La connaissance de la fusion des alliages de moulage sous pression
Les phénomènes physiques et chimiques du processus de fusion
La fusion des alliages est une partie importante du processus de moulage sous pression. Le processus de fusion ne consiste pas seulement à obtenir du métal en fusion, mais plus important encore, à obtenir une composition chimique conforme aux exigences, de sorte que le moulage sous pression puisse obtenir une bonne structure cristalline et un métal avec de très petits gaz et inclusions.
Au cours du processus de fusion, l'interaction entre le métal et le gaz et l'interaction entre le métal en fusion et le creuset provoquent des modifications de la composition, entraînant des inclusions et une inhalation. Par conséquent, formuler les règles correctes du processus de fusion et les appliquer strictement est une garantie importante pour l'obtention de pièces moulées de haute qualité.
1. Interaction entre le métal et le gaz
Lors du processus de fusion, les gaz rencontrés sont l'hydrogène (H2), l'oxygène (O2), la vapeur d'eau (H2O), l'azote (N2), le CO2, le CO, etc. Ces gaz se dissolvent dans le métal en fusion ou réagissent avec eux. effet.
2. La source du gaz
Le gaz peut pénétrer dans l'alliage liquide à partir du gaz du four, du revêtement du four, des matières premières, du flux, des outils, etc.
3. L'interaction entre le métal et le creuset
Lorsque la température de fusion est trop élevée, le creuset en fer réagit rapidement avec le zinc liquide et une réaction d'oxydation du fer se produit à la surface du creuset pour former des oxydes tels que Fe2O3 ; en outre, l'élément de fer réagit également avec le zinc liquide pour former le composé FeZn13 (scorie de zinc), qui est dissous dans le zinc liquide. L'épaisseur de la paroi du creuset en fer est réduite en continu jusqu'à ce qu'il soit mis au rebut.
Contrôle de la température de fusion
1. Température de moulage sous pression
Le point de fusion de l'alliage de zinc utilisé pour le moulage sous pression est de 382 ~ 386℃, et un contrôle approprié de la température est un facteur important dans le contrôle de la composition de l'alliage de zinc. Afin d'assurer la bonne fluidité du liquide d'alliage pour remplir la cavité, la température du métal en fusion dans le pot de zinc de la machine de moulage sous pression est de 415 ~ 430℃. La limite supérieure de la température de moulage sous pression des pièces à parois minces et complexes peut être prise; la limite inférieure des pièces à parois épaisses et simples peut être prise. La température du métal en fusion dans le four de fusion central est de 430 ~ 450℃. La température du métal fondu entrant dans le col de cygne est fondamentalement la même que la température dans le pot de zinc.
La température de coulée peut être contrôlée avec précision en contrôlant la température du zinc fondu dans le pot de zinc et obtenir :
- Le métal en fusion est un liquide propre sans oxydes ;
- ② La température de coulée ne fluctue pas.
Dommages causés par une température excessive :
- ① Brûlage d'éléments en aluminium et magnésium.
- La vitesse d'oxydation du métal augmente, la perte par combustion augmente et les crasses de zinc augmentent.
- ③ L'effet de la dilatation thermique provoquera le blocage de la tête du marteau.
- ④ Plus de fer est fondu dans l'alliage dans le creuset en fonte, et la réaction entre le zinc et le fer est accélérée à haute température. Des particules dures de composés intermétalliques fer-aluminium se forment, provoquant une usure excessive de la tête du marteau et du col de cygne.
- ⑤ La consommation de carburant augmente en conséquence.
Température trop basse : L'alliage a une mauvaise fluidité, ce qui n'est pas propice au formage et affecte la qualité de surface des moulages sous pression.
Les creusets ou fours actuels des machines de moulage sous pression sont équipés de systèmes de mesure et de contrôle de la température. Dans le travail quotidien, des inspections régulières sont principalement utilisées pour s'assurer de la précision des instruments de mesure de la température. Des thermomètres portables (thermomètres) sont utilisés pour mesurer et corriger régulièrement la température réelle du four.
Les syndicats de moulage sous pression expérimentés observent la fonte à l'œil nu. Si la fonte n'est pas trop visqueuse et limpide après grattage, le laitier ne monte pas rapidement, indiquant que la température est appropriée ; si la masse fondue est trop visqueuse, cela indique que la température est basse ; Une couche de givre apparaît à la surface du liquide après le laitier et le laitier monte trop vite, indiquant que la température est trop élevée et doit être ajustée à temps.
2. Comment maintenir la température stable
- L'une des meilleures méthodes : utilisez un four de fusion central et un four de machine de moulage sous pression comme four de maintien pour éviter les grands changements de température lorsque le lingot de zinc est directement ajouté au pot de zinc à fondre. La fusion concentrée peut assurer la stabilité de la composition de l'alliage.
- La deuxième meilleure méthode: l'utilisation d'un système d'alimentation automatique de liquide en métal avancé peut maintenir une vitesse d'alimentation stable, une température de liquide d'alliage et un niveau de liquide de pot de zinc.
- Si les conditions de production actuelles sont une alimentation directe dans le pot de zinc, il est recommandé d'ajouter le lingot d'alliage entier en une seule fois à l'ajout de petits lingots d'alliage plusieurs fois pour réduire le changement de température causé par l'alimentation.
3. Génération et contrôle des scories de zinc
C'est un processus physique et chimique compliqué pour faire fondre l'alliage du solide au liquide. Le gaz réagit chimiquement avec le métal en fusion, et la réaction à l'oxygène est la plus forte, et la surface de l'alliage est oxydée pour produire une certaine quantité d'écume. Les crasses contiennent des oxydes et des composés intermétalliques de fer, de zinc et d'aluminium. Les crasses grattées de la surface de la fonte contiennent généralement environ 90 % d'alliage de zinc. La vitesse de réaction de formation des crasses de zinc augmente de façon exponentielle à mesure que la température de fusion augmente.
Dans des circonstances normales, la sortie de laitier du lingot d'alliage de zinc d'origine est inférieure à 1 %, ce qui est compris entre 0.3 et 0.5 % ; tandis que la production de laitier des buses de refusion et des déchets de pièces est généralement comprise entre 2 et 5 %.
Contrôle de la quantité de scories de zinc
- Contrôlez strictement la température de fusion, plus la température est élevée, plus il y a de scories de zinc.
- Évitez autant que possible de remuer le liquide d'alliage dans le pot de zinc, toute façon d'agiter entraînera le contact d'une plus grande quantité de liquide d'alliage avec les atomes d'oxygène dans l'air, formant ainsi plus d'écume.
- Ne pas sceller trop fréquemment. Lorsque l'alliage fondu est exposé à l'air, il s'oxyde et forme de l'écume. Garder une fine couche d'écume sur la surface du four aidera le liquide dans le pot à ne pas s'oxyder davantage.
- ④ Lors du scorification, utilisez un râteau à scories en forme de disque poreux (Ф6 mm) pour gratter doucement sous l'écume afin d'éviter autant que possible l'agitation du liquide d'alliage, et ramasser les scories grattées. Frappez légèrement pour faire refluer le métal en fusion dans le pot en zinc.
Traitement des scories de zinc
- Le revendre au fournisseur de matières premières ou à une usine de transformation spéciale, car le coût de l'auto-traitement peut être plus élevé.
- ② L'usine de moulage sous pression le gère elle-même. Un four séparé est nécessaire, et la température de refusion du laitier de zinc se situe dans la plage de 420 à 440°C. Ajouter du flux en même temps. Pour fondre 100 kg de laitier, il faut ajouter 0.5 à 1.5 kg de fondant, qui est d'abord réparti uniformément sur la surface du métal, puis mélangé uniformément dans le métal en fusion avec un agitateur (environ 2 à 4 minutes). Après avoir tenu pendant 5 minutes, la surface produira un La couche ressemble plus à de la saleté, alors grattez-la.
- ③ Les matériaux des buses, les déchets de refusion des matériaux des buses, les déchets, les emplacements des déchets, les pièces mises au rebut, etc., ne doivent pas être directement placés dans le pot en zinc de la machine de moulage sous pression pour la refusion. La raison en est que la surface de ces matériaux de buse est oxydée pendant le processus de moulage sous pression et que la teneur en oxyde de zinc est beaucoup plus élevée que celle du lingot d'alliage d'origine. Lorsque ces matériaux de buse sont refondus dans le pot de zinc, car l'oxyde de zinc est dans un état visqueux dans des conditions de température élevée, lorsqu'il est retiré du pot de zinc, une grande quantité de composants d'alliage sera enlevée. Le but de la refusion du matériau de la buse et d'autres matériaux est de séparer efficacement l'oxyde de zinc de l'alliage liquide. Un peu de solvant doit être ajouté pendant la fusion et utilisé après avoir été coulé en lingot.
4. Refusion des déchets de galvanoplastie
Les déchets de galvanoplastie doivent être fondus séparément des déchets non électrolytiques, car le cuivre, le nickel, le chrome et d'autres métaux dans les déchets de galvanoplastie sont insolubles dans le zinc et existeront sous forme de particules dures dans l'alliage de zinc, ce qui entraînera des difficultés de polissage et d'usinage.
Lors de la refusion des déchets de galvanoplastie, veillez à séparer le matériau de revêtement de l'alliage de zinc. Mettez d'abord les déchets de galvanoplastie dans le creuset contenant l'alliage de zinc fondu. À ce stade, ne remuez pas la fonte et n'ajoutez pas de fondant. Utilisez le matériau de revêtement pour avoir un point de fusion élevé. Il ne fondra pas dans l'alliage, mais flottera à la surface de la fonte pendant la première période de temps. Lorsqu'il est complètement fondu, laissez le creuset reposer pendant 15 à 20 minutes pour voir s'il y a de l'écume sur la surface et grattez l'écume pour la nettoyer. Après ce processus, nous verrons s'il est nécessaire d'ajouter un agent de raffinage.
5. Questions nécessitant une attention particulière dans l'opération de fusion
- 1. Creuset : il doit être nettoyé avant utilisation pour éliminer l'huile, la rouille, les scories et l'oxyde sur la surface. Afin d'empêcher l'élément en fer du creuset en fonte de se dissoudre dans l'alliage, le creuset doit être préchauffé à 150 ~ 200 , pulvériser une couche de peinture sur la surface de travail, puis chauffé à 200 ~ 300 ℃ pour éliminer complètement l'eau dans la peinture.
- 2. Outils : Avant d'utiliser les outils de fusion, la saleté de surface doit être éliminée et les pièces en contact avec le métal doivent être préchauffées et peintes. L'outil ne doit pas être mouillé, sinon il provoquera des éclaboussures et une explosion de la fonte.
- 3. Matériau en alliage : nettoyer et préchauffer avant de fondre pour éliminer l'humidité adsorbée sur la surface. Afin de contrôler la composition de l'alliage, il est recommandé d'utiliser 2/3 du nouveau matériau et 1/3 du matériau recyclé.
- 4. La température de fusion ne doit pas dépasser 450 °C.
- 5. Nettoyez l'écume sur la surface liquide dans le pot de zinc à temps, reconstituez le zinc à temps et maintenez la hauteur normale du niveau de fusion (pas moins de 30 mm sur la surface du creuset), car trop d'écume et un niveau de liquide trop bas est facile Le laitier de matériau pénètre dans le cylindre à col de cygne, tend la rêne en acier, la tête de marteau et le cylindre lui-même, entraînant le blocage de la tête de marteau, du col de cygne et de la ferraille de la tête de marteau.
- 6. L'écume sur la fonte est doucement agitée avec un grattoir à scories pour l'accumuler et l'éliminer.
Veuillez conserver la source et l'adresse de cet article pour réimpression: La connaissance de la fusion des alliages de moulage sous pression
Minghé Société de moulage sous pression sont dédiés à la fabrication et à la fourniture de pièces de moulage de qualité et de haute performance (la gamme de pièces de moulage sous pression en métal comprend principalement Moulage sous pression à paroi mince,Chambre chaude coulée sous pression,Chambre froide coulée sous pression), Service rond (Service de moulage sous pression,Usinage CNC,Fabrication de moules,Traitement de surface). Tout moulage sous pression en aluminium personnalisé, moulage sous pression en magnésium ou en zamak/zinc et autres exigences en matière de moulages sont invités à nous contacter.
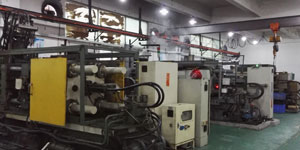
Sous le contrôle des normes ISO9001 et TS 16949, tous les processus sont effectués via des centaines de machines de moulage sous pression avancées, de machines à 5 axes et d'autres installations, allant des blasters aux machines à laver Ultra Sonic.Minghe dispose non seulement d'équipements de pointe, mais également de professionnels équipe d'ingénieurs, d'opérateurs et d'inspecteurs expérimentés pour réaliser la conception du client.
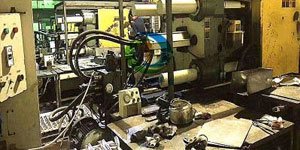
Fabricant sous contrat de moulages sous pression. Les capacités incluent des pièces de moulage sous pression en aluminium à chambre froide à partir de 0.15 lb. jusqu'à 6 lb, configuration à changement rapide et usinage. Les services à valeur ajoutée comprennent le polissage, la vibration, l'ébavurage, le grenaillage, la peinture, le placage, le revêtement, l'assemblage et l'outillage. Les matériaux travaillés comprennent des alliages tels que 360, 380, 383 et 413.
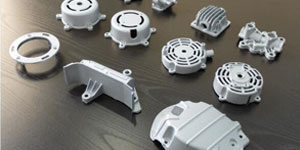
Assistance à la conception de moulage sous pression de zinc/services d'ingénierie simultanés. Fabricant sur mesure de pièces moulées en zinc de précision. Des moulages miniatures, des moulages sous pression à haute pression, des moulages en moules à glissières multiples, des moulages en moules conventionnels, des moulages sous pression unitaires et indépendants et des moulages à cavité scellée peuvent être fabriqués. Les pièces moulées peuvent être fabriquées dans des longueurs et des largeurs allant jusqu'à 24 po avec une tolérance de +/- 0.0005 po.
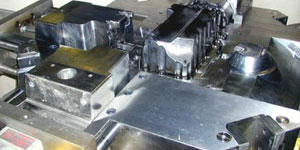
Fabricant certifié ISO 9001 : 2015 de magnésium moulé sous pression, les capacités incluent le moulage sous pression de magnésium sous pression jusqu'à une chambre chaude de 200 tonnes et une chambre froide de 3000 tonnes, la conception d'outillage, le polissage, le moulage, l'usinage, la peinture en poudre et liquide, une assurance qualité complète avec des capacités CMM , assemblage, emballage et livraison.
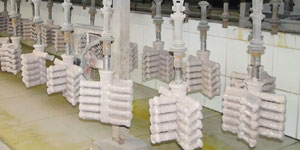
Certifié ITAF16949. Service de casting supplémentaire inclus coulée d'investissement,moulage en sable,Coulée par gravité, Coulée de mousse perdue,Coulée centrifuge,Coulée sous vide,Moulage de moule permanentLes capacités comprennent l'EDI, l'assistance technique, la modélisation solide et le traitement secondaire.
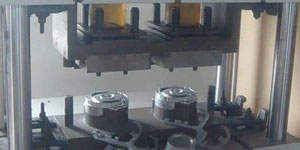
Industries de moulage Études de cas de pièces pour : voitures, vélos, avions, instruments de musique, motomarines, appareils optiques, capteurs, modèles, appareils électroniques, boîtiers, horloges, machines, moteurs, meubles, bijoux, gabarits, télécommunications, éclairage, appareils médicaux, appareils photographiques, Robots, Sculptures, Équipement de sonorisation, Équipement de sport, Outillage, Jouets et plus encore.
Que pouvons-nous vous aider à faire ensuite ?
∇ Aller à la page d'accueil pour Moulage sous pression Chine
→Pièces de fonderie-Découvrez ce que nous avons fait.
→Conseils à propos de Services de moulage sous pression
By Fabricant de moulage sous pression Minghe |Catégories : Articles utiles |Matières Mots clés: Moulage d'aluminium, Moulage de zinc, Coulée de magnésium, Moulage de titane, Fonderie en acier inoxydable, Coulée de laiton,Coulée de bronze,Vidéo de casting,Historique de l'entreprise,Moulage sous pression en aluminium |Commentaires fermés