Optimisation et application du schéma de moulage sous pression du moulage de coque en aluminium d'étrangleur ETC basé sur MAGMASOFT
Ces dernières années, avec le développement de l'économie mondiale, la demande de pièces automobiles en alliage d'aluminium a un impact important sur les perspectives globales de développement de l'industrie du moulage sous pression. Face à une concurrence industrielle de plus en plus sévère et au raccourcissement constant des cycles de développement de nouveaux produits, la livraison de produits qualifiés répondant aux exigences des clients dans un court laps de temps constituera une nouvelle direction pour le développement des entreprises de moulage sous pression ; cet article utilise la fonction DOE de MAGMASOFT pour effectuer une analyse de simulation et une comparaison de différents schémas de coulée et de divers paramètres de processus au début des coulées de coque en aluminium d'étranglement ETC. Et l'optimisation, pour sélectionner la meilleure solution, réduisant ainsi le cycle de développement et assurant le succès de l'essai ponctuel du produit et une production et une livraison de masse fluides.
Face à l'aggravation de la crise climatique mondiale et à la tendance de plus en plus sévère aux économies d'énergie, à la réduction des émissions et à la réduction de la pollution, l'industrie automobile continuera également à se développer dans le sens des économies d'énergie, de la réduction des émissions et de l'intelligence ; et le système d'accélérateur électronique est né dans cet environnement (Electronic Throttle Control System pour faire court ETC) est une partie indispensable et importante du système de moteur automobile actuel. Il détermine les conditions de fonctionnement du moteur en contrôlant le débit d'air d'admission du moteur pour assurer la meilleure puissance et carburant du véhicule. Économique, afin de contrôler davantage les exigences en matière d'émissions. Il est prévisible que l'accélérateur électronique, en tant que l'une des technologies clés des systèmes avancés de contrôle et de sécurité des véhicules, aura sûrement de bonnes perspectives d'application comme d'autres technologies avancées de contrôle des véhicules.
En tant que l'un des composants les plus importants du système d'accélérateur électronique, les moulages de coque en aluminium d'accélérateur ETC affecteront certainement la faisabilité et la stabilité du système ; par conséquent, la production de pièces moulées en aluminium d'étranglement ETC qui répondent aux exigences sera extrêmement importante. Dans cet article, avec l'aide de la fonction DOE de MAGMASOFT, au début des moulages de boîtiers en aluminium d'étranglement ETC, différents schémas de coulée et diverses comparaisons et optimisations d'analyse de simulation de paramètres de processus sont effectués pour sélectionner le meilleur schéma, réduisant ainsi le développement cycle et garantir ce produit une fois Le succès du modèle d'essai et la production en série et la livraison en douceur.
1 Analyse de la structure du produit et exigences techniques
La qualité du matériau de moulage sous pression de la coque en aluminium d'étranglement ETC étudiée dans cet article est AlSi12Cu1Fe, et sa dimension de contour maximale est de 111 mm * 109 mm * 84 mm. L'épaisseur moyenne de ce moulage est de 4 mm et l'épaisseur à l'épaisseur de paroi maximale est de 13 mm. La structure globale du produit est plus compliquée. , Il existe de nombreuses nervures hautes isolées, ce qui n'est pas propice au remplissage ordonné de l'aluminium en fusion ; l'épaisseur de paroi de certaines positions diffère considérablement et la zone à paroi mince se solidifiera d'abord en un état solide, ce qui équivaut à diviser l'alliage fondu en plusieurs. La petite zone fermée forme une zone de phase liquide isolée au niveau de la paroi épaisse. Lorsque le processus de solidification et de retrait du métal en fusion dans ces zones isolées en phase liquide ne peut pas être complété, le problème des cavités de retrait et de la porosité se produira inévitablement à l'intérieur.
En raison de l'environnement de travail compliqué des moulages de coques en aluminium d'étranglement ETC, le grenaillage est nécessaire pour renforcer la qualité de surface des moulages et améliorer leur résistance à la corrosion ; la position d'installation correspondante du produit a des exigences de tolérance géométrique et dimensionnelle plus élevées ; Assurez-vous que le volume de fuite à la pression de test de fuite de 3 bars est inférieur ou égal à 3 cc/min, et que le diamètre du trou de retrait dans la zone locale du produit ne doit pas dépasser 0.7 mm, le nombre total ne ne dépasse pas 5, l'espacement n'est pas inférieur à 10 mm et ne dépasse pas 10 % de la surface totale. ; Par conséquent, pour ce moulage sous pression, des exigences de conception de processus de moulage très élevées sont nécessaires pour garantir que la qualité interne du moulage peut répondre à la norme d'acceptation du client ;
2 Schéma de moulage sous pression du produit et conception des paramètres de processus
2.1 Conception du schéma de moulage sous pression du produit
Le lien extrêmement important de conception de porte de moulage sous pression dans la technologie de production de moulage sous pression détermine la qualité des pièces de moulage sous pression, l'efficacité de la production de moulage sous pression, la durée de vie du moule, le découpage et le nettoyage des pièces de moulage sous pression, le taux de refusion des alliages de moulage sous pression, et l'efficacité énergétique des machines de moulage sous pression. Il a un impact de grande envergure; par conséquent, la conception d'une position de porte, d'une épaisseur et d'une taille de porte raisonnables et d'une quantité de porte sont les clés pour assurer une qualité de moulage sous pression qualifiée ; à partir de l'analyse des caractéristiques de la structure du produit et de l'expérience en matière de conception de processus, le boîtier en aluminium d'étranglement ETC Il existe trois emplacements pour les pièces moulées qui conviennent à la conception de l'entrée d'alimentation ; par conséquent, cet article concevra trois schémas de coulée de moulage sous pression différents. À partir du chemin de remplissage théorique et de la distance d'écoulement, différents schémas de coulée produiront différents effets de remplissage, ils doivent donc être basés sur les résultats du logiciel de simulation MAGMA qui sont comparés et analysés pour vérification ;
2.1.1 Plan de coulage monotype
Comme le montre la figure, le nombre de vannes dans le premier schéma de coulée est conçu sous forme de doubles brins, qui sont respectivement conçus dans la zone de paroi latérale de la position d'installation du moteur et de la position d'installation de la plaque de vanne. Le poinçon d'injection d'un diamètre de 60 mm est sélectionné et le rapport de vitesse d'injection est de 1:14 ; L'avantage de ce schéma de coulée est que le flux de métal en fusion est relativement court, ce qui a peu d'effet sur la valeur de réduction de température pendant le processus de remplissage ; la conception de trois canaux d'écoulement est propice à la transmission de la pression et à l'alimentation du métal en fusion, ce qui est utile pour réduire le processus de production ultérieur. Le risque de défauts de retrait a un certain effet positif ; son inconvénient est qu'en raison de la classification des produits et des raisons de structure, le patin doit être conçu avec certaines marches et des zones à parois minces. Ces positions sont susceptibles d'envelopper le gaz pendant le processus de remplissage ultérieur. De plus, la position d'installation du moteur de ce produit n'est pas traitée et la conception de la porte est ici, ce qui permet de laver directement le noyau de la paroi intérieure et la température à la position de la porte. Plus haut, il est facile de provoquer des défauts de matrice et d'érosion dans la position d'installation du moteur ; et la position de la porte n'est pas traitée, ce qui a un certain impact négatif sur le rognage et le nettoyage des moulages sous pression ultérieurs ;
2.1.2 Conception du deuxième schéma de coulée
Comme le montre la figure, le nombre de portes dans le deuxième schéma de coulée est conçu pour être un, et la position est conçue dans la zone du trou circulaire latéral de la position d'installation de la plaque de vanne. Le poinçon d'injection d'un diamètre de 60 mm est sélectionné et le rapport de vitesse d'injection est de 1:30; cette coulée L'avantage de la solution est que la rigole peut être conçue avec une transition relativement douce, ce qui est bénéfique au remplissage du métal en fusion et réduit le phénomène d'enveloppement de gaz pendant le processus de remplissage, et réduit les défauts causés par le gaz apporté par le coureur ; la porte est conçue à la position de la surface de traitement. Réduisez la charge de travail de coupe et de nettoyage des pièces moulées sous pression et réduisez les coûts de production ; la grille à un seul brin peut empêcher plusieurs brins de métal en fusion d'entrer dans la cavité et de provoquer un vortex, un entraînement et une oxydation. L'inconvénient est qu'il est à l'extrémité de la porte. L'effet d'alimentation de la position du point chaud fait fondamentalement défaut et d'autres schémas d'alimentation auxiliaires doivent être pris en compte ; et le flux de métal en fusion est relativement long, ce qui a un certain impact négatif sur la température du métal en fusion pendant le processus de remplissage, et des défauts de matériau froid peuvent se produire dans des emplacements locaux. ;
2.1.3 Conception du troisième schéma de coulée
Comme le montre la figure, le nombre de trois portes dans le schéma de coulée est conçu pour être un, et la position est définie dans la zone du trou circulaire latéral de la position d'installation de la plaque de soupape. Le poinçon d'injection d'un diamètre de 60 mm est sélectionné et le rapport de vitesse d'injection est de 1:30; L'avantage de la porte est qu'elle est conçue dans la position de la surface de traitement, ce qui peut réduire la charge de travail de coupe et de nettoyage de la machine de moulage sous pression, et réduire les coûts de production. La porte est conçue avec un style de remplissage linéaire, ce qui peut réduire la course de remplissage de l'aluminium fondu et la perte de température de l'aluminium fondu. Le montant est réduit; la distance entre le poinçon et la porte est courte, ce qui peut assurer la transmission efficace de la pression du poinçon ; l'inconvénient est que la flexibilité des paramètres d'ajustement de production ultérieurs est médiocre et que la qualité du produit ne peut pas être améliorée en ajustant les paramètres de moulage sous pression.
2.2 Conception des paramètres de processus du produit
Selon l'analyse structurelle et les exigences de qualité des moulages de coque en aluminium ETC, ce produit utilise une machine de coulée sous pression 350T, un moule et une cavité, et la pression de coulée est réglée sur 100MPa pour assurer une efficacité d'alimentation suffisante et réduire l'apparition de défauts de retrait dans la période ultérieure. ; La température de coulée est conçue pour être de 660-680℃, et les noyaux de moule mobiles et fixes sont préchauffés à 180-200℃; pendant le remplissage, la basse vitesse est réglée sur 0.25 m/s, la grande vitesse est réglée sur 3 m/s et les points de commutation à grande vitesse sont testés à 340 mm et 350 mm respectivement. La position permet de déterminer l'état de remplissage le plus stable du métal en fusion et le moindre phénomène de courants de Foucault et d'entraînement ; en même temps, le système de contrôle de la température du refroidissement en ligne et du refroidissement ponctuel est utilisé pour assurer un bon équilibre thermique du moule;
3. Simulation numérique et analyse comparative de l'import en un clic
Le contrôle du processus de remplissage et de solidification de la coulée a une influence décisive sur la qualité de la coulée sous pression, mais comme ces deux processus sont achevés dans une cavité fermée et invisible pendant le processus de production, il est impossible d'observer et d'analyser directement ou indirectement, la valeur précédente Simulation est donc particulièrement importante ; en utilisant la fonction DOE du code MAG, l'importation en un clic des trois schémas d'injection ci-dessus et deux tests de positions de commutation à grande vitesse, le calcul unique de plusieurs schémas, la prédiction la plus rapide de l'emplacement du défaut et la recherche du meilleur plan à améliorer la qualité interne des produits, réduire les cycles de développement et réduire les coûts de production.
3.1 Simulation et analyse du processus de remplissage
Comme le montre la figure 3, le résultat de la simulation de la première ligne de l'image est le temps de remplissage. La position de commutation à grande vitesse des trois premiers schémas est de 340 mm et le temps de remplissage est court. La position de commutation à grande vitesse des trois derniers schémas est de 350 mm et le temps de remplissage est long. La position de couleur vive est la dernière position de remplissage des trois schémas d'injection ;
Le résultat de la deuxième ligne de l'image est le résultat de la pression atmosphérique maximale. La couleur vive du résultat de la simulation est la position à haute pression d'air et le risque de stomates est élevé. Par comparaison, on constate que la valeur de la pression d'air des schémas 2 et 5 est relativement faible et que le risque de stomie est relativement faible ;
Le résultat de la troisième rangée de l'image est le résultat du volume de remplissage. Le résultat de la simulation présente une teneur en air élevée en position lumineuse et un risque élevé de fuite. Par comparaison, on constate que la valeur des deuxième et cinquième volumes du schéma est relativement faible, et le risque de fuite est relativement faible ;
Une analyse complète des résultats de simulation du processus de remplissage montre que la pression d'air et l'entraînement des deuxième et cinquième options sont relativement faibles, que la deuxième position de commutation à grande vitesse est vers l'avant et que le temps de remplissage est court, de sorte que la formabilité globale est bon.
3.2 Simulation et analyse du processus de solidification
Comme le montre la figure 4, le résultat de la première ligne de l'image est le champ de température de congélation. Les résultats de simulation montrent que le temps de solidification de la grille intérieure du schéma 3 et du schéma 6 est le plus long, et le temps d'alimentation en pression est le plus long ; le schéma 1 et le schéma 4 sont le second, et le temps d'alimentation sous pression est le milieu ; le temps de solidification de la porte intérieure du schéma 2 et du schéma 5 Le temps le plus court et le plus court pour l'alimentation en pression;
Le résultat de la deuxième rangée est le temps d'alimentation effectif du joint chaud, et la couleur vive du résultat de la simulation est la position du joint chaud du produit, qui est la position où la structure du produit est relativement épaisse et finalement solidifiée. Les emplacements des programmes 1, 2, 4 et 5 sont fondamentalement les mêmes. Les schémas 3 et 6 ont des grilles intérieures relativement épaisses, donc si les deux points chauds de la grille intérieure sont connectés ensemble, les points chauds augmenteront ;
Le résultat de la troisième ligne est le résultat du retrait. En raison de l'alimentation sous pression, l'état de rétrécissement des schémas 3 et 6 est le plus petit, et le rétrécissement des quatre autres schémas est fondamentalement le même. En comparaison, le schéma 2 et le schéma 5 sont relativement petits.
Sur la base de l'analyse des résultats de simulation du processus de solidification, la cavité de retrait du schéma 3 et du schéma 6 est la plus petite, mais le joint chaud à la porte intérieure est le plus grand, et le joint thermique et les résultats de retrait du schéma 2 et le schéma 5 sont relativement meilleurs.
4. Vérification de la production
Analyse de simulation complète, la deuxième méthode de coulée est utilisée pour la production. La figure 5 montre l'image de production des moulages de boîtiers en aluminium d'étranglement ETC ; grâce à l'inspection du produit et à l'inspection aux rayons X, les pièces moulées ne présentaient pas de pores et de défauts de retrait dépassant les exigences de qualité du client ; également passé les exigences de fuite latérale, aucune fuite ne s'est produite; la surface de la coulée était brillante, aucun défaut évident de matériau froid et un coulage insuffisant n'apparaissaient, l'effet global répondait pleinement aux exigences d'inspection de qualité du client et une production en série fluide.
Veuillez conserver la source et l'adresse de cet article pour réimpression:Optimisation et application du schéma de moulage sous pression du moulage de coque en aluminium d'étrangleur ETC basé sur MAGMASOFT
Minghé Société de moulage sous pression sont dédiés à la fabrication et à la fourniture de pièces de moulage de qualité et de haute performance (la gamme de pièces de moulage sous pression en métal comprend principalement Moulage sous pression à paroi mince,Chambre chaude coulée sous pression,Chambre froide coulée sous pression), Service rond (Service de moulage sous pression,Usinage CNC,Fabrication de moules,Traitement de surface). Tout moulage sous pression en aluminium personnalisé, moulage sous pression en magnésium ou en zamak/zinc et autres exigences en matière de moulages sont invités à nous contacter.
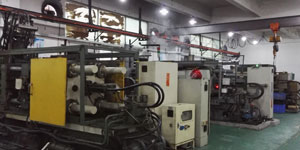
Sous le contrôle des normes ISO9001 et TS 16949, tous les processus sont effectués via des centaines de machines de moulage sous pression avancées, de machines à 5 axes et d'autres installations, allant des blasters aux machines à laver Ultra Sonic.Minghe dispose non seulement d'équipements de pointe, mais également de professionnels équipe d'ingénieurs, d'opérateurs et d'inspecteurs expérimentés pour réaliser la conception du client.
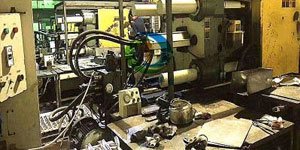
Fabricant sous contrat de moulages sous pression. Les capacités incluent des pièces de moulage sous pression en aluminium à chambre froide à partir de 0.15 lb. jusqu'à 6 lb, configuration à changement rapide et usinage. Les services à valeur ajoutée comprennent le polissage, la vibration, l'ébavurage, le grenaillage, la peinture, le placage, le revêtement, l'assemblage et l'outillage. Les matériaux travaillés comprennent des alliages tels que 360, 380, 383 et 413.
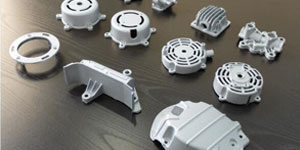
Assistance à la conception de moulage sous pression de zinc/services d'ingénierie simultanés. Fabricant sur mesure de pièces moulées en zinc de précision. Des moulages miniatures, des moulages sous pression à haute pression, des moulages en moules à glissières multiples, des moulages en moules conventionnels, des moulages sous pression unitaires et indépendants et des moulages à cavité scellée peuvent être fabriqués. Les pièces moulées peuvent être fabriquées dans des longueurs et des largeurs allant jusqu'à 24 po avec une tolérance de +/- 0.0005 po.
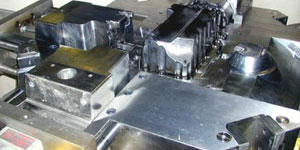
Fabricant certifié ISO 9001 : 2015 de magnésium moulé sous pression, les capacités incluent le moulage sous pression de magnésium sous pression jusqu'à une chambre chaude de 200 tonnes et une chambre froide de 3000 tonnes, la conception d'outillage, le polissage, le moulage, l'usinage, la peinture en poudre et liquide, une assurance qualité complète avec des capacités CMM , assemblage, emballage et livraison.
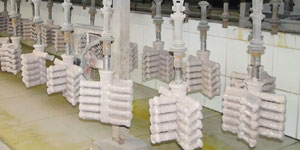
Certifié ITAF16949. Service de casting supplémentaire inclus coulée d'investissement,moulage en sable,Coulée par gravité, Coulée de mousse perdue,Coulée centrifuge,Coulée sous vide,Moulage de moule permanentLes capacités comprennent l'EDI, l'assistance technique, la modélisation solide et le traitement secondaire.
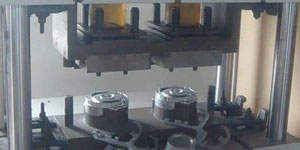
Industries de moulage Études de cas de pièces pour : voitures, vélos, avions, instruments de musique, motomarines, appareils optiques, capteurs, modèles, appareils électroniques, boîtiers, horloges, machines, moteurs, meubles, bijoux, gabarits, télécommunications, éclairage, appareils médicaux, appareils photographiques, Robots, Sculptures, Équipement de sonorisation, Équipement de sport, Outillage, Jouets et plus encore.
Que pouvons-nous vous aider à faire ensuite ?
∇ Aller à la page d'accueil pour Moulage sous pression Chine
→Pièces de fonderie-Découvrez ce que nous avons fait.
→Conseils à propos de Services de moulage sous pression
By Fabricant de moulage sous pression Minghe |Catégories : Articles utiles |Matières Mots clés: Moulage d'aluminium, Moulage de zinc, Coulée de magnésium, Moulage de titane, Fonderie en acier inoxydable, Coulée de laiton,Coulée de bronze,Vidéo de casting,Historique de l'entreprise,Moulage sous pression en aluminium |Commentaires fermés