Recueil des défauts courants et mesures préventives en cémentation et trempe
La cémentation et la trempe sont en fait un processus composite, à savoir la cémentation + la trempe. On a souvent l'habitude de parler des deux ensemble, car les deux procédés qui sont réalisés sur le même équipement sont les plus couramment rencontrés en production (mais il y a aussi les procédés de refroidissement par air cémentation, de refroidissement lent cémentation puis de réchauffage et de trempe, et les procédés secondaires puis certains des phénomènes indésirables rencontrés dans la production sont des problèmes de cémentation, certains sont des problèmes de trempe, et certains sont le résultat des effets combinés de la cémentation et de la trempe.
Nous savons que tous les processus de traitement thermique sont indissociables de trois problèmes fondamentaux : le chauffage, la conservation de la chaleur et le refroidissement. En détail, y compris la température de chauffage, la vitesse de chauffage, le temps de maintien, la vitesse de refroidissement et, bien sûr, les problèmes d'atmosphère. Donc, une fois que quelque chose ne va pas, nous analyserons habituellement la cause à partir de ces aspects.
Pour la cémentation et la trempe, nous testons souvent ces indicateurs : aspect de surface du produit, dureté de surface, dureté à cœur, profondeur de couche cémentée (profondeur de couche durcie effective, profondeur de couche entièrement durcie), structure métallographique et déformation. Partageons mon point de vue sur ces indicateurs respectivement.
1. Problème d'apparence
1. Échelle d'oxyde : Ceci est principalement dû à une fuite d'équipement, à un gaz vecteur impur ou à la teneur en eau. Besoin de trouver la raison de l'équipement et des matières premières.
2. L'autre problème le plus gênant est le problème des taches, qui est également une exigence nouvelle et difficile pour le traitement thermique à l'époque moderne. Les raisons sont compliquées et très profondes.
deux. Dureté sans réserve
1. Haute dureté (non discuté)
2. Faible dureté : il existe deux situations, l'une est une carburation non qualifiée. La raison peut être que la couche carburée est trop peu profonde pour répondre aux exigences des dessins (la couche carburée n'est pas infiltrée), ou que l'échelle de détection sélectionnée dépasse la plage tolérable de la couche carburée existante, ce qui décomposera la couche carburée.
Solution : reconstituer l'infiltration et suivre la règle d'inspection. JBT 6050-2006 "Principes généraux pour l'inspection de la dureté par traitement thermique des pièces en acier" La profondeur de la couche cémentée est en fait fonction de la température, du temps et du potentiel carbone. À partir des facteurs ci-dessus, nous pouvons envisager des moyens d'augmenter la température de chauffage, de prolonger le temps de maintien et d'augmenter le potentiel de carburation. (Bien sûr, le réglage de chaque paramètre doit être pleinement combiné avec les exigences de vos propres équipements et produits) Cela peut également être dû à l'existence d'organisations non équestres en surface. Une autre situation se produit lorsque la dureté est faible, c'est-à-dire que la cémentation est qualifiée, mais la trempe est non qualifiée. D'une manière générale, il n'est pas éteint. Cette situation est la plus compliquée, comme le dit l'adage : le traitement thermique repose sur le chauffage pendant trois quarts, et le refroidissement pendant sept quarts. Il reflète également la place qu'occupe le processus de refroidissement dans le processus de traitement thermique.
Ce qui suit est un test comparatif que j'ai conçu. Vous pouvez discuter de l'effet du refroidissement sur la dureté.
Prenez 3 groupes de barres de test avec des matériaux différents mais les mêmes spécifications et dimensions, dont la taille est Φ20mmX100mm. (Nous appelons barre d'essai en acier n° 20 n° 1, barre d'essai 20Cr n° 2 et barre d'essai 20CrMnTi n° 3) Les barres d'essai sont cémentées à la même chaleur en utilisant le même procédé. En supposant que la profondeur de la couche cémentée des trois barres d'essai est de 0.6-0.7 mm (ps : l'hypothèse n'est établie que dans un état idéal).
Veuillez tenir compte des conditions suivantes :
une. Finir la trempe dans les mêmes conditions
b. Le milieu de trempe est une huile lente, une huile rapide, de l'eau claire, de l'eau salée
c. Dans le même milieu sans agitation et agitation et trempe intensives, les trois barreaux de test sont prélevés chacun en deux groupes pour test.
Une fois la cémentation terminée, le groupe A est trempé à 800 degrés et le groupe B est trempé à 860 degrés. Quel est l'ordre de leur dureté de haute à basse? Comment ordonner la couche durcie (avec 550HV1.0 comme limite) de profonde à peu profonde ? Prenez deux barres d'essai du même matériau et comparez et testez, quel groupe peut obtenir une dureté de trempe plus élevée et une profondeur de couche durcie efficace ?
Peut-on conclure des résultats des tests ci-dessus que la profondeur de la couche cémentée n'est pas égale à la profondeur de la couche durcie effective, et la profondeur réelle de la couche durcie est affectée par la trempabilité du matériau, la température de trempe et le refroidissement taux. Les caractéristiques de refroidissement et l'intensité de refroidissement du fluide de refroidissement affectent également l'effet de refroidissement. Ce qui précède est le point de vue des gens, s'il y a des lacunes, vous pouvez ajouter. Bien entendu, l'effet de taille des pièces affecte également l'effet de durcissement.
Je pense qu'un inspecteur expérimenté peut déterminer la cause réelle de la faible dureté en organisant et en combinant d'autres méthodes de test, puis trouver la vraie cause pour la résoudre ; en tant qu'artisan, si vous connaissez les caractéristiques des matières premières métalliques conventionnelles, les performances de refroidissement de ses propres équipements et milieu ont atteint un certain niveau de reconnaissance, ce qui est d'une grande aide pour la formulation des procédés de cémentation et de trempe.
3. Dureté inégale : température uniforme du four (affectant l'uniformité de la cémentation), structure de l'équipement, circulation de l'atmosphère, chargement du four (affectant l'uniformité de la couche de cémentation et affectant en même temps l'uniformité de la trempe)
4. La dureté du noyau n'est pas qualifiée. Trop élevé : la température de trempe est trop élevée, la trempabilité du matériau est trop bonne, la limite supérieure de la composition du carbone et de l'alliage et la vitesse de refroidissement moyenne est trop rapide. La dureté à cœur est faible : bien au contraire.
Exemple de partage : produit en acier 20# de 1.5 mm, exigences : couche d'infiltration 0.2-0.4 mm noyau HV250, certains amis du même secteur pensent que les exigences sont déraisonnables (tout le monde doit savoir que la dureté la plus élevée de la martensite de dalle d'acier 20# sera HV450-470) Pour résoudre ce problème, il faut d'abord comprendre les caractéristiques de ce matériau : notamment la trempabilité et la trempabilité.
Ensuite, combinez les facteurs mentionnés ci-dessus qui affectent l'effet de trempe et trouvez des moyens de chauffer et de refroidir. Dans ce cas, le matériau est fixe. Nous pouvons trouver un moyen à partir de la température de trempe et de la vitesse de refroidissement. Ce fabricant utilise de l'huile pour survitesse. Si la réduction de l'intensité de trempe ne répond pas aux exigences, nous pouvons également réduire la température de trempe. Méthode.
Toujours la même phrase, de 860-760 degrés, (lorsque la température est abaissée à un certain niveau, une certaine quantité de ferrite sera précipitée de l'austénite surfondue dans le noyau, et la dureté diminuera à ce moment. , Plus plus la température diminue, plus la quantité de ferrite précipitée, plus la dureté diminue.
Voici un rappel : Il est nécessaire de combiner pleinement les conditions existantes de l'équipement et de faire tout un plat sur l'indice favorable spécial de perméabilité peu profonde.
3. La couche carburée ou couche carburée efficace est plus profonde et moins profonde
Comme mentionné précédemment, la profondeur de la couche d'infiltration est une fonction globale de la température, du temps et de la concentration en carbone. Pour résoudre ce problème, nous devons commencer par la température de chauffage, la vitesse de chauffage, le temps de maintien, la vitesse de refroidissement et le contrôle du gradient de concentration en carbone dans la couche de carbone. Plus la température est élevée, plus le temps est long, et plus le potentiel carbone est élevé, plus la couche d'infiltration est profonde, et vice versa.
Mais en fait, c'est bien plus que cela. Pour concevoir un procédé de cémentation, vous devez également tenir compte de l'équipement, de la capacité du four, des caractéristiques de l'huile, de la structure métallographique, de la trempabilité du matériau, du gradient de concentration en carbone dans la couche cémentée et de la vitesse de refroidissement. Et bien d'autres facteurs. Ceci peut être analysé en référence à la situation précédente de faible dureté, et ne sera pas expliqué en profondeur.
Quatrièmement, l'organisation métallographique
Martensite excessive : la matière première a des grains grossiers, ou n'est pas normalisée, et la température de cémentation est trop élevée. Solution : normalisation ou normalisation multiple (il est recommandé que la température de normalisation soit supérieure de 20 à 30 degrés à la température de cémentation) Si possible, envisagez une cémentation et un refroidissement lent, puis un réchauffage et une trempe
Paralympique excessif : la température de trempe est trop élevée, la teneur en carbone dans l'austénite est trop élevée (le potentiel carbone est trop élevé). Solution : La diffusion complète et les conditions permises peuvent réduire la température de trempe, le revenu à haute température et le réchauffage et la trempe, ou le traitement cryogénique.
Carbure excessif : teneur en carbone trop élevée dans l'austénite (potentiel carbone trop élevé), processus de refroidissement trop lent, précipitation du carbure
Solution : diffuser complètement, contrôler la vitesse de refroidissement, réduire autant que possible la différence de température entre la cémentation et la trempe et utiliser le moins possible la trempe à basse température ou à sous-température. Si ce procédé doit être utilisé, la charge du four doit être contrôlée. Imaginons : le même équipement est cémenté à 920°C et trempé à 820°C. La capacité du four est de 1000 kg et 600 kg, et le taux de refroidissement est le même ? Lequel prendra plus de temps ? Quelle nuance de carbure est la plus élevée ?
Cinq. Oxydation non équine et interne
Oxydation interne : C'est la réaction entre les éléments d'alliage tels que le chrome, le manganèse et le molybdène dans l'acier et l'atmosphère oxydante dans l'atmosphère (principalement l'oxygène, l'eau, le dioxyde de carbone), qui épuise les éléments d'alliage dans la matrice, entraînant une diminution dans la trempabilité du matériau. La structure du réseau noir est visible au microscope, son essence est la structure troostite obtenue par l'épuisement des éléments d'alliage dans la matrice et la diminution de la trempabilité.
La solution consiste à trouver des moyens d'augmenter la vitesse de refroidissement du milieu, d'améliorer l'intensité de la trempe et de réduire l'atmosphère oxydante dans le four (assurer la pureté des matières premières et auxiliaires de cémentation, minimiser la quantité d'air équilibré, contrôler l'équilibre teneur en humidité de l'air, et s'assurer que l'équipement ne fuit pas Échappement suffisant) L'équipement conventionnel est difficile à éliminer. Il est dit que l'équipement de cémentation sous vide à basse pression peut être complètement éliminé. De plus, un grenaillage puissant peut également réduire le niveau d'oxydation interne.
J'ai lu les opinions de certains experts, et certains pensent qu'un excès d'ammoniac dans le processus de carbonitruration peut également causer de graves problèmes de chevaux. Personnellement, j'ai une opinion différente à ce sujet : peut-être est-ce dû à une teneur excessive en eau dans l'ammoniac ? Étant donné que j'ai été exposé à de nombreux processus de carbonitruration, aucun tissu non-cheval évident n'a été trouvé lors de l'inspection du produit. (Mais je ne pense pas que ce point de vue soit faux) Certaines industries de machines étrangères attachent une grande importance à l'oxydation interne, en particulier l'industrie des engrenages. Au niveau national, la profondeur ne doit généralement pas dépasser 0.02 mm selon la qualification.
Non martensitique : une structure non martensitique apparaît à la surface de la couche cémentée en raison de problèmes de carburation ou de trempe après trempe, comme la ferrite, la bainite, et bien sûr, la troostite de type oxydation interne. Le mécanisme de génération est similaire à l'oxydation interne, et la solution est similaire.
Six. Problème de déformation
C'est un problème de système, et c'est aussi le problème le plus gênant pour notre personnel engagé dans le traitement thermique. Il est garanti de plusieurs aspects du milieu de refroidissement de processus de matière première. Le contenu ci-dessus n'est qu'une expérience personnelle. S'il y a une incohérence, n'hésitez pas à me corriger, merci.
Veuillez conserver la source et l'adresse de cet article pour réimpression:Recueil des défauts courants et mesures préventives en cémentation et trempe
Minghé Société de moulage sous pression sont dédiés à la fabrication et à la fourniture de pièces de moulage de qualité et de haute performance (la gamme de pièces de moulage sous pression en métal comprend principalement Moulage sous pression à paroi mince,Chambre chaude coulée sous pression,Chambre froide coulée sous pression), Service rond (Service de moulage sous pression,Usinage CNC,Fabrication de moules,Traitement de surface). Tout moulage sous pression en aluminium personnalisé, moulage sous pression en magnésium ou en zamak/zinc et autres exigences en matière de moulages sont invités à nous contacter.
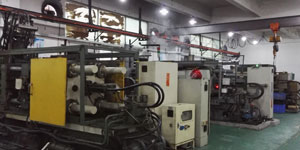
Sous le contrôle des normes ISO9001 et TS 16949, tous les processus sont effectués via des centaines de machines de moulage sous pression avancées, de machines à 5 axes et d'autres installations, allant des blasters aux machines à laver Ultra Sonic.Minghe dispose non seulement d'équipements de pointe, mais également de professionnels équipe d'ingénieurs, d'opérateurs et d'inspecteurs expérimentés pour réaliser la conception du client.
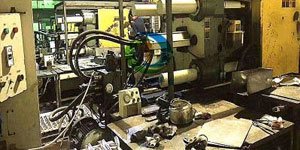
Fabricant sous contrat de moulages sous pression. Les capacités incluent des pièces de moulage sous pression en aluminium à chambre froide à partir de 0.15 lb. jusqu'à 6 lb, configuration à changement rapide et usinage. Les services à valeur ajoutée comprennent le polissage, la vibration, l'ébavurage, le grenaillage, la peinture, le placage, le revêtement, l'assemblage et l'outillage. Les matériaux travaillés comprennent des alliages tels que 360, 380, 383 et 413.
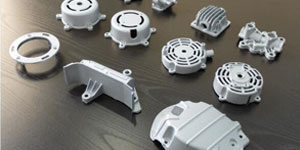
Assistance à la conception de moulage sous pression de zinc/services d'ingénierie simultanés. Fabricant sur mesure de pièces moulées en zinc de précision. Des moulages miniatures, des moulages sous pression à haute pression, des moulages en moules à glissières multiples, des moulages en moules conventionnels, des moulages sous pression unitaires et indépendants et des moulages à cavité scellée peuvent être fabriqués. Les pièces moulées peuvent être fabriquées dans des longueurs et des largeurs allant jusqu'à 24 po avec une tolérance de +/- 0.0005 po.
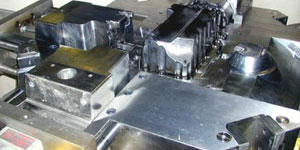
Fabricant certifié ISO 9001 : 2015 de magnésium moulé sous pression, les capacités incluent le moulage sous pression de magnésium sous pression jusqu'à une chambre chaude de 200 tonnes et une chambre froide de 3000 tonnes, la conception d'outillage, le polissage, le moulage, l'usinage, la peinture en poudre et liquide, une assurance qualité complète avec des capacités CMM , assemblage, emballage et livraison.
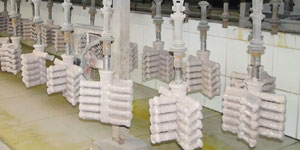
Certifié ITAF16949. Service de casting supplémentaire inclus coulée d'investissement,moulage en sable,Coulée par gravité, Coulée de mousse perdue,Coulée centrifuge,Coulée sous vide,Moulage de moule permanentLes capacités comprennent l'EDI, l'assistance technique, la modélisation solide et le traitement secondaire.
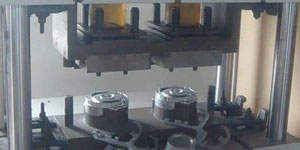
Industries de moulage Études de cas de pièces pour : voitures, vélos, avions, instruments de musique, motomarines, appareils optiques, capteurs, modèles, appareils électroniques, boîtiers, horloges, machines, moteurs, meubles, bijoux, gabarits, télécommunications, éclairage, appareils médicaux, appareils photographiques, Robots, Sculptures, Équipement de sonorisation, Équipement de sport, Outillage, Jouets et plus encore.
Que pouvons-nous vous aider à faire ensuite ?
∇ Aller à la page d'accueil pour Moulage sous pression Chine
→Pièces de fonderie-Découvrez ce que nous avons fait.
→Conseils à propos de Services de moulage sous pression
By Fabricant de moulage sous pression Minghe |Catégories : Articles utiles |Matières Mots clés: Moulage d'aluminium, Moulage de zinc, Coulée de magnésium, Moulage de titane, Fonderie en acier inoxydable, Coulée de laiton,Coulée de bronze,Vidéo de casting,Historique de l'entreprise,Moulage sous pression en aluminium |Commentaires fermés