choisi un désaérateur à rotor rotatif développé par FOSECO pour la désaération des liquides d'alliage d'aluminium. Son principe de fonctionnement est le suivant : le rotor rotatif brise les grosses bulles de gaz inerte ordinaire en petites bulles et les disperse dans le métal en fusion. En réduisant le diamètre des bulles, la surface des bulles augmente fortement, et il y a plus d'inertie. La surface de la bulle est en contact avec l'hydrogène et les impuretés du métal en fusion, améliorant ainsi l'efficacité du dégazage. Le dégazage à rotor tournant est reconnu comme l'un des meilleurs procédés de dégazage. Le schéma de structure de la machine de dégazage à rotor rotatif est le suivant : le moteur entraîne la rotation de la tige rotative et du rotor en graphite, et le gaz inerte pénètre dans la tige rotative par l'accouplement rotatif. La tige rotative et le rotor en graphite ont un trou central qui permet au gaz inerte de passer à travers et de pulvériser dans le liquide métallique. Le rotor en graphite rotatif brise les bulles de gaz inerte en très fines bulles, qui se diffusent dans tout le métal en fusion. En ajustant et en contrôlant le débit du gaz inerte et la vitesse du rotor en graphite, la taille des bulles est contrôlée et l'effet de purification est amélioré. En même temps, l'agent de raffinage placé sur la machine de dégazage est ajouté au liquide d'aluminium traité dans une certaine proportion pour garantir que l'écume d'oxyde est encore éliminée pendant le dégazage. Exigences du processus de raffinage : transférer l'eau d'aluminium dans le four de fusion vers le désaérateur rotatif avec un sac d'eau de transfert : la pression d'azote doit être contrôlée à 0.1-0.3 mpa pour empêcher l'aluminium d'éclabousser et de se blesser ; le temps d'affinage et de dégazage Contrôlé dans les 5min. L'élimination des scories et l'affinage de l'alliage d'aluminium moulé sous pression est un processus de temps qui ne peut pas être achevé rapidement. C'est une mauvaise opération de raccourcir le temps d'affinage. L'adsorption du gaz dans l'aluminium fondu et le flottement des impuretés nécessitent un temps fixe, seulement une garantie. Il existe un temps d'adsorption et un temps de flottement des impuretés suffisants pour atteindre l'objectif de raffinage. Pendant l'affinage, assurez-vous que l'aluminium liquide est en plein contact avec les bulles. Une agitation constante est nécessaire. Le gaz dans l'aluminium liquide est éliminé et les impuretés sont éliminées pour garantir les pores du produit.
5.Conclusion
Le choix d'un processus de fusion raisonnable dans le processus de production d'alliage d'aluminium moulé sous pression est la première étape pour obtenir une excellente qualité de produit de moulage sous pression. Le contrôle strict des matières premières est une étape clé de la fusion. Dans le même temps, il est nécessaire d'avoir une compréhension simple des effets des différents éléments de l'alliage avant la fusion. L'élimination des scories et l'affinage sont des processus très importants dans le processus de fusion des alliages d'aluminium. Grâce à des recherches théoriques sur l'élimination des scories et le dégazage, un procédé de fusion adapté à notre entreprise a été obtenu.
Veuillez conserver la source et l'adresse de cet article pour réimpression:La fonte et le traitement de l'ADC12
Minghé Société de moulage sous pression sont dédiés à la fabrication et à la fourniture de pièces de moulage de qualité et de haute performance (la gamme de pièces de moulage sous pression en métal comprend principalement Moulage sous pression à paroi mince,Chambre chaude coulée sous pression,Chambre froide coulée sous pression), Service rond (Service de moulage sous pression,Usinage CNC,Fabrication de moules,Traitement de surface). Tout moulage sous pression en aluminium personnalisé, moulage sous pression en magnésium ou en zamak/zinc et autres exigences en matière de moulages sont invités à nous contacter.
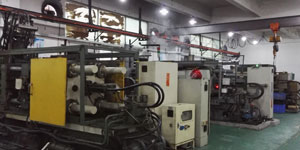
Sous le contrôle des normes ISO9001 et TS 16949, tous les processus sont effectués via des centaines de machines de moulage sous pression avancées, de machines à 5 axes et d'autres installations, allant des blasters aux machines à laver Ultra Sonic.Minghe dispose non seulement d'équipements de pointe, mais également de professionnels équipe d'ingénieurs, d'opérateurs et d'inspecteurs expérimentés pour réaliser la conception du client.
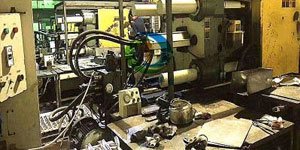
Fabricant sous contrat de moulages sous pression. Les capacités incluent des pièces de moulage sous pression en aluminium à chambre froide à partir de 0.15 lb. jusqu'à 6 lb, configuration à changement rapide et usinage. Les services à valeur ajoutée comprennent le polissage, la vibration, l'ébavurage, le grenaillage, la peinture, le placage, le revêtement, l'assemblage et l'outillage. Les matériaux travaillés comprennent des alliages tels que 360, 380, 383 et 413.
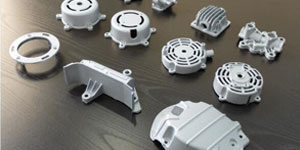
Assistance à la conception de moulage sous pression de zinc/services d'ingénierie simultanés. Fabricant sur mesure de pièces moulées en zinc de précision. Des moulages miniatures, des moulages sous pression à haute pression, des moulages en moules à glissières multiples, des moulages en moules conventionnels, des moulages sous pression unitaires et indépendants et des moulages à cavité scellée peuvent être fabriqués. Les pièces moulées peuvent être fabriquées dans des longueurs et des largeurs allant jusqu'à 24 po avec une tolérance de +/- 0.0005 po.
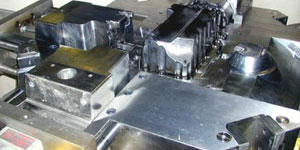
Fabricant certifié ISO 9001 : 2015 de magnésium moulé sous pression, les capacités incluent le moulage sous pression de magnésium sous pression jusqu'à une chambre chaude de 200 tonnes et une chambre froide de 3000 tonnes, la conception d'outillage, le polissage, le moulage, l'usinage, la peinture en poudre et liquide, une assurance qualité complète avec des capacités CMM , assemblage, emballage et livraison.
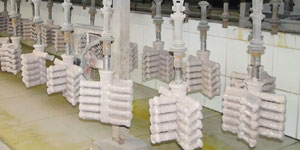
Certifié ITAF16949. Service de casting supplémentaire inclus coulée d'investissement,moulage en sable,Coulée par gravité, Coulée de mousse perdue,Coulée centrifuge,Coulée sous vide,Moulage de moule permanentLes capacités comprennent l'EDI, l'assistance technique, la modélisation solide et le traitement secondaire.
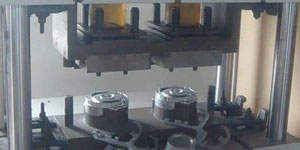
Industries de moulage Études de cas de pièces pour : voitures, vélos, avions, instruments de musique, motomarines, appareils optiques, capteurs, modèles, appareils électroniques, boîtiers, horloges, machines, moteurs, meubles, bijoux, gabarits, télécommunications, éclairage, appareils médicaux, appareils photographiques, Robots, Sculptures, Équipement de sonorisation, Équipement de sport, Outillage, Jouets et plus encore.
Que pouvons-nous vous aider à faire ensuite ?
∇ Aller à la page d'accueil pour Moulage sous pression Chine
→Pièces de fonderie-Découvrez ce que nous avons fait.
→Conseils à propos de Services de moulage sous pression
By Fabricant de moulage sous pression Minghe |Catégories : Articles utiles |Matières Mots clés: Moulage d'aluminium, Moulage de zinc, Coulée de magnésium, Moulage de titane, Fonderie en acier inoxydable, Coulée de laiton,Coulée de bronze,Vidéo de casting,Historique de l'entreprise,Moulage sous pression en aluminium |Commentaires fermés