Alliage d'aluminium et gestion des matériaux auxiliaires dans la production de moulage sous pression
Gestion du matériel principal
1. Contrôle d'entrée des lingots d'alliage d'aluminium
En raison de la teneur en gaz et des exigences de point dur de l'alliage d'aluminium, les usines de production de lingots d'aluminium doivent faire un bon travail de raffinage, de dégazage et d'élimination des scories pour éviter que des défauts tels qu'une teneur élevée en gaz et de nombreuses impuretés dans les lingots d'aluminium ne soient hérités dans la matrice. coulée d'aluminium liquide. Une fois que le lingot d'alliage d'aluminium est entré dans l'usine, la première étape consiste à inspecter l'apparence. La surface du lingot d'aluminium doit être lisse, exempte de rugosité, exempte de taches d'huile, de moisissure et de tartre d'oxyde, et la structure de fracture du lingot d'alliage d'aluminium est fine et dense. Il ne devrait y avoir aucune ségrégation, rétrécissement ou rétrécissement sérieux. Scories et inclusions. Échantillonnage de la composition de chaque lot et numéro de coulée pour s'assurer que la composition d'alliage utilisée est qualifiée. Dans la production de produits avec des exigences particulières, d'autres éléments de test doivent être ajoutés. Par exemple, lors de la fabrication de produits avec des exigences de performances mécaniques, lorsque le lingot d'alliage d'aluminium est livré pour la production, il est nécessaire de soumettre une barre d'essai de traction pour chaque four ; lors de la production de produits avec des exigences d'étanchéité à l'air, le degré de trou d'épingle du lingot d'alliage d'aluminium doit être augmenté. Détecter
Les types d'alliages d'aluminium utilisés dans la production réelle ne sont souvent pas limités à une seule qualité, et les exigences de composition chimique de chaque qualité d'alliage d'aluminium sont très différentes. Les principaux éléments d'une nuance d'alliage se trouvent dans une autre nuance d'alliage. Il peut être considéré comme une impureté. Pour la coexistence de plusieurs nuances, il est nécessaire de bien distinguer visuellement les alliages de chaque nuance pour éviter l'apparition de mélanges lors de l'utilisation. La mesure générale consiste à spécifier clairement et uniformément la couleur d'apparence des alliages d'aluminium de différentes marques et différents fabricants, et de stocker différents matériaux dans différentes zones après leur arrivée à l'usine.
2. Contrôle du processus de fusion d'alliage d'aluminium
La pratique de la production montre que l'amélioration de la qualité de l'alliage fondu est un facteur clé dans l'amélioration de la qualité des moulages sous pression. Par conséquent, la gestion des matières premières doit être strictement contrôlée afin que les matières premières non qualifiées ne soient pas mises dans l'atelier ou mises en production. Opérer strictement conformément aux normes requises par le processus de fusion des alliages et renforcer la gestion des diverses matières premières (nouveaux matériaux, matériaux recyclés et matériaux auxiliaires).
Le processus de fusion des alliages d'aluminium doit avoir des réglementations claires sur la température de fusion, le temps de fusion et la proportion de matériaux re-cuits, en particulier les matériaux re-cuits doivent être strictement classés et gérés, et ils ne doivent pas être mélangés. Le matériau recyclé doit être propre et exempt d'huile, de rouille, de limon, d'humidité et d'inserts. Les contaminants huileux dans le matériau recyclé peuvent être refondus par le fabricant de lingots d'aluminium et ne peuvent pas être directement mis dans le four de fusion pour être utilisés ; pour les blocs d'aluminium épars, ils doivent être tamisés et la poussière, le sable et autres débris à l'intérieur peuvent être enlevés. Utilisation : Lorsque l'aluminium fondu est utilisé pour le réchauffage, le rapport entre l'agent d'affinage et l'éliminateur de scories est supérieur à celui lorsque seul un lingot d'alliage d'aluminium est utilisé pour la fusion. Dans la production par temps avec une humidité relative élevée, la proportion de matériau recyclé ne doit pas dépasser 30%, et le matériau recyclé peut être augmenté de manière appropriée par temps sec, mais il ne doit pas dépasser 40%.
Le laitier et le dégazage de l'aluminium fondu après la fusion doivent être effectués en temps opportun et les paramètres correspondants doivent être enregistrés selon les besoins. Dans le processus de fusion centralisé, la composition chimique de chaque pot d'aluminium liquide doit être testée pour s'assurer que la composition chimique du produit est qualifiée pendant le processus de fusion. De plus, la fusion à long terme doit être évitée, sinon la teneur en hydrogène du liquide d'alliage d'aluminium augmentera, ce qui affectera la résistance et l'étanchéité à l'air du produit de moulage sous pression. Généralement, il ne dépasse pas 4h de la fusion à la coulée sous pression.
Gestion des matériels auxiliaires
1. Contrôle de l'agent de démoulage
L'utilisation d'un agent de démoulage peut rendre le remplissage de métal liquide en douceur, faciliter le formage, empêcher le moulage de coller, faire en sorte que les pièces moulées obtiennent une qualité de surface brillante, lisse et plane et avoir une grande influence sur le rythme de production, la surface de coulée et la qualité interne. En même temps, il peut protéger le moule, éviter l'érosion du métal liquide à haute température sur la surface du moule, réduire la conductivité thermique et la température du moule et prolonger la durée de vie du moule. Lorsque le moule est ouvert, il favorise l'éjection en douceur de la pièce moulée et joue également un rôle important dans la réduction des frottements et de l'usure du poinçon, de la tige d'éjection et des pièces mobiles. Le contrôle de l'agent de démoulage comprend non seulement la sélection et le ratio de l'agent de démoulage lui-même, mais comprend également la gestion de la pulvérisation et du brushing de l'agent de démoulage par l'opérateur. Généralement, la sélection de l'agent de démoulage a les exigences suivantes.
- Il a un bon pouvoir lubrifiant à haute température et un faible point de volatilisation. L'eau contenue dans l'agent de démoulage peut se volatiliser rapidement à 100-150°C.
- Il n'a aucun effet corrosif sur les moules de moulage sous pression et les pièces de moulage sous pression, et a des performances stables. L'agent de démoulage ne doit pas se volatiliser trop vite et s'épaissir dans l'air.
- Aucun gaz nocif ne sera précipité à haute température et aucun encrassement ne se produira à la surface de la cavité de moulage sous pression.
À l'heure actuelle, la pulvérisation de l'agent de démoulage est principalement une opération manuelle, et une opération de pulvérisation raisonnable est un facteur important pour assurer la qualité de la coulée, la durée de vie du moule de coulée sous pression et l'efficacité de la production. Le temps de pulvérisation de l'agent de démoulage change également avec les performances de démoulage, le taux de dilution, les différentes formes de moulage sous pression et les différentes températures de moule des différents types d'agents de démoulage. L'agent de démoulage est pulvérisé du pistolet de pulvérisation à la surface du moule pour se condenser en un film protecteur. Cela prend beaucoup de temps. Lorsque le processus n'est pas terminé, l'opération de coulée est effectuée, ce qui est souvent à l'origine des défauts lâches de la coulée. Selon les réglementations du processus de moulage sous pression, une plage de temps de pulvérisation raisonnable doit être adoptée pour un type différent d'agent de démoulage et différents rapports de dilution. Les ouvriers du moulage sous pression doivent comprendre la signification des limites supérieure et inférieure des paramètres de processus et la tendance de l'influence de l'ajustement, et effectuer les ajustements appropriés en fonction des conditions de surface des moulages sous pression produits.
Lors de l'utilisation d'agents de démoulage à base d'eau, le rapport des agents de démoulage doit être strictement contrôlé. Si le rapport de l'agent de démoulage à l'eau est trop épais, un film plus épais se formera sur la surface du moule et une accumulation d'agent de démoulage se formera lentement sur la surface du moule. L'humidité dans l'agent de démoulage ne peut pas être complètement évacuée et du gaz sera généré, ce qui fera la pièce de moulage sous pression. La compacité interne se détériore. Si le rapport de l'agent de démoulage à l'eau est trop mince, l'effet ne sera pas atteint et les pièces moulées sous pression souffriront de la déformation et du collage du moule.
Par conséquent, dans le contrôle qualité de l'atelier de moulage sous pression, la gestion de l'agent de démoulage a un impact plus important sur la qualité des pièces de moulage sous pression. Il est nécessaire de renforcer la gestion dans ce domaine, par exemple en nommant une personne spéciale pour être responsable de la proportion de l'agent de démoulage et en stipulant clairement différents types de différents Le rapport de l'agent de démoulage et de l'eau dans le processus de production du moulage sous pression produits est déterminé et quantifié selon le processus de préparation de l'agent de démoulage. Lors de la pulvérisation, l'opérateur doit suivre une formation stricte sur l'action de pulvérisation, et l'action doit être effectuée conformément aux exigences et aux spécifications, et il n'est pas permis de pulvériser plus, moins de pulvérisation ou de manquer de pulvérisation.
2. Gestion de l'huile de poinçon
À l'heure actuelle, la plupart de l'utilisation d'huile de graissage de poinçon à base d'huile ou de lubrification par particules, quelle que soit la forme de lubrification de poinçon, une fois que le liquide d'aluminium est entré dans le canon, il doit être complètement brûlé en peu de temps et le résidu doit être distribué sur la couche supérieure du liquide d'alliage, de sorte que l'impact de l'huile de poinçon sur le produit ne soit pas trop important. Sinon, les gaz générés par la combustion et les résidus après combustion entreront dans le produit, et le résultat peut être imaginé.
Le moyen simple de vérifier l'huile de poinçon est d'observer la couleur de la poignée du matériau sur le moule. Généralement, l'épaisseur du manche en matériau est de 1/3 à 1/4 du diamètre du poinçon, et la longueur du noircissement de l'huile du poinçon ne doit pas dépasser 3 de l'épaisseur du manche en matériau. /5 ; Dans le même temps, il ne devrait pas y avoir de noircissement évident à l'extrémité du manche du matériau (c'est-à-dire trop de résidus de poudre de graphite). Sinon, une fois le produit traité, les défauts tels que les pores augmenteront inévitablement.
Dans le processus de production, nous devons également faire attention à tout moment à l'état de fonctionnement du dispositif de lubrification du poinçon. Si le lubrifiant est pulvérisé trop ou trop peu, cela aura un impact négatif sur la durée de vie de la chambre de pression et du poinçon et sur la qualité du moulage sous pression. Lors du réglage de la quantité de lubrifiant utilisé, il est nécessaire de prendre en compte à la fois le pouvoir lubrifiant du poinçon et la démoulabilité du moule. Surtout lors de l'utilisation de la lubrification par particules, quelle que soit la manière dont les pastilles de cire sont utilisées dans le moule de coulée sous pression, il y aura un problème de volatilisation de la matière organique. Si une grande quantité de matière organique volatile ne peut pas être correctement évacuée, cela aura un impact important sur la génération de pores dans la pièce de moulage sous pression.
3. Gestion des poinçons
Le poinçon et la chambre de pression constituent un système interdépendant. Dans des circonstances normales, la durée de vie de la chambre de pression peut atteindre 2 à 3 ans, et la durée de vie d'un poinçon est courte, un quart de travail, et la longue durée de vie peut atteindre plus de 10,000 XNUMX fois. La différence de durée de vie entraînera des fluctuations de la qualité du produit et des changements importants dans les coûts de production. Par conséquent, une bonne gestion des poinçons peut non seulement stabiliser la qualité des pièces moulées sous pression, mais également réduire considérablement le coût de production du moulage sous pression.
- Conception de la taille du poinçon. Dans des circonstances normales, il doit y avoir un certain jeu entre le poinçon et la chambre de pression. La pratique montre que l'écart idéal est d'environ 0.1 mm. Pendant l'injection, si l'espace est trop grand, le liquide d'alliage d'aluminium peut pénétrer dans l'espace, et des fuites de liquide d'aluminium et de la fumée se produiront, ce qui aggravera l'usure du poinçon et réduira sa durée de vie ; si l'écart est trop petit, le poinçon se déplacera dans le processus Il y a coincement, la vitesse du poinçon ne peut pas atteindre la vitesse prédéterminée par le processus, le temps de remplissage du moule est prolongé, et les problèmes de qualité du moulage sous pression les pièces augmentent. Par conséquent, le traitement et la fabrication du poinçon doivent être effectués strictement selon le dessin, afin de contrôler enfin l'écart critique, de prolonger la durée de vie du poinçon et d'assurer la qualité du produit.
- Le refroidissement du poinçon Étant donné que le processus de moulage sous pression détermine que la température du poinçon change constamment, avec le changement de température, l'écart entre le poinçon et la chambre de pression change également. Ces changements affectent non seulement la durée de vie du poinçon, mais également la stabilité du processus d'injection pendant le processus de moulage sous pression. Pour maintenir l'écart idéal, il est nécessaire de refroidir le poinçon. Dans la conception, on considère que le piston est entièrement refroidi par le noyau d'eau de la tige d'injection, et la chaleur du poinçon est évacuée au maximum, et l'écart idéal entre le poinçon et la chambre de pression peut être conservé stable. Ces mesures permettent d'assurer la stabilité du processus d'injection de chaque moule et la stabilité de la qualité des produits de coulée sous pression. La pratique a montré que le système d'injection avec un bon refroidissement du poinçon peut considérablement prolonger la durée de vie du poinçon tout en assurant la stabilité du processus d'injection. Cependant, il faut faire un bon travail d'étanchéité du circuit d'eau de refroidissement du poinçon, et se méfier des fuites d'eau de refroidissement provoquées par une mauvaise étanchéité entre le poinçon et la tige d'injection. Si une attention suffisante n'est pas accordée aux fuites d'eau de refroidissement, cela affectera sérieusement le produit. Étanchéité à l'air.
4. Gestion du creuset
L'utilisation de creusets est très importante pour la coulée sous pression d'alliages d'aluminium, en particulier l'utilisation de creusets en fonte. Si les creusets ne peuvent pas être exploités strictement conformément aux spécifications des creusets, la teneur en Fe dans la composition de l'alliage d'aluminium dans le processus de production ultérieur peut dépasser la norme. Selon notre expérience, si le creuset en fonte peut être brossé avec la peinture du creuset en stricte conformité avec les exigences d'utilisation du nouveau pot, et brossé tous les 3 jours pendant l'utilisation, essentiellement l'augmentation de la teneur en Fe pendant toute la filière. le processus de production de moulage ne dépassera pas 0.2% (ce sont les données statistiques de l'entreprise au fil des ans, il peut y avoir des différences entre les différentes entreprises). Dans le cadre du contrôle de l'inspection entrante des lingots d'alliage d'aluminium, il peut pleinement garantir que la composition de l'alliage des pièces moulées sous pression produites répond aux exigences standard. Bien qu'il n'y ait aucune préoccupation concernant l'augmentation du fer dans l'utilisation des creusets en graphite, il convient également d'y prêter attention. Le processus de séchage pour la première utilisation des creusets en graphite doit être strictement mis en œuvre. Ces opérations affecteront la durée de vie des creusets en graphite à l'avenir et n'ont pas été bien préchauffés. La durée de vie du creuset en graphite sera grandement affectée. Le prix élevé de chaque creuset en graphite affectera le coût de production du moulage sous pression.
Conclusion
Parmi les cinq éléments majeurs de la gestion de la qualité, ce qui précède aborde principalement les questions de « matériaux » et « personnes ». Tout en gérant les matières premières et les matériaux auxiliaires, la formation et la gestion du personnel doivent être bien faites et le niveau technique des ouvriers du moulage sous pression doit être encore amélioré. Afin de résoudre efficacement les problèmes de qualité dans la production de moulage sous pression, appliquez l'idée de gestion de la qualité totale au contrôle qualité de l'atelier de moulage sous pression et utilisez les connaissances théoriques systématiques de la production de moulage sous pression pour guider la production, ce qui améliorera sûrement la capacité de contrôle de la qualité de l'atelier de moulage sous pression à une nouvelle hauteur. .
Veuillez conserver la source et l'adresse de cet article pour réimpression: Alliage d'aluminium et gestion des matériaux auxiliaires dans la production de moulage sous pression
Minghe Casting Company se consacre à la fabrication et à la fourniture de pièces de moulage de qualité et de haute performance (la gamme de pièces de moulage sous pression en métal comprend principalement Moulage sous pression à paroi mince,Chambre chaude coulée sous pression,Chambre froide coulée sous pression), Service rond (Service de moulage sous pression,Usinage CNC,Fabrication de moules,Traitement de surface). Tout moulage sous pression en aluminium personnalisé, moulage sous pression en magnésium ou en zamak/zinc et autres exigences en matière de moulages sont invités à nous contacter.
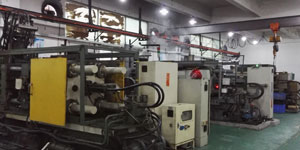
Sous le contrôle des normes ISO9001 et TS 16949, tous les processus sont effectués via des centaines de machines de moulage sous pression avancées, de machines à 5 axes et d'autres installations, allant des blasters aux machines à laver Ultra Sonic.Minghe dispose non seulement d'équipements de pointe, mais également de professionnels équipe d'ingénieurs, d'opérateurs et d'inspecteurs expérimentés pour réaliser la conception du client.
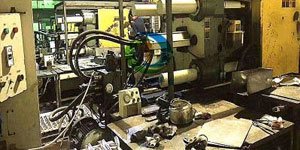
Fabricant sous contrat de moulages sous pression. Les capacités incluent des pièces de moulage sous pression en aluminium à chambre froide à partir de 0.15 lb. jusqu'à 6 lb, configuration à changement rapide et usinage. Les services à valeur ajoutée comprennent le polissage, la vibration, l'ébavurage, le grenaillage, la peinture, le placage, le revêtement, l'assemblage et l'outillage. Les matériaux travaillés comprennent des alliages tels que 360, 380, 383 et 413.
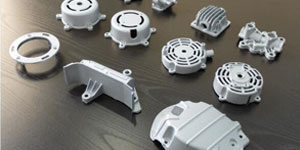
Assistance à la conception de moulage sous pression de zinc/services d'ingénierie simultanés. Fabricant sur mesure de pièces moulées en zinc de précision. Des moulages miniatures, des moulages sous pression à haute pression, des moulages en moules à glissières multiples, des moulages en moules conventionnels, des moulages sous pression unitaires et indépendants et des moulages à cavité scellée peuvent être fabriqués. Les pièces moulées peuvent être fabriquées dans des longueurs et des largeurs allant jusqu'à 24 po avec une tolérance de +/- 0.0005 po.
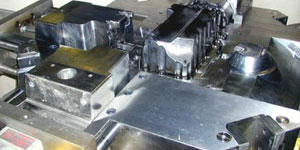
Fabricant certifié ISO 9001 : 2015 de magnésium moulé sous pression, les capacités incluent le moulage sous pression de magnésium sous pression jusqu'à une chambre chaude de 200 tonnes et une chambre froide de 3000 tonnes, la conception d'outillage, le polissage, le moulage, l'usinage, la peinture en poudre et liquide, une assurance qualité complète avec des capacités CMM , assemblage, emballage et livraison.
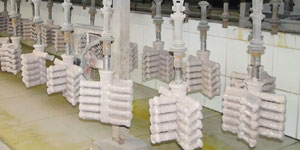
Certifié ITAF16949. Service de casting supplémentaire inclus coulée d'investissement,moulage en sable,Coulée par gravité, Coulée de mousse perdue,Coulée centrifuge,Coulée sous vide,Moulage de moule permanentLes capacités comprennent l'EDI, l'assistance technique, la modélisation solide et le traitement secondaire.
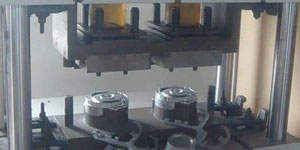
Industries de moulage Études de cas de pièces pour : voitures, vélos, avions, instruments de musique, motomarines, appareils optiques, capteurs, modèles, appareils électroniques, boîtiers, horloges, machines, moteurs, meubles, bijoux, gabarits, télécommunications, éclairage, appareils médicaux, appareils photographiques, Robots, Sculptures, Équipement de sonorisation, Équipement de sport, Outillage, Jouets et plus encore.
Que pouvons-nous vous aider à faire ensuite ?
∇ Aller à la page d'accueil pour Moulage sous pression Chine
→Pièces de fonderie-Découvrez ce que nous avons fait.
→Conseils à propos de Services de moulage sous pression
By Fabricant de moulage sous pression Minghe |Catégories : Articles utiles |Matières Mots clés: Moulage d'aluminium, Moulage de zinc, Coulée de magnésium, Moulage de titane, Fonderie en acier inoxydable, Coulée de laiton,Coulée de bronze,Vidéo de casting,Historique de l'entreprise,Moulage sous pression en aluminium |Commentaires fermés